Fiber Reinforced Concrete is a composite material consisting of fibrous material which increases its structural integrity. It includes mixtures of cement, mortar or concrete and discontinuous, discrete, uniformly dispersed suitable fibers. Fibers are usually used in concrete to control cracking due to plastic shrinkage and to drying shrinkage. They also reduce the permeability of concrete and thus reduce the bleeding of water.
Advantages of Fiber-reinforced concrete
- Fibers reinforced concrete may be useful where high tensile strength and reduced cracking are desirable or when conventional reinforcement cannot be placed
- It improves the impact strength of concrete, limits the crack growth and leads to a greater strain capacity of the composite material
- For industrial projects, macro-synthetic fibers are used to improve concrete’s durability. Made from synthetic materials, these fibers are long and thick in size and may be used as a replacement for bar or fabric reinforcement
- Adding fibers to the concrete will improve its freeze-thaw resistance and help keep the concrete strong and attractive for extended periods.
- Improve mix cohesion, improving pumpability over long distances
- Increase resistance to plastic shrinkage during curing
- Minimizes steel reinforcement requirements
- Controls the crack widths tightly, thus improving durability
- Reduces segregation and bleed-water
- FRC, toughness is about 10 to 40 times that of plain concrete
- The addition of fibers increases fatigue strength
- Fibers increase the shear capacity of reinforced concrete beams
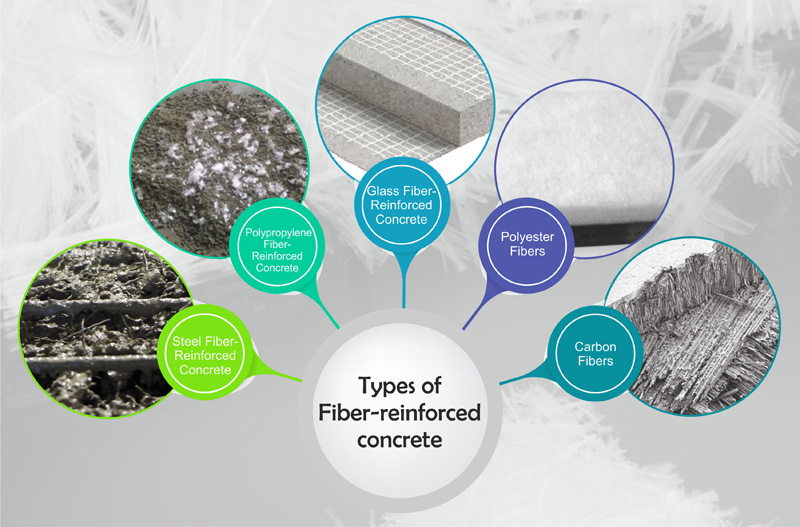
Different types of Fiber-reinforced concrete
Fibers for concrete are available in different sizes and shapes. The major factors affecting the characteristic of fiber-reinforced concrete are a water-cement ratio, percentage of fibers, diameter and length of fibers. Given below are different types of fiber-reinforced concrete used in construction.
Steel Fiber Reinforced Concrete
Steel fiber is a metal reinforcement. A certain amount of steel fiber in concrete can cause qualitative changes in concrete’s physical property. It can greatly increase resistance to cracking, impact, fatigue, and bending, tenacity, durability, and others. For improving long-term behavior, enhancing strength, toughness, and stress resistance, SFRC is being used in structures such as flooring, housing, precast, bridges, tunneling, heavy-duty pavement, and mining. The types of steel fibers are defined by ASTM A820 are, Type I: cold-drawn wire, Type II; cut sheet, Type III: melt-extracted, Type IV: mill cut and Type V: modified cold-drawn wire

Polypropylene Fiber Reinforced (PFR) Concrete
Polypropylene fiber reinforced concrete is also known as polypropene or PP. It is a synthetic fiber, transformed from propylene, and used in a variety of applications. These fibers are usually used in concrete to control cracking due to plastic shrinkage and drying shrinkage. They also reduce the permeability of concrete and thus reduce the bleeding of water. Polypropylene fiber belongs to the group of polyolefins and is partially crystalline and non-polar. It has similar properties as polyethylene, but it is harder and more heat resistant. It is a white rugged material with high chemical resistance. Polypropylene is manufactured from propylene gas in the presence of a catalyst such as titanium chloride. Polypropylene fiber displays good heat-insulating properties and is highly resistant to acids, alkalies, and organic solvents.

Glass Fiber Reinforced Concrete
Glass fiber reinforced concrete is a material consisting of numerous extremely fine fibers of glass. Glass fiber has roughly comparable mechanical properties to other fibers such as polymers and carbon fiber. Although not as rigid as carbon fiber, it is much cheaper and significantly less brittle when used in composites. Glass fibers are therefore used as a reinforcing agent for many polymer products; to form a very strong and relatively lightweight fiber-reinforced polymer (FRP) composite material called glass-reinforced plastic (GRP), also popularly known as “fiberglass”. This material contains little or no air or gas, is denser, and is a much poorer thermal insulator than is glass wool.

Polyester fibers
Polyester fibers are used in fiber-reinforced concrete for industrial and warehouse floors, pavements and overlays and precast products. Polyester micro- and macro-fibers are used in concrete to provide superior resistance to the formation of plastic shrinkage cracks versus welded wire fabric and to enhance toughness and the ability to deliver structural capacity when properly designed, respectively. Polyester micro- and macro-fibers are used in concrete to provide superior resistance to the formation of plastic shrinkage cracks versus welded wire fabric and to enhance toughness and the ability to deliver structural capacity when properly designed, respectively.

Carbon fibers
Carbon fibers are fibers about 5–10 micrometers in diameter and composed mostly of carbon atoms. Carbon fibers have several advantages including high stiffness, high tensile strength, low weight, high chemical resistance, high-temperature tolerance and low thermal expansion. Carbon fibers are usually combined with other materials to form a composite. When impregnated with a plastic resin and baked it forms carbon-fiber-reinforced polymer (often referred to as carbon fiber) which has a very high strength-to-weight ratio, and is extremely rigid although somewhat brittle. Carbon fibers are also composited with other materials, such as graphite, to form reinforced carbon composites, which have a very high heat tolerance.

Macro synthetic fibers
Macro synthetic fibers are made from a blend of polymers and were originally developed to provide an alternative to steel fibers in some applications. Initially, they were identified as a potential alternative to steel fibers in sprayed concrete, but increasing research and development showed that they had a role to play in the design and construction of ground-supported slabs and a wide range of other applications. They are particularly suitable for providing nominal reinforcement in aggressive environments, such as marine and coastal structures, as they do not suffer the problems of staining and spalling that can result from the corrosion of steel. Besides, because they are non-conducting, they have been used in tram and light railway developments.

Micro-synthetic fibers
Micro-synthetic fibers provide superior resistance to the formation of plastic shrinkage cracks versus welded wire reinforcement, they are unable to provide any resistance to further crack width openings caused by drying shrinkage, structural load or other forms of stress. However, these products should be regularly specified in any type of concrete to improve cracking resistance, spall protection, freeze-thaw durability and improve the homogeneity of concrete during placement.

Natural fibers
The natural fiber is directly obtainable from an animal, vegetable, or mineral source and convertible into nonwoven fabrics such as felt or paper or, after spinning into yarns, into woven cloth. A natural fiber may be further defined as an agglomeration of cells in which the diameter is negligible in comparison with the length. Although nature abounds in fibrous materials, especially cellulosic types such as cotton, wood, grains, and straw. The use of natural fibers in making concrete is recommended since several types of these fibers are available locally and are plentiful. The idea of using such fibers to improve the strength and durability of brittle materials is not new; for example, straw and horsehair are used to make bricks and plaster. Natural fibers are suitable for reinforcing concrete and are easily available in developing countries.

Cellulose fibers
Cellulose fibers are made with ethers or esters of cellulose, which can be obtained from the bark, wood or leaves of plants, or other plant-based material. In addition to cellulose, the fibers may also contain hemicellulose and lignin, with different percentages of these components altering the mechanical properties of the fibers. The main applications of cellulose fibers are in the textile industry, as chemical filters, and as fiber-reinforcement composites, due to their similar properties to engineered fibers, being another option for biocomposites and polymer composites.

Application of Fiber-reinforced concrete

The applications of fiber reinforced concrete depend on the applicator and builder in taking advantage of the static and dynamic characteristics of the material. Some of its area of application is-
- Runway
- Aircraft Parking
- Pavements
- Tunnel Lining
- Slope Stabilization
- Thin Shell
- Walls
- Pipes
- Manholes
- Dams
- Hydraulic Structure
- Elevated decks
- Roads
- Bridges
- Warehouse floors
Conclusion
Durability to aesthetics fiber-reinforced concrete can add benefits to your project. Fiber-reinforced concrete has been rapidly growing throughout the building industry since contractors and homeowners started to recognize its many benefits. Fibre Reinforced Concrete is gaining an increasing interest among the concrete community for the reduced construction time and labor costs. Besides cost issues, quality matters are of paramount importance for construction and fiber-reinforced concrete also fulfills these requirements.
Image Source: rejuvaflooring.com, sciencedirect.com, researchgate.net, jeccomposites.com, tunneltalk.com, denaworld.com, frontiersin.org, tmrresearchblog.com,