Formwork refers to temporary molds or structures that are created to hold and shape concrete until it gains sufficient strength to be self-supporting. Although conventional materials such as timber and plywood have historically been the primary choices, plastic formwork is increasingly gaining traction as a viable alternative. Notably, plastic formwork is emerging as a viable choice, particularly for projects where its unique advantages align with the scale and requirements.
What is Plastic Formwork?
Plastic formwork represents a contemporary advancement in the construction sector. It’s typically made from high-quality plastic materials, often recycled, and designed to mold concrete into various shapes and structures. Unlike traditional timber or plywood formwork, plastic formwork is characterized by its lightweight nature, reusability, and resistance to water and chemicals, rendering it a flexible choice for numerous projects.
Plastic formwork presents an effective answer to the sustainability issues confronting the construction sector. By switching to plastic formwork, we can reduce deforestation, minimize waste, and lower carbon emissions.
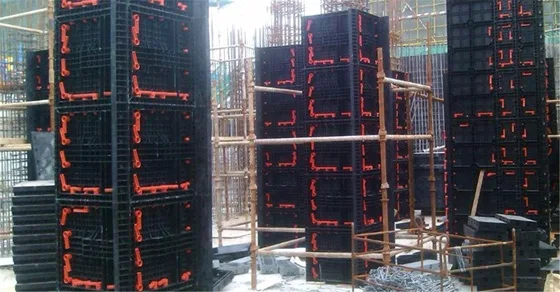
How Does Plastic Formwork Work?
Similar to other formwork systems, plastic formwork is constructed around the designated area for concrete pouring. Once the concrete is poured into the plastic mold and after it has set and hardened, the plastic formwork can be dismantled and utilized again for subsequent stages of the project. Although plastic formwork presents numerous benefits, it is essential to consider both its advantages and disadvantages before deciding to implement it. Let us examine both aspects in detail.
Pros of Plastic Formwork
Reusability
A significant advantage of plastic formwork is its reusability. Unlike plywood, which often degrades after just a few uses, plastic formwork can be reused up to 100 times or more, depending on the care and maintenance it receives. This characteristic of reusability renders it a valuable investment for contractors engaged in extensive projects.
Lightweight and Easy to Handle
Plastic formwork is significantly lighter than its timber or metal options. This lightweight nature makes it easier to transport, assemble, and dismantle, reducing labor costs and improving overall efficiency on the construction site As a result, workers can install plastic formwork more rapidly, contributing to the timely completion of projects.
Water and Weather Resistant
Unlike wood, which can absorb moisture and warp, plastic formwork is highly resistant to water. This makes it particularly suitable for projects in humid or wet climates where traditional materials may face challenges. Furthermore, plastic formwork is also resistant to chemicals and ultraviolet rays, thereby enhancing its longevity in various environmental conditions.
Cost-Effective in the Long Term
While the initial expense of plastic formwork may exceed that of plywood, its longevity and reusability make it a cost-effective choice in the long term. Utilizing plastic formwork eliminates the need for frequent purchases of new materials for every stage of your project. The upfront investment becomes advantageous after repeated uses, especially in large-scale or repetitive construction projects.
Eco-Friendly
Most of the plastic formwork systems are made from recycled materials, thereby promoting sustainability in the construction industry. The ability to reuse plastic formwork multiple times also minimises material waste, helping to lower the overall environmental impact of construction projects.
Provides a Smooth, Quality Finish
Plastic formwork has a smooth surface that ensures a high-quality finish on the concrete. This reduces the need for additional work to smooth or repair the surface after the formwork is removed, thereby saving both time and resources.
Cons of Plastic Formwork
Higher Initial Cost
One of the primary disadvantages of plastic formwork is its elevated initial expense in comparison to conventional materials such as plywood. Although plastic formwork proves to be more economical in the long run due to its ability to be reused, the initial financial outlay may pose a challenge for smaller contractors or projects operating within limited budgets.
Limited Customization
Plastic formwork is generally available in standard sizes and shapes. Although this modularity offers convenience for numerous projects, it may not be suitable for custom or complex designs that necessitate on-site cutting or adjustments.
Requires Proper Storage and Maintenance
Although plastic formwork is known for its durability, it is essential to maintain it properly to extend its lifespan. After each use, the panels should be cleaned and stored under suitable conditions to avoid any potential damage. Poor storage can lead to warping or cracking, reducing the number of times the formwork can be reused.
Step-by-Step Guide for Using Plastic Formwork
Plan Your Formwork Layout
Before assembling your formwork, it’s essential to have a detailed plan in place. Determine the dimensions of the concrete structure, the desired shape, and the positioning of the formwork. Additionally, consider important factors such as the weight of the concrete and the pressure it will apply to the formwork.
Using modular plastic formwork allows you to easily adjust the size and shape, but careful planning is still essential to avoid delays and ensure a perfect fit.
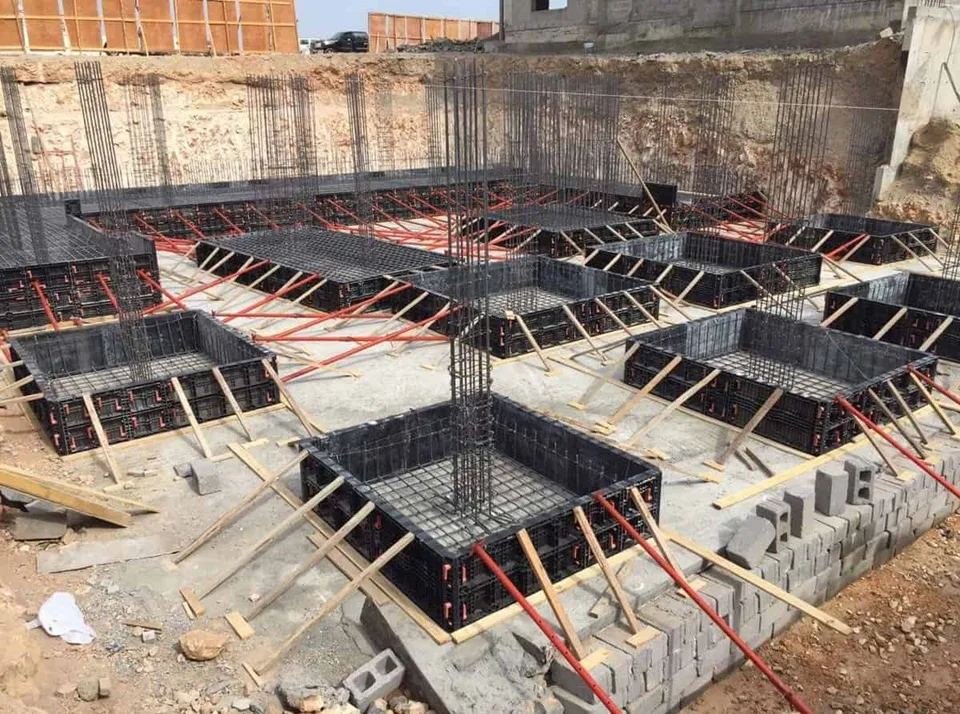
Prepare the Site
Ensure that your job site is properly prepared before setting up the formwork. The surface should be clean, level, and free from debris. Any irregularities in the ground may result in alignment or stability problems during the concrete pouring process. Additionally, it is advisable to review the weather forecast, as severe conditions such as heavy rainfall or strong winds could affect the setup and stability of your formwork.
Assemble the Plastic Formwork
Assembling plastic formwork is straightforward due to its modular nature. Start by connecting the panels or sheets according to your planned layout. Typically, plastic formwork systems are equipped with user-friendly locking mechanisms that facilitate to connect the pieces securely.
During the assembly process, it is essential to ensure that all panels are correctly aligned and that the joints between them are tightly sealed to avoid any leakage of concrete. Additionally, reinforce the formwork with ties or clamps to uphold its shape and stability throughout the pouring process.
Apply Release Agent
To prevent the concrete from adhering to the formwork, it is advisable to apply a release agent to the inside surfaces. This practice facilitates the removal of the formwork once the concrete has set, resulting in a smooth finish. Exercise caution to avoid excessive application of the release agent, as this may alter the texture of the concrete.
Pour the Concrete
After the formwork has been firmly established, you can proceed with pouring the concrete. Begin the process by pouring at a gradual pace to guarantee that the formwork can withstand the pressure. Although plastic formwork is engineered for strength, a rapid pour may lead to shifting or bulging.
Use a vibratorortampingrod to remove any air bubbles from the concrete, ensuring that it fills the entire mold evenly. This step is crucial for preventing voids and ensuring the structural integrity of the finished concrete.
Monitor the Curing Process
Once the concrete has been poured,allow it to cure according to the recommended time frame . During this process, avoid disturbing the formwork. While plastic formwork is designed to withstand various weather conditions, it’s still advisable to monitor the site and and ensure that no factors disrupt the curing process.
Remove the Formwork
Once the concrete has cured, carefully dismantle the formwork by unlocking the panels or sheets. The use of a release agent will facilitate the easy removal of the formwork, resulting in a smooth concrete surface. It is advisable to clean the plastic formwork promptly after use to eliminate any residue and ensure it is ready for future applications.
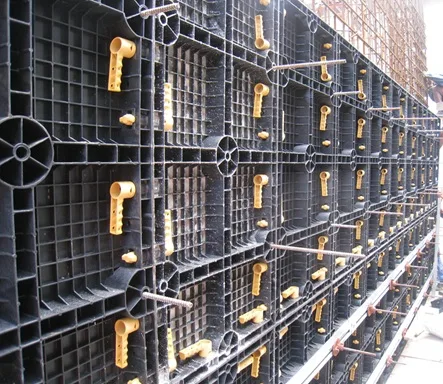
Common Mistakes to Avoid
Even the pros can make mistakes when working with plastic formwork. Here are a few common pitfalls to avoid:
Skipping the release agent: Failing to apply a release agent may complicate the removal of the formwork, potentially resulting in damage to the concrete surface.
Incorrect assembly: Improper alignment of the formwork panels can lead to uneven concrete pours and poor structural quality.
Pouring too quickly: Pouring concrete too fast may lead to the displacement of the formwork, resulting in uneven or bulging surfaces.
Ignoring the weather: Extreme temperatures or adverse weather conditions can influence the curing process; therefore, it is essential to monitor the weather forecast regularly.
Conclusion
Plastic formwork plays a significant role in reducing the carbon footprint of construction projects. With its lightweight and modular design, transportation emissions are reduced during the delivery and installation process. Moreover, the high durability of plastic formwork leads to longer service life, resulting in lower maintenance costs and fewer replacements.
One of the key advantages of plastic formwork is its recyclability. At the end of a project’s lifespan, the plastic panels can be recycled and transformed into new construction materials. This closed-loop process not only decreases waste but also lessens the environmental footprint of construction activities. By adopting plastic formwork, construction firms can pursue a more sustainable methodology and play a role in fostering a greener future.