In the heart of the Earth’s embrace, where the secrets of underground infrastructure are unveiled, lies an engineering marvel that moves with precision and grace – the rotating tunnel boring machine (TBM). As the world’s ambitions for subterranean projects grow bolder, this innovative marvel emerges as the conductor of an underground symphony, orchestrating the seamless ballet of tunnel construction. With a mesmerizing pirouette, the rotating TBM defies traditional tunneling limits, unlocking a realm of possibilities and paving the way for faster, safer, and more efficient excavation journeys.
In this context, the Silvertown Tunnel project in London employed a pioneering nitrogen skate system to gracefully rotate the United Kingdom’s largest TBM by a full 180 degrees. This distinctive approach showcased its remarkable efficiency and cost-effectiveness, unfurling avenues for future large-scale TBM rotations while curbing disruptions to proximate assets.
About Silvertown Tunnel project
The Silvertown Tunnel project is a major infrastructure initiative located in London, United Kingdom. It aims to address the increasing demand for transport capacity in the east of the city by creating a new road tunnel under the River Thames. The project is aimed to alleviate traffic congestion, improve connectivity, and enhance transportation options in the area.The project involves the construction of a twin-bore road tunnel, which will accommodate vehicles travelling in both directions. The tunnel will be equipped with modern infrastructure and safety features.
Transport for London (TfL) awarded the project to Riverlinx consortium, comprising Ferrovial subsidiary Cintra, Abrdn, Invesis, Macquarie Capital and SK Ecoplant, the monumental task of carving a twin-bore tunnel beneath the River Thames, connecting Silvertown on the northern bank with Greenwich on the southern, in a venture valued at £1 billion.

Nitrogen skate system for TBM rotation
Nitrogen skates are specialised hydraulic devices designed to facilitate the smooth and precise rotation of tunnel boring machines. By utilising compressed nitrogen gas, these skates create a cushion of air that reduces friction between the TBM and the surrounding surfaces, allowing for controlled movement. This innovation has significantly enhanced the feasibility of rotating large TBMs, which is a critical requirement in many tunneling projects.
Advantages of Nitrogen Skates:
- Friction Reduction: The cushion of compressed nitrogen minimises friction between the TBM and the tunnel walls, reducing wear and tear on both the machine and the tunnel structure.
- Precise Control: Enable precise control over the TBM’s rotation, ensuring accurate alignment and excavation within the tunnel.
- Efficiency: Smooth and controlled rotation optimises TBM performance, leading to more efficient excavation processes and potentially faster project completion.
- Minimised Wear: Reduced contact and friction translate to less mechanical stress and wear on the TBM’s components, prolonging its operational lifespan.
- Minimised Disruption:Using nitrogen skates can lead to smoother and quieter TBM operation, minimising disturbances to nearby structures and communities.
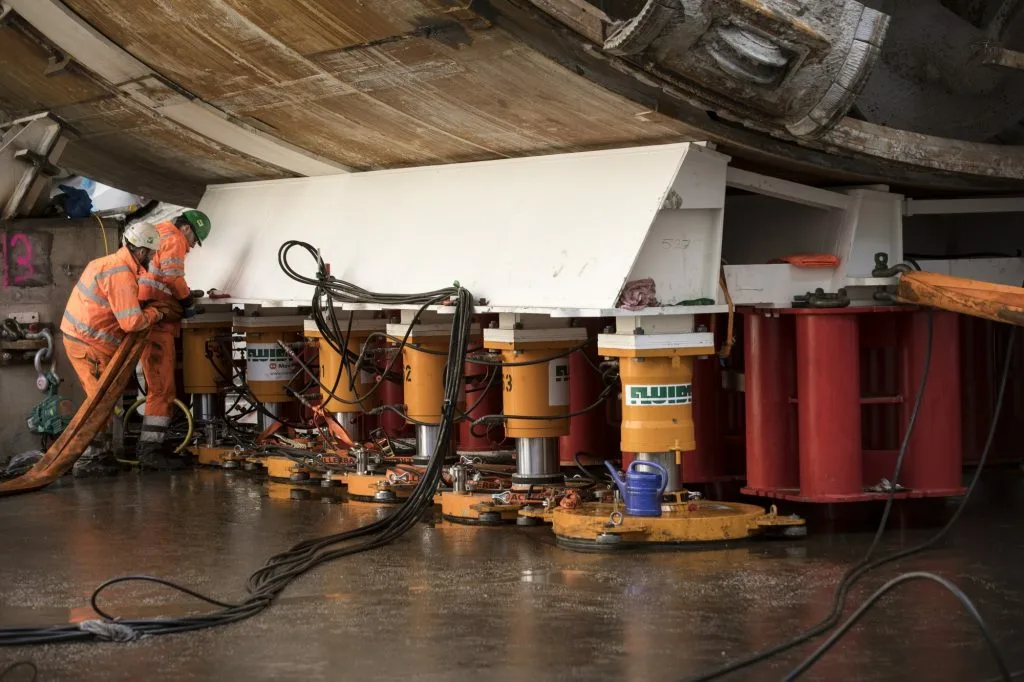
How does the nitrogen skate system work?
- Step 1; Nitrogen Skate Placement: Nitrogen skates are positioned beneath the TBM sections. These skates consist of hydraulic feet equipped with rubber skirts, with compressed nitrogen pumped into the base of each skate.
- Step 2; Rotation Process: The hydraulic system is turned off, allowing the TBM sections to rest on the cushion of compressed nitrogen. The skates facilitate smooth and controlled rotation of the TBM.
- Step 3; Adjustment and Reassembly:** Throughout the rotation process, adjustments are made to ensure proper alignment. Once rotated, the TBM sections are reassembled, and the machine is prepared for its next phase of tunneling.
Why was the Nitrogen Skate system selected for TBM rotation for the Silvertown Tunnel project?
“It’s the first time a machine of this size has been rotated using nitrogen skates,” said Riverlinx operations director Borja Trashorras. “We have just finished rotating the first section of the TBM outside the southern portal so it can begin the second bore. Out of three available options, that was the most efficient “from a cost perspective and a time perspective”, he further explained.
Other options included the use of two TBMs, but powering two separate machines would have been less cost-efficient. The second option was using one TBM and returning it to the original side, which could have added months onto the completion date. “That would involve stripping [the TBM] down and reinstalling it all with lifting gear, [so] you might be talking about five or six months,” Trashorras says.
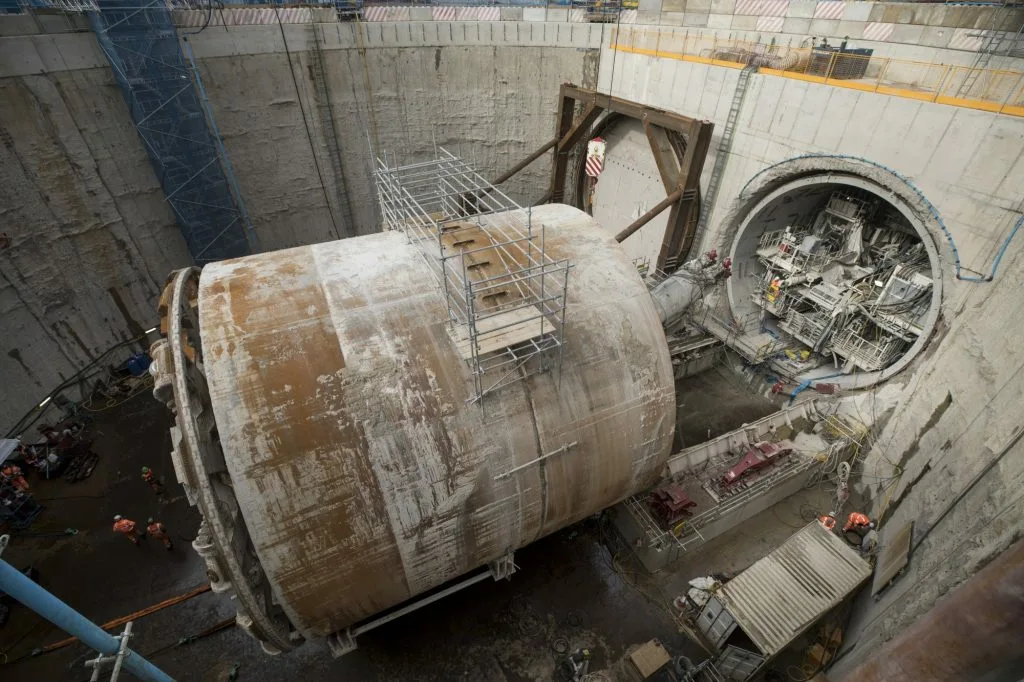
How was the Nitrogen skate system used for the Silvertown Tunnel project?
Only about 12 bottles of nitrogen were needed for the TBM rotation, significantly reducing the cost and supply obstacles. The nitrogen significantly reduced friction between the steel plates and the TBM, allowing the 1,400-tonne machine to be pulled out and rotated in just eight hours using remote pendant control and 25-tonne chain pulls.
Nitrogen skate system was chosen as it is readily available, inert, non-poisonous, and lighter than air. It provided an efficient and cost-effective solution for turning the TBM. Client Transport for London expressed satisfaction with the outcome and stated there is no reason why nitrogen skates can’t be used again.
Application of Nitrogen Skate System:
The Silvertown TBM, being larger than the machines used in Paris and Stuttgart, required innovative engineering. Steel plates were installed at the base of the rotation chamber, providing a smooth surface. Nitrogen served the purpose of reducing friction between the steel plate and the TBM, enabling the 1,400-tonne machine to be pulled out and turned within approximately eight hours using 25-tonne chain pulls controlled remotely.
Smooth and Precise TBM Rotation:
The TBM emerged in Greenwich at a 4-degree angle after its journey under the Thames. Using the nitrogen skates placed underneath and bolted into position, the machine was floated on top of a steel cradle. The hydraulic system was utilized to level the TBM entirely horizontal, preparing it for the 180-degree turn.
Efficient use of Nitrogen Skate System:
The nitrogen skates, equipped with hydraulic feet, allowed the TBM to hover or “skate” on the smooth steel surface. The hydraulic system was then locked off, and the nitrogen skates were employed to move the TBM forward and sideways in two turns, positioning it for the second tunnel boring. Meanwhile, the tunnel behind the TBM was fitted out with concrete for the road deck and low-point sumps to pump water out of the tunnel.
According to Riverlinx project manager Ivor Thomas, the nitrogen skate system proved highly efficient. “We would probably need to hire all of the air compressors in the UK to make that [method] a success,” he said, highlighting the simplicity and cost-effectiveness of using nitrogen instead. Transport for London, the client for the project, expressed satisfaction with the outcome and stated that nitrogen skates could be employed again in the future.
The “Flying Launch” System: Streamlined TBM Deployment
The unique approach involved installing steel plates on the TBM’s rotation chamber, allowing it to slide smoothly on a nitrogen-aided surface. Nitrogen was used to minimize friction between the steel plate and the TBM, making it easier to pull out and rotate the 1,400-tonne machine within approximately eight hours. The process required hydraulic feet and compressed nitrogen to move the TBM, achieving a UK-first accomplishment in large-scale TBM rotation.
The Silvertown project introduced another groundbreaking concept – the “flying launch” system. Departing from conventional launch methods, this innovative system eliminated the need for a temporary tunnel and optimized space utilization. By constructing the propulsion frame close to the tunnel eye, the TBM shield was drawn forward using a combination of a steel pressure ring, tension bars, and hydraulic jacks. This approach reduced the need for space-consuming infrastructure, making it particularly suitable for constrained sites. The process involved a phased approach where the TBM initially bored a segment of the drive, followed by the addition of the remaining gantries. Once reassembled, the TBM entered “full mode” and embarked on its northbound journey. This efficient and space-saving technique showcased the capacity of modern engineering to innovate and streamline tunnel construction.
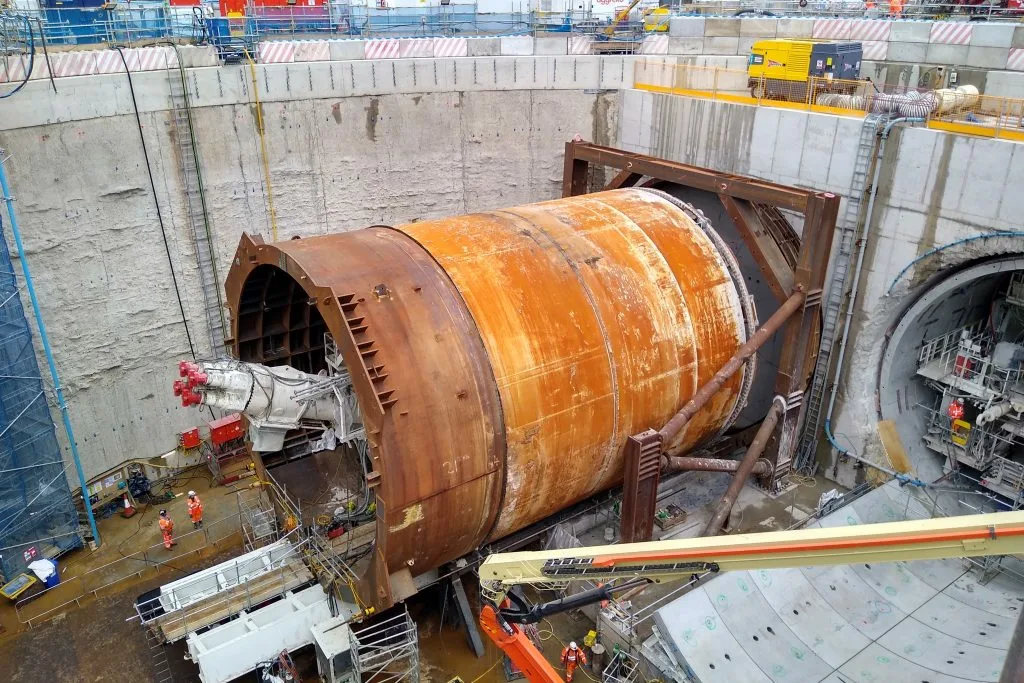
Challenges and Innovations in Ground Freezing
Beyond TBM rotation, the Silvertown project tackled the complex issue of challenging ground conditions beneath the Thames. The mixed face and high water content of the ground posed difficulties. To address challenging ground conditions beneath the Thames, ground freezing techniques were used. By freezing water-saturated sediments, the project team created a stable environment for safe cross-passage excavation. Notably, the Silvertown project took a unique approach by integrating temporary propping directly into the cross passage linings, eliminating the need for traditional propping methods.
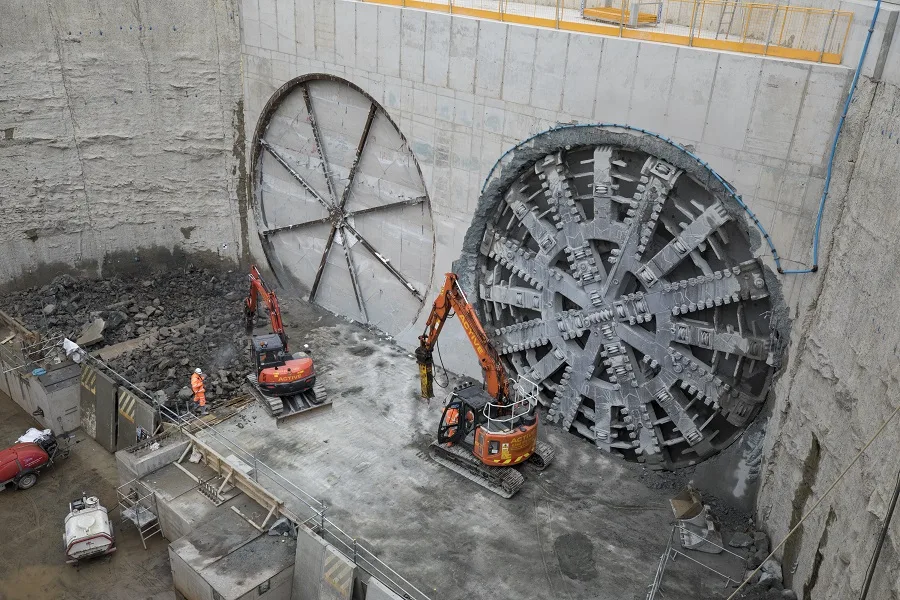
UK Firsts and Minimal Disruptions:
The Silvertown TBM is the first of its size used in the UK and the first time a machine this large has been rotated using nitrogen skates. The project achieved its ambitions at the southern portal by not disrupting nearby assets, including the O2 car park above part of the tunnel. This efficient fit-out program garnered interest from clients looking to follow Riverlinx’s footsteps, impressed by the savings in time, cost, and materials.
One of the key ambitions at the southern portal was to not disrupt a host of nearby assets, including the car park at the O2, which will be above part of the tunnel. “We’ve done all the design and professional work without affecting any third parties,” Trashorras says, which included Thames Water, UK Power Networks and National Grid Transco. “When you have a concert in the O2, you can imagine that the car park is flooded with people.”
Environmentally Responsible Disposal:
To ensure environmentally responsible disposal, the spoil, amounting to 600,000 tonnes, was transported by barges down the Thames to the Ingrebourne Valley nature park, where it will be used to restore local areas into sustainable sites. This approach reflects the project’s commitment to minimizing its ecological impact.
Conclusion
In the realm of tunnel construction, innovation is driving progress. The application of nitrogen skates for TBM rotation and the implementation of ground freezing to overcome challenging ground conditions demonstrate the potential of modern engineering to reshape established practices. These techniques, borne out of collaboration, ingenuity, and technological advancement, are redefining the future of tunnel construction.
References; Constructionnews.co.uk, geplus.co.uk