Reactive Powder Concrete (RPC) is an advanced construction material that differs significantly from traditional concrete. It is characterized by its unique composition, which includes fine powders and small steel fibers but lacks large aggregates commonly found in conventional concrete. RPC is designed to offer exceptional strength, durability, and low permeability. Its unique formulation and high-performance characteristics make it suitable for a wide range of applications in construction, where strength, durability, and reduced permeability are critical requirements. RPC is often used in projects where traditional concrete may not meet the desired performance standards.
AN OVERVIEW
Reactive Powder Concrete (RPC) is an ultra-high-strength and highly ductile cementitious composite boasting advanced mechanical and physical properties. It is a unique type of concrete where the microstructure is precisely tailored to achieve maximum density through the meticulous grading of all particles in the mix. RPC extensively harnesses the pozzolanic attributes of finely refined silica fumes and optimizes the chemistry of Portland cement to produce the strongest possible hydrates.
This novel material exhibits significantly enhanced strength and durability characteristics compared to both traditional concrete and even high-performance concrete. These improvements stem from the homogenization of the concrete, achieved by eliminating large aggregates, increasing the compactness of mixtures through the optimization of fine particle packing, and introducing fine steel fibers to enhance ductility.
COMPOSITION OF REACTIVE POWDER CONCRETE
RPC is composed of very fine powders (cement, sand, quartz powder and silica fume), steel fibres (optional) and super plasticizer. The super plasticizer used at its optimal dosage, decreases the water to cement ratio (w/c) while improving the workability of the concrete. A very dense matrix is achieved by optimising the granular packing of the dry fine powders. This compactness gives RPC ultra-high strength and durability. Reactive Powder Concretes have compressive strengths ranging from 200 MPa to 800 MPa.
PRINCIPLES FOR DEVELOPING RPC ARE AS FOLLOWS
- Enhancement of homogeneity by elimination of coarse aggregates.
- Enhancement of compacted density by optimization of the granular mixture.
- Enhancement of the microstructure by Post-set heat-treatment.
- Enhancement of ductility by addition of small-sized steel fibres.
- Application of pressure before and during setting to improve compaction.
- The optimal usage of super plasticizer to reduce w/c and improve workability.
Properties of RPC enhancing its homogeneity and strength
PROPERTY OF RPC | DESCRIPTION | RECOMMENDED VALUES | TYPES OF FAILURE ELIMINATED |
Reduction inaggregate size | Coarse aggregates are replaced by fine sand, with a reduction in the size of the coarsest aggregate by a factor of about 50. | Maximum size of fine sand is 600 µm | Mechanical, Chemical &Thermo-mechanical |
Enhanced mechanical properties | Improved mechanical properties of the paste by the addition of silica fume | Young’s modulus values in 50– 75 GPa range | Disturbance of the mechanical stress field. |
Reduction in aggregate to matrix ratio | Limitation of sand content | Volume of the paste is at least 20% greater than the voids index of non-compacted sand. | By any external source (e.g., formwork). |
Table describes the different ingredients of RPC and their selection parameters
The mixture design of RPC primarily involves the creation of a dense granular skeleton. Optimization of the granular mixture can be achieved either by the use of packing models or by particle size distribution software, such as LISA. For RPC mixture design an experimental method has been preferred. The major parameter that describes the quality of the mixture is its water demand (quality of water for minimum flow of concrete). In fact the voids index of the mixture is related to the sum of water demand and entrapped air.
Selection Parameters for RPC components
SL NO | COMPONENTS | SELECTION PARAMETERS | FUNCTION | PARTICLE SIZE | TYPES |
1 | Sand | Good hardnessReadily available and low cost. | Give strength, Aggregate | 150 µmto600 µm | Natural, Crushed |
2 | Cement | C3S : 60%; C2S : 22%;C3A : 3.8%;C4AF: 7.4%.(optimum) | Binding material,Production of primary hydrates | 1 µmto 100 µm | OPC, Medium fineness |
3 | Quartz Powder | Fineness | Max. reactivity during heat-treating | 5 µmto 25 µm | Crystalline |
4 | Silica fume | Very less quantity of impurities | Filling the voids, Enhance rheology, Production of secondary hydrates | 0.1 µ to 1 µm | Procured from Ferrosilicon industry (highly refined) |
5 | Steel fibers | Good aspect ratio | Improve ductility | L : 13 – 25 mm Ø : 0.15 – 0.2 mm | Straight |
6 | Super plasticizer | Less retarding characteristic | Reduce w/c | _ | Polyacrylate based |
After selecting a mixture design according to minimum water demand, optimum water content is analysed using the parameter relative density (d0/dS).Here d0 and dS represent the density of the concrete and the compacted density of the mixture (no water or air) respectively. Relative density indicates the level of packing of the concrete and its maximum value is one. For RPC, the mixture design should be such that the packing density is maximized.
Heat curing is performed by simply heating (normally at 90°C) the concrete at normal pressure after it has set properly. This considerably accelerates the pozzolanic reaction, while modifying the microstructure of the hydrates that have formed. Pre-setting pressurization has also been suggested as a means of achieving high strength.
The high strength of RPC makes it highly brittle. Steel fibres are generally added to RPC to enhance its ductility. Straight steel fibres used typically are about 13 mm long, with a diameter of 0.15 mm. The fibres are introduced into the mixture at a ratio of between 1.5 and 3% by volume. The cost-effective optimal dosage is equivalent to a ratio of 2% by volume.
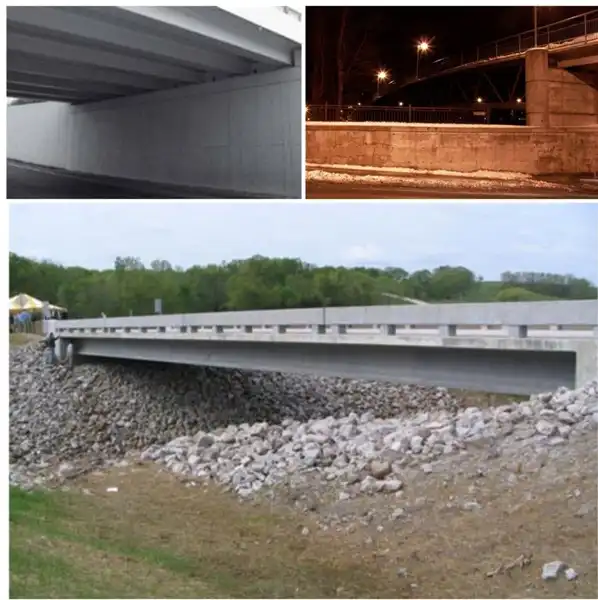
MECHANICAL PERFORMANCES AND DURABILITY OF RPC
The RPC family includes two types of concrete, designated RPC 200 and RPC 800, which offer interesting implicational possibilities in different areas. Mechanical properties for the two types of RPC are given in Table. The high flexural strength of RPC is due to the addition of steel fibres.
Table Comparison of RPC 200 and RPC 800
PROPERTIES | RPC 200 | RPC 800 |
Pre-setting pressurisation | None | 50 MPa |
Heat-treating | 20 to 90°C | 250 to 400°C |
Compressive strength (using quartz sand) | 170 to 230 MPa | 490 to 680 MPa |
Compressive strength (using steel aggregate) | — | 650 to 810 MPa |
Flexural strength | 30 to 60 MPa | 45 to 141 MPa |
Table shows typical mechanical properties of RPC compared to a conventional HPC of compressive strength 80 MPa. As fracture toughness, which is a measure of energy absorbed per unit volume of material to fracture, is higher for RPC, it exhibits high ductility. Apart from their exceptional mechanical properties, RPCs have an ultra-dense microstructure, giving advantageous waterproofing and durability characteristics. These materials can therefore be used for industrial and nuclear waste storage facilities.
Table – Durability of RPC Compared to HPC
Abrasive Wear | 2.5 times lower |
Water Absorption | 7 times lower |
Rate of Corrosion | 8 times lower |
Chloride ions diffusion | 2 times lower |
THE BENEFITS OF RPC
The benefits of Reactive Powder Concrete are as follows:-
- RPC is a better alternative to High Performance Concrete and has potential to structurally compete with steel.
- Its superior strength combined with higher shear capacity results in significant dead load reduction and limitless structural member shape.
- With its ductile tensile failure mechanism, RPC can be used to resist all but direct primarily tensile stresses. This eliminates the need for supplemental shear and other auxiliary reinforcing steel.
- RPC improves seismic performance by reducing inertia loads with lighter members, allowing larger deflections with reduced cross sections, and providing higher energy absorption.
- Its low and non-interconnected porosity diminishes mass transfer making penetration of liquid/gas or radioactive elements nearly non- existent. Cesium diffusion is non-existent and Tritium diffusion is 4.5 times lower than conventional containment materials.
LIMITATIONS OF RPC
In a typical RPC mixture design, the least costly components of conventional concrete are basically eliminated or replaced by more expensive elements.
- In terms of size scale, the fine sand used in RPC becomes equivalent to the coarse aggregate of conventional concrete.
- The Portland cement plays the role of the fine aggregate and the silica fume that of the cement.
- The mineral component optimization alone results (5 to 10 times higher than HPC).
- RPC should be used in areas where weight savings can be realized and where some of the remarkable characteristics of the material can be fully utilized.
- Owing to its high members where durability issues are at stake (for example, in marine condition), since RPC is in its infancy.
CONCLUSION
Reactive Powder Concrete (RPC) stands as a remarkable innovation in the field of construction materials. Its unique composition, which excludes coarse aggregates in favor of fine powders and steel fibers, grants it exceptional mechanical strength, durability, and reduced permeability compared to traditional High-Performance Concrete. RPC’s potential to replace steel in specific applications further underscores its significance in the construction industry.
The development of RPC relies on fundamental principles, resulting in a homogeneous mixture, excellent workability, thorough compaction, improved microstructure, and heightened ductility. Its ultra-dense microstructure provides invaluable waterproofing and durability properties, making it a compelling choice for various construction projects.
As the construction industry seeks innovative solutions that balance strength, sustainability, and longevity, RPC emerges as a compelling candidate. Its ability to optimize material use, enhance structural integrity, and promote economic efficiency positions RPC as a promising material for the construction of strong, durable, and long-lasting infrastructure. In the years to come, RPC is likely to play an increasingly pivotal role in shaping the future of construction practices and standards.
About Author
The author is the Managing Director at Skanda Group of Constructions. He is an experienced Civil Engineer with a demonstrated history of working in the construction industry.