Ready-mix plaster, also known as pre-mixed or pre-bagged plaster, is a construction material that comes in a ready-to-use form. It is a blend of cement, aggregates, additives, and sometimes polymers, which are pre-mixed in precise proportions at a manufacturing facility. This pre-mixed composition ensures consistent quality and performance. Ready-mix plaster eliminates the need for on-site mixing, which can be time-consuming and labour-intensive. With ready-mix plaster, you can save time and effort as the plaster is already pre-mixed and ready to use. This can significantly speed up the plastering process, allowing for quicker project completion.
Materials used for manufacturing of ready-mix plasters
Ready-mix plasters typically consist of a combination of cement, sand, and various additives. The specific materials used may vary depending on the manufacturer and the desired properties of the plaster. Here are the primary materials commonly used in the production of ready-mix plaster:
1. Cement: Cement is a key component of ready-mix plaster. It provides the binding properties that hold the plaster together. Ordinary Portland cement (OPC) is often used, although specialized types of cement, such as sulfate-resistant cement or high-performance cement, may be used in specific applications.
2. Sand: Sand is another essential ingredient in ready-mix plaster. It acts as the filler and provides bulk to the mixture. The sand used in plaster should be clean, free from impurities, and have the appropriate particle size distribution for optimal workability and strength.
3. Additives: Various additives are incorporated into the ready-mix plaster formulation to enhance its performance and workability. Some common additives used in ready-mix plaster include:
a. Retarders: These additives slow down the setting time of the plaster, allowing for better workability and extended application time.
b. Accelerators: Accelerators are used to speed up the setting time of the plaster, which can be beneficial in cold weather conditions or when rapid setting is desired.
c. Plasticizers: Plasticizers improve the workability and flow characteristics of the plaster, making it easier to mix, spread, and apply.
d. Fibers: Fibers, such as cellulose or synthetic fibers, can be added to enhance the strength, crack resistance, and overall durability of the plaster.
e. Water-retaining agents: These additives help the plaster retain moisture, preventing it from drying out too quickly and ensuring proper curing.
f. Bonding agents: Bonding agents improve the adhesion of the plaster to various substrates, promoting better bond strength and durability.
g. Air-entraining agents: Air-entraining agents introduce small air bubbles into the plaster, improving its workability, freeze-thaw resistance, and reducing shrinkage cracks.
These are some of the common materials used in the production of ready-mix plaster. The specific composition and proportions of these materials can vary based on the manufacturer’s formulations.
Advantages of ready-mix plasters
- Ensures consistent quality and composition as it is manufactured in controlled conditions
- Comes with excellent workability, making it easier to apply and manipulate on different surfaces
- Can be modified with additives and binders that enhance its durability and resistance to cracking, shrinkage, and moisture.
- Reduces the time required for plaster preparation, as it doesn’t involve the measurement and mixing of ingredients on-site.
- Comes with added polymers and negligible silt content. It sets faster than regular plaster and controls cement shrinkage.
- Additives and graded sand used in ready-mix plaster reduce water absorption
- Provides excellent coverage due to the mineral binders present in it
- Premix nature of the product ensures faster applications
Different types of ready-mix plaster products
There are several ready-mix plaster products available in the market that offer convenient and efficient solutions for plastering applications. Fosroc India, Asian Paints India, Berger India, JK cement India, Ultratech India, Nuvoco India are some of the prominent manufacturers of ready- mix plasters in India. Here are some popular ready-mix plaster products in India:
1. Cement-Based Ready-Mix Plaster: Cement-based ready-mix plaster is a common choice for plastering applications. It consists of a blend of cement, sand, and additives, which are pre-mixed in precise proportions. This product only requires the addition of water to achieve the desired consistency. Cement-based ready-mix plaster provides good adhesion, workability, and durability, making it suitable for interior and exterior plastering.

2. Gypsum-Based Ready-Mix Plaster: Gypsum-based ready-mix plaster is formulated using gypsum powder, aggregates, and additives. It offers advantages such as fast drying time and ease of application. Gypsum-based plaster is commonly used for interior plastering, including walls and ceilings. It provides a smooth and even finish and has excellent fire resistance properties.

3. Lime-Based Ready-Mix Plaster: Lime-based ready-mix plaster is formulated using lime, sand, and additives. Lime plaster has been traditionally used in India for its excellent breathability and flexibility. It is suitable for both interior and exterior plastering applications and is known for its durability, crack resistance, and water resistance.

4. Polymer-Modified Ready-Mix Plaster: Polymer-modified ready-mix plaster is a modern plastering solution that incorporates polymers or additives to enhance the properties of the plaster. These additives improve the workability, adhesion, strength, and crack resistance of the plaster. Polymer-modified ready-mix plaster offers excellent bonding and can be used for a wide range of surfaces, including concrete, masonry, and AAC blocks.

5. Exterior Grade Ready-Mix Plaster: Exterior grade ready-mix plaster is specifically formulated for external plastering applications. It is designed to withstand weathering, UV exposure, and moisture, providing long-lasting protection and aesthetics. Exterior grade ready-mix plaster offers excellent adhesion to various substrates and helps in maintaining the structural integrity of the building envelope.

The application method of ready-mix plasters
The application method of ready-mix plaster typically involves the following steps:
1. Surface Preparation: Ensure that the surface to be plastered is clean, free from dust, loose particles, grease, or any other contaminants. Repair any cracks or damaged areas and make sure the surface is stable.
2. Mixing: Ready-mix plaster comes in a pre-mixed form, so there is no need for on-site mixing. However, before application, it is recommended to stir or mix the plaster lightly to ensure uniform consistency.
3. Application: Use a steel trowel, hawk, or spray machine for applying the ready-mix plaster. Start by applying a thin layer of plaster onto the surface ensuring good adhesion.
4. Leveling and Smoothing: Once the ready-mix plaster is applied, use a straightedge or a plastering float to level and smooth the surface. Remove any excess plaster and create a uniform and even surface.
5. Drying and Curing: Allow the plaster to dry and cure as per the manufacturer’s instructions. This typically involves keeping the plastered surface moist by misting it with water or covering it with a damp cloth to slow down the drying process and promote proper curing.
6. Finishing: Once the plaster is completely dry and cured, it can be finished using sandpaper, a float, or a trowel to achieve the desired texture or smoothness. You can also apply a final coat of paint or other decorative finishes if desired.
It’s important to note that specific instructions may vary depending on the manufacturer and the type of ready-mix plaster being used.
Applications of Ready-mix plasters:
1. Interior Walls and Ceilings: Ready-mix plaster is commonly used for plastering interior walls and ceilings. It provides a smooth and uniform finish, creating a suitable surface for painting, wallpapering, or other decorative treatments.
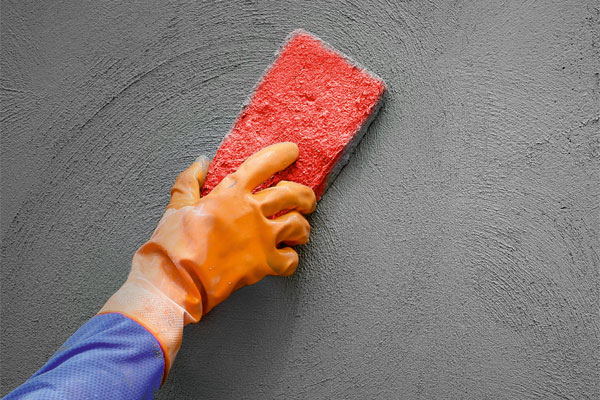
2. External Rendering: Ready-mix plaster is also used for external rendering of buildings. It helps protect the underlying structure from weather elements and provides an attractive finish. The type of ready-mix plaster used for external rendering may vary based on the specific requirements of the project, such as weather resistance or breathability.

3. Plastering of Concrete Surfaces: Ready-mix plaster is widely used for internal plastering of walls and ceilings in residential, commercial, and industrial buildings as well as external plastering of building facades.

4. Repair and Patching: Ready-mix plaster is used for repair and patching work on existing plaster surfaces. It can be applied to fill cracks, holes, or damaged areas, restoring the integrity and appearance of the plastered surface.

5. Skimming and Smoothing: Ready-mix plaster is commonly used for skimming or smoothing uneven surfaces. It helps in achieving a level and uniform substrate for further finishing work, such as applying tiles, wallpaper, or paint.
6. Drywall Jointing: Ready-mix plaster is used for jointing and finishing of drywall panels. It helps in creating a seamless and smooth surface between adjacent panels.

7. Decorative Finishes: Ready-mix plaster can serve as a base for various decorative finishes, such as textured coatings, stucco, or decorative plasters.
Conclusion
Ready-mix concrete offers convenience, consistent quality, strength, durability, waste reduction, safety, and versatility, making it an essential component in modern construction projects. It streamlines the construction process, enhances the performance of structures, and contributes to overall project efficiency.