Thermal insulation is used to prevent or reduce the transfer of heat between objects or spaces. The goal of thermal insulation is to maintain a comfortable indoor temperature by reducing the amount of heat that enters or leaves a building, which in turn can lower energy costs and improve energy efficiency. When installed into a home, commercial, institutional or industrial building it provides an environment where you can live, work and play in comfort, all while reducing your energy consumption. This is especially important considering our varied and sometimes extreme weather conditions across the world.
Residential
Insulation is one of the most important, cost-effective, energy saving building materials in a home. In fact, without the insulation, some of the other energy-efficient components in a home won’t perform as intended. Insulation is used as a thermal and acoustical solution in the walls, ceilings, floors, and attics of a home or every part of the building envelope. Insulation keeps your home cooler in the summer and warmer in the winter. Insulation in a home saves energy and is perhaps the most cost-effective way to lower energy bills. Insulation reduces noise and adds to the quality and comfort of your home. Whether you’re building a new home, renovating a room, cottage, basement, attic or entire home, select an insulation that is ‘installer friendly’ one that anyone can do safely.

Commercial
Insulation systems are used extensively in commercial, institutional and metal buildings as a solution to reduce the rate of heat transfer through the roofs and sidewalls. Board, blanket and batt insulation also installed on and within the interior walls, reduces the transmission of room-to-room noise. Insulation is used on chilled water piping, HVAC ducts and equipment for thermal, sound, condensation and process control. Insulating saves energy and helps reduce greenhouse gas emission.

Industrial
Insulation is used to insulate HVAC ducts and equipment, process piping, industrial equipment, tanks and vessels found in power plants, petrochemical plants, refineries and other industrial applications. These insulation systems are carefully specified to reduce energy costs, enhance process performance, reduce greenhouse gas emissions, protect personnel, control condensation, reduce noise levels and to maximize a return on investment.

WHY WE INSULATE OUR HOMES?
One of the most important and cost-effective energy saving materials in our home is the insulation. It quietly performs some remarkable functions despite the fact most of us never see it, or know that it is working day in and day out saving us energy and keeping us comfortable. Insulation keeps our homes warm in winter and cool in summer. In fact, it works so well that comfort is something that many now take for granted. The insulation system also helps the heating and cooling equipment perform better and more efficiently. It keeps our homes quieter, it provides a healthier environment, and insulation keeps our energy bills down. Reducing energy costs is one of the top reasons homeowners are reassessing the insulation in their homes. Whether building a new home, or renovating your current one, the selection of your insulation system warrants some serious attention. Adding insulation can offer you a lifetime of energy savings while improving the energy efficiency and comfort to your home.
WHERE WE SHOULD INSULATE?
Generally insulation is installed between the framing members in the home. Walls, ceilings, floors around the perimeter, basements, attics and even interior rooms of the home.

- Exterior walls. Sections sometimes overlooked are walls between living spaces and unheated garages or storage rooms, dormer walls, and the portions of walls above ceilings of adjacent lower sections of split-level homes.
- Ceilings with cold spaces above, including dormer ceilings.
- Knee walls of attic spaces finished as living quarters.
- Sloped walls and ceilings of attic spaces finished as living quarters.
- Perimeters of slabs on grade.
- Floors above vented crawlspaces. Insulation may also be placed on crawlspace floors and walls.
- Floors over unheated or open spaces such as over garages or porches. Floors over unheated basements. The cantilevered portions of floors.
- Basement walls.
- Band or header joists, the wall sections at floor levels.
- Interior walls, ceilings and floors where sound control is desired.
SELECTING THE RIGHT INSULATION MATERIALS
While some insulation materials lend themselves better to the do-it-yourself, it is generally recommended that a professional or certified insulation contractor perform the insulation work. As the consumer, however you need to be informed about the types of insulation available, their rated thermal performance, their ease of application, the impact the installation will have on your family while the work is being done and of course, their value. You should also consider the overall lifetime performance of the insulation, its environmental features, and any safety-related considerations.
Mineral Wool
Mineral wool covers quite a few types of insulation. It could refer to either glass wool which is fibreglass manufactured from recycled glass or rock wool which is a type of insulation made from basalt. Mineral wool can be purchased in batts or as a loose material. Most mineral wool does not have additives to make it fire resistant, making it poor for use in situation where extreme heat is present. Mineral wool has an R-value ranging from R-2.8 to R-3.5.

Fibreglass
Fibreglass is an extremely popular insulation material. One of its key advantages is value. Fibreglass insulation has a lower installed price than many other types of insulating materials and, for equivalent R-Value performance (i.e., thermal resistance), it is generally the most cost-effective option when compared to cellulose or sprayed foam insulation systems. Because of how it is made, by effectively weaving fine strands of glass into an insulation material, fibreglass is able to minimize heat transfer. It is essential when installing fibreglass that the necessary safety equipment is worn, as glass powder and tiny shards of glass are formed, which could potentially cause damage to the eyes, lungs, and skin. Fibreglass is an excellent non-flammable insulation material, with R-values ranging from R-2.9 to R-3.8 per inch.

Polystyrene
Polystyrene is a waterproof thermoplastic foam which is an excellent sound and temperature insulation material. It comes in two types, expanded (EPS) and extruded (XEPS) also known as Styrofoam. The more costly XEPS has an R-value of R-5.5 while EPS is R-4. Polystyrene insulation has a uniquely smooth surface which no other type of insulation possesses. It is used in both residential and commercial settings. Polystyrene insulation is very rigid, unlike its fluffier cousins. Typically the foam is created or cut into blocks, ideal for wall insulation.
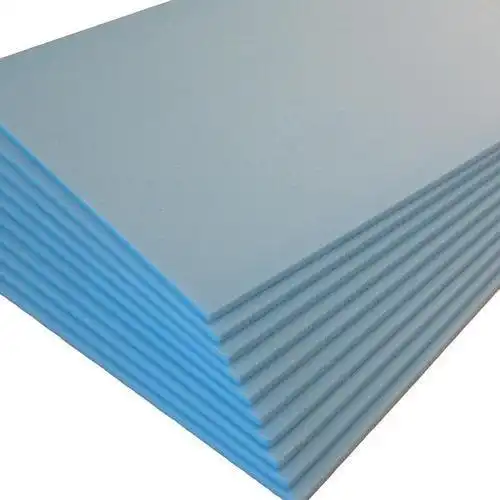
Cellulose
Cellulose is a very eco-friendly form of insulation. It is composed of 75-85% recycled paper fibre, usually post-consumer waste newsprint. The other 15% is a fire retardant such as boric acid or ammonium sulphate. Because of the compactness of the material, cellulose contains next to no oxygen within it. Without oxygen within the material, this helps to minimize the amount of damage that a fire can cause. So not only is cellulose perhaps one of the most eco-friendly forms of insulation, but it is also one of the most fire resistant forms of insulation. Cellulose has an R-value between R-3.1 and R-3.7.
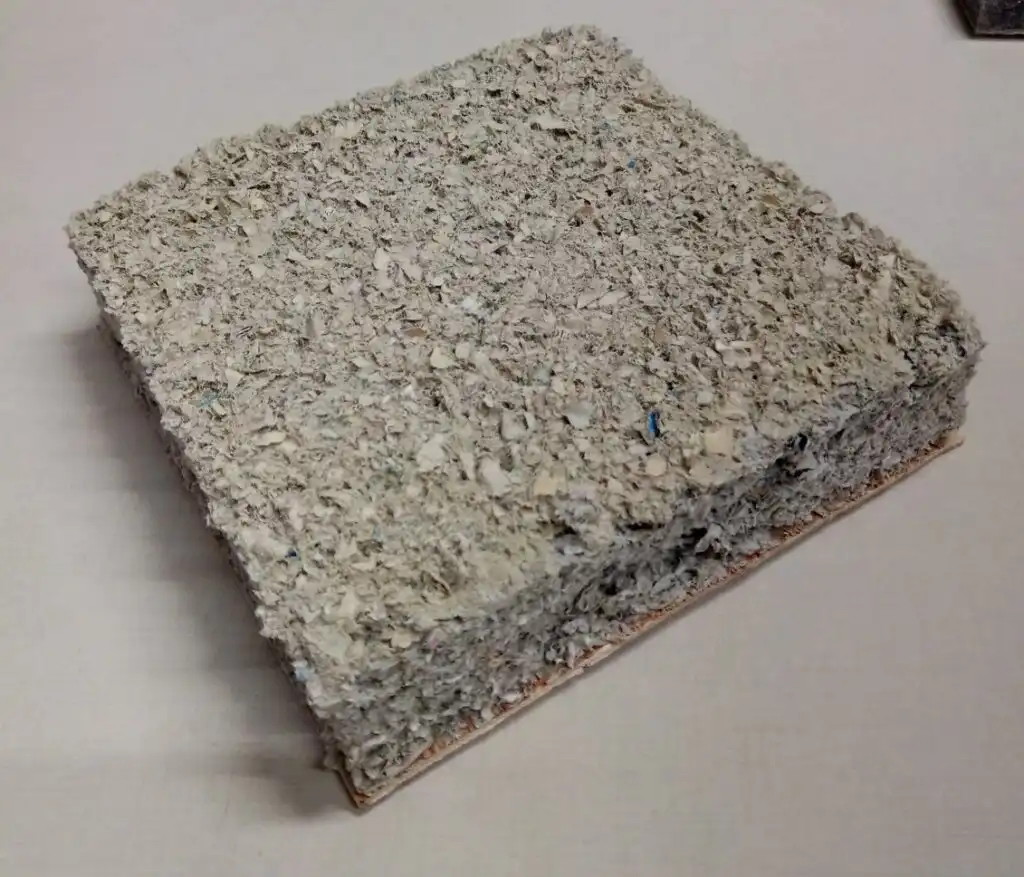
Polyurethane Foam
Spray polyurethane foam (SPF) is made by mixing and reacting chemicals to create a foam. The mixing and reacting materials react very quickly, expanding on contact to create foam that insulates, air seals and provides a moisture barrier. They are relatively light, weighing approximately two pounds per cubic foot, and have an R-value of approximately R-6.3 per inch of thickness.

SUSTAINABILITY
Today’s built environment specifiers are under increasing pressure; to be more green, to engineer a lower carbon environment and to move towards greater sustainability. The larger insulation manufacturers have put significant measures in place to:
- Reduce reliance upon raw materials.
- Recycle pre and post-manufacture.
- Reduce packaging and ensure packaging remains recyclable.
- Reduce energy use in production and transport.
- Have zero waste to landfill policies.
Manufacturers market their products as ‘sustainable’ on the premise that their insulation products will save far more energy/carbon, over the installation lifetime than it has cost to manufacture.
CONCLUSION
Insulation materials are reliant upon their inherent molecular make-up, to minimize the three forms of heat transfer – radiation, conduction and convection. The greatest building heat losses are from air movement. Any moving body of air will extract heat from an object or surface over which it passes. The heat loss is proportional to the speed of the moving air, the amount of water present and the temperature differential between heat source and air.
The faster the air movement over a heat source, the faster the heat transfer occurs. The presence of water droplets will act as an acceleration to this process, although control over water vapour saturation will usually need to be exercised to avoid problems caused by condensation.
Condensation may be controlled to a large extent by ensuring water vapour in the air is contained within the warm internal environment. Vapour control layers on the warm side of the insulation, effectively sealing the envelope to air migration between warm and cooler zones are the theoretical solution.
Current materials technology and carefully monitored workmanship in assembling those materials, can achieve near zero air leakage through the insulated envelope, and indeed Passives design is reliant upon this, while using controlled ventilation to remove contaminated air, design principles that are reliant upon workmanship in order to succeed.
Addressing the cellular construction of dedicated insulation materials, the intrinsic aim is to prevent the movement of gases within the insulation core matrix, in doing so the loss of heat consequential to that movement will also be reduced.
Although ‘open cell’ insulation products, such as wool allow much greater migration of air across them, and this limits their performance, their flexible construction gives a far greater advantage in terms of quality control of installation workmanship. Due to the nature of the material, jointing produces a very similar result to the material itself. Whereas rigid board products carry an onerous installation premium penalty to achieve manufacturer’s ‘lab test’ precision standards of jointing.
Insulation materials with a more dense, self-contained cellular composition will provide a lower thermal conductivity (λ value) and so a higher thermal resistivity (R value) to out-perform ‘open cell’ materials, which rely on maintaining dry air within their cores for ultimate performance.
There are open cell foamed products available that due to their core matrix composition have a higher thermal conductivity than their closed cell cousins, but have advantages with greater flexibility to accommodate building movement, and any deterioration of cell walls will not result in the liberation of the gas content.
In specifying insulation products the building designer should consider the potential for water contamination, and the possibility of gas migration within the core matrix and the resulting compromise in performance, that could deteriorate further over the lifetime of the building, unseen and unchecked.
There are better performing technologies on the market with ‘ and ‘evacuated panels’, but performance is reliant upon the same principles of heat transfer, and for the time being has a limited specification niche, remaining largely cost prohibitive for the vast majority of applications.
