An AAC (Autoclaved Aerated Concrete) block making machine is a specialized construction machine used for the production of AAC blocks. These machines are engineered to mix and combine raw materials like sand, cement, lime etc. in precise proportions, creating an AAC slurry. This slurry is then poured into molds within the machine, which are subsequently cured in an autoclave to produce AAC blocks. These machines streamline the manufacturing process, ensuring consistent quality and efficiency in the production of these lightweight, high-insulation construction materials.
Components of AAC block making machines;
An AAC (Autoclaved Aerated Concrete) block making machine typically consists of several key components:
- Mixer: This component is used to mix raw materials like cement, lime, sand, aluminum powder, and water to create the AAC slurry.
- Batching System: It measures and proportionally mixes the raw materials to ensure consistency in the AAC mixture.
- Moulds: These are used to shape the AAC mixture into blocks or panels of the desired size and shape.
- Cutting Machine: After the AAC mixture has been poured into the moulds and cured, a cutting machine is used to cut the blocks or panels to the required dimensions.
- Autoclave: The AAC blocks or panels are placed in an autoclave chamber, where they undergo a high-temperature and high-pressure curing process. This step is crucial for the formation of air bubbles and the hardening of the material.
- Crane or Handling System: To move and transport the heavy AAC blocks or panels within the production facility.
- Control Panel: An electronic control system manages and monitors the entire AAC block making process, including temperature and pressure control in the autoclave.
- Conveyors: These are used to transport raw materials, cured AAC blocks, and other components within the production line.
- Drying Area: The freshly molded AAC blocks need to be air-cured before they are placed in the autoclave. This area provides the necessary space and conditions for drying.
- Packaging and Stacking Equipment: Once the AAC blocks are cured and ready for use, there is equipment for packaging and stacking them for storage or transportation.
These are the primary components of an AAC block making machine, and the specific configuration may vary depending on the manufacturer and the scale of production.
Types of AAC Block Making Machines
There are different types of AAC block making machines used to manufacture products as per project requirements. Each of them are discussed below.
Manual AAC Block Making Machines:
Manual AAC block machines heavily rely on human labour. Operators manually mix raw materials such as cement, lime, sand, and aluminium powder before pouring the mixture into molds. After curing, blocks are manually cut and removed. These machines are typically chosen for small-scale production, startup ventures, or regions with limited resources where labor is readily available but machinery is scarce.
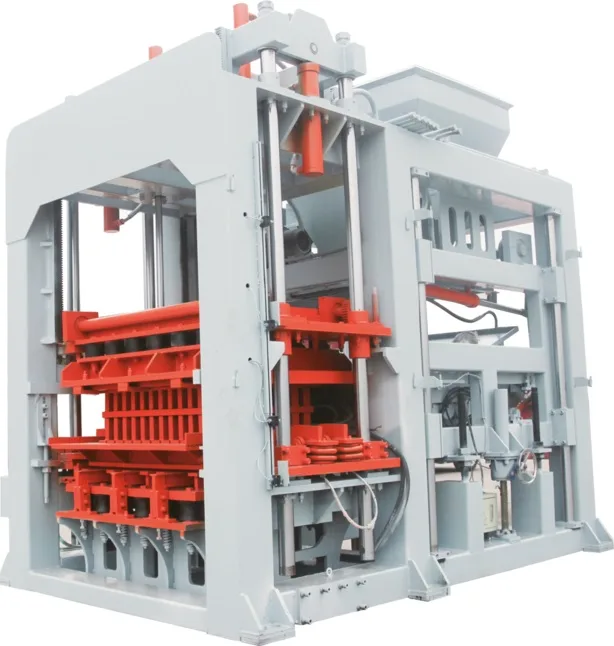
Semi-Automatic AAC Block Making Machines:
Semi-automatic AAC block making machines strike a balance between manual and automated processes. They incorporate automated systems for material mixing and pouring but require manual intervention for tasks such as cutting and block removal. These machines are well-suited for medium-scale production scenarios where some level of manual labour is acceptable and a moderate level of automation is desired.
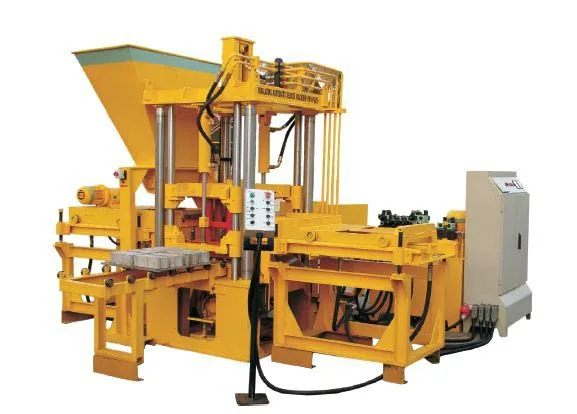
Fully Automatic AAC Block Making Machines:
Fully automatic AAC block making machines epitomise automation and efficiency. They require minimal manual labour. The entire production process, from mixing to pouring, cutting, and even packaging, is predominantly automated. These machines are the ideal choice for large-scale production facilities with high output demands, ensuring consistent quality and productivity.
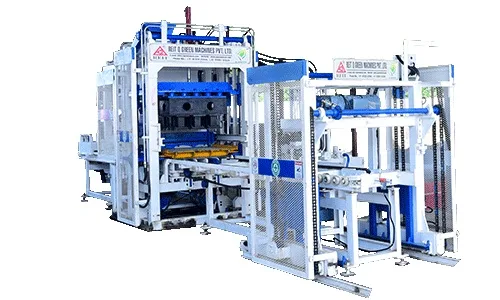
Vertical AAC Block Machines:
Vertical AAC block machines are designed with molds that move vertically through each production stage. They offer advantages in terms of space efficiency and the ability to accommodate fully automated processes. Manufacturers often customize these machines to produce various block sizes and shapes. They are commonly found in extensive manufacturing plants.

Horizontal AAC Block Machines:
In contrast, horizontal AAC block machines feature molds that move horizontally through the production process. They are well-suited for high-capacity production facilities and can be fully automated. Their flexibility in handling various block sizes makes them a popular choice for large-volume AAC block production, ensuring efficiency and consistency.
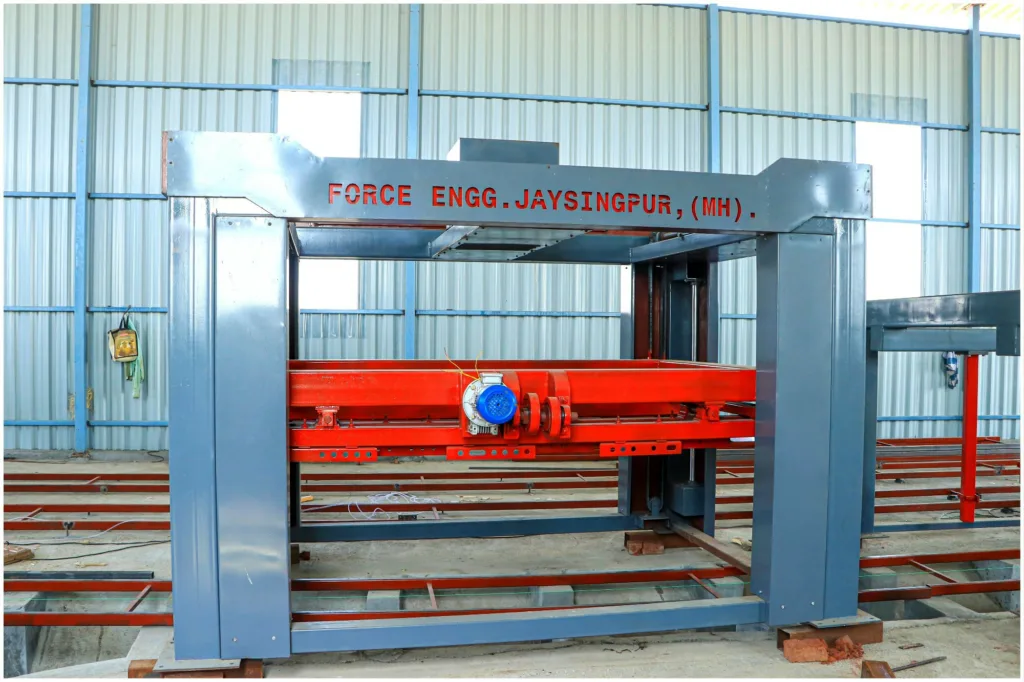
Tilting AAC Block Machines:
Tilting machines have a unique capability to tilt molds, simplifying the block removal process. This design reduces the need for manual labor during block extraction and enhances overall efficiency. They can be found in production facilities of various scales, particularly for their utility in optimizing block handling.
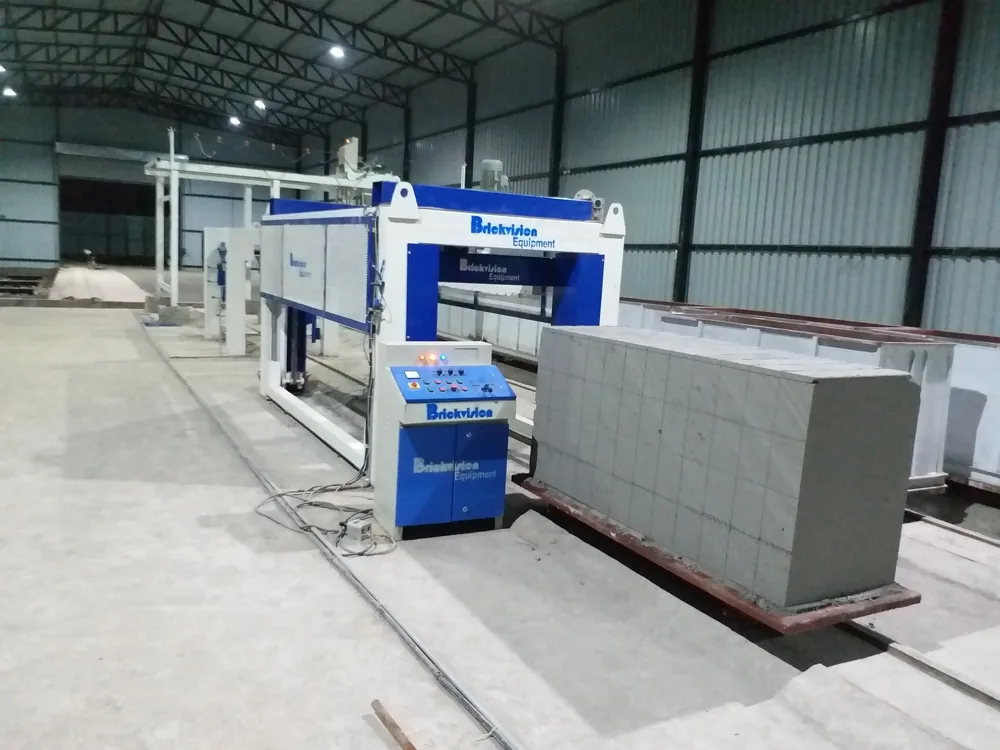
Portable AAC Block Machines:
Portable AAC block machines are compact and mobile, making them suitable for on-site or remote construction projects. These machines offer versatility and are often used in areas with limited access to traditional manufacturing facilities, enabling AAC block production closer to the construction site.

Customized AAC Block Machines:
Customized AAC block machines offer versatility by allowing manufacturers to tailor them to meet specific production requirements, block sizes, shapes, and automation levels. These machines are chosen when standard models do not align with unique project needs, ensuring a perfect fit for production goals, quality standards, and efficiency objectives.
Different products manufactured with AAC block making machines;
- AAC Blocks: Standard autoclaved aerated concrete blocks used for wall construction.
- AAC Panels: Large panels used for walls and partitions, often in commercial buildings.
- AAC Lintels: Load-bearing lintels used above doors and windows.
- AAC Floor and Roof Panels: Panels used for flooring and roofing systems, providing thermal insulation and strength.
- AAC Wall Tiles: Decorative tiles made from AAC for interior and exterior wall cladding.
- AAC Pavers: Pavers used for outdoor pathways, driveways, and landscaping.
- AAC Bricks: Smaller-sized AAC units suitable for various masonry applications.
- AAC Soundproofing Panels: Special panels designed to offer sound insulation in walls and ceilings.
- AAC Pipes: Drainage and sewage pipes made from autoclaved aerated concrete.
- AAC Precast Elements: Customized precast elements for construction, such as beams, columns, and decorative elements.
Applications of AAC block making machines
AAC block making machines across various construction projects that includes;
- Residential and Commercial buildings
- Industrial facilities
- Educational institutions
- Healthcare facilities
- Hotels and resorts
- Warehouses and storage buildings
- Infrastructure projects (bridges, tunnels)
- Renovation and retrofitting projects
- Low-cost housing initiatives
- Sustainable and green building projects
- Soundproofing and acoustic projects
- Interior partition walls
- Swimming pools
- High-rise buildings etc.
Conclusion
AAC (Autoclaved Aerated Concrete) machines offer a diverse range of options to cater to various project scales and requirements, from fully automated plants for large-scale construction to mobile units for on-site flexibility. As the construction industry continues to prioritize efficiency and sustainability, AAC block making machines are poised to play an important role in modern construction.
Image Source: brickwell.in, parijatha.com, qgreentech.com, apollozenith.com, forceengineering.co.in, brickvisionequipment.com, marutihydraulics.com