Trenchless technology can be described as a type of subsurface construction work that requires few trenches or no continuous trenches. Trenchless technology is an underground construction method of installing, repairing and renewing underground pipes, ducts and cables using techniques which minimize or eliminate the need for excavation.
The process of trenchless technology
Trenchless technologies involve methods of new pipe installation with minimum surface and environmental disruptions. Construction can be carried out under a busy highway without closing it to traffic. Traffic congestion is significantly reduced, resulting in less air and noise pollution. Trenchless projects are also less hazardous to workers, as the process can be controlled from the surface. In many densely populated urban areas, open-cut excavations are simply not practical and the social costs are too great. Also, open-cut excavations tend to increase pavement failures and can result in damage to adjacent structures. Trenchless construction lends itself to many infrastructure applications, including gas, water, sewer, pipelines, power, and communications.
Different methods of trenchless technology
Trenchless technology consists of the methods, materials, and equipment used for replacing, rehabilitating, or installing pipes with little or no excavation of the ground above. It also makes it possible to install the utilities under rivers, highways, canals and other obstacles with no disruption of flow and with minimum or no damage to the environment. Given below is an insight of different types of trenchless technologies.
Horizontal auger boring
Horizontal auger boring is a method of trenchless excavation that uses a rotating helical shaft to extract soil while advancing along a more or less level line. The spiral edges of the auger, something akin to a large screw, remove the spoil left behind as the operation progresses. Once the boring reaches its endpoint, the auger is removed, leaving only the casing.
Encasing an auger ensures that whatever is encountered by the cutting head has nowhere else to go but up or out. A machine placed securely into the entrance pit of a drilling operation uses both torque and thrust to move the auger with its casing forward along a horizontal path. The pipe casing is laid in sections, one after another, as forward sections progress through the hole. With horizontal auger boring, the making of the hole and the installation of the pipe are accomplished simultaneously.
Auger boring is best suited for softer ground conditions. An auger boring machine jacks the casing into the ground while the auger turns. Horizontal auger boring is a trusted method in the trenchless construction industry.
Horizontal Directional boring
Directional boring also referred to as horizontal directional drilling (HDD), is a minimal impact trenchless method of installing underground utilities such as pipe, conduit, or cables in a relatively shallow arc or radius along a prescribed underground path using a surface-launched drilling rig. Directional Boring/HDD offers significant environmental advantages over the traditional cut and cover pipeline/utility installations. The technique is routinely used when conventional trenching or excavation is not practical or when a minimal surface disturbance is required.
Directional Boring/HDD is generally accomplished in three principal phases. First, a small diameter pilot hole is drilled along a directional path from one surface point to another. Next, the bore created during pilot hole drilling is enlarged to a diameter that will facilitate the installation of the desired pipeline. Lastly, the pipeline is pulled into the enlarged hole, thus creating a continuous segment of pipe underground and exposed only at the two initial end points. Directional Boring/HDD can be utilized to cross any number of surface obstacles including roadways, railroads, wetlands, and water bodies of varying sizes/depths. The process is suitable for a variety of soil conditions including clay, silt, sand, and rock. Problematic soil conditions include large grain content in the form of coarse gravel, cobbles, and boulders.
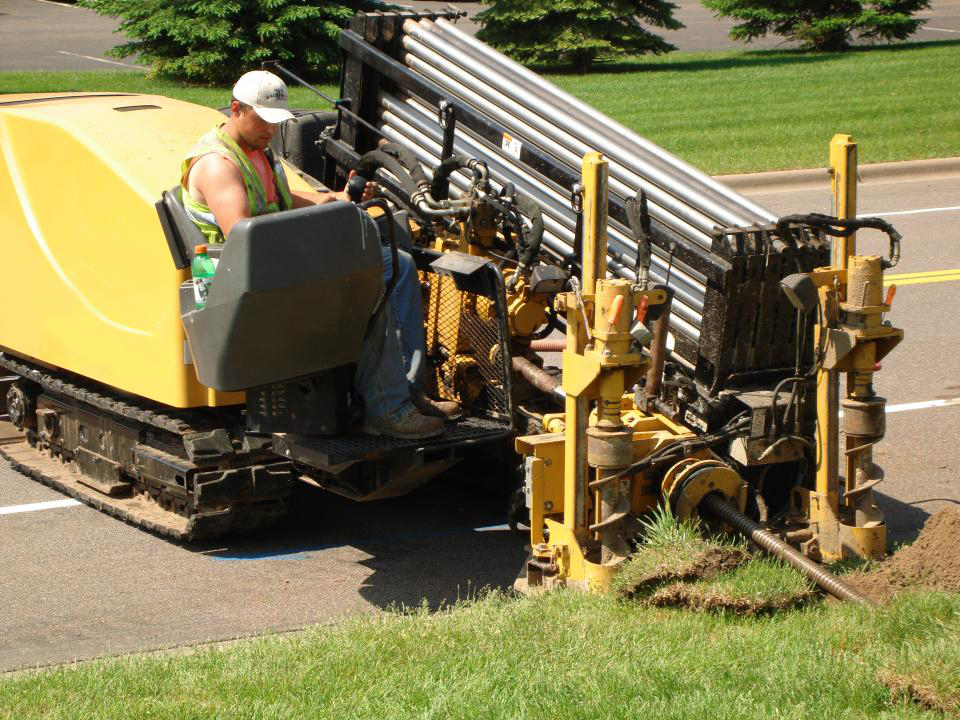
Directional drilling
Directional drilling (or slant drilling) is the practice of drilling non-vertical wells. It can be broken down into four main groups: oilfield directional drilling, utility installation directional drilling (horizontal directional drilling), directional boring, and surface in seam (SIS), which horizontally intersects a vertical well target to extract coal bed methane.
Directional drilling has been an integral part of the oil and gas industry since the 1920s. While the technology has improved over the years, the concept of directional drilling remains the same: drilling wells at multiple angles, not just vertically, to better reach and produce oil and gas reserves. Additionally, directional drilling allows for multiple wells from the same vertical wellbore, minimizing the wells’ environmental impact.
Microtunneling
Microtunneling is a digging technique used to construct small tunnels. These small diameter tunnels make it impossible to have an operator driving the machine itself. Instead, the microtunnel boring machine (MTBM) has to be operated remotely from a control room. Microtunnel boring machines are very similar to normal tunnel boring machines (TBMs), but on a smaller scale. These machines generally vary from 0.61 to 1.5 meters (2 ft 0 in to 4 ft 11 in) but smaller and larger machines have existed. Usually, the operator controls the machine from a control room on the surface. The Microtunneling machine and jacking frame are set up in a shaft at the required depth. The operator is given constant feedback about the machine’s location, orientation and hydraulic devices via a computer console or CCTV camera. Most machines also have video cameras set up to enable the operator to monitor activities in the jacking shaft and at the separation plant. The operator controls the MTBM and the jacking frame from the safety of the control room which is usually situated on the surface, next to the jacking shaft.
In most microtunneling operations the machine is launched through an entry eye and pipes are pushed behind the machine. This is a process often called pipe jacking and is repeated until the Microtunneling machine reaches the reception shaft. As the machine advances, more tunnel liner or pipe is pushed from the starting shaft, through the entry eye. Thus, the speed of the advancing machine is controlled by the speed at which the pipe is inserted into the entry eye via the extension of the hydraulic rams in the jacking frame.
Pilot tube microtunneling
Pilot tube microtunneling uses a guided boring process to jack hollow steel rods through the ground to pilot a hole for the new pipe. The new pipe is then directly jacked behind the pilot tubes. This process avoids long, open trenches, which means minimal intrusion to the area above ground. This method is useful for projects that require pinpoint accuracy for pipe replacement.
Pilot Tube Microtunneling is a multistage version of multiple trenchless methods. The main aspects of this installation process is putting a pilot tube on line and grade and then pipe-jacking steel casing into place followed by removal of the spoils by auger excavation. This method is appropriate for softer soils and lengths up to 400 linear feet. The pilot tube method uses an auger boring unit and pilot tube guidance system, sized for microtunneling. The pilot auger is guided along the design pathway at the appropriate depth to ream the initial bore accurately.
The pilot tube method itself was originally a microtunneling method used to install small service laterals. The process, initiated in a manhole, uses a theodolite — similar to a surveyor’s level — a camera mounted on the auger, an LED target and a computer and screen to provide the operator with information for a precision bore. As the auger/pilot rods emerge at the exit side of the bore, the rods are removed from the auger and the pipe is pulled through the bore.
The microtunneling process’ success has led to its application in larger bores to ensure that piping follows design pathways direction and grade with extreme accuracy.
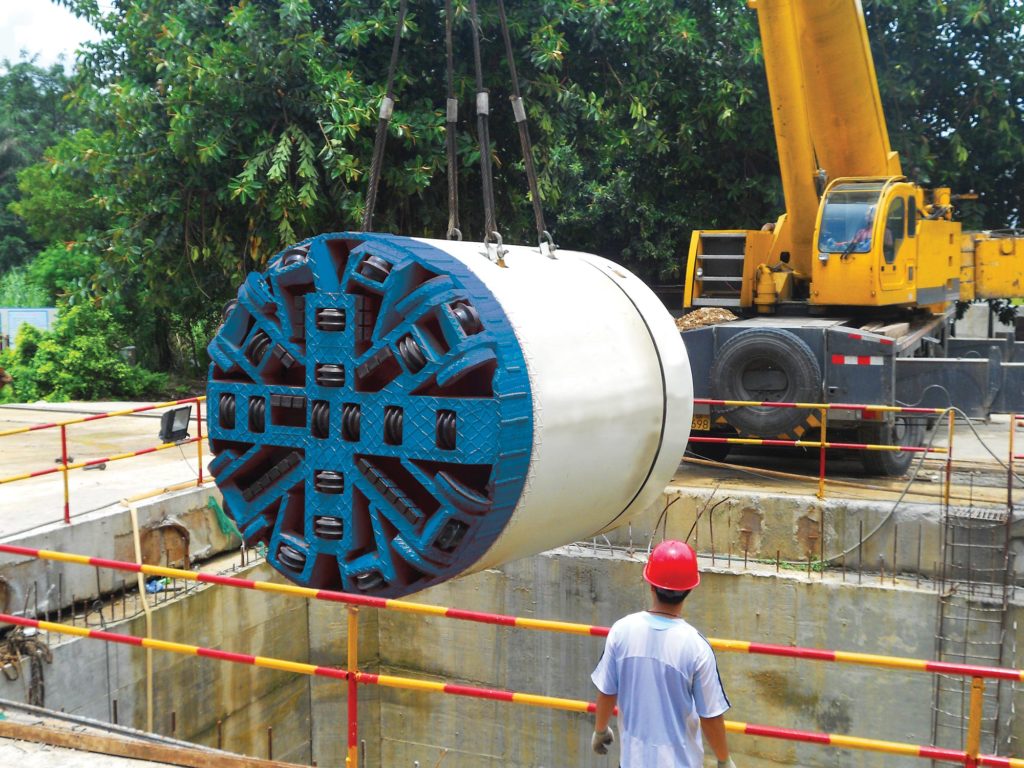
Utility tunneling
A utility tunnel, utility corridor, or utilidor is a passage built underground or above ground to carry utility lines such as electricity, steam, water supply pipes, and sewer pipes. Communications utilities like fiber optics, cable television, and telephone cables are also sometimes carried. One may also be referred to as a services tunnel, services trench, services vault, or cable vault. Smaller cable containment is often referred to as a cable duct or underground conduit. Direct-buried cable is a major alternative to ducts or tunnels.
Pipe lining
Trenchless pipe lining is a great alternative to traditional pipe replacement. Traditional pipe replacement requires more time, more money, more mess and more damage to your yard. Lining differs in that there is much less digging so that it takes less time and manpower to complete. Lining is where a pipe is created within an existing pipe. This pipe is created out of a special epoxy and maintains the strength of a new pipe without damaging the existing structure or landscaping.
The inside of a sewer line needs cleaning and repair if it cracks due to corrosion and tree root intrusion. Using mechanical cutters to clean removes the buildup of roots and corrosion, ensuring cured-in-place-pipe (CIPP), an epoxy liner, adheres to the damaged pipe.
After the pipe is clean, the epoxy saturates a felt liner cut on the outside so that the two-part epoxy adheres to the tube’s inner side. The adhesion makes it impossible for water to flow between the damaged host pipe and liner. Before the deflation and removal of the bladder from the tube, the liner needs to be pulled through the pipe quickly, expanding the rubber bladder inside the epoxy-saturated liner, which allows the epoxy to adhere and cure.
The liner separates the material flowing through the damaged sewer line that is susceptible to failure of the pipe itself once the CIPP liner hardens. Apart from solving the issue of a cracked sewer line, the CIPP liner is also a structural tube, which means that you will still have a serviceable trenchless pipe repair even if the host pipe deteriorates.
Trenchless technology brings an alternative to sewer line replacement and repair. The process involved is known as cured-in-place-pipe (CIPP), and it entails the creation of a new pipe within the existing pipe. Special epoxy resins, most commonly nu flow, create the structural strength of the new pipes without damaging structures, interior walls, floors, sidewalks, landscaping, or streets.
Pipe bursting
Pipe bursting is a trenchless method of replacing buried pipelines (such as sewer, water, or natural gas pipes) without the need for a traditional construction trench. “Launching and receiving pits” replace the trench needed by conventional pipe-laying.
There are five key pieces of equipment used in a pipe bursting operation: the expander head, pulling rods, a pulling machine, a retaining device, and a hydraulic power pack. Today’s expander heads have a leading end much smaller in diameter than the trailing (bursting) end, small enough to fit through the pipe that will be replaced. The smaller leading end is designed to guide the expander head through the existing pipe; earlier models did not have this feature and lost course at times, resulting in incomplete pipe bursts and project failures. The transition from the leading end to the trailing end can include “fins” that make first contact with the existing pipe. Using these fins as the primary breaking point is a very effective way to ensure that the pipe is broken along the entire circumference. A machine is set in the receiving pit to pull the expander head and new pipe into the line. The head is pulled by heavy, interlocking links that form a chain. Each link weighs several hundred pounds. All of the equipment used in a pipe bursting operation is powered by one or multiple hydraulic power generators.
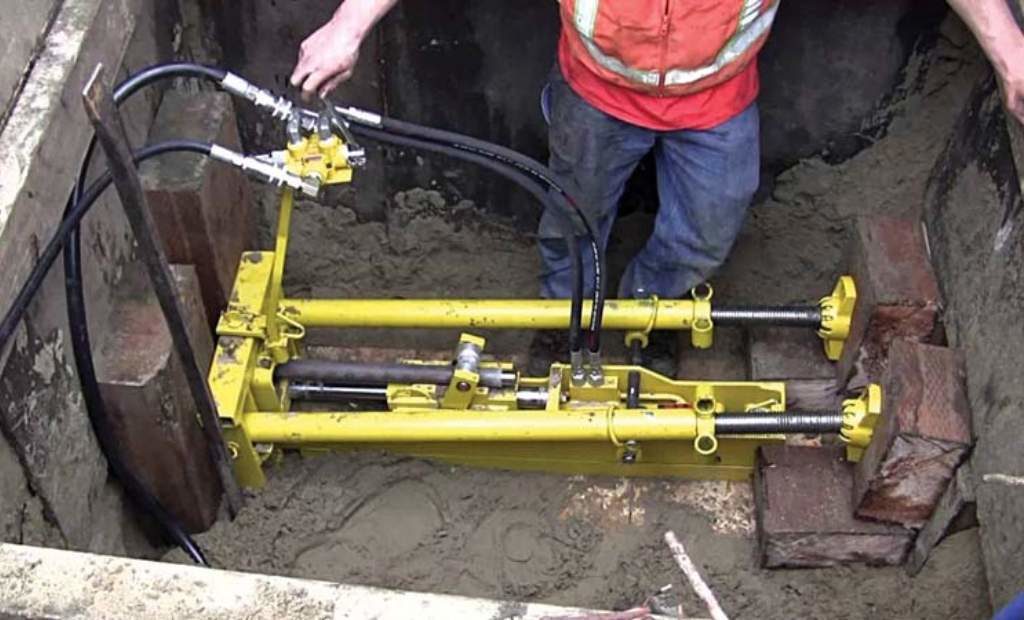
Pipe ramming
Pipe ramming (sometimes also called pipe jacking) is a trenchless method for installation of steel pipes and casings. Distances of 30 m (150 feet) or more and over 1,500 mm (60 inches) in diameter are common, although the method can be used for much longer and larger installations. The method is useful for pipe and casing installations under the railway lines and roads, where other trenchless methods could cause subsidence or heaving. The majority of installations are horizontal, although the method can be used for vertical installations.
The method uses pneumatic percussive blows to drive the pipe through the ground. The leading edge of the pipe is almost always open, and is typically closed only when smaller pipes are being installed. The shape allows a small overcut (to reduce friction between the pipe and soil and improve load conditions on the pipe), and directs the soil into the pipe interior instead of compacting it outside the pipe. These objectives are usually achieved by attaching a soil-cutting shoe or special bands to the pipe. Further reduction of friction is typically achieved with lubrication, and different types of bentonite and/or polymers can be used (as in horizontal directional boring) for this purpose. Spoil removal from the pipe can be done after the entire pipe is in place (shorter installations). If the pipe containing the soil becomes too heavy before the installation is complete, the ramming can be interrupted and the pipe cleaned (longer installations). Spoil can be removed by auger, compressed air or water jetting.
Pipe eating
Pipe eating is a replacement process similar to pipe jacking, where powerful hydraulic jacks force a pipeline into a bore as the bore is created. Also known as pipe replacing, in the pipe eating process, a drill destroys the pipe and removes its fragments while inserting a new pipeline or sewer – of the same size or large – in the original bore.
Pipe eating is similar to pipe bursting and isn’t as unappetizing as it sounds. The old pipe remains in the ground where it’s ground into small pieces by drill while a hydraulic jack forcing a new pipe into place, The flow of drilling fluid from the BHA (bottom hole assembly) carries the fragments of the old pipe away while the drill and jack continue to ram the new — and possibly larger — pipe into place.
Pipe Jacking
Pipe jacking is a trenchless technology method similar in principle to microtunneling. The method uses a horizontal jacking force to advance the pipe. Unlike microtunneling, pipe jacking requires personnel entry inside the pipe to carry out excavation and spoil removal (URS, 2002). The method is best suited to large-diameter pipes in order to provide adequate space and ventilation for workers (Iseley and Gokhale, 1997).
Pipe jacking is a cyclic method that uses thrust to force pipes through the ground. After each pipe segment has been installed, the ram of the jack is retracted so that another pipe segment can be placed in position and the jacking cycle can begin again. Once the jacking process is started, it should not be interrupted to prevent the pipes from freezing in place. Pipe ends must be parallel to assure uniform distribution of forces. The spoil material is transported to the inside of the pipe. Spoil removal can be accomplished manually or mechanically. Spoil conveyance systems include wheeled carts or skips, belt or chain conveyors, slurry systems, auger systems, and vacuum extraction systems. Soil is removed by hand mining or mechanical excavation within a shield or by a tunnel boring machine. If there is a possibility of the excavation face collapsing, various soil stabilization techniques, including dewatering and grouting, may be required
Moling
In the construction industry, moling is a trenchless method used to lay pipes. During the moling process, a pneumatically-driven machine known as a mole forces its way through the soil along the desired path of the pipe. Moling avoids the need to dig a trench and can be used to lay water pipes and the heating coils of heat pump systems.
Recently moles that are steerable have been developed allowing an operator to correct the track of the mole and to achieve curved bores. Mole The standard approach to moling is to dig a hole about 1 m square and 2 m deep. Such a hole is small enough that it can be dug by hand instead of by machine in inaccessible locations. The mole is then entered into the earth on the horizontal face at the bottom of this hole. A destination hole of similar proportions is also dug, and this is where the mole emerges. The mole itself is a steel cylinder about 60 cm long and 6 cm in diameter. It works as a pneumatic cylinder with pulsed compressed air causing the head of the mole to repeatedly hammer against the soil in front of the mole. Once the mole has passed through the earth the pipe can be pulled through the long horizontal hole.
Hydro excavation
Hydro excavation is a method of removing soil through the use of highly pressurized water. It is a non-destructive method, using an air vacuum to evacuate soil in a controlled manner. It safely brings up the soil and transfers it to the debris tank. Because of this it is the perfect method to use for exposing utilities.
Earlier excavation processes such as hand digging or augers often caused safety, hazards, delays and possibly service interruptions from damage. With hydro excavation, pipes can be installed, repairs can be done to existing lines, and new lines of utilities can be installed with fewer safety and service issues.
Hydro excavation has a lot of functions. One of these functions is to expose utilities. Checking the utilities occasionally needs to be done to ensure that they are in their proper condition. It is also needed to see if there are parts that have been damaged. The hydro excavation process allows excavation and digging to be done without disturbing the surrounding soil and underground utilities. There will be no problem even when the ground is frozen. The heater that is installed in the hydro excavation equipment can remove even frozen soil efficiently.
It also eliminates unnecessary traffic congestion and it provides a cleaner excavation site. Moreover, hydro excavation is cost effective. It reduces the unnecessary costs that may be spent if the manual or mechanical excavating method is used. These advantages have made hydro excavation the preferred method for exposing utilities.
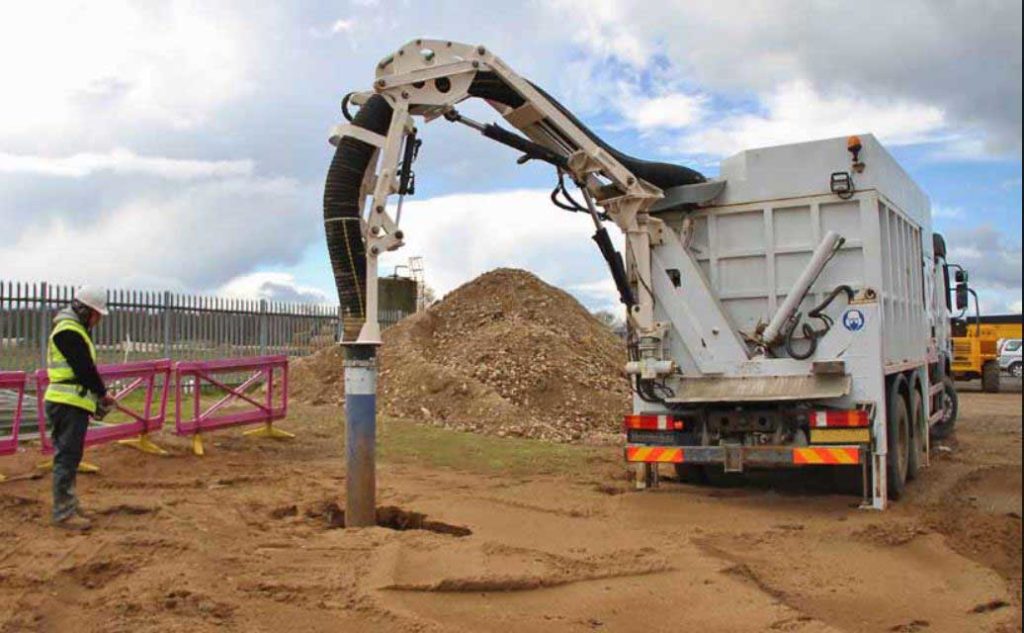
Guided drilling
Guided drilling is defined as a process, or trenchless construction method, which involves the use of a pilot tube to control the desired route through the ground, followed by auger boring, to set the pipe in place. The pilot tube can be precisely controlled to create a path for the auger to follow. This technique is useful in directional drilling, especially in displaceable ground.
Guide drilling employs an excavation or soil displacement with compact lightweight rig for rapid mobilization. Small diameter jets mechanized cutting tools or displacement heads attached to a flexible drill string are positioned to form a bore as the head is thrust forward. The drilling head is launched from the surface at an inclined angle. Controlling the orientation of a slant face at the head affects steering in both vertical and horizontal planes. Monitoring of the alignment takes place using a transmitter in the head and a locating device at ground level. I having established the pilot bore; back reaming equipment is drawn through the hole to enable it to accept the product pipe, duct, or cable using an impact mole.
Jack and Bore
Jack and bore, also known as auger boring, is one of the most popular methods of trenchless technology. Jack and bore is a process of simultaneously jacking casing while removing the spoil material by means of an auger. A rotating cutting head is attached to the leading edge of the auger string. The spoil is transported back by the rotation of auger flights within the steel pipe casing being placed.
The most common type of jack and bore for transportation applications is the track system. The main parts of the track system include the supporting track, boring machine, casing pipe, cutting head, and augers. Optional components include a casing lubrication system. Lubricants are typically bentonite and polymer mixtures. Once launched, jack and bore is typically unguided. Subsurface obstructions can cause large deflections. Recent technological improvements allow significantly greater accuracy for shorter drives.
One of the main benefits of jack and bore is that workers are not required to enter the shaft during trenchless construction. The rotating auger brings the spoil material back to the machine. Hydraulic jacks at the boring machine are used to advance the casing. The track system must be positioned on the same line and grade as the bore (Iseley and Gokhale, 1997). This is usually the most critical part of the project. Jack and bore requires a relatively high skill level of the operator to achieve good results.
Conclusion
The use of trenchless technology in your piping project can help save costs, protect the environment, and minimize surface disruptions. When it comes to Trenchless Technology, not having to dig a trench is the whole point. Trenchless technology is tunneling below the surface to install service lines like water or gas pipes, electric or telecommunication cables, without anyone noticing on the surface. This method also makes it possible to install utilities under rivers canals and other obstacles with no disruption of flow and with minimum or no damage to the environment. Trenchless methods have been used for the last 50 years, but these days, with advancements in technology for excavation and guidance systems, trenchless methods are becoming more commonly used around the world when soil conditions and location permits.