The sheet piling equipments are used in construction to install sheet piles, which are interlocking steel or concrete sheets driven into the ground to construct retaining walls, cofferdams, foundations etc. These equipments utilizes hydraulic or vibratory mechanisms to push or vibrate the sheet piles into the soil, providing stability and structural support.
Components of sheet piling driver equipments
- Hammer or Vibrator Mechanism: Provides the driving force to insert sheet piles into the ground. It can be a hammer that strikes the sheet pile or a vibrator that imparts vibrations for penetration.
- Leader System: Guides and supports the sheet pile during driving. It includes a vertical or inclined structure that allows precise positioning of the sheet pile.
- Power Pack: Supplies the necessary hydraulic or diesel power to drive the hammer or vibrator. It often includes pumps, motors, and control systems.
- Winch System: Manages the vertical movement of the leader system, allowing precise control over the sheet pile installation depth.
- Controls: Enables the operator to monitor and control the driving process, this include levers, buttons, and a control panel with feedback on pile depth and other parameters.
- Chassis: Provides a stable platform for mounting the components and ensures the overall stability of the sheet pile driver during operation.
- Counterweight: Balances the weight of the hammer or vibrator, enhancing stability and efficiency during sheet pile driving.
How do sheet pile driving equipments operate?
Transport and setup sheet pile driving equipment on stable ground.
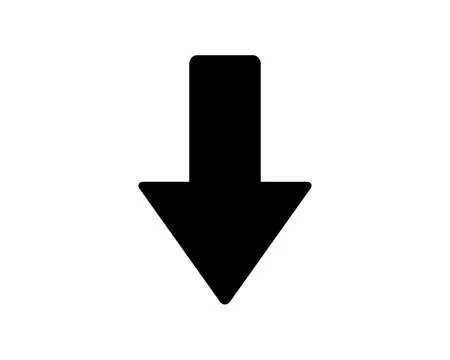
Align with designated sheet pile placement and attach sheet pile using clamps or hydraulic arms.
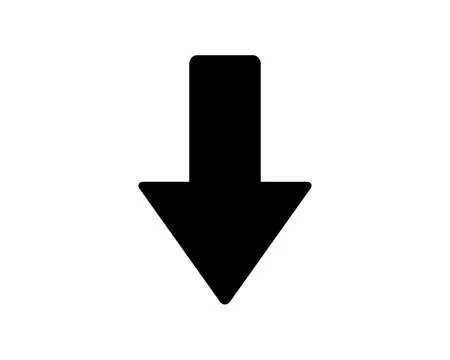
Power on a hydraulic system or vibratory motor.
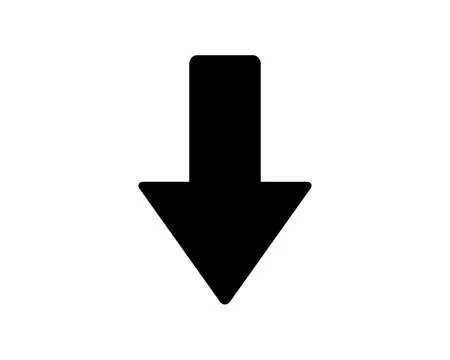
Lower sheet pile for stable positioning.
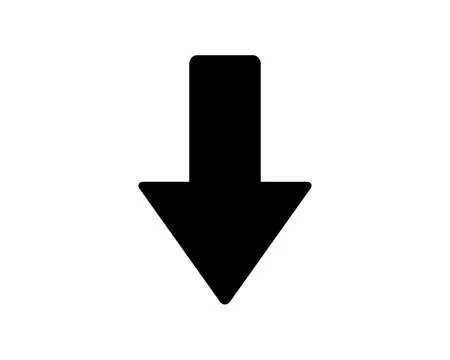
Drive sheet pile using lifting and vibration system, adjusting force and alignment as needed.
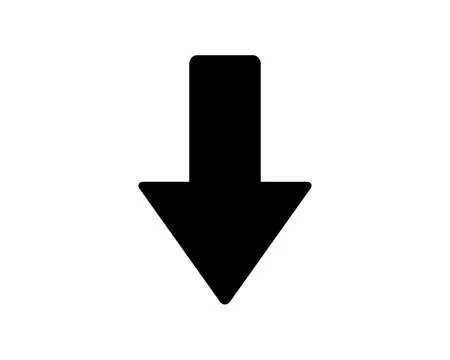
Continue driving until the sheet pile reaches the required depth for structural support.
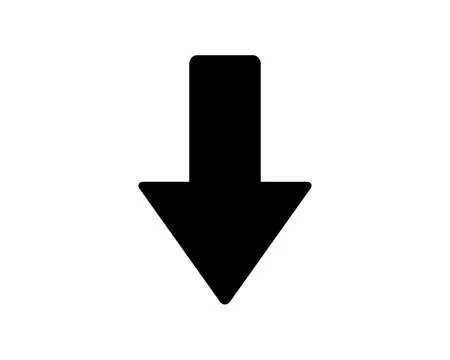
Reverse driving mechanism for sheet pile extraction if necessary.
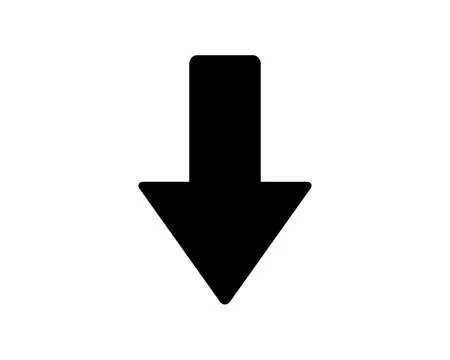
Repeat the process for additional sheet piles if multiple are needed.
Advantages of sheet pile drivers
- Rapid and efficient installation of sheet piles
- Precise placement in construction projects
- Versatility across different soil conditions
- Minimization of vibrations for structural integrity
Different types of sheet pile driving equipments
Diesel Hammers:
Diesel hammers are recognized for their robustness and adaptability, particularly in challenging soil conditions. Fueled by diesel engines, these hammers boast an internal combustion system, generating substantial impact energy. This distinctive feature allows for the efficient driving of sheet piles into dense or hard formations, making them a reliable choice for projects with diverse soil profiles. With their significant mass and force, diesel hammers excel in penetrating considerable depths, offering a steadfast solution for deep foundation construction projects that demand durability and versatility.

Vibratory Hammers:
Vibratory hammers are used for sheet pile driving in granular soils. Their unique feature lies in harnessing vibrational energy through eccentric weights or hydraulic motors, creating high-frequency vibrations that reduce friction during penetration. Beyond their efficiency, a key advantage is their ability to minimize soil disturbance and noise, making them invaluable in urban settings or projects adhering to strict environmental regulations. The rapid installation in specific soil types further enhances their appeal for efficient and eco-friendly sheet pile driving, especially where minimizing environmental impact is important.

Pneumatic Hammers:
Pneumatic hammers, powered by compressed air, play a key role in sheet pile driving, particularly in cohesive soils. Their distinctive feature lies in delivering impact energy effectively across various soil conditions. Often chosen for projects emphasizing environmental concerns, pneumatic hammers minimize diesel emissions, contributing to a greener construction approach. Their adaptability and relatively low environmental impact make them a practical choice for diverse construction projects, providing an efficient and eco-friendly solution for sheet pile installation in varying soil conditions.

Impact Hammers:
Impact hammers, characterized by a striking mechanism and mechanical drive, offer concentrated impact energy for sheet pile driving. Their key feature lies in high driving efficiency, making them suitable for a broad range of soil conditions, from cohesive to granular. The robust construction and adaptability of impact hammers contribute to their reliability in diverse construction scenarios. Whether facing challenging ground conditions or requiring versatility in soil types, impact hammers emerge as an effective and dependable solution for sheet pile driving, showcasing their prowess in varied construction applications.

Applications of sheet pile drivering equipments
- Retaining Walls
- Foundation Support
- Wharf and Quay Walls
- Bridge Abutments
- Trench Shoring
- Cofferdams
- Underground Parking
- Riverbank Stabilisation
- Pipeline Installation
The demand of sheet pile driving equipments
As urban areas expand and undergo redevelopment, the demand for sheet pile drivers increases. Its demand is driven by various factors such as;
- Construction Growth
- Infrastructure Demand
- Urbanisation Needs
- Coastal Development
- Technological Advancements
Conclusion
Sheet pile drivers play an important role in different construction and infrastructure projects. Their versatility, and speed make them indispensable in tasks such as retaining wall construction, foundation support, and flood control. As technology continues to advance, innovations in sheet pile drivers will likely enhance their performance and broaden their applications, contributing to the evolution of modern construction practices.