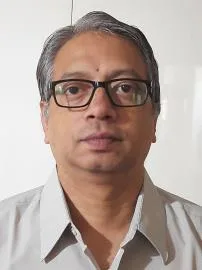
Speed of construction, consistency in quality for better finishes, cost of construction and standardization of construction processes are becoming essential requirements of construction projects in India. Precast technology can be one of the most suitable option on these parameters. Many construction companies / contractors aspire to adopt automated construction processes, which can reduce uncertainties of labour availability and speed up the construction process. Instead of spending huge time, money and labour in shuttering activities, people are finding out ways to cast precast elements at one centralized location under controlled condition and install it to different locations in the project.
Contracting companies will be required to change their present construction processes to get aligned to more automated construction techniques. Various technology options are now available in India. People have used formwork systems like Mivan/Durand Aluform systems, Tunnel formwork system, light gauge structural steel systems for reduction of time and labour at site.
Precast technology can be one of the most attractive options among these technologies mainly because of its inherent characteristics of durability of construction, speed of construction, flexibility to adopt for different design types, and cost competitiveness. Although conventional RCC + Brickwork + Plaster is the cheapest building skeleton system, it is a very labour intensive and time consuming method, which will get outdated, once speed and quality of construction will become prime requirements of construction projects.
Different precast technology options are now available in India like hollow core slabs, half slabs, rib slabs, notched solid slabs, double tee elements etc. for floor systems. Precast solid wall panels, sandwich wall panels, double walls, retaining walls, architectural cladding panels, columns etc. for vertical load carrying members. This paper will review these various precast technology options.
Introduction:
We have seen automation and mechanization of manufacturing processes in the automobile industry. For example, a car manufacturing unit has assembly line system, where different parts manufactured at different locations as per the engineering specifications and connection requirements are connected together in assembly line to form a car of required design specifications and finishes.
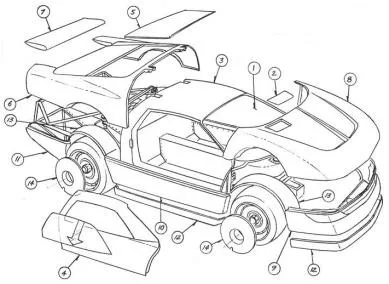
Similar concept is being used in automation of construction processes, where different elements are casted at factory location as per engineering specifications, under controlled conditions where we can achieve better speed and assured consistency in quality. These elements are then connected at site as per connection specifications.
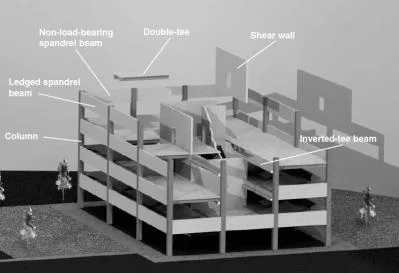
Production of precast elements in plant is very different from conventional Site cast reinforced concrete. The degree of precast process automation generally decides the precasting methodology. There are various methods of manufacturing of these precast elements depending on requirement of speed of production, cost of production, quality of production.
Precast structural skeleton systems:
Precast buildings can have three types of structural configurations depending on its gravity and lateral load resisting systems:
- Shear walled system: The lateral load resistance of these type of buildings is mainly offered by shear walls provided in the buildings.
- Moment resisting frame system: The lateral load resisting system in these type of buildings is mainly the moment frames with rigid column and beam joints which provides lateral stability to the building by column beam frame action.
- Hybrid system : This is a combination of above two systems, where the lateral loads are partly resisted by shear walls and partly by moment frames provided in the building skeleton.
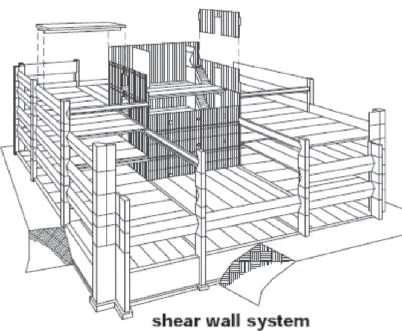
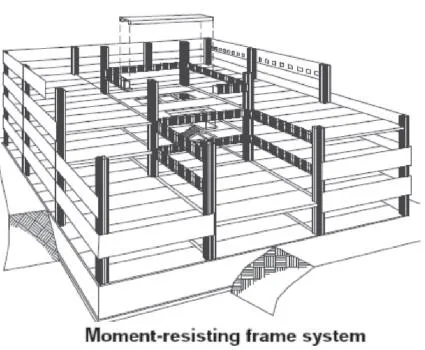
Precast structural skeleton systems
The precast floor system in all these configurations act like a horizontal diaphragm to transfer earthquake forces to different lateral load resisting elements.
Precast floor systems:
Various methods of precast Floor system construction are as follows:
Hollow core slabs with structural screed/topping: Hollowcore slabs are casted on long line prestressed bed with zero slump concrete using specially manufactured automatic hollow core slab casting machine. Some of the salient features of hollow core slabs floors are as listed below:
- Hollow core slabs being prestressed slab elements can be used efficiently for larger spans from 8 m to 12 m
- Manufactured in Factory with stringent quality controls on 100m to 200m long beds with fully automated machines
- Zero slump Concrete with higher strengths of M50, M60.
- High tensile Prestressing strands (fy) = 1860 N/mm2
- Hollow core slab section is designed to remain in the elastic limit. It behaves as an uncracked section as against a cracked section of conventional R.C. slab.
- Hollow core slabs are more durable as compared to conventional R.C. slabs because of higher concrete grade and uncracked section behavior.
- Concrete near Neutral Axis portion which does not contribute in Bending Moment resistance is removed to make the cross section structurally efficient with lesser weight and enhanced capability to span larger distances without support.
- Production of hollow core slabs is very fast. Around 1300 sq ft. of hollow core slab gets produced on one hollow core bed. Generally, a mid-sized precasting the unit has 4 to 8 nos. of hollow core casting beds.
- Erection of hollow core slabs is also very fast. Around 3000 sq ft. of hollow core slabs can be erected in one day by one erection team.
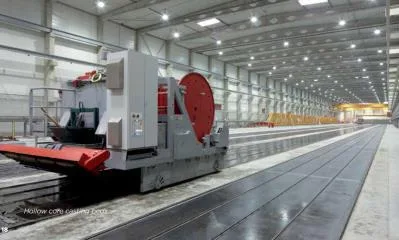
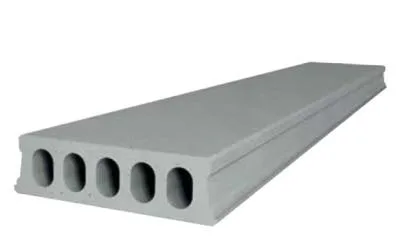
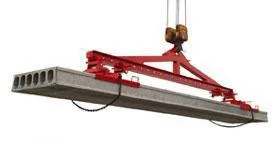
Hollow core slabs with structural screed/topping
Some of the photographs of projects in India where hollow core slabs are used as floor system are listed below:
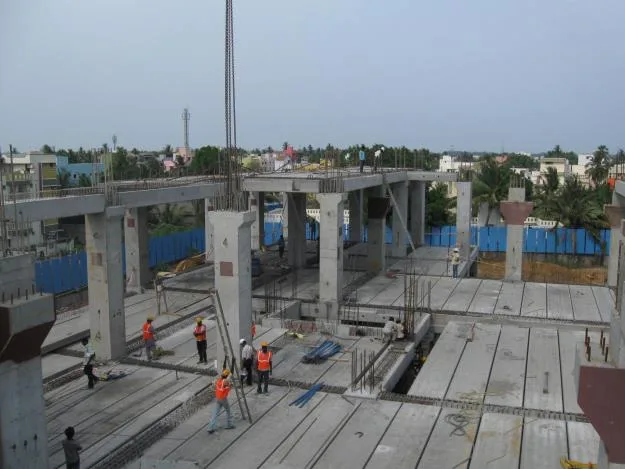
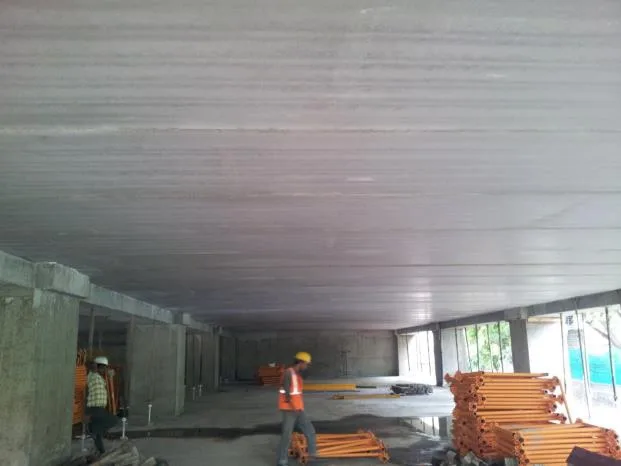
Double Tee elements with structural screed/topping: Hollowcore slabs are efficiently used for spans from 6m to 12m. In case where slab spans more than 12m to 18m in length are required then precast prestressed ‘Double Tee’ elements (DT elements) are the efficient solution. Some of the salient features of precast ‘Double Tee’ elements are as listed below:
- They are casted either on long line prestressing beds or self-stressing beds using wet concrete of grades M40, M50, M60.
- Sizes of DT elements can be from 2.5m wide x 14m long x 0.50m deep up to 3.5m wide x 18m long x 0.65m deep. Larger DT size is useful for faster erection of floor slabs.
- Section of DT element is structurally efficient section, as it eliminates the bottom flange of hollow core slab section which does not contribute to moment resisting capacity of a section for larger spans.
- Around eight DT elements (14m to 16m long and 3.0m to 3.5m wide) can be casted in a day from a 120m long DT casting bed. Thus around 4000 sft. Area of DT elements can be produced from one DT bed.
- One experienced erection team can erect around 12 to 14 large DT elements in a day’s work. This means around 6000 sft area slab can be installed in position in one day.
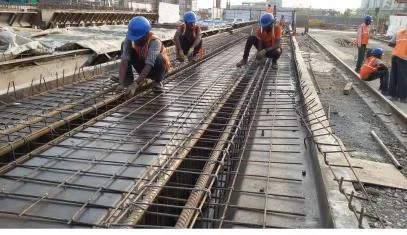
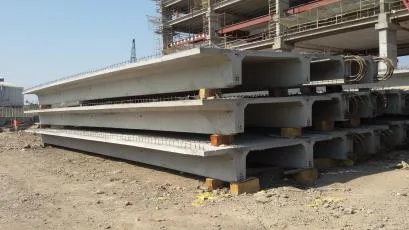
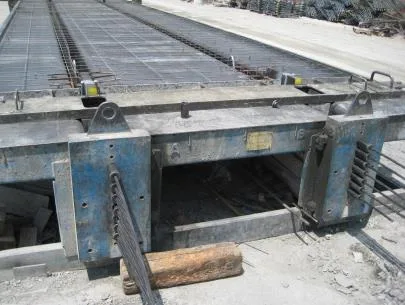
Double Tee elements with structural screed/topping
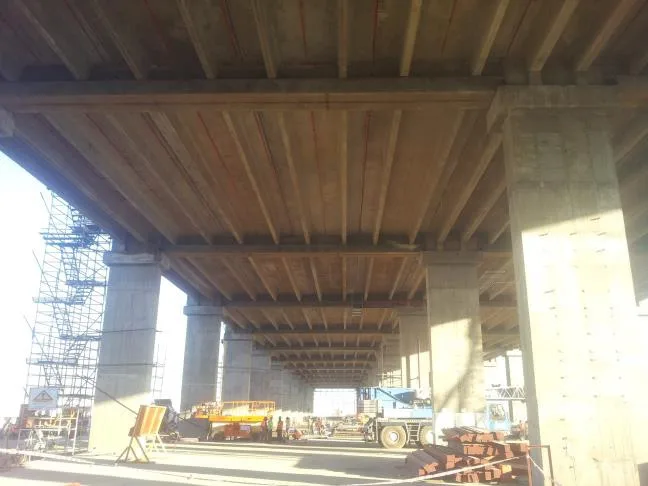
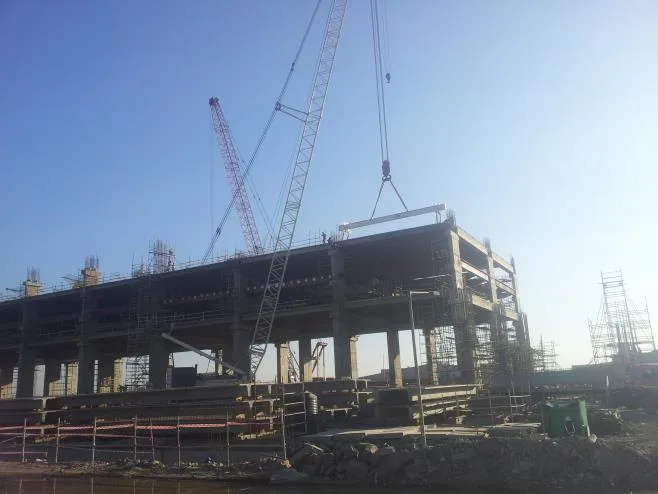
Photographs of a project in Pune where 3.5m wide x 15m long DT elements are used to complete a large six levels building having slab area of 16 Lac. sft. was completed in 10 months.
Precast wall panels and solid slab configuration:
In case of residential projects where the span of slabs are smaller say around 3m to 4m, then combination of precast load bearing wall panels and precast half slabs or notched solid slabs can be effective solution. Some of the salient features of precast ‘wall panels and precast slabs’ combination are as listed below:
- Precast wall panels are generally casted either on tilting tables or automated circulating system, where pallets on which walls are casted move at different stations in plant similar to assembly line process.
- Precast half slabs or notched solid slabs are casted either on stationary tables or automated circulating system, where pallets on which slabs are casted move at different stations in plant similar to assembly line process.
- Concrete grades used for precast wall panels and slabs are M30, M40 depending upon finish and stripping time requirements.
- Most of the walls act as load bearing wall panels and shear walls. Hence, vertical load carrying members like columns can be eliminated in the superstructure.
- All the MEP services that get concealed inside wall panels need to planned well in advance and their connections with services concealed in slab panels and upper floor level wall panels need to worked out before casting of wall panels in the factory.
- Precast load bearing wall panels cannot be removed once the building is constructed, hence partition walls or non-load bearing wall panels need to be identified in the planning stage so that even if they are removed at later stage the structural load path does not change.
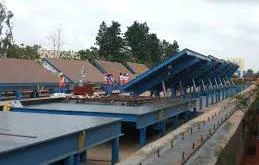
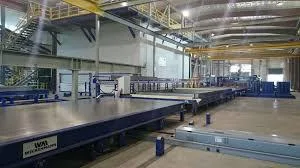
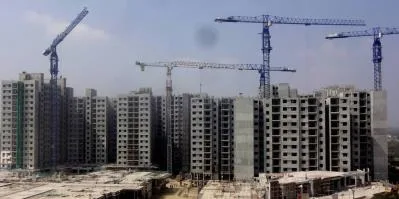
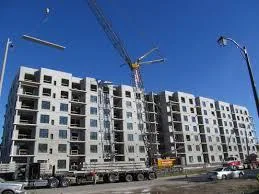
Precast wall panels and solid slab configuration
Precast Column & Beam configuration:
In case of Commercial projects where the usage pattern varies at different levels and larger spans are required, precast columns and precast beams with hollow core slabs can be an efficient structural system. Some of the salient features of precast ‘precast column and beam’ configuration are as listed below:
- Lower level precast column to upper level precast column connections are very critical to execute. Special connection for these moment connection locations need to be used for ductile behaviour of these connections.
- Precast columns can have corbels to rest precast beams during the construction phase. If column corbels are eliminated, then precast beams need to be temporarily supported for construction stage loads, till the time beam to column connections achieve desired strength.
- As shear walls are reduced or practically eliminated in this type of arrangement, the building structure gets more open spaces for better functional planning.
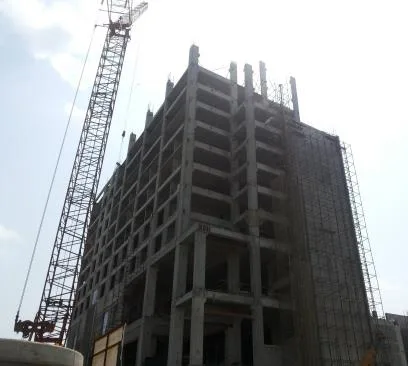
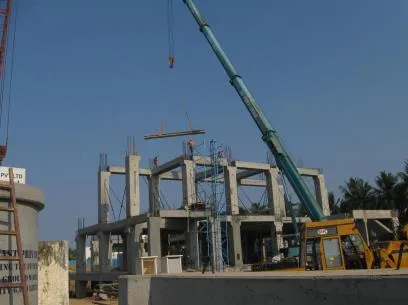
Precast Column & Beam configuration
The choice of appropriate precast structural system needs to be done by evaluating above mentioned aspects along with the aesthetical and functional requirements.
Conclusions:
- Every precasting method has a set of advantages and limitations associated with it. While selecting any precast structural system, the effect/requirement of cost, speed and quality needs to be evaluated for adopting that method.
- For longer spans from 6m to 12m, precast prestressed ‘Hollow core slabs’ is the efficient solution.
- For extra larger spans from 12m to 18m, precast prestressed ‘Double Tee elements’ are effective.
- For residential projects of smaller spans 3m to 4m, structural system of precast wall panels and precast solid slabs is suitable.
- For commercials and I.T. park projects, having requirements of open spaces and varied usage pattern, precast columns and precast beams structural configuration is efficient.
- Techno-commercial feasibility of suitable precasting methodology needs to be evaluated based on these parameters.
References:
- PCI-MNL-120, PCI Design Handbook, Precast and Prestressed Concrete, 7th Edition.
- PCI-MNL-116, Manual for Quality Control for Plants and Production of Structural Precast Concrete
About the Author
Mr. Dhananjay S. Bhosale completed his M.E. (Structures) in 1993 and M.E. (Construction & Management) in 1995. Since then, he has been actively engaged in the field of Structural Engineering. He has contributed to numerous prestigious National and International projects, adhering to IS, ACI, and BS codes. His expertise lies in designing both Precast and RC/PT structures, encompassing High-rise, Mid-rise, and Low-rise Residential, Commercial, and Industrial buildings. Additionally, he has presented technical papers at several national and international conferences.