Sheet piles are sections of sheet materials with interlocking edges that are driven into the ground to provide earth retention and excavation support. Sheet piles are most commonly made of steel, but can also be formed of timber or reinforced concrete. They are installed in sequence to design depth along the planned excavation perimeter or seawall alignment. The interlocked sheet piles form a wall for permanent or temporary lateral earth support with reduced groundwater inflow. Anchors can be included to provide additional lateral support if required.
Sheet piles are commonly used for retaining walls, land reclamation, underground structures such as car parks and basements, in marine locations for riverbank protection, seawalls, cofferdams, and so on. Permanent steel sheet piles are designed to provide a long service life. Vibratory hammers are typically used to install sheet piles. If soils are too hard or dense, an impact hammer can be used to complete the installation. For the development of sheet piles, there are two main techniques: hot-rolled and cold-formed. At high temperatures, hot rolled piles are produced and the interlocks appear to be stronger and more resilient.
Advantages of sheet pile;
- Recyclable and reusable.
- Available a wide range of lengths, size and steel options.
- Can be used for temporary and permanent structures.
- Can be installed using silent and vibration-free methods.
- Quicker installation than contiguous or secant walls.
- Cofferdams can be constructed in almost any desired shape,
- Provide a close-fitting joint to form an effective water seal.
- Light in weight, making lifting and handling easy
- Length and design of the pile are easily adjustable
- Joints are designed to withstand the high pressure necessary for them to be placed in place
- A little maintenance is needed above and underwater
Different types of sheet piles
Steel sheet pile
It is available in various cross-sections and shapes. They can be hot-rolled sheet piles, cold-rolled, or cold-formed sheet piles. Steel sheet piles durability is enhanced with the aid of corrosion protection measures such as coating and cathodic protection. Steel is the most common form of sheet piles as it has good resistance to high driving stresses, excellent water-tightness, and can be increased in length either by welding or bolting. They are connected by interlocking. There are four basic forms of steel sheet piles, Normal sections, Straight web sections, Box sections and Composite sections.
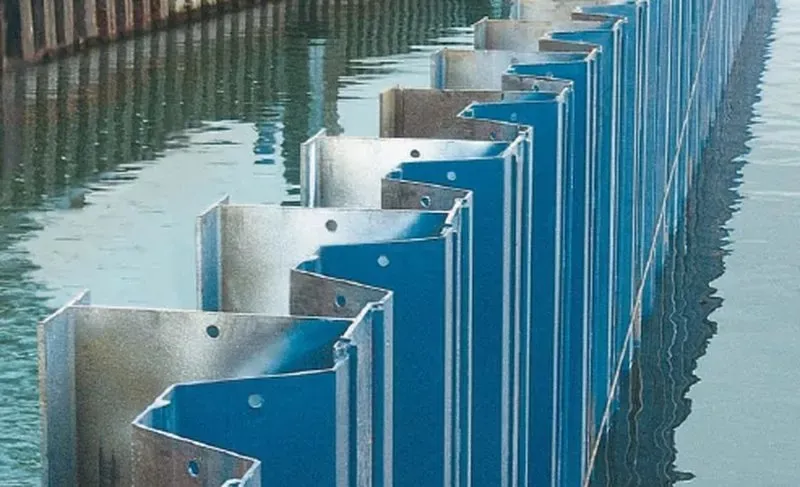
Vinyl sheet pile
An effective alternative to steel sheet piling for bulkheads, seawalls and cutoff walls. They are also superior to alternative materials like concrete and wood. The main advantage of vinyl sheet piles is the superior corrosion resistance when exposed to seawater, where no oxidation occurs.
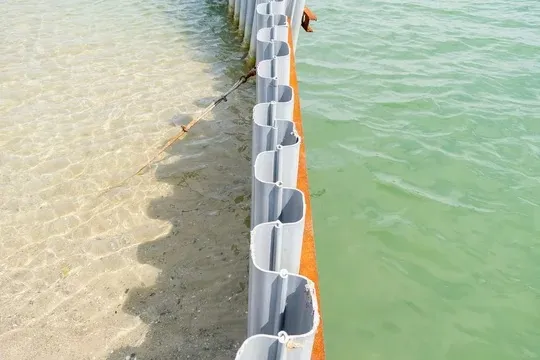
Wooden sheet pile
These are used for temporary structures and braced sheeting in excavation works. If it is to be used in permanent structures above the water table, some form of preservative treatment shall be given. Even given the preservative treatment the life of timber sheet pile is short, Timber sheet piles are joined utilizing tongue and groove joints. Timber piles are not suitable in the strata consisting of gravel and boulders.
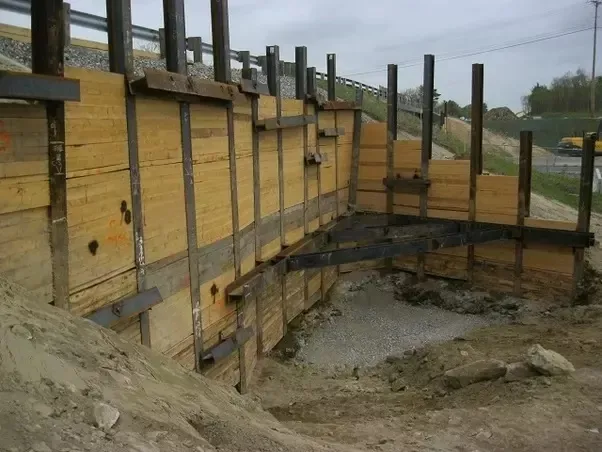
Concrete sheet pile
These are usually connected by tongue and groove joints. They are commonly used in permanent river embankments, canals and other marine structures. The toes of the piles are usually cut with an oblique face to facilitate easy driving and interlocking, while the heads are finished off by casting a capping beam. These pre-cast concrete members are usually joined by tongue and groove joints. They are relatively heavy and bulky and displace large volumes of soil during driving. This large volume displacement increases the driving resistance. Handling and driving should not damage the piles and suitable reinforcement shall have to be provided.
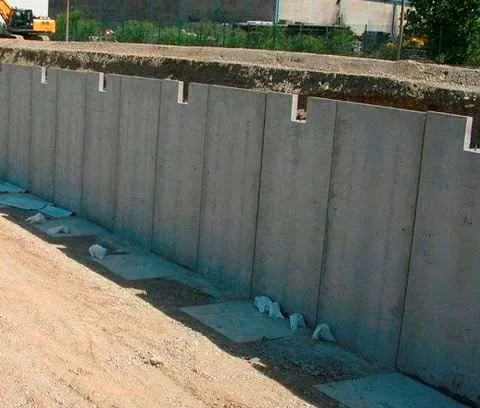
Method of sheet piling
Driving must be carefully monitored and should stop immediately if the pile ceases to penetrate the soil, before moving on to the next pile along. In some cases, several adjacent piles will be unable to penetrate to the design depth. At this point, effort should be made to remove the obstacle, either by partial excavation or using a water jet. There is an acceptable number of ‘under-driven’ sheet piles, but this will vary according to the specific design requirements.
Guide controls should be used to counter this. One technique is to drive piles in panels. This involves pitching and driving two piles to part or full penetration at either end of a panel of piles. The panel is therefore supported by the ‘bookended’ piles during driving to their final position. The pair left on the end then forms the support of the next panel along. Another technique is to use trestles and walings to support and position sheet piles during driving. Vibratory hammers are often used to install sheet piles, although if soils are too hard or dense, an impact hammer can be used. At certain sites where vibrations are a concern, the sheets can be hydraulically pushed into the ground. The sequence is as followed;
- Situ soil to placed behind of the proposed structure
- Drive the sheet piles
- The level of the anchor backfilled up and placed the system of the anchor. and backfill up to the height of the wall
- Dredge the front side of the wall
Conclusion
Sheet piles are designed to interlock with each other. They are installed in sequence along the planned excavation perimeter. When arranged together, they form a wall for permanent or temporary earth support, along with anchors to provide extra lateral support.