Automated clean room doors are specially designed doors equipped with automated mechanisms for opening and closing, often used in facilities that require stringent cleanliness standards. These doors help maintain the cleanliness of the controlled environment by minimizing the potential for contamination that manual opening and closing may introduce. They are typically operated by sensors, push buttons, or remote controls to ensure smooth and controlled access while minimizing human contact.
The components of automated clean room doors typically include:
1. Door Panels: The main physical structure of the door, often made of materials like stainless steel or fiberglass to withstand rigorous cleaning and maintain cleanliness.
2. Automation Mechanism: This includes motors, gears, and sensors that enable the door to open and close automatically in response to triggers such as motion sensors or remote controls.
3. Sealing Systems: Specialized gaskets or seals are integrated into the door frame to ensure an airtight and contaminant-free seal when the door is closed, maintaining the integrity of the clean room environment.
4. Control System: The control system manages the operation of the door, including user interface elements such as push buttons, keypads, or touch screens, as well as the integration with other systems like HVAC or access control.
5. Safety Features: These include presence sensors to prevent the door from closing on a person or object, emergency stop buttons, and alarms to ensure safe operation in the clean room environment.
6. Airflow Management: Some automated clean room doors may have features to control air pressure differentials between rooms, such as interlocking mechanisms to prevent simultaneous opening of adjacent doors, helping to maintain clean room classification levels.
7. Optional Accessories: Depending on the specific requirements of the application, automated clean room doors may include additional features such as windows for visibility, intercom systems, or integration with clean room monitoring and control systems.
Where are automated clean room doors used?
- Pharmaceutical manufacturing facilities
- Semiconductor manufacturing clean rooms
- Biotechnology laboratories
- Hospitals and healthcare facilities
- Food processing and packaging facilities
- Aerospace and precision engineering industries
- Microelectronics manufacturing facilities
- Nanotechnology research labs
- Research and development laboratories for advanced materials
- Optics and photonics laboratories
- Environmental testing facilities for product quality control
- Clean rooms in the cosmetics and personal care product manufacturing industry
- Clean rooms used in the production of medical devices
- Clean rooms in the renewable energy sector, such as for manufacturing solar panels or batteries etc.
Advantages of automated clean room doors
- Enhanced cleanliness and sterility maintenance
- Reduced risk of contamination from human contact
- Controlled access to the clean room environment
- Improved operational efficiency with automated opening and closing
- Compliance with regulatory standards for cleanliness and safety
- Minimized disruption to airflow patterns within the clean room
- Increased safety with built-in sensors and emergency stop features
- Integration with facility monitoring and control systems
- Customizable options to meet specific clean room requirements
- Enhanced convenience for users with remote control or sensor-based operation
- Enhanced security through access control features, such as keycard or biometric authentication
Types of automated clean room doors
1. Sliding Doors
Sliding doors are designed to open and close horizontally along a track system, making them an excellent choice for areas with limited space. Their smooth, space-saving operation allows for efficient passage of personnel and equipment without obstructing walkways or work areas. Sliding doors are often equipped with sensors for automated operation, ensuring seamless access control while minimizing the risk of contamination. Their simple yet effective design, combined with their ability to maintain cleanliness standards, makes sliding doors a popular choice for clean room environments.

2. Swing Doors
Swing doors operate on hinges and open either inward or outward, providing a traditional entryway into clean room areas. They offer ease of use and are suitable for applications where frequent passage of personnel and equipment is expected. Swing doors can be automated for hands-free operation, enhancing convenience and reducing the potential for contamination from manual contact. Their robust construction and versatility make them suitable for various clean room settings, from laboratories to manufacturing facilities.
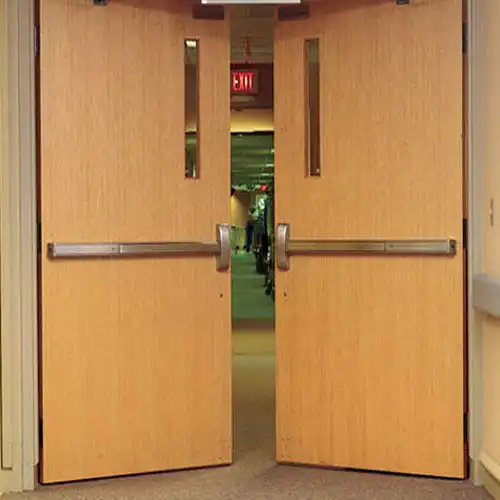
3. Roll-up Doors
Roll-up doors consist of horizontal slats that roll up and down along a track, offering rapid operation and minimal obstruction when opening and closing. These doors are well-suited for environments where speed and efficiency are paramount, such as high-traffic clean room areas or areas with limited overhead clearance. Roll-up doors can be automated for seamless integration with facility control systems, providing enhanced access control and minimizing the risk of contamination. Their durable construction and low maintenance requirements make them a cost-effective solution for clean room environments.
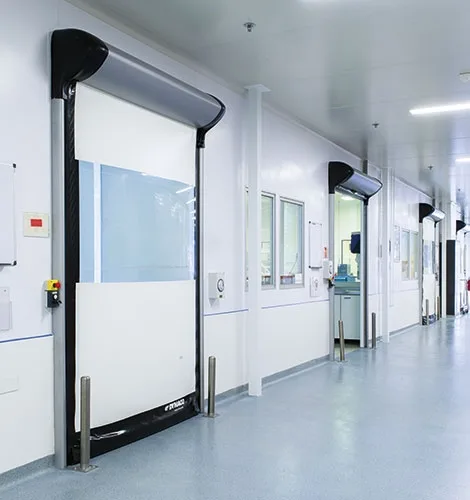
4. Hermetic Doors
Hermetic doors are designed to provide an airtight seal when closed, preventing the transfer of contaminants between clean room areas and the surrounding environment. These doors are essential for maintaining the integrity of critical processes and ensuring compliance with stringent cleanliness standards. Hermetic doors feature specialized sealing systems and robust construction to withstand the demanding requirements of clean room environments. They can be automated for hands-free operation, enhancing convenience and minimizing the risk of contamination from manual handling. Hermetic doors are commonly used in pharmaceutical manufacturing, biotechnology research, and other industries where cleanliness and sterility are paramount.
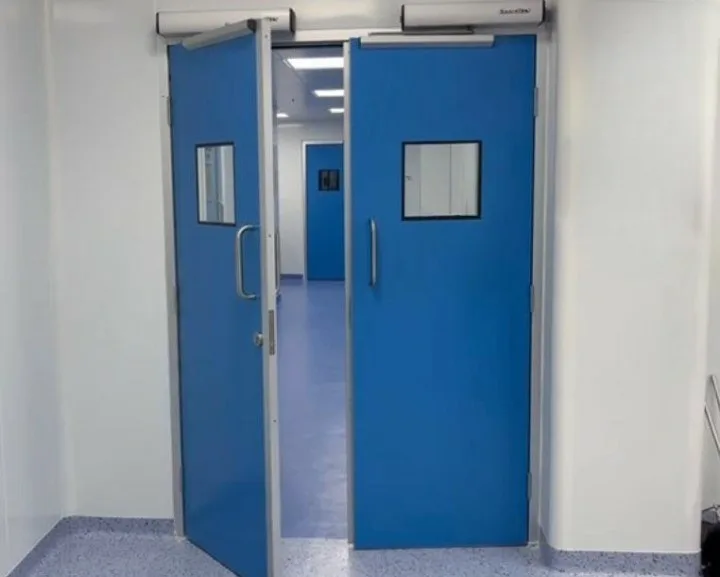
5. Air Shower Doors
Air shower doors are equipped with high-velocity air jets that blow off particulate contaminants from personnel and equipment before they enter the clean room. These doors are typically installed at the entrance to clean room facilities to provide an additional layer of contamination control. Air shower doors feature automated operation and interlocking mechanisms to ensure controlled access and prevent contamination from entering the clean room environment. Their effectiveness in removing surface contaminants makes them an essential component of clean room entryways, particularly in industries with stringent cleanliness requirements such as microelectronics manufacturing and pharmaceutical production.
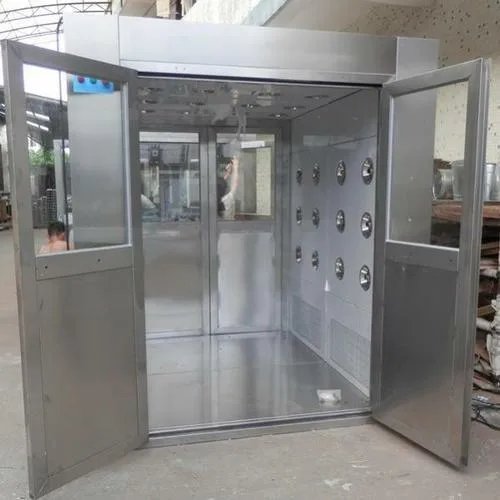
6. Pass-Through Doors
Pass-through doors are designed to facilitate the transfer of materials and equipment into the clean room without compromising its cleanliness. These doors typically feature interlocking mechanisms that allow only one door to be opened at a time, maintaining controlled access and preventing cross-contamination between clean room areas and adjacent spaces. They are commonly used in industries such as pharmaceutical manufacturing, biotechnology research, and semiconductor fabrication, where strict cleanliness standards must be maintained during material transfer processes.
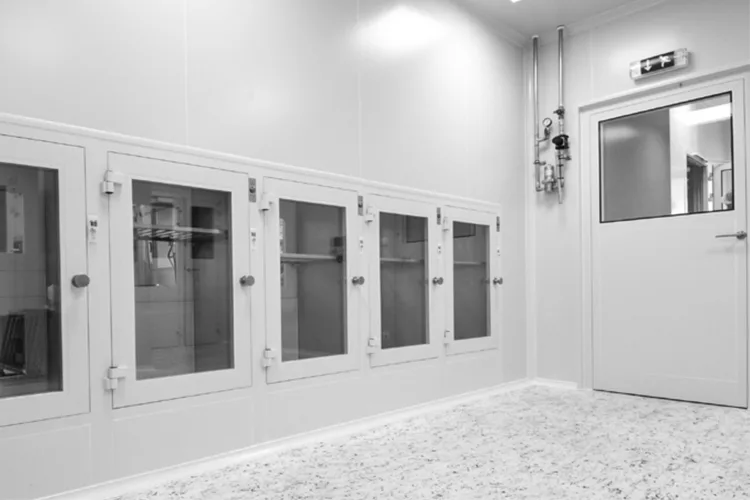
7. High-Speed Doors
High-speed doors are characterized by their rapid opening and closing speeds, minimizing the time during which the clean room is exposed to the external environment. These doors are ideal for applications where frequent access is required, such as loading docks or high-traffic clean room areas. High-speed doors feature advanced automation systems and durable construction to withstand the demands of continuous operation. They can be equipped with sensors for motion detection and obstacle avoidance, ensuring safe and efficient passage of personnel and equipment. High-speed doors help maintain cleanliness standards by reducing the opportunity for airborne contaminants to enter the clean room environment, making them suitable for use in industries such as food processing, pharmaceutical manufacturing, and electronics assembly.
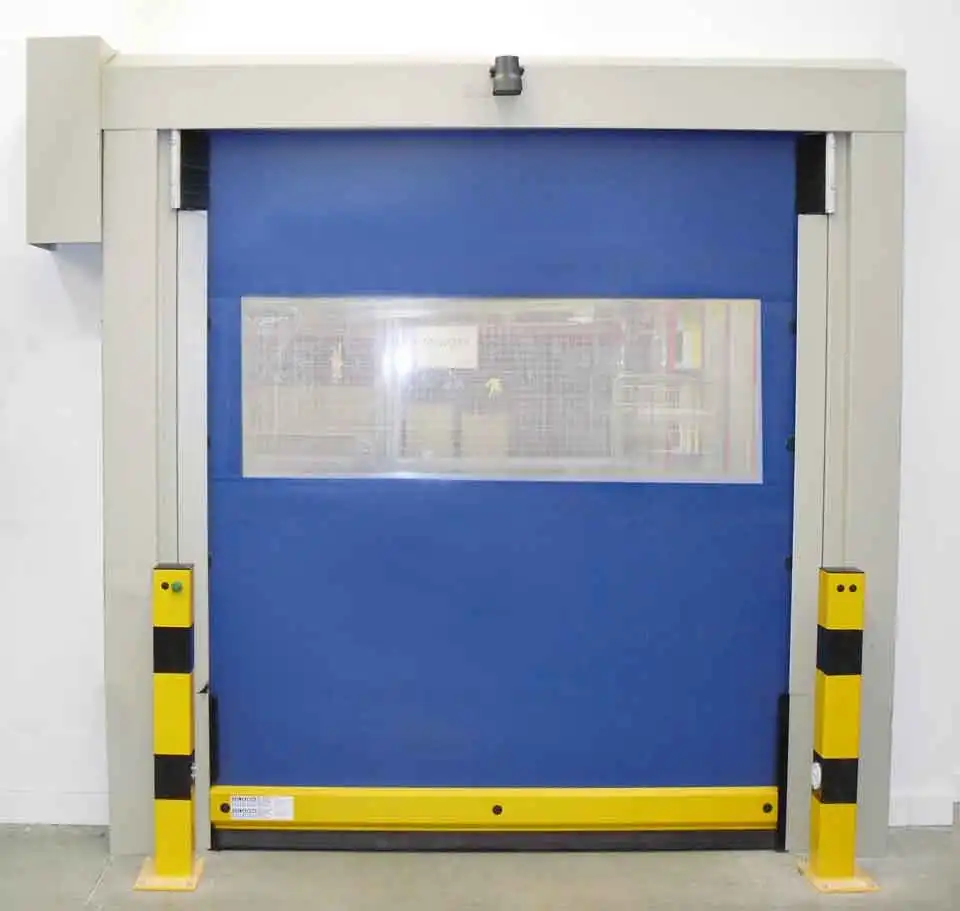
8. Folding Doors
Folding doors, also known as accordion doors, consist of multiple panels that fold and unfold to open and close. These doors are versatile and space-efficient, making them suitable for areas with limited clearance where traditional swinging or sliding doors may not be practical. Folding doors can be automated for seamless operation, allowing for hands-free access while maintaining cleanliness and sterility in clean room environments. Their modular design and customizable configurations make them adaptable to various clean room layouts and requirements.
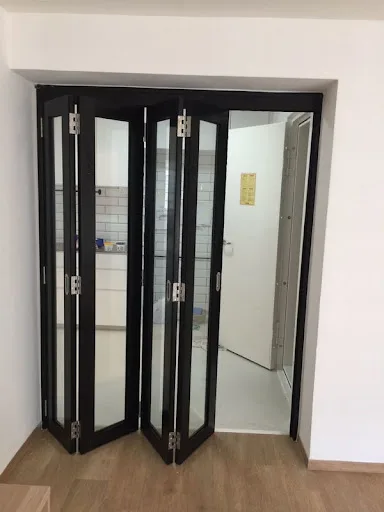
9. Revolving Doors
Revolving doors feature a rotating central chamber surrounded by multiple door panels, allowing for continuous movement of people or equipment while maintaining a seal between the clean room and external environment. They can be equipped with automated controls for seamless operation and integrated with access control systems to ensure controlled entry and exit. These doors are ideal for high-traffic areas where maintaining a controlled environment is essential, such as entrances to clean room facilities in hospitals, research laboratories, or manufacturing plants.

Conclusion
Automated clean room doors offer numerous benefits such as improved efficiency, enhanced cleanliness, and increased safety. With advanced technology and seamless integration, these doors are becoming essential components in various industries, ensuring controlled environments and optimal working conditions. As automation continues to evolve, the future of clean room doors holds promise for even greater efficiency and reliability.