Potholes are not only dangerous, but they are also a major source of inconvenience for commuters. A pothole is a type of road defect that occurs when the surface of a road or pavement deteriorates, creating cracks. Potholes are typically formed due to a combination of factors, including weather conditions, heavy traffic, poor construction or maintenance, and the age of the road surface. India’s pothole problem is a major issue that affects the safety and mobility of millions of people. The problem is not only restricted to a few states, but it is a nationwide issue.
How potholes are formed and what are its causes?
The process of pothole formation often begins with small cracks in the road surface. These cracks allow water to seep into the underlying layers, such as the base and subbase. When the water freezes during cold weather, it expands, putting pressure on the pavement and causing it to crack further. As traffic passes over the weakened area, the pavement can break apart, leading to the formation of a pothole.
Potholes occur on roads due to a combination of several factors, including:
1. Water Ingress: When water seeps into the cracks and pores of the road surface, it weakens the underlying layers. During colder weather, the water freezes and expands, exerting pressure on the pavement and causing it to crack further.
2. Traffic Load: Heavy traffic, particularly from vehicles such as trucks and buses, puts stress on the road surface. Over time, the repeated weight and movement of vehicles can weaken the pavement and lead to the development of cracks and potholes.
3. Age and Wear: Roads deteriorate naturally over time due to aging and wear. As the road surface ages, it becomes more susceptible to damage from traffic, weather, and other factors. The constant exposure to sun, rain, and temperature variations causes the road materials to weaken and break down, leading to the formation of potholes.
4. Poor Construction or Maintenance: Inadequate construction techniques, such as improper compaction of layers during road construction, can contribute to the formation of potholes. Similarly, if roads are not adequately maintained, such as neglecting to fill cracks and repair damaged areas, potholes are more likely to develop.
5. Weather Conditions: Extreme weather conditions, such as heavy rainfall or intense freeze-thaw cycles, can accelerate the formation of potholes. Excessive rainwater can infiltrate the road layers, weakening the pavement structure. Freeze-thaw cycles, where water freezes and thaws repeatedly, further exacerbate cracking and damage.
6. Subsurface Issues: Problems in the underlying layers of the road, including inadequate base or subbase support, poor drainage, or soil instability, can contribute to pothole formation. These subsurface issues weaken the road structure and make it more prone to developing potholes.
Other than the above-mentioned causes, there could be other factors that can contribute to pothole development such as;
- Diesel (or other chemical) spillages.
- Damage caused by falling rocks in cuttings
- Insufficient drainage
- Failures at utility trenches and castings (manhole and drain casings)
- Pavement defects and cracks left unmaintained and unsealed
To address the potholes across the country different types of pothole machines are used.
Pothole patching machines for road repair
Pothole repair machines play a crucial role in India, where the road network is extensive and faces significant challenges related to potholes. Pothole repair machines enable efficient and timely repairs of potholes. With the ability to quickly prepare and apply repair materials, these machines help minimise the time required to fix potholes. This is especially important in India, where heavy traffic congestion is common, and road closures for repairs can cause significant disruptions and inconvenience to commuters.
Types of pothole repair machines
Truck-mounted patcher for pothole repair
A truck-mounted pothole patcher is a type of pothole repair equipment that is mounted on a truck chassis. It combines the convenience of a truck with the functionality of a pothole patching machine. The truck-mounted design allows for easy transportation of the pothole patcher to different work sites. The machine is integrated onto a truck chassis, providing the ability to move between locations efficiently.
The truck-mounted pothole patcher has a hopper or material storage compartment where the patching material, such as hot mix asphalt or proprietary patching mix, is stored. The hopper capacity can vary depending on the size and model of the machine.The patching material is delivered and distributed using pneumatic or hydraulic systems. Truck-mounted pothole patchers are equipped with a heating system to maintain the patching material at an optimal temperature. This ensures the material remains workable and can be easily applied to the pothole. The heating system may use propane burners, electric heaters, or other methods to heat the patching material.The truck-mounted patcher has a patching mechanism, such as a spray bar or nozzle, that applies the patching material into the pothole. This mechanism ensures proper placement and coverage of the patching material.
Truck-mounted pothole patchers have controls and instrumentation located in the operator’s cab. These controls allow the operator to adjust various parameters, such as material flow rate, heating temperature, patching depth, and compaction force. The operator can control the patching process from within the cab for convenience and safety. They are commonly used by road maintenance crews, municipalities, and contractors for pothole repair operations.

Patch fill automated pothole repair machines
Patch fill machine is specially built to work on roads in areas having width limitations, small city streets, hilly roads etc, however due to its compactness it can be efficiently used on major roads and expressways to tackle the Pothole problem at its start and to prevent it from progressing to bigger potholes like pavement distress and base failure. With a choice of very compact chassis for better maneuverability, this machine has exceptional work quality with a variety of materials and climatic work conditions. With maximum Indian components, this machine is built tough with easy to control instrumentation to ensure operator friendly work environment.
With simple electronic process control based on PLC, the operation of this machine is simple through Touch Screen HMI. First in its class, the electronic calibration console is integrated with the operation program for easy and accurate estimation of each individual component output. Pneumatic synchronization of dosing operation ensures best operator compliance. The high efficiency single shaft multi paddle pug mill ensures best mixing of components before their discharge into the pothole.
Apart from PLC based automated sequencing, special provisions have been done for electronic override and control of dosing of twin components to ensure real time control of mix consistency. This machine is built strong with simple yet powerful mixer, chemical resistant paint coated pipelines, stainless steel tanks, antistrip anti-scratch coating on aggregate bin etc., apart from pneumatically operated valves and system integration.

Spray injection pothole repair machines
A spray injection pothole patcher uses a combination of compressed air and specialized emulsion or asphalt mix to clean and repair potholes. Spray injection patchers have a hopper or storage compartment where the patching material, usually an emulsion or asphalt mix, is stored. The hopper capacity can vary depending on the size and model of the machine. Spray injection patchers use a high-pressure air and/or water system to clean the pothole before repair. This system removes loose debris, water, and other contaminants from the pothole, providing a clean surface for better adhesion of the patching material.
Spray injection patchers have a delivery system that combines compressed air and the patching material to repair the pothole. This can involve a specialized nozzle or spray bar that injects the patching material into the pothole, ensuring it fills the void and bonds with the surrounding pavement. Spray injection patchers utilize a compressed air system to propel the patching material into the pothole.
Spray injection patchers have user-friendly controls that allow the operator to adjust parameters such as material flow rate, air pressure, compaction force, and other settings. The operator can control the patching process and monitor the machine’s performance.

Infrared pothole repair machines
Infrared pothole repair machines are specialised equipment used for repairing potholes using infrared technology. These machines utilise heat generated by infrared rays to heat and recondition the existing asphalt in and around the pothole, enabling seamless patching. Here are the key features and benefits of infrared pothole repair machines:
The machines are equipped with infrared heating panels or elements that emit infrared rays. These rays penetrate the damaged asphalt surface, heating it to a controlled temperature. The infrared rays penetrate several inches into the existing asphalt, softening the material and allowing it to be reworked and recompacted. Infrared technology enables the existing asphalt to be blended seamlessly with the new asphalt or repair material. This results in a strong bond between the repaired area and the surrounding pavement, reducing the likelihood of future pothole formation at the same spot.
Infrared pothole repair is generally faster than traditional methods. The heat from the infrared panels accelerates the heating and cooling process, reducing repair time and enabling quicker reopening of the road to traffic. Infrared pothole repair machines offer a versatile and efficient solution for repairing potholes. They are commonly used by road maintenance crews, municipalities, and contractors due to their ability to deliver high-quality repairs in a timely and cost-effective manner.

Combination mastic machine for pothole repair
A combination mastic machine is a specialized equipment used for pothole repair that combines the functions of a pothole patcher and a mastic or asphalt mixer. A combination mastic machine has a built-in mixing system that blends asphalt or mastic materials with aggregates and additives. This allows for on-site production of the mastic material, ensuring freshness and optimal composition. The machine can mix various types of materials, including hot mix asphalt, cold mix asphalt, rubberized asphalt, and proprietary mastic mixes. This versatility allows for customized material formulations based on the specific needs and conditions of the pothole repair.
Once the mastic material is mixed, the combination mastic machine typically has a delivery system that applies the mixture directly into the pothole. This results in efficient and precise placement of the mastic, minimizing material waste and maximizing repair quality. The combination mastic machine enables fast pothole repair due to its integrated mixing and application capabilities. The on-site production of the mastic material and its immediate application reduce the time required for repair, minimizing traffic disruption and enhancing road user safety.
The mastic material produced by the combination machine is designed to be highly durable and long-lasting. It forms a strong bond with the existing pavement, providing a reliable repair solution that resists cracking, rutting, and deterioration over time. Combination mastic machines are commonly used in road maintenance operations, particularly for repairing potholes in asphalt pavements. Their ability to mix and apply mastic materials on-site provides a convenient and effective solution for achieving durable and long-lasting pothole repairs.
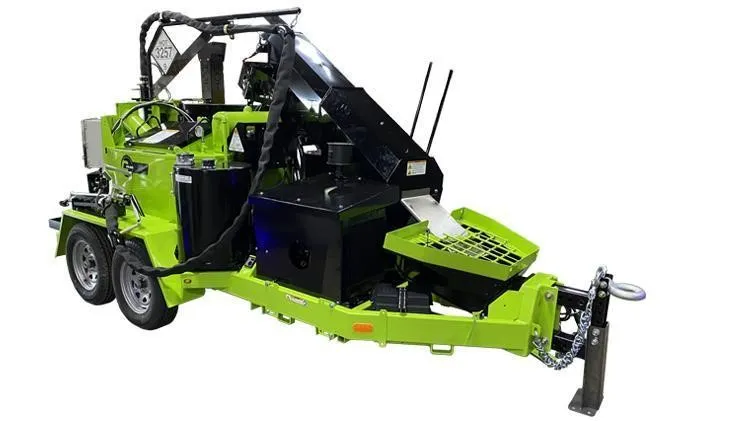
Road milling machines for pothole repair
Road milling machines, also known as cold milling machines or asphalt milling machines, are commonly used for road maintenance and rehabilitation, including pothole repair. While they are primarily used for removing old or damaged asphalt layers, they can also be utilized for preparing potholes for repair. Here are some key points about road milling machines for pothole repair: Road milling machines use rotating drum cutters with specially designed teeth to remove the top layers of asphalt or concrete. This process creates a rough surface and removes damaged areas, including potholes, to prepare the road for repair.
Road milling machines can be used to mill around and within potholes, effectively removing the damaged asphalt material. This prepares the pothole for subsequent repair by creating clean edges and a stable base for the patching material.Road milling machines come in various sizes, from compact models suitable for small roads and tight spaces to larger machines for major road rehabilitation projects. This versatility allows them to address different pothole sizes and road conditions.
Modern road milling machines offer advanced features and controls that enable precise milling operations. Operators can adjust the milling depth, speed, and other parameters to ensure accurate removal of the damaged asphalt layers and proper preparation of the pothole.Road milling machines are designed for high productivity, allowing for efficient removal of damaged asphalt and rapid preparation of potholes. Their robust construction and powerful engines enable them to handle tough road surfaces and expedite the repair process.
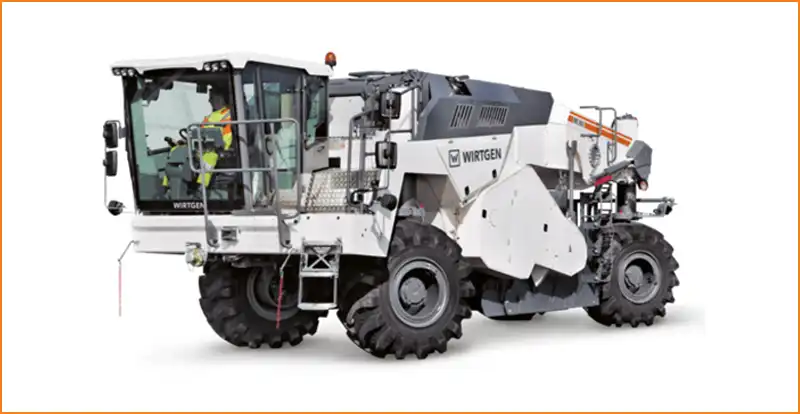
Conclusion
Pothole repair machines play a vital role in ensuring that roads remain in good condition. Pothole repair machines enable road maintenance crews, municipalities, and contractors to proactively address potholes, preventing them from becoming larger and more costly issues. Given the size and complexity of India’s road network, investing in pothole repair machines can significantly improve the overall condition of roads and enhance road safety.
Image Source: speedcrafts.com, petrochemsp.com, tpsmfg.com, metalite.in, Neha Infra Services, timlin.com wirtgen-group.com/en-in/, cimline.com