Chemical anchors are fastening systems used to create a strong and reliable bond between an anchor and a base material. They are commonly used in construction and engineering applications where high load capacity and long-term durability are required.Chemical anchors consist of two main components: a resin adhesive and a hardener. These components are typically supplied as separate materials and are mixed together just before installation. The mixing process initiates a chemical reaction that causes the resin to cure and harden, creating a strong bond with the base material.
Advantages of chemical anchors
Chemical anchors offer several advantages that make them a popular choice in construction and engineering applications. Here are some of the key advantages of chemical anchors:
1. High Load Capacity: Chemical anchors provide a strong and reliable bond between the anchor and the base material, resulting in high load-bearing capacity. They are capable of withstanding significant loads and forces, making them suitable for securing heavy structural elements and equipment.
2. Versatility: Chemical anchors can be used with various base materials, including concrete, masonry, stone, and even some types of wood. This versatility allows for their use in a wide range of applications and construction projects.
3. Durability: Once cured, chemical anchors offer long-term durability and resistance to environmental factors such as moisture, temperature fluctuations, and chemical exposure. They maintain their strength and performance over time, ensuring the stability and integrity of the anchored elements.
4. Improved Load Distribution: The chemical adhesive used in chemical anchors helps distribute the load evenly across the base material. This feature reduces stress concentrations and minimizes the risk of localized failure, improving the overall structural integrity.
5. Easy Installation in Deep or Overhead Applications: Chemical anchors are especially useful in deep or overhead applications where mechanical anchors may be difficult to install or may not provide sufficient holding power. The fluid nature of the adhesive allows it to reach and bond with the entire depth of the drilled hole, ensuring a secure connection.
6. Increased Flexibility: Chemical anchors allow for adjustments and corrections during the installation process. Unlike mechanical anchors that require precise alignment and positioning, the fluid nature of the adhesive allows for slight adjustments before the curing process begins.
Types of chemical anchors
There are several types of chemical anchors available, each with its own characteristics and applications. Here are some common types of chemical anchors:
1. Epoxy Adhesive Anchors: Epoxy anchors are widely used in construction and engineering applications. They consist of a two-part epoxy resin that is mixed together before installation. Epoxy anchors offer excellent bonding strength, chemical resistance, and load-bearing capacity. They are suitable for high-stress applications and can be used with various base materials such as concrete, masonry, and stone.
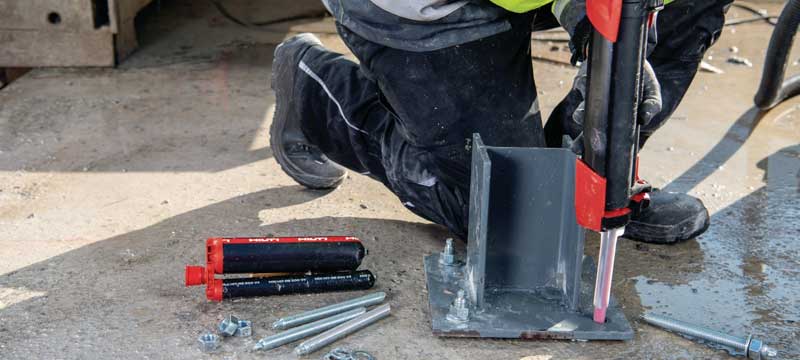
2. Vinylester Adhesive Anchors: Vinylester anchors use a vinylester resin instead of epoxy. They provide similar properties to epoxy anchors, including high strength and chemical resistance. Vinylester anchors are often preferred in environments where exposure to chemicals or corrosive substances is a concern.
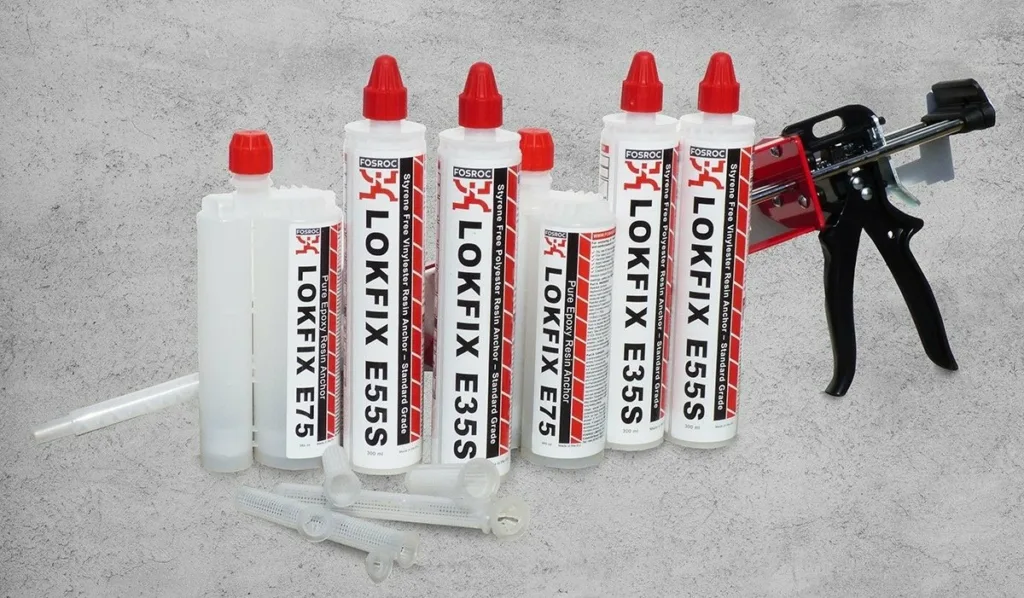
3. Polyester Adhesive Anchors: Polyester anchors use a polyester resin for bonding. They are typically used in non-structural applications and offer a more cost-effective option compared to epoxy or vinylester anchors. Polyester anchors are suitable for light to medium load applications.
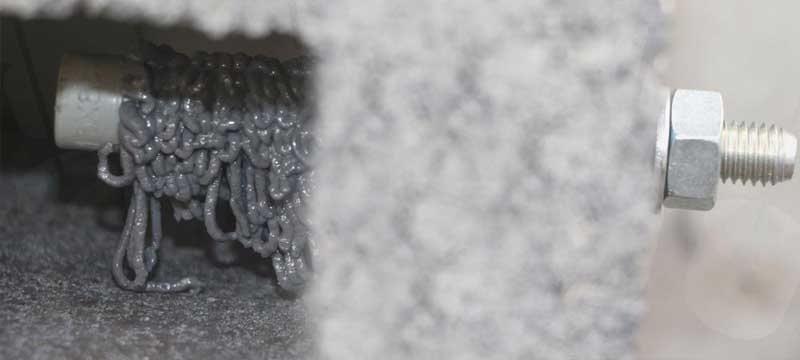
4. Acrylic Adhesive Anchors: Acrylic anchors use an acrylic-based adhesive for bonding. They are known for their fast curing times and are often used when a quick installation is required. Acrylic anchors are suitable for lighter load applications and can be used with materials such as concrete, masonry, and some types of stone.
5. Pure Cementitious Anchors: Pure cementitious anchors consist of a cement-based material that is mixed with water and used as an adhesive. They rely on the hydration and setting of the cement to create a bond. Cementitious anchors are commonly used in non-structural applications and for fixing rebar in concrete.
6. Hybrid Adhesive Anchors: Hybrid anchors combine two or more types of adhesive materials to achieve enhanced performance. For example, a hybrid anchor may incorporate a combination of epoxy and cementitious elements to provide high load capacity, fast curing, and improved chemical resistance.

How to install chemical anchors?
The application method for chemical anchors typically involves the following steps:
1. Surface Preparation: Ensure that the surface where the chemical anchor will be installed is clean, free from dust, debris, grease, or any loose particles. Use a wire brush, compressed air, or other appropriate cleaning methods to prepare the surface.
2. Drilling: Drill a hole into the base material using the recommended diameter and depth specified by the manufacturer. The hole should be clean and free of any obstructions. The depth of the hole is typically determined by the length of the anchor and the required embedment depth.
3. Cleaning: Thoroughly clean the drilled hole to remove any drilling dust or debris. Use a brush or compressed air to ensure the hole is clean and ready for the adhesive.
4. Mixing: Follow the manufacturer’s instructions to mix the two-part adhesive system. The adhesive typically consists of a resin and a hardener. Mix them in the correct ratio and use a suitable mixing container and mixing tool. Thoroughly mix the components until a homogeneous mixture is obtained.
5. Injection: Use a suitable injection system, such as a cartridge or specialized injection gun, to inject the mixed adhesive into the drilled hole. Insert the nozzle of the injection system into the hole and apply pressure to ensure the adhesive fills the hole completely.
6. Anchor Insertion: While the adhesive is still fluid, insert the anchor into the hole. Rotate or push the anchor to ensure it is fully surrounded by the adhesive and that there are no voids or air pockets. Ensure the anchor is inserted to the desired depth and alignment.
7. Curing: Allow the adhesive to cure according to the manufacturer’s instructions. Curing times can vary depending on the specific adhesive and environmental conditions. It is crucial to adhere to the recommended curing time before applying any load or stress to the anchor.
8. Finishing: After the adhesive has fully cured, any excess adhesive that may have squeezed out of the hole can be removed using appropriate tools or methods. Ensure that the anchor and surrounding area are clean and free from adhesive residues.
It is important to note that the application method can vary depending on the specific manufacturer, adhesive system, and project requirements. Always refer to the manufacturer’s instructions and consult with professionals experienced in chemical anchor installation for the best practices and specific guidance.
Uses of chemical anchors
Chemical anchors are versatile and widely used in various construction and engineering applications. Some common applications of chemical anchors include:
1. Structural Connections: Chemical anchors are extensively used for structural connections in building and infrastructure projects. They provide a reliable and durable bond for connecting steel columns, beams, and structural members to concrete or masonry elements.
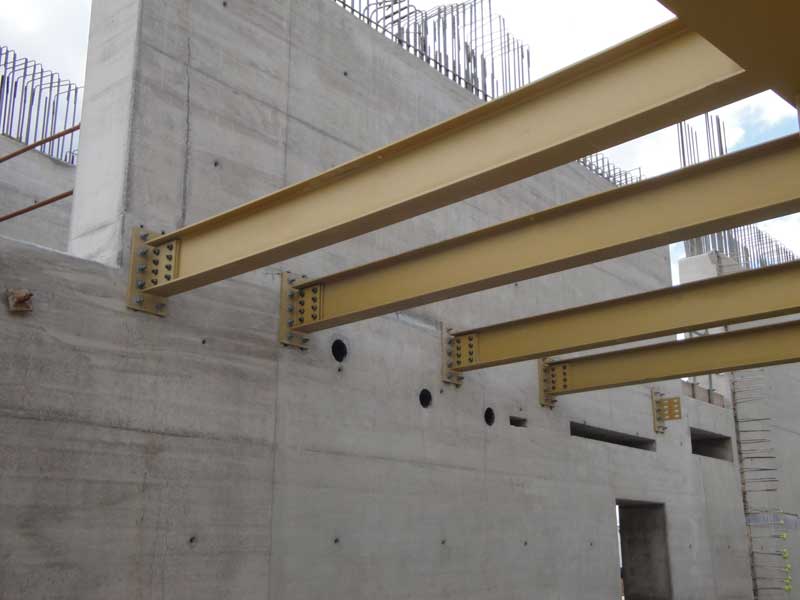
2. Façade Systems: Chemical anchors are used in the installation of façade systems, such as curtain walls, cladding, and external insulation systems. They secure the façade components to the underlying structure, ensuring stability and load transfer.
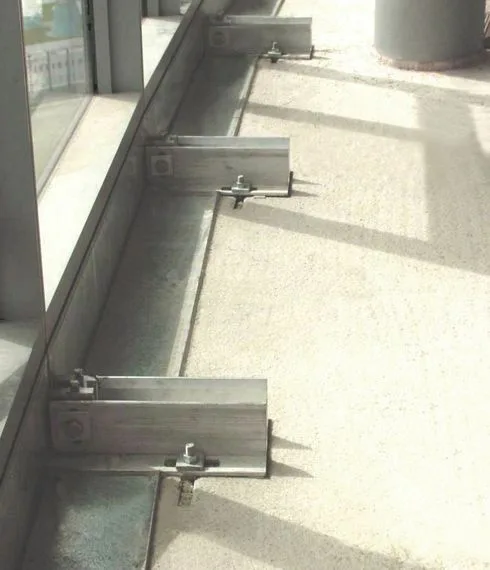
3. Anchoring Machinery and Equipment: Chemical anchors are employed to anchor heavy machinery, equipment, and fixtures to the floor or foundation. They provide a secure connection and prevent movement or vibrations during operation.
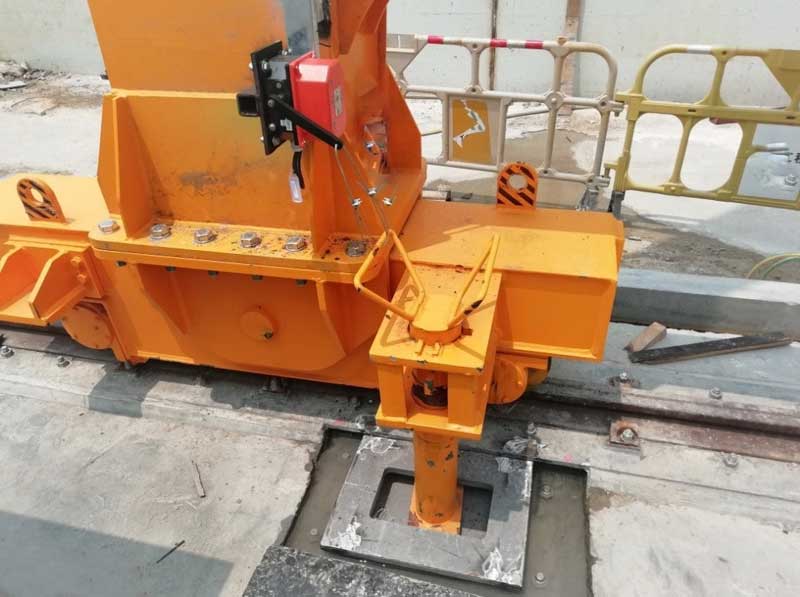
4. Bridge Construction and Repair: Chemical anchors are used in bridge construction and repair projects. They secure bridge components, such as guardrails, expansion joints, and concrete barriers, to the bridge deck and substructure.
5. Reinforcement and Strengthening: Chemical anchors are utilized in concrete reinforcement and strengthening applications. They anchor reinforcing bars (rebar) into existing concrete structures, increasing their load-bearing capacity and structural integrity.
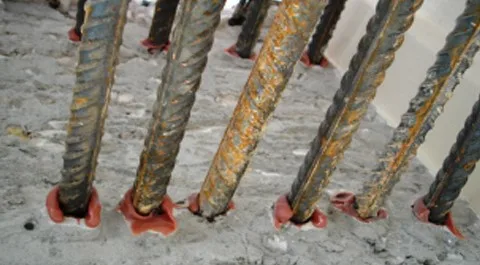
6. Fixing Handrails and Balustrades: Chemical anchors are employed to fix handrails, balustrades, and guardrails in staircases, balconies, and walkways. They provide a secure and stable attachment, ensuring safety for users.
7. Seismic Retrofitting: Chemical anchors are used in seismic retrofitting projects to enhance the structural stability and resistance of buildings and infrastructure. They anchor structural elements, such as steel braces or reinforcement, to existing concrete or masonry elements.
8. Anchoring Signage and Street Furniture: Chemical anchors are employed to anchor signage, street furniture, and urban elements like bollards and bike racks to the ground. They ensure the stability and security of these installations in public spaces.
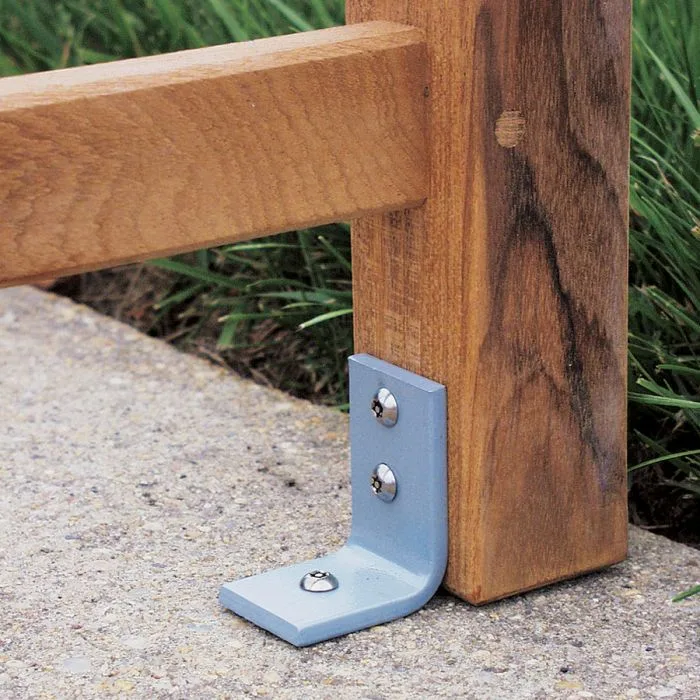
9. Pipe and Cable Supports: Chemical anchors are used for securing pipe and cable supports to walls, ceilings, or floors. They provide a strong attachment point for the supports, preventing movement and ensuring the integrity of plumbing or electrical systems.
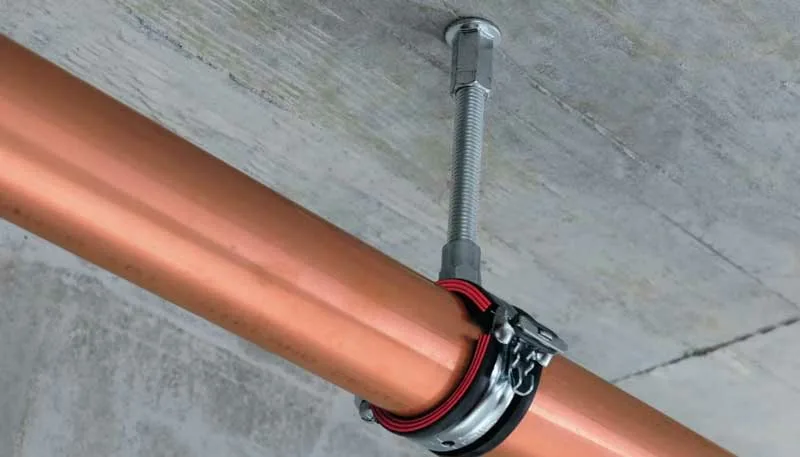
10. Anchoring Safety Systems: Chemical anchors are employed in safety systems such as fall arrest anchors and lifeline systems. They securely anchor the safety equipment to the structure, protecting workers at heights.
Conclusion
Chemical anchors are highly effective and versatile solutions for various construction and engineering applications. They provide exceptional load-bearing capacity and durability, making them suitable for both light-duty and heavy-duty applications.
Image Source: hilti.in, fosroc.com, cranedge.com