Silicone sealant is an adhesive used to prevent air and water from getting between two surfaces by sealing, bonding, filling gaps and joints The sealant consists of a silicone polymer that solidifies upon exposure to moisture in the air. This solidification process creates a resilient, rubbery seal capable of withstanding water, temperature fluctuations, and diverse environmental conditions. They come in various formulations, including different colours and levels of flexibility, to suit specific needs and applications.
Advantages of silicone sealants
Silicone sealants provide numerous advantages as discussed below;
- Exhibit high flexibility, accommodating building material movements without cracking.
- Highly resistant to extreme weather conditions, including rain, snow, and intense sunlight.
- They resist UV radiation, preventing deterioration when exposed to sunlight.
- Adhere well to various construction materials like glass, metal, concrete, wood, ceramics, and plastics.
- Create effective waterproof barriers, blocking water and moisture infiltration.
- Maintain properties across wide temperature ranges, from freezing cold to high heat.
- Offer good resistance to chemicals, acids, and alkalis, suitable for environments with exposure.
- Emit low volatile organic compounds (VOCs), enhancing indoor air quality.
- Non-corrosive to metals, reducing risks of degradation or rusting on metal surfaces.
Types of silicone sealants
1. Acetoxy Cure Silicone Sealants: These are the most commonly used silicone sealants. As they cure, they release acetic acid, which causes the vinegar-like odour. They adhere well to a wide variety of materials such as glass, metal ceramics etc.
2. Neutral Cure (Oxime) Silicone Sealants: These sealants release non-acidic byproducts during curing. This makes them suitable for a broader range of surfaces, including metals and porous materials. They typically offer superior adhesion, weather resistance, and have a milder odour compared to acetoxy sealants. They are often chosen for applications where compatibility with different materials is essential.
3. Alkoxy Cure Silicone Sealants: Similar to oxime sealants, these produce non-acidic curing byproducts. They offer strong adhesion and weather resistance, frequently applied in outdoor scenarios. Notably, they possess excellent UV resistance, making them ideal for applications exposed to sunlight.
4. Condensation Cure Silicone Sealants: These silicone sealants are also known as tin-cure or tin-addition cure sealants,these sealants use moisture in the air to initiate the curing process. They are commonly used for bonding, sealing, and encapsulating various materials due to their flexibility, durability, and resistance to moisture, heat, and chemicals.
5. General Purpose Silicone Sealants: These acetic sealants are used for sealing, gaps and joints between surfaces. It comprises of silicone based compound that hardens when it comes in contact with moisture in the air. It easily adheres to glazed ceramic tiles, glass, aluminium, etc. This sealant offers strong resistance to ozone, UV radiation, and extreme temperatures. It’s commonly applied in plumbing, sanitary work, metal-to-metal joints, duct sealing, and aluminium-glass or standard glazing.
6. Neutral Silicone Sealants: These are non-staining, neutral-cure silicone sealants that are used for granite and marble applications. It’s suitable for both indoor and outdoor use, boasting resistance to ozone, UV, and temperature variations. This neutral sealant is apt for non-structural glazing, panel stiffening, joining bathtubs and washbasins, sealing windows, door frames, and various materials like marble, stone, concrete, brick, and plastic.
7. Acryfill Silicone Sealants: These types of sealants are manufactured from acrylic emulsions and specialised chemicals, this gun-grade sealant offers a thin, easily paintable fill. It’s perfect for sealing low-movement joints, especially in uPVC and aluminium window applications. It’s used to seal window and door frames, duct holes, joints between ceilings and windows, and low-movement joints in blockwork.
8. Hybrid Silicone Sealants: These types of single component elastic sealants used for interior and exterior bonding and sealing in construction. It’s excellent for transparent and elastic bonding of various materials like glass, metal, and panels. It’s applied in interior glass bonding, metal and building industry bonding, and elastic bonding of panels and profiles on common substrates.
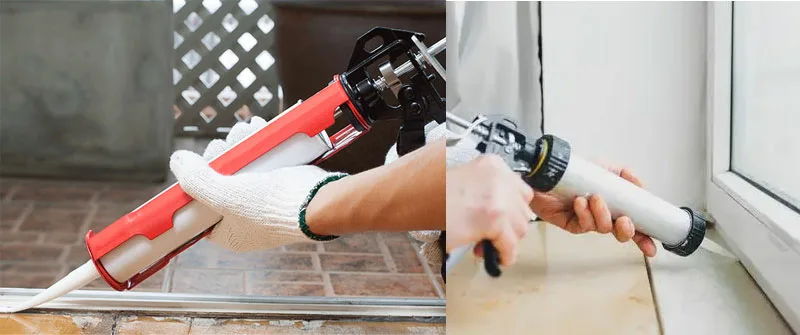
Applications of silicone sealants
Silicone sealants find numerous applications in construction due to their versatile properties. Here are some common applications of silicone sealants in construction:
1. Window and Door Sealing: used to seal gaps and joints around windows and doors, preventing drafts, water leakage, and improving energy efficiency.
2. Expansion Joints: applied to expansion joints in concrete and other materials to accommodate movement caused by temperature changes, preventing cracks and maintaining structural integrity.
3. Curtain Wall Glazing: used in curtain wall systems to bond glass panels to metal frames, providing weatherproofing, structural support, and aesthetics.
4. Sanitary Areas: used in bathrooms, kitchens, and other wet areas to create waterproof and mold-resistant seals around sinks, bathtubs, showers, and tiles.
5. Roofing: used to seal roof joints, flashings, and penetrations, preventing water infiltration and maintaining the integrity of roofing systems.
6. Concrete Joints: used in construction joints and control joints in concrete slabs to prevent water penetration and maintain durability.
7. Structural Bonding: used in structural glazing applications, bonding glass or other cladding materials to frames without the need for mechanical fasteners.
8. Fire Barriers: used to create fire barriers by sealing joints and penetrations in fire-rated walls and floors, preventing the spread of flames and smoke.
9. Electrical Sealing: used to seal electrical boxes, connections, and components to protect them from moisture, dust, and environmental elements.
10. Acoustic Insulation: used to fill gaps and joints in walls, floors, and ceilings to improve acoustic insulation and reduce sound transmission.
12. Glass Bonding: used for bonding glass to glass or glass to metal in applications such as glass railings, partitions, and structural glazing.
13. Swimming Pools: used to seal joints and gaps in swimming pool construction to prevent water leakage and ensure a watertight seal.
14. Atriums and Skylights: used to seal joints and gaps in atriums, skylights, and canopies, preventing water leakage and maintaining transparency
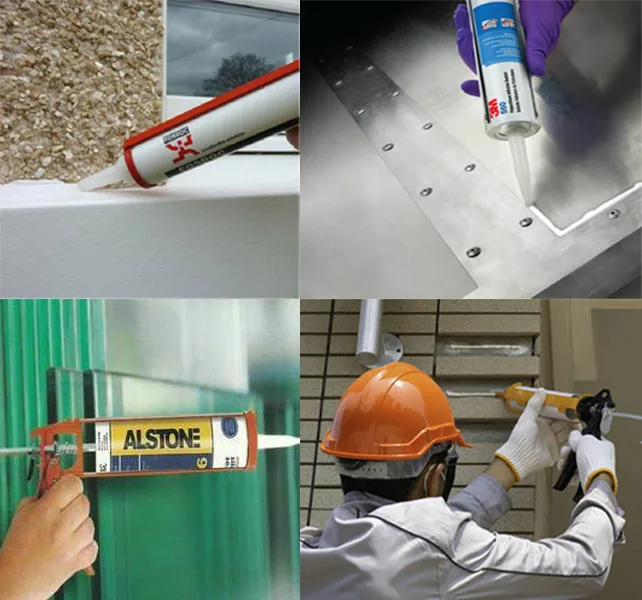
These are just a few examples of the diverse applications of silicone sealants in construction.
Application method of silicone sealants
Here’s a comprehensive overview of the application method for silicone sealants in construction:
1. Surface Preparation:
- Clean and dry surfaces: Ensure that the surfaces to be sealed are clean, dry, and free of dust, dirt, oil, and debris. Proper adhesion depends on a clean substrate.
- Remove old sealant: If there is existing sealant, remove it using appropriate tools before applying the new silicone sealant.
- Check for compatibility: Ensure that the surfaces are suitable for silicone sealant application, and that they won’t react negatively with the sealant.
2. Selecting the Right Silicone Sealant:
- Choose the appropriate type: Select a silicone sealant suitable for the specific application (e.g., weatherproofing, expansion joints, window installation, etc.).
- Consider environmental factors: Take into account factors such as temperature variations, UV exposure, and potential water exposure when selecting the sealant.
3. Gather Materials:
- Silicone sealant cartridge: Choose the correct type and quantity of sealant cartridges.
- Caulking gun: Use a heavy-duty caulking gun capable of handling construction sealant cartridges.
- Nozzle cutter: Cut the nozzle at a 45-degree angle to achieve the desired bead size.
- Backer rod (if needed): For wider joints, use a backer rod to control sealant depth and ensure proper adhesion.
4. Load and Prepare the Cartridge:
- Insert the silicone sealant cartridge into the caulking gun.
- Cut the nozzle tip to the desired size for the joint width.
- Apply masking tape to the surfaces surrounding where you’ll be applying the sealant to create neat lines and make cleanup easier
5. Application:
- Hold the caulking gun at a 45-degree angle to the surface.
- Start at one end of the joint and apply an even and continuous bead of sealant, moving steadily along the joint’s length.
6. Tooling and Smoothing:
- Use a suitable tool (caulk smoother or spatula) to shape and smooth the sealant bead, ensuring proper contact with both surfaces.
- Maintain a consistent angle and pressure for a uniform appearance.
7. Masking Tape Removal:
- Gently remove any masking tape before the sealant begins to skin over or cure. This prevents the tape from pulling up the sealant.
8. Curing Time:
- Allow the silicone sealant to cure according to the manufacturer’s guidelines. Curing times may vary based on temperature and humidity.
9. Inspection:
- After the sealant has cured, inspect the joint to ensure proper adhesion and coverage.
10. Clean Up:
- Remove excess sealant with a plastic putty knife or a suitable solvent before it fully cures.
Conclusion
Silicone sealant adhesives have become essential due to their versatility and resilience against challenging environmental conditions. These adhesives play a vital role by sealing gaps and joints, effectively blocking the entry of water, air, and moisture. This not only contributes significantly to the durability and effectiveness of structures but also extends their lifespan. As construction standards continue to evolve, silicone sealant adhesive continues to evolve as well, offering improved formulations that meet the demands of modern building practices.
Image Source: www.fosroc.com, alstoneindia.in, bondzil.com, 3mindia.in