Adhesives can be defined as non-metallic materials capable of joining permanently to surfaces by an adhesive process. The use of adhesives in construction offers certain advantages over other binding techniques. These include the ability to bind different materials together, the more efficient distribution of stress across a joint, the cost-effectiveness of an easily mechanized process, and greater flexibility in design.
Different types of adhesives used in construction
Adhesives may be found naturally or produced synthetically. There are different kinds of adhesives used in construction, some of them are given below.
Polymer adhesives
A polymer adhesive is a synthetic bonding substance made from polymers and is considered to be stronger, more flexible, and has greater impact resistance than other forms of adhesives. These bonding products are used in multiple industries including automotive, aerospace, aviation, construction, electronics, and electrical. Polymer adhesives are broadly classified as thermoplastic, or thermosetting, depending on the molecular structure. Many polymer adhesives are dispersed in water and are suitable for use with both solid and engineered wood flooring.
Hot melt adhesives
Hot melt adhesive (HMA), is a form of thermoplastic adhesive that is commonly sold as solid cylindrical sticks of various diameters designed to be applied using a hot glue gun. The gun uses a continuous-duty heating element to melt the plastic glue, which the user pushes through the gun either with a mechanical trigger mechanism on the gun or with direct finger pressure. In industrial use, hot melt adhesives provide several advantages over solvent-based adhesives. Volatile organic compounds are reduced or eliminated, and the drying or curing step is eliminated. Hot melt adhesives have a long shelf life and usually can be disposed of without special precautions. Some of the disadvantages involve a thermal load of the substrate, limiting use to substrates not sensitive to higher temperatures, and loss of bond strength at higher temperatures, up to complete melting of the adhesive. Hot melt adhesives can also be applied by dipping or spraying, and are popular with hobbyists and crafters both for affixing and as an inexpensive alternative to resin casting.
Acrylic adhesives
Acrylic adhesives are key to large sections of modern industry, providing high strength bonds that work well as an alternative to rivets or other more mechanical joining techniques. Acrylic adhesives are useful for a wide range of surfaces, they can also be used to join acrylics. Acrylic adhesives are either thermoplastics, which can be moulded above a certain temperature or thermosetting polymer, which ‘cure’ once and cannot be remoulded. Acrylic adhesives have traditionally been used for their strong structural adhesive properties. As a good structural adhesive, acrylic adhesives are naturally in high demand. As an inexpensive structural adhesive, they can be very useful to very many projects! Acrylic adhesives also look good and bond easily to several different materials. This gives them great flexibility in terms of applications


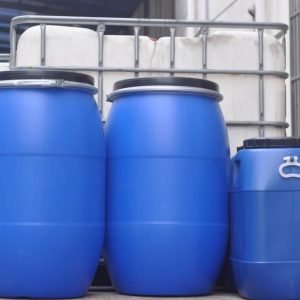
Resin adhesives
Resin adhesive provides superior bonding capabilities. It is manufactured in powdered, spray, emulsion, and liquid forms. Resin adhesives are used to enhance the retention of both composites and compomers and hence prevent bacterial microleakage. It can be used with various materials, including, wood, fabric, glass, china or metal. It’s important to note, however; the epoxy resin is not considered to be water-resistant. Repeated moist or wet conditions can cause deterioration over time which will affect durability.
Anaerobic adhesives
Anaerobic adhesives are one-part adhesives composed of dimethacrylate monomers that cure only in the absence of air. They are less toxic than other acrylics, have a mild, inoffensive odor, and are not corrosive to metals. Anaerobic adhesives are stored in partially filled polyethylene containers, in which the ratio of air-exposed surface to volume is high. Anaerobic adhesives are used for structural bonds, primarily with materials such as metals and glass and to a lesser extent, wood and plastic (thermosets and some thermoplastics). An activator is applied to one or both joint surfaces; adhesive is then applied to one surface to begin curing. Joints produced using anaerobic adhesives can withstand exposure to organic solvents and water, weathering, and temperatures of up to about 200°C
Epoxy adhesives
Epoxy adhesives can adhere to a wide variety of materials, their high strength, their resistance to chemicals and environments, and their ability to resist creep under sustained load, epoxies are the most widely used structural adhesive. They are available in one component, heat curing and two-component, room temperature curing systems. Unmodified epoxies cure hard, brittle solids. Most adhesive formulations include modifiers to increase the flexibility or toughness of the cured adhesive. This results in bond lines that can resist more peel and cleavage stress as well as impact. As the most widely used structural type adhesive, epoxy adhesives are commonly offered as either one component or two-component systems. One component epoxy adhesives are generally cured at temperatures between 250-300°F, conditions that engineer a product of high strength, excellent adhesion to metals, and outstanding environmental and harsh chemical resistance. Check out the selection of epoxy adhesives from Gluegun.com .



Pressure adhesives
Pressure adhesives remain viscous. As a result, they remain permanently tacky and can wet surfaces on contact. Bonds are made by bringing the adhesive film in contact with the substrate and applying pressure. If inadequate pressure is applied or the processing temperature is too low, bonding faults such as bubbles or detachment can occur. Since these adhesives are not true solids, the strength of pressure-sensitive adhesives decreases when the temperature is increased. Pressure-sensitive adhesives also tend to undergo creep when subjected to loads. They are typically formulated from natural rubber, certain synthetic rubbers, and polyacrylates.
Electrically conductive adhesives
Modern electrically conductive adhesives provide excellent adhesion and reliability. They cure in times of less than two minutes, and in-line processing capability for exceptionally high throughput. n electrically conductive adhesive is an adhesive made of conductive particles suspended in a sticky compound. With about 80% of the mass of the adhesive made of the conductive particles, they are spaced closely enough to each other to allow a substantial current to pass. The composition of conductive adhesives can vary greatly from one product to another. The base adhesive is typically a 2-component epoxy, although acrylate and polyester are also quite common. The conductive component plays a huge role in determining the cost of a conductive adhesive: inexpensive ones use iron, which has poor conductivity, while the most expensive ones use either silver or copper.
Phenolic resin adhesives
Phenolic resins adhesives are the condensation products of phenol and formaldehyde and are an important class of adhesives. They are relatively inexpensive and are manufactured as liquid compositions and films. Thermosetting phenolic resins withstand high temperatures both under mechanical load and in severe environments with minimal deformation and creep. The primary use of phenolic resins is as a bonding agent. Phenolic resins readily penetrate and adhere to many organic and inorganic fillers and reinforcements, and when cross-linked throughout the fillers and reinforcements, provide excellent mechanical, thermal, and chemically resistant properties. Their exceptional compatibility with cellulose fillers makes them the ideal binder for particleboard, plywood, hardboard, and oriented strand board (OSB).



Plastisol adhesives
Plastisol are single-component adhesives that are applied as a paste to the substrate. The paste consists of solid polyvinyl chloride (PVC) particles dispersed in plasticizer. To form a bond, the applied adhesive is heated so that the thermoplastic PVC swells and can take up the plasticizer. Plastisols have high flexibility and good peel resistance. They can be flexible or rigid depending on the type and amount of plasticizer added and give good adhesion to most types of (oiled) metals, and plastics. They are often the preferred material for applications where low-flammability at a low cost is required or advantageous. They are also easy to apply, require no meter mixing, and allow for fast processing.
Reactive adhesives
Reactive adhesives require a chemical reaction for bonding two surfaces. These adhesives are classified into one- and two-component reactive adhesives and have been used in applications where substrates require substantial permanency and high strength adherence such as high-tech devices. Highly reactive adhesives with quick gelling and hardening behavior and steep increases in bonding strength even at a low degree of chemical curing. Its mixes are produced by including accelerators, special hardeners, crosslinkers and other materials.
Solvent-Based adhesives
These are called binding agents and are dispersed in an organic solvent. When the solvent evaporates, the adhesive changes from liquid to its final solid form – the pure bonding substance remains. The function of the relatively highly volatile solvents is to facilitate easy transport and application of the adhesive: They ensure that the binding agents stay liquid and can, therefore, be processed. Also, the solvents influence key adhesive characteristics such as adhesion, by promoting the wetting of the substrate or by biting the substrate surface or dwell time and open time, depending on how fast they evaporate. The performance of solvent-based adhesives is largely determined by the polymer system in the formulation. The choice of adhesive type depends on the specific substrates and environmental resistance needed – temperature resistance, oil and plasticizer resistance, etc.



Thermoset adhesives
Thermoset adhesives are crosslinked polymeric resins that are cured using heat and/or heat and pressure. Due to their superior strength and resistance, thermosets are widely used for structural load-bearing applications. Thermoset adhesives have very high strength, excellent gap filling ability, and resistance to moisture and heat. Most thermoset adhesives are supplied as a two-component system although one-part adhesives are used as well. Two-component adhesives are typically made up of a resin and a hardener, in liquid or gel form, which are mixed to initiate the curing process.
UV Curing adhesives
UV glue curing is gaining popularity over other methods of bonding such as drying or exposure to chemicals. Bonding with heat or drying works by evaporation, which can be inconsistent and can also take time for the inks to dry. Chemical treatment can be costly to purchase materials and may expose employees to harmful inhalants or respiratory contaminants. UV glue curing is quick and consistent, providing and instantly hardened surface with no harmful chemical exposure. One big advantage to the finishes with UV curing is that it dries clear, allowing multiple layers if need be while sanding down the finish will provide an invisible ‘liquid plastic’ unbreakable bond. Paint or stain can be applied to the finish, giving endless options for applications with various products.
Water-based adhesives
Water-based (or more commonly referred to as waterborne) adhesives are typically formulated from natural polymers and soluble synthetic polymers. These adhesives may be supplied as solutions or formulated as dry powders which must be mixed with water before application. The strength of the adhesive is attained when water is lost from the glue line by evaporation or absorption by the substrate. Because of this requirement, the use of these adhesives requires that at least one substrate is permeable. Where neither substrate is permeable, it is possible to apply a thin coat of adhesive, allow it to dry, and then activate the adhesive by lightly wiping with a wet brush or roller or spraying with water.


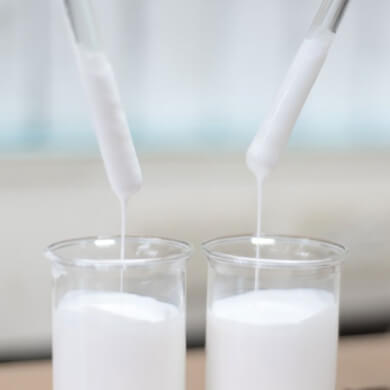
Conclusion
With rapid evolution, the adhesive manufacturers are spending on research and development for the compilation of properties of two or more materials to get the required results. With time and during their development, adhesives have gained a stable position in an increasing number of production processes.