Post-tensioning is a prestressing method to reinforce concrete using strong steel tendons or cables placed strategically within the concrete, typically within protective ducts or sheaths. These tendons are then tightened, applying significant force.The method is executed once the concrete has completely cured and offers several advantages, such as creating concrete structural spans, reducing concrete thickness, and improving structural performance. It’s commonly used in various construction projects like bridges, buildings, and parking structures.
The post-tensioning process involves several stages:
- Casting of Concrete: The process begins by pouring concrete and shaping concrete structural components such beams, slabs, etc. based on project requirements.
- Placement of Tendons: Before the concrete sets, ducts or tubes are strategically placed within the mold or formwork to serve as channels for the tendons that will be tensioned later.
- Placement of Anchorage Block and Jack: Anchorage blocks and hydraulic jacks are positioned at the ends of the tendons. The anchorage block securely grips the tendon, while the jack applies tension.
- Applying Tension to the Tendons: Hydraulic jacks apply significant force to the tendons, creating compressive stress within the concrete, enhancing its strength and resilience.
- Seating of the Wedges: Wedges are used to maintain tension in the tendons, ensuring that the applied force is retained, which stabilizes the structure.
- Cutting of the Tendons: After reaching the desired tension level and verifying it, the tendons are cut and secured, maintaining the prestress within the structure.
Throughout these stages, various components, equipments and devices are used to ensure the successful execution of post-tensioning, ensuring the concrete becomes a robust and reliable part of the construction.
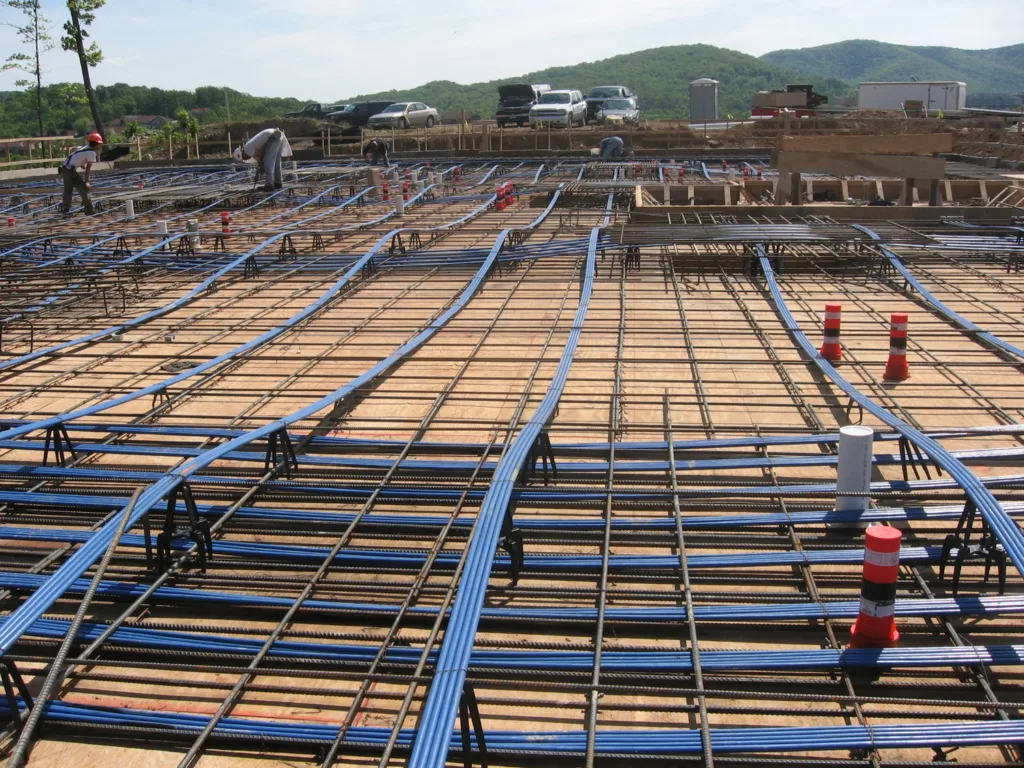
Different Components Used in Post-Tensioning:
1. Casting Bed:
The casting bed serves as the foundation for the entire post-tensioning process. It provides a flat, robust surface upon which the concrete structure is constructed. Ensuring the casting bed’s level and proper preparation is crucial to maintain the concrete’s uniformity and integrity. Casting beds can range from simple flat surfaces for small projects to specialized forms for complex structures, such as precast segments for bridges or multi-level building components.
2. Mould/Shuttering:
Moulds or shuttering structures are employed to shape and mold the concrete into the desired form. These forms are essential for creating the intended shape of the structure, such as beams, slabs, or bridges. Moulds are meticulously designed to accommodate post-tensioning ducts and tendons, ensuring their correct placement within the concrete. Moulds can be constructed from various materials, including timber, plywood, steel, or prefabricated forms, depending on factors like project size, budget, and the desired concrete finish.
3. Ducts:
Ducts are integral components of post-tensioning systems. They are essentially tubes or channels made of materials like high-density polyethylene (HDPE) or galvanized steel, designed to house the restressing tendons. Ducts protect the tendons from environmental factors and provide a path for tensioning and grouting processes.
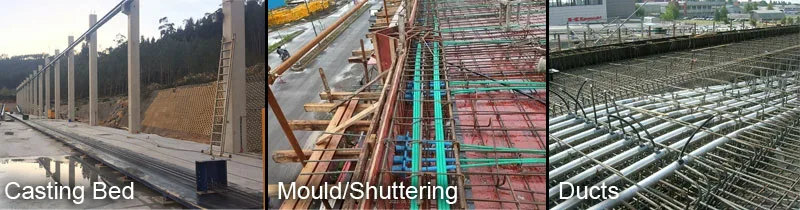
Devices and Equipments Used in Post-Tensioning:
Anchoring Devices:
Anchoring devices are responsible for transferring the prestressing force from the tendons to the surrounding concrete. These devices are securely embedded within the concrete and ensure that the tensioned tendons effectively reinforce the structure. These devices operate on different principles to secure the tendons effectively. Here, we discuss three key principles of anchoring tendons:
1. Wedge Action
An anchoring device based on wedge action comprises an anchorage block and wedges. The strands are secured by the frictional grip of the wedges within the anchorage block. Some examples of systems utilizing wedge action include Freyssinet, Gifford-Udall, Anderson, and Magnel-Blaton anchorages.
1.1. Direct Bearing
In this principle, rivet or bolt heads, or button heads formed at the end of the wires, directly bear against a block. The B.B.R.V post-tensioning system and the Prescon system are examples of systems based on this principle.
1.2. Looping the Wires
The Baur-Leonhardt system, Leoba system, and the Dwidag single-bar anchorage system operate on the principle of looping the wires around the concrete. The wires are looped to form a bulb shape.
There are several types of anchoring devices used in post-tensioning systems, each designed for specific applications. Here are some common types:
1. Wedge-Type Anchors: These are the most commonly used anchoring devices in post-tensioning. They consist of a wedge and a bearing plate. As the tendon is tensioned, the wedge is driven into the anchor body, clamping the tendon and creating frictional resistance that locks the tendon in place.
2. Grip-End Anchors: Grip-end anchors are similar to wedge-type anchors but use a different mechanism to secure the tendon. They have serrated gripping elements that hold the tendon firmly when tension is applied.
3. Plate Anchors: Plate anchors utilize a flat plate or multiple plates to anchor the tendon. The plates grip the tendon, and tension is maintained by the friction between the plates and the tendon.
4. Button-Head Anchors: These anchors have a button-like component that clamps onto the tendon when tensioned. They are often used in smaller-scale post-tensioning applications.
5. Multi-Strand Anchors: Multi-strand anchors are designed to secure multiple strands or cables simultaneously. They feature multiple wedges or gripping elements to hold each strand securely.
6. Barrel and Wedge Anchors: In this design, a barrel and wedge system is used to secure the tendon. The tendon is inserted into the barrel, and the wedge is driven into the barrel to create tension and lock the tendon in place.
7. Live Anchors: Live anchors are adjustable anchoring devices that allow for post-tensioning adjustments. They are used when precise tension control is required or when tensioning might need to be adjusted over time.
Jacks:
Hydraulic jacks are used for tensioning the tendons to impart the required compressive stress to the concrete. The hydraulic force applied by jacks allows for precise control over the prestressing force, ensuring the structural integrity of the concrete members. There are several types of hydraulic jack devices used for post-tensioning, each designed for specific purposes and applications. Here are some common types:
1. Single-Acting Hydraulic Jacks: These jacks operate using hydraulic pressure to extend a single piston. They are commonly used for post-tensioning applications where only tensioning (extension) of the tendon is required. They are simpler in design and operation.
2. Double-Acting Hydraulic Jacks: Double-acting jacks are more versatile as they can both extend and retract the piston. This feature allows for greater control over the tensioning process, making them suitable for applications where precise adjustments are needed.
3. Multi-Strand Jacks: Multi-strand jacks are designed to simultaneously tension multiple strands or cables. They are equipped with multiple hydraulic lines and gripping mechanisms to apply uniform force to all the strands in one operation. These jacks are efficient for multi-strand post-tensioning systems.
4. Specialized Post-Tensioning Jacks: In some cases, specialized jacks are designed for specific post-tensioning applications, such as those requiring unique shapes or configurations to accommodate the project’s needs.
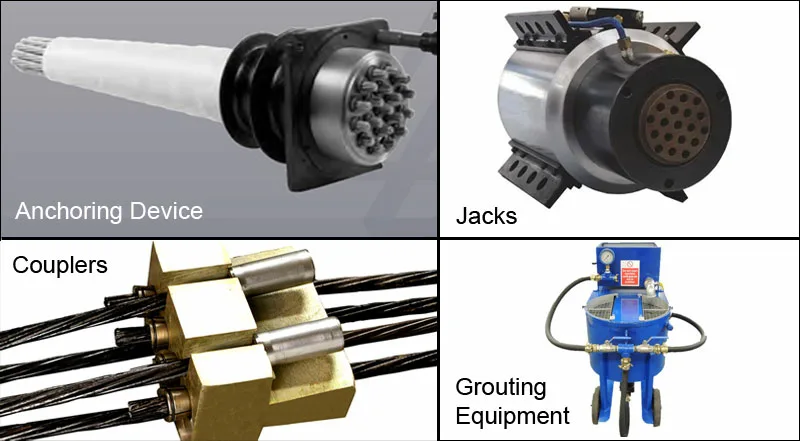
Couplers (optional):
Couplers are optional devices used at junctions or splice points in the post-tensioning system. They provide a secure and efficient means of connecting two tendons, ensuring the continuity of the prestressing force throughout the structure. While not always necessary, couplers can be beneficial in specific design scenarios.There are several types of coupler devices used for post-tensioning in construction:
1. Grout Filled Couplers: These are the most common type of couplers. They consist of a cylindrical steel sleeve that joins two post-tensioning tendons together. Grout is pumped into the sleeve to bond the tendons and transfer the tension forces.
2. Wedge Couplers: These couplers use a wedge mechanism to grip and hold the tendons together. As the wedge is tightened, it creates a strong connection between the tendons.
3. Threaded Couplers: Threaded couplers have threads on the inside of a steel sleeve, allowing the tendons to be screwed into place. This provides a secure connection and is often used for repair work.
4. Compression Couplers: Compression couplers use compression forces to connect tendons. They work by compressing the tendons against a conical or tapered surface within the coupler.
5. Shear Plate Couplers: These couplers have a plate that applies shear forces to the tendons. They are designed for use in applications where a high load capacity is required.
6. Anchor Plate Couplers: Anchor plate couplers incorporate an anchor plate and a series of wedges to secure the tendons. This type of coupler is particularly useful when dealing with larger tendons.
7. Bonded Couplers: In bonded couplers, the tendons are bonded together using epoxy resin or another adhesive material. This type of coupler is used when a high level of corrosion protection is required.
Grouting Equipment:
Grouting equipments though optional, plays a crucial role in post-tensioning systems. Grout is a specialized cementitious material injected into the ducts housing the tendons. It serves multiple purposes, including filling voids, protecting the tendons from corrosion, and improving load transfer. Proper grouting is essential for the long-term performance and durability of post-tensioned structures.. Here are some common grouting devices used in post-tensioning:
1. Grout Pump: A grout pump is a machine used to mix and pump grout into the tendon ducts. It typically consists of a hopper for mixing the grout, a pump to pressurize it, and hoses to deliver the grout to the injection points.
2. Injection Nozzles: Injection nozzles are placed at the ends of tendon ducts and serve as entry points for the grout. They are designed to create a seal around the duct to prevent grout from leaking out and ensure it flows into the duct properly.
3. Pressure Gauges: Pressure gauges are used to monitor the pressure applied during grout injection. Maintaining the correct pressure is essential for ensuring that the grout fully fills the duct and bonds with the tendon.
4. Mixing Equipment: Properly mixed grout is essential for its effectiveness. Mixing equipment includes mixers and agitators to prepare a consistent grout mixture.
5. Grout Hose: Grout hoses are used to transport the grout from the pump to the injection points. They are designed to handle the high pressure of the grout and are typically made of durable materials.
Conclusion
In this article we have analysed different components, equipments and devices using the post tensioning method. In an upcoming article we will focus on the pretensioning method.