Hardened concrete is the solid state of concrete that results from the curing process, during which the mixture of cement, water, and aggregates chemically reacts and sets. This transformation leads to the formation of a durable material with significant compressive strength, making it essential in various construction applications. The properties of hardened concrete, such as strength, durability, and resistance to environmental factors, depend on the quality of the mix, the curing conditions, and the time allowed for the concrete to set.
Despite its strength, hardened concrete is susceptible to damage due to its inherent brittleness and the presence of microcracks that can develop during the curing process. The concrete’s rigid structure limits its ability to absorb tensile forces, making it vulnerable under stress or impact. Additionally, environmental factors, such as temperature fluctuations, moisture, and chemical exposure, can exacerbate these vulnerabilities. As a result, the durability and overall performance of hardened concrete can be compromised, necessitating careful attention to construction practices and environmental conditions to mitigate potential damage.
Causes of hardened concrete damage:
- Shrinkage
- Temperature fluctuations
- Moisture ingress
- Chemical attacks
- Poor curing practices
- Overloading
- Freeze-thaw cycles
- Abrasion
- Alkali-silica reaction (ASR)
- Carbonation
- Inadequate mixing
- Contamination of materials
- Insufficient reinforcement
- Soil settlement or movement
- Design flaws
- Exposure to aggressive environments
Types of damages that can occur in Hardened Concrete:
Cracking- Cracking is a prevalent damage type in hardened concrete, occurring when tensile stress exceeds the concrete’s strength. It can result from thermal expansion, shrinkage during curing, or overloading. Cracks may range from hairline fractures to significant fissures, which can allow water infiltration and further damage over time.

Spalling- Spalling involves the breaking away of concrete surface layers, often leading to pitting or flaking. This damage typically results from freeze-thaw cycles, where trapped water expands when frozen, or from corrosion of embedded steel reinforcement, which exerts pressure as it rusts.

Delamination- Delamination is the separation of concrete layers due to insufficient bonding or moisture issues. It often arises from inadequate curing or poor mixing, resulting in weak interfaces. Delaminated surfaces may sound hollow when tapped, indicating compromised structural integrity.

Shrinkage- Shrinkage occurs as concrete dries and loses moisture, causing volume reduction that can lead to cracking, particularly in large slabs. It includes plastic shrinkage, which happens before setting, and drying shrinkage, which occurs as moisture evaporates over time.

Chemical Deterioration- Chemical reactions, such as alkali-silica reaction (ASR) and sulfate attack, can significantly deteriorate hardened concrete. ASR occurs when reactive silica in aggregates interacts with alkalis in cement, leading to gel formation and expansion.

Corrosion of Steel Reinforcement: Corrosion of embedded steel reinforcement bars occurs when moisture and chlorides penetrate the concrete. Once these elements reach the steel, they initiate a chemical reaction that forms rust. As rust develops, it expands, creating internal pressure within the concrete, leading to cracks.
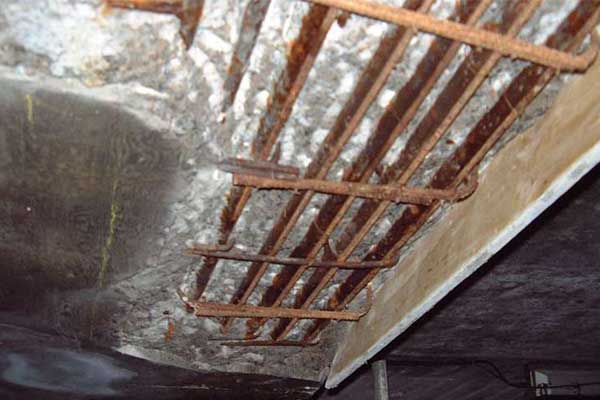
Surface Wear- Surface wear results from mechanical actions, environmental exposure, or abrasive materials, particularly in high-traffic areas. This cumulative effect can erode the concrete surface, reducing load-bearing capacity and creating safety hazards.
Crazing- Crazing is marked by fine, hairline cracks on the surface, often caused by rapid drying or excessive moisture evaporation during curing. While it doesn’t usually affect structural integrity, it can diminish the concrete’s appearance.

Efflorescence- Efflorescence appears as white, powdery deposits on the concrete surface due to soluble salts migrating as water evaporates. While not structurally damaging, it can indicate moisture issues that may lead to corrosion or mold growth.

Honeycombing- Honeycombing occurs when voids or air pockets are present in the concrete, often due to improper compaction. This defect weakens structural integrity and reduces durability.

How to avoid damage in Hardened Concrete?
To effectively avoid damage in hardened concrete, a comprehensive approach encompassing proper planning, material selection, construction practices, and maintenance is essential.
- Engage qualified engineers for appropriate concrete mix design and load assessments.
- Use premium-grade cement, aggregates, and admixtures to enhance durability.
- Ensure aggregates are clean and free from contaminants.
- Adhere strictly to mix design specifications, including water-to-cement ratios.
- Ensure uniform mixing of all components to avoid weak points.
- Use effective curing techniques, such as wet curing or curing compounds, to maintain moisture and temperature.
- Regularly monitor environmental conditions during curing.
- Avoid excessive dropping of concrete during placement to minimize segregation.
- Use appropriate vibration methods for proper consolidation.
- Apply protective sealants to enhance moisture resistance and prevent chemical ingress.
- Design drainage systems to prevent water accumulation around concrete structures.
- Conduct regular inspections to identify early signs of damage or deterioration.
- Address any issues promptly to prevent further deterioration.
- Consider local climate conditions when designing and placing concrete.
- Be cautious of chemicals that may adversely affect concrete, such as de-icing salts.
Repairing hardened concrete
If damage has already occurred, repairing them is essential. It involves various methods that address surface defects, cracks, and structural weaknesses. Here are some common methods:
- Crack Injection
- Epoxy Injection: Used to repair structural cracks, epoxy is injected under pressure into the cracks, restoring strength and providing a waterproof seal.
- Polyurethane Injection: Effective for active water leaks and non-structural cracks, this material expands to fill voids and seal cracks.
- Surface Patching
- Dry Pack Mortar: For small, shallow repairs, dry pack mortar (low water-cement ratio) is hand-applied and packed into surface voids.
- Cementitious or Polymer-Modified Mortars: Applied as a thin layer over the damaged surface, these mortars are highly durable and bond well with the existing concrete.
- Overlay and Resurfacing
- Thin-Bonded Overlay: A thin layer of concrete or polymer-modified mortar is applied to restore the surface appearance and increase durability.
- Shotcrete: A method where concrete is sprayed onto the surface, often used in areas with limited access or complex geometry.
- Reinforcement and Bonding
- Steel Plate Bonding: Plates are bonded to the surface with epoxy to reinforce load-bearing structures.
- Fiber-Reinforced Polymer (FRP) Wraps: Carbon or glass fiber wraps are applied for structural strengthening and reinforcement.
- Grouting
- Cement Grouting: Used for filling voids or honeycombs in concrete, it involves pumping cement slurry under pressure.
- Chemical Grouting: Expansive resins are injected to stabilize soil or fill gaps, especially where waterproofing is required.
- Concrete Replacement
- Spall Repair and Replacement: Damaged sections are removed, and new concrete is cast-in-place or prefabricated pieces are installed.
- Preplaced Aggregate Concrete: Aggregate is placed into the repair area, then grout is injected to fill the voids, providing a strong bond.
- Rehabilitation of Surface Defects
- Grinding and Polishing: For minor surface imperfections, grinding smooths the surface, while polishing improves appearance.
- Application of Sealers or Coatings: Sealers, such as silicate or silane-based, are applied to protect the surface from further damage, chemical attack, or moisture intrusion.
Selecting the right method depends on the type, location, and severity of damage.
Conclusion
Hardened concrete, although inherently strong, is susceptible to various forms of damage that can compromise its overall performance. Maintaining its durability and structural integrity requires proactive measures and regular assessments. By prioritising preventive care and addressing any issues promptly, the longevity and reliability of hardened concrete can be effectively ensured.