Flyovers, as essential infrastructure components, face numerous challenges that can affect their structural soundness over the years. Factors such as constant vehicular wear, the impact of environmental conditions, and potential seismic disturbances can compromise the durability and safety of these structures. With the evolution of vehicular traffic and design norms, it often becomes vital to reinforce and modify original designs to ensure they remain fit for their intended purpose.
The primary aim is to upgrade the flyover’s structural strength, making it more resilient to various stress factors and extending its useful life. A proven method in such scenarios involves the use of Carbon Fiber Wrap technology.
The Reliance Carbon Fiber products are typically applied as a flexible fabric. Once installed, these fabrics are combined with a resin matrix, transforming them into a formidable, rigid material that boasts an unparalleled strength-to-weight ratio.
A thorough understanding of the site’s historical background, the problems it faced, and the reasons for opting for a retrofitting method were established. Following this, a bespoke solution tailored to the specific needs of the site was proposed. The entire process of application, from site preparation to the final steps of the retrofitting process, is documented in this study.
This case offers a perspective on the significance and efficacy of such retrofitting measures, particularly in areas susceptible to distinct structural issues.
Site Background:
Over the course of 50 years, the flyover experienced degradation, necessitating retrofitting to enhance its load-bearing capacity. As the flyover neared its original design capacity, the retrofitting process became indispensable to ensure continuous safety and functionality. The retrofitting effort utilized Reliance Carbon Fiber Reinforced Polymer (CFRP) solutions to improve the load-bearing capability of the structure.
Solution Provided:
The Carbon Fiber Wrapping Solution implemented for this site included:
- Applying four layers of carbon fiber to the underside of the girder along its entire length.
- Applying a single layer of carbon fiber in a U-wrap configuration, spanning one-third of the span’s length from both ends of the girder.
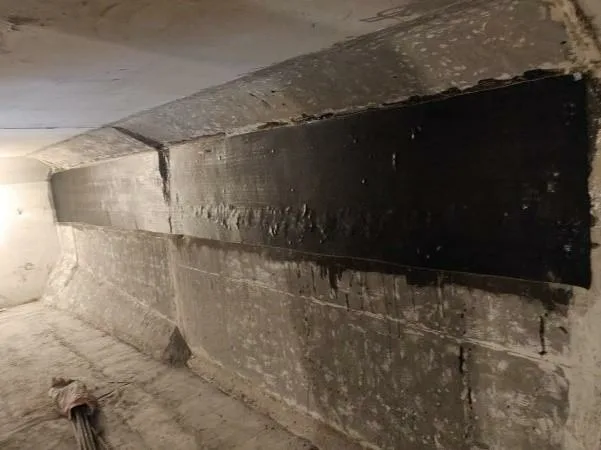
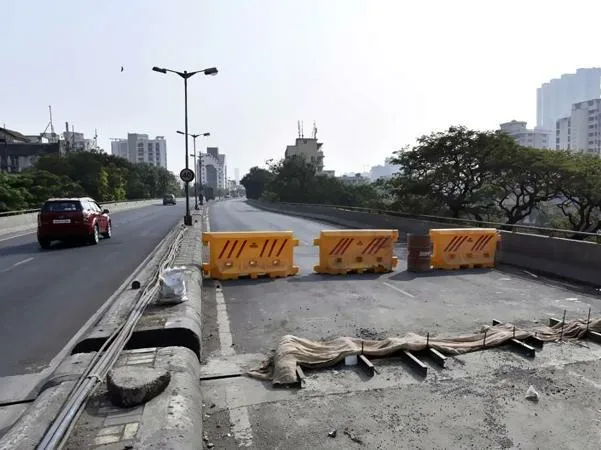
Carbon Fiber Wrapping Solution for the Flyover
Materials Used:
- Relinforce™ C Fab 600- Carbon Fabric for FRP Structural Strengthening
- Relinforce™ EP Putty- Two Component Thixotropic Moisture Sensitive Epoxy Putty for Levelling Surfaces
- Relinforce™ Fab S- Two Component epoxy resin system for impregnation & bonding
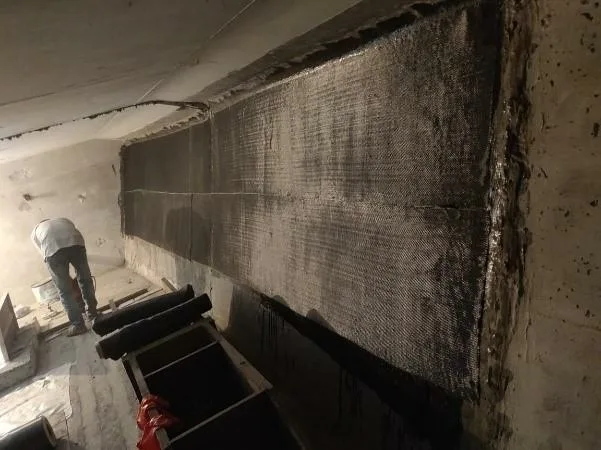
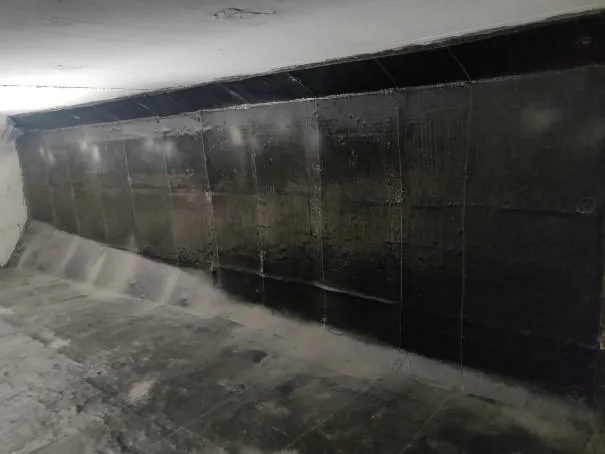
Relinforce™ products used for Flyover Retrofitting
Advantages of Using Relinforce™ products in the Flyover Project:
- Offered quicker repairs compared to conventional methods without necessitating hot work like welding.
- Completion of the entire bridge wrapping process occurred within 12-18 months due to straightforward application.
- The flyover remained operational during the repair work, eliminating the need for road blockages typically associated with conventional repair methods.
- Minimal change in the structure’s weight was observed.
Application Process
- Considering the flyover’s age, micro-concreting was performed, and undulations were smoothed using Relinforce™ EP Putty, resulting in a suitably even surface for CFRP application.
- Relinforce™ facilitated a primer-less system for CFRP wrapping on concrete structures.
- Following surface preparation, Relinforce™ C Fab 600 was applied to girders, beams, and pillars, assisted by Relinforce™ Fab S in accordance with the specified consumption.
- To fulfil site requirements, four layers of carbon fiber were applied along the beam’s length.
- Upon the installation of four horizontal carbon fiber layers, the U-Wrapping process commenced. These four layers played a significant role in bolstering the beam’s strength and overall structure support.
- The U-Wrapping process provided essential support for the applied carbon fabric layers, further enhancing the structure’s strength.
- The CFRP-wrapped fabric was subsequently coated with epoxy and polyurethane-based coatings to shield against environmental degradation of the epoxy saturant and enhance the flyover’s aesthetics.
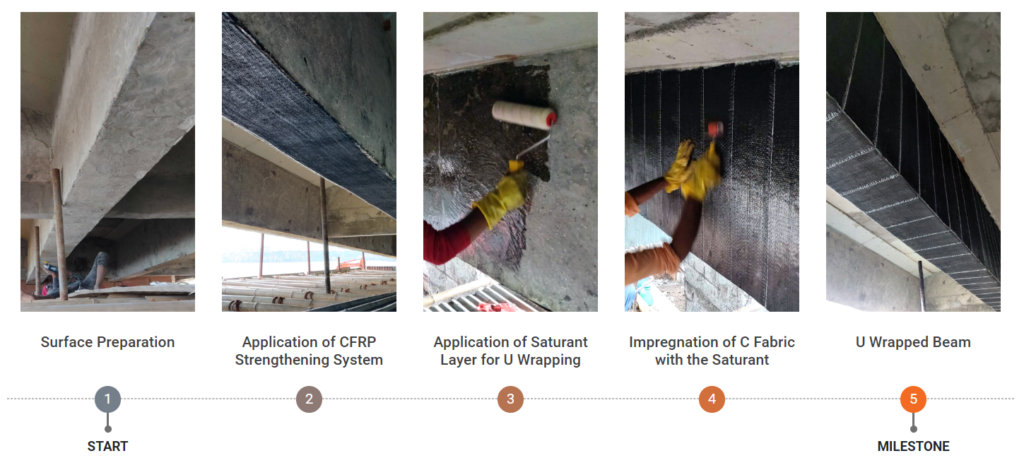
Completion Timeline:
The project was completed within 24 months, encompassing all stages from surface preparation to the final wrapping process.
Final Report:
The strategic incorporation of carbon fiber polymers not only bolstered the structural integrity of the flyover but also exceeded expectations by substantially augmenting load capacity and effectively addressing expansion joint challenges.
The case study underscores the importance of continuous innovation in the realm of civil engineering, setting a precedent for sustainable and adaptable methods that can be applied to similar projects.
About Relinforce™ Composite solution
Relinforce™ range of Carbon wrap & Glass Fiber-reinforced polymer products are manufactured and supplied under Reliance India’s Composites Solution Division. Reliance Industries Limited is India’s largest private and one of the most profitable private sector companies and the first Indian Fortune 500 company.
Relinforce™ product range is used for structural strengthening & protection of the structural members using guidelines that conform to international standards. These products just don’t repair degraded structures, but it makes the structures stronger even against harmful effects of seismic forces or further corrosion. There is a wide range of products combined with outstanding combinations of properties, such as low weight, immunity to corrosion, excellent mechanical strength and stiffness to tackle the issues on hand with ease.
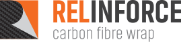
Reliance Industries Limited
Vadodara Composites Division, Vadodara – Halol Expressway, Vill – Asoj, Taluka – Waghodia, Vadodara, Gujarat 391510
Phone:+91-95104-03668
Email: Petchem.Relinforce@ril.com