Fibers have emerged as a game-changing product in the realm of 3D concrete printing, sparking a paradigm shift in construction methodologies. These microscale reinforcements, typically composed of materials like steel, polymers, or carbon, are seamlessly integrated into the concrete mixture, endowing it with enhanced mechanical attributes and heightened durability. As layers of concrete are precisely deposited, the fibers interlace to form a robust lattice, imparting remarkable tensile strength, crack resistance, and structural integrity.
Within the realm of 3D concrete printing, fiber-reinforced composites offer unprecedented versatility and innovation. Strategically embedded fibers work in tandem with the concrete matrix, bolstering its capacity to withstand forces and deformations. This synergistic relationship between fibers and concrete enables engineers and designers to realize previously unattainable structures through additive manufacturing techniques There are different types of fibers used for 3D concrete printing, Polypropylene Monofilament Fibers are one of the most preferred ones.
Polypropylene Monofilament Fibers in 3D Concrete Printing
Polypropylene Monofilament Fibers are a type of synthetic fiber that can be utilized in the context of 3D concrete printing to enhance the properties of the printed structures. These fibers are commonly added to the concrete mixture to improve its mechanical performance and durability. These fibers act as micro-reinforcements within the concrete matrix, helping to distribute and dissipate stresses. This results in improved crack resistance, which is particularly crucial for 3D printed structures that may be subjected to various loads and environmental conditions. The addition of these fibers can also improve the workability of the concrete mixture, making it easier to handle during the printing process. This can lead to smoother printing and better-quality control.
*Fiber Compatibility: Not all Polypropylene Fibers are compatible with all types of concrete mixes. Ensuring the right combination is critical for achieving the desired mechanical properties & performance of the printed structures. The right product selection is therefore pivotal.
FIBERCRETE-MF (Synthetic Monofilament Fiber) for 3D printing concrete mix
FIBERCRETE-MF (Synthetic Monofilament Fiber) is one of the most commonly used polypropylene fibers for 3D printing concrete mixes. Comprising of meticulously engineered synthetic polymers, these fibers seamlessly integrate into the concrete matrix, ushering in a new era of structural integrity and durability. As the layers of concrete are deposited in the intricate patterns of 3D printing, Fibercrete MF fibers form a resilient network that disperses stress, effectively reducing the risk of cracks and fractures. This innovation extends beyond reinforcement, as the fibers also contribute to improved flexural strength, bolstering the material’s ability to withstand bending forces. Their ability to mitigate shrinkage-related concerns during curing ensures the longevity and aesthetics of the final 3D printed structures. Furthermore, the fibers play a pivotal role in minimizing the risk of shrinkage-related flaws during the curing process, preserving both the visual appeal and the mechanical performance of the final printed structures

The fiber properties are given in the below table
Parameters | Specifications |
Fiber Material | Polypropylene |
Cross Section | Circular |
Type of Fiber | Monofilament |
Fiber Length | 6 -12 mm |
Equivalent Diameter | < 20 Micron |
Aspect Ratio | > 300 |
Tensile Strength | > 200Mpa |
Advantages of FIBERCRETE-MF (Synthetic Monofilament Fiber)
- Dispersion: Tend to disperse relatively well in concrete mixes, which can be beneficial for achieving uniform homogeneous concrete throughout the printing operations.
- Printability: Monofilament nature of fibers reduces the likelihood of nozzle clogging during the printing process, facilitating a smoother & continuous printing experience.
- Layer Adhesion: Enhances the bond between layers, contributing to improved interlayer adhesion & overall structural integrity.
- Flexibility: Provides a degree of flexibility, which can help in accommodating the movement & stress that structures might experience due to thermal expansion, shrinkage, external forces etc.
- Cost Efficiency: More economical for projects with budget constraints.
- Ease of Handling: Lightweight & easy to handle during printing operations.
Fiber Infused Innovations in 3D Concrete Printing




FIBERCRETE-MF : Synthetic Monofilament Fibers emerge as a groundbreaking concrete fiber, transcending traditional limitations. These fibers, meticulously engineered from synthetic polymers, interlace with the concrete matrix to create an intricate web of strength and resilience.
About Kalyani Polymers Pvt Ltd.
Kalyani Polymers Pvt Ltd. under the brand name FIBERCRETE® offers a World Class Synthetic Micro & Macro Concrete Fiber Products under “MAKE IN INDIA” and “ATMANIRBHAR” to cater the requirements of Construction Sector in India and around the World and carries a valid CE (European Conformity) mark.
Kalyani Polymers has developed an in-depth understanding of trends and requirements, and in accordance developed unique technologies and manufacturing to best meet customers’ requirements. Having Accredited with ISO 9001 from TUV since 2008, Quality, Service and Innovation have been their Pillars of Development.
They have customized Concrete Fibers products for every client, and cater to their needs after a thorough investigation of the requirements and necessities. The company’s ability to continuously expand its product range and apply new techniques to present systems by installing new machines for efficient manufacturing is aided by the ample space to innovate and commercialize new products.
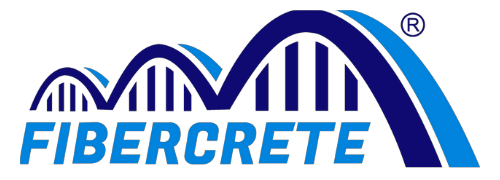
“Neo Fibers For Next Generation Concrete”
FIBERCRETE
46/1, 11th KM Off Kanakapura Road, Doddakalasandra. Bangalore – 560062 Karnataka, INDIA
Phone: +91-80-40991198, +91-80-40991001
Email: sales@fibercrete.in
Website: www.fibercrete.in