Perforated metal mesh is a precisely engineered sheet with evenly spaced holes or openings, created using punching , laser cutting etc. Made from materials like steel, aluminum, and stainless steel, it is available in various thicknesses and perforation patterns to meet specific requirements. The size, shape, and arrangement of the perforations influence its strength, weight, and ability to manage airflow, light, and sound. Designed for durability and consistency, it maintains structural integrity while serving a wide range of construction industrial and infrastructure needs.
Applications of Perforated metal mesh
- Construction – Used for facades, ceilings, sunshades, stair treads, and ventilation grilles.
- Industrial – Applied in filtration systems, machinery enclosures, soundproofing panels, and HVAC components.
- Infrastructure – Utilized for bridge decking, drainage covers, fencing, and reinforcement in concrete structures.
Perforated metal mesh manufacturing methods
Perforated metal mesh is manufactured using precision techniques to create evenly spaced holes or patterns in metal sheets. The key manufacturing methods include:
- Punching – A mechanical or CNC-controlled press uses a die to punch holes in the metal sheet, creating uniform perforations.
- Laser Cutting – A high-powered laser precisely cuts the perforations, allowing for intricate designs and minimal material wastage.
- Etching – A chemical process selectively removes material to create fine perforations, commonly used for delicate or thin metal sheets.
- Water Jet Cutting – A high-pressure stream of water with abrasive particles cuts through metal, producing clean edges without heat distortion.
- Rotary Pin Perforation – A rolling pin with sharp needles or punches continuously perforates the metal sheet, often used for large-scale production.
Each method is chosen based on material type, perforation design, precision requirements, and production volume.
Perforated metal mesh advantages
- Provides high structural integrity while remaining lightweight.
- Materials like stainless steel and galvanized steel withstand harsh environments.
- Allows controlled air circulation, reducing heat buildup in enclosed spaces.
- Regulates natural light while maintaining visibility and privacy.
- Helps in noise control when used in acoustic panels and enclosures.
- Reduces cooling and lighting costs in buildings by optimizing airflow and light diffusion.
- Can be cut, shaped, and installed with minimal effort.
- Resistant to wear, requiring minimal upkeep over time.
- Often made from recyclable materials, supporting sustainability in construction.
- Acts as a barrier for safety applications without obstructing visibility.
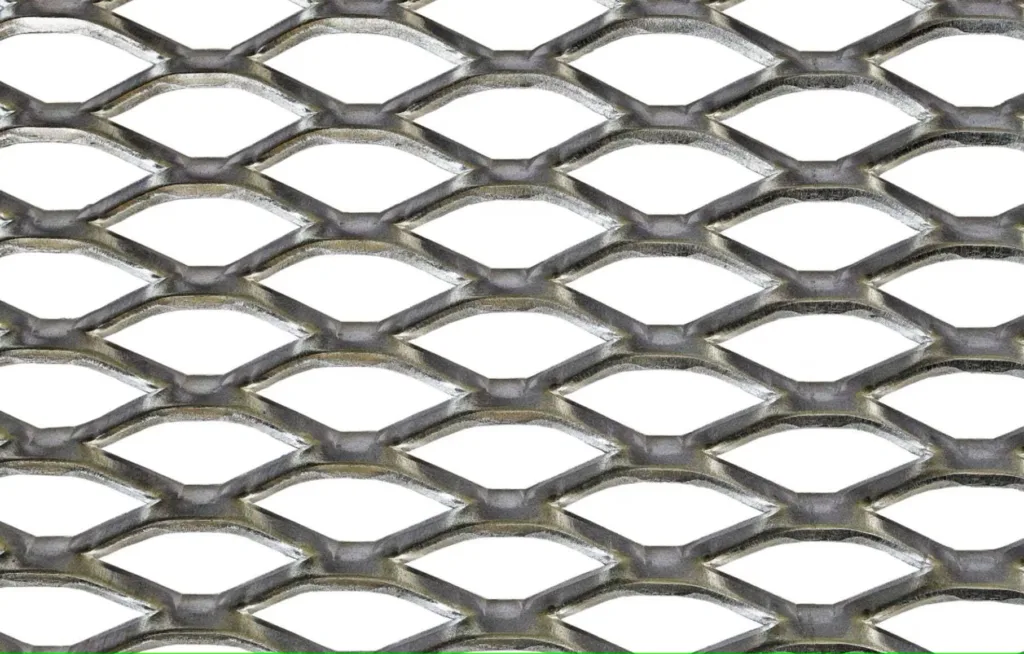
Types of Perforated metal mesh
Round Hole Perforated Mesh
Round hole perforated mesh is the most widely used type, known for its uniform strength, balanced open area, and efficient airflow. It is manufactured by punching evenly spaced circular holes into metal sheets, making it suitable for various applications, including ventilation, filtration, and protective barriers. Its versatility and structural stability make it a preferred choice in construction, industrial enclosures, and HVAC systems.
Square Hole Perforated Mesh
Square hole perforated mesh features a grid-like pattern that provides a modern appearance while maintaining a high open-area percentage. The square perforations allow for efficient airflow and visibility while offering enhanced strength compared to round hole designs. This type is commonly used in architectural applications, security screens, and industrial sieve.
Slotted Hole Perforated Mesh
Slotted hole perforated mesh consists of elongated openings that enhance ventilation, fluid drainage, and material separation. The shape and orientation of the slots can be customized to direct airflow or drainage in specific directions, making it ideal for HVAC systems, machinery enclosures, and industrial processes that require efficient filtration and airflow control.
Hexagonal Hole Perforated Mesh
Hexagonal hole perforated mesh is designed to maximize open space while maintaining high structural integrity. The honeycomb-like pattern allows for superior ventilation, reduced weight, and enhanced strength, making it suitable for applications such as speaker grilles, lighting fixtures, and lightweight structural components. Its unique design offers both functional and visual advantages, especially in architectural and industrial facilities.
Decorative Perforated Mesh
Decorative perforated mesh is customized with intricate patterns to enhance the visual appeal of facades, partitions, and interior designs. This type is commonly used in commercial and residential buildings to create visually striking elements while still allowing for light diffusion, airflow, and partial visibility.
Embossed Perforated Mesh
Embossed perforated mesh includes raised patterns that add texture and rigidity to the metal sheet. This design improves slip resistance, making it a preferred choice for anti-slip flooring, stair treads, and industrial work platforms. The embossed patterns also enhance strength and durability, allowing it to withstand heavy loads and harsh conditions.
Micro Perforated Mesh
Micro perforated mesh features extremely small holes, typically used in fine filtration, acoustic control, and precision industrial applications. The small perforations effectively diffuse sound, making it ideal for noise-reducing panels and speaker covers.
Heavy Gauge Perforated Mesh
Heavy gauge perforated mesh is manufactured from thick metal sheets to provide maximum strength and durability. Designed to withstand high-impact forces, it is used in security enclosures, bridge decking, reinforced structures, and other applications requiring robust load-bearing capacity.
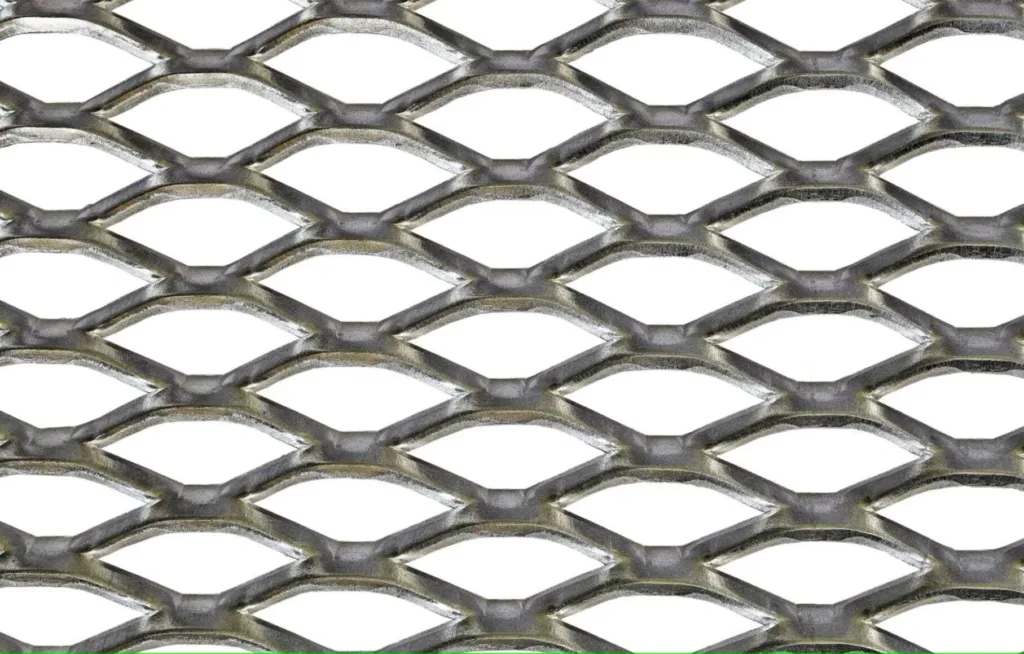
Key Factors for Selecting the Right Type of Perforated Metal Mesh
- Material Type – Strength, corrosion resistance, and environment.
- Hole Shape & Size – Affects airflow, filtration, and strength.
- Open Area – Determines ventilation, weight, and visibility.
- Sheet Thickness – Impacts durability and load capacity.
- Manufacturing Method – Punching, laser cutting, or etching.
- Environmental Exposure – Moisture, chemicals, and temperature resistance.
- Aesthetic Needs – Custom patterns for design applications.
- Installation & Maintenance – Ease of handling and upkeep.
- Cost Efficiency – Balances performance and budget.
Conclusion
Perforated metal mesh offers strength, durability, and versatility, making it essential for diverse applications. Selecting the right perforation type ensures efficiency, durability, and sustainability, reinforcing its importance in modern infrastructure and sustainable construction.