The rising demand for housing and improvement in techniques is increasing in acceptance. There is a faster and sustainable approach towards the construction of buildings in order to meet the ever-increasing demands of the construction industry. In regard to this, a recent case has come into focus wherein a 10-storey building in Changsha, China was constructed in a day. The China-based manufacturing enterprise Broad Group managed to construct a 10-storey steel apartment building in just over a day.
Yes, 28 hours and 45 minutes to be precise. So, how did they manage to pull it off?
It is the use of prefabricated construction systems, wherein the building is constructed by means of assembling small self-contained modular units that were built in advance in a factory. Designed to be easy to transport and install, Broad Group’s “Living Building” system used components that are able to fit into a standard shipping container, and then be bolted together and made into a fully constructed building. Finally, power and water connections were added.
Modular Prefab construction is not entirely new to the Indian construction space too. Office and commercial buildings have been using prefab wall panels, ceiling panels, plasterboards and flooring systems to create interiors of offices and other places. Though this construction practice has been in use for over eight decades, it is getting its due in recent years due to increasing demand for mass housing and faster construction.

What is modular prefab construction?
It is the practice of assembling components of a structure in a factory or other manufacturing site as modules and transporting complete or sub-assemblies to the construction site where the structure is to be located. Modular prefab units include doors, wall panels, floor panels, stairs, window, walls, roof trusses, room-sized components, and entire buildings. The different modular prefab sections are produced in huge quantities and then shipped to various construction sites. The precast concrete units are hardened and cast before it is used in the construction. However, sometimes, builders cast components at the construction site and hoist them into the actual location after they hardened..
Apart from moving a large proportion of the work from a messy, exposed open-air setting with limited working hours into a safe, controlled indoor factory setting with 24/7 production uptime potential. Construction waste and emissions can be halved, by production efficiencies and increased recycling. Modular prefab construction also offers equally important benefits such as sustainability, water conservation, carbon footprint, reduction in traffic congestion around the site and better green building support.
Advantages of modular prefab construction
Whether using modular prefab for just a section of a new project or the vast majority, the benefits are undeniable. Its advantages are;
- Moving partial assemblies from a factory often costs less than moving pre-production materials to each site
- Prefabricated components are made in a controlled manufacturing environment and follow specified standards, the sub-assemblies of the structure will be built to a uniform quality.
- Prefabricated assemblies can save costs by reducing on-site work
- The consistent indoor environments of factories eliminate most impacts of weather on production
- Factory tools such as jigs, cranes, conveyors, etc. can make production faster and more precise
- Offsite production of assemblies results in reduced pollution and disturbance of job sites. This protects nearby wetlands or protected areas and minimizes disruption of local flora and fauna.
- Cranes and reusable factory supports can allow shapes and sequences without expensive on-site falsework
- Higher-precision factory tools can aid the more controlled movement of building heat and air, for lower energy consumption and healthier buildings
- Factory production can facilitate more optimal materials usage, recycling, noise capture, dust capture, etc.
- By reducing the timeframe of a construction site, you concurrently reduce the amount of time that site is vulnerable to vandalism or theft
- Machine-mediated parts movement and freedom from wind and rain can improve construction safety
- This benefit stems from the process’s efficient raw material utilization and reusability.
Other than these advantages, the developments and standardization of construction and manufacturing methods, coupled with the growing need for housing and office spaces, modular prefab buildings are being innovated continuously in place of conventional construction. The emergence of modeling tools and processes such as BIM (Building Information Modeling) are helping architects, engineers, and contractors by digitally representing the characteristics of the structure.
Different types modules of modular prefab systems
Modular prefab systems consist of different types of modules that are three-dimensional in construction usually made up of four shop-assembled panels. Several modules are placed adjacent or on top of each other which forms the whole building. Modules are connected by inter-module connections which are bolted on-site. There are different types of modular prefab according to their form of construction.
Four-sided Modules: This type of module is manufactured with four closed sides creating a cellular space. The panel frames are load-bearing which can transfer both vertical and lateral loads.
Partially Open-sided Modules: This module consists of one or more walls made up of an assembly of panels that do not completely span the entirety of the wall. The partitions are open which can serve as accessways or corridors that connect adjacent modules.
Open-sided Modules: This module consists of one or two sides that are designed to be fully open. The long sides are usually removed so that by attaching to other adjacent open-sided modules a larger space is created.
Modules Supported by Primary Structure: In this type of module, an external steel structural frame is added to support and transfer loads. The external structure can provide open spaces at or below ground levels while the modules are stacked above.
The modules help to fabricate components such as windows, doors, and trusses as per project demand. You can use them for Hybrid Prefab Buildings that utilize both three- and two- dimensional components from modular and panel systems to create a whole or a part of a building or a Complete Building which are delivered and installed at the site with prepared foundations.
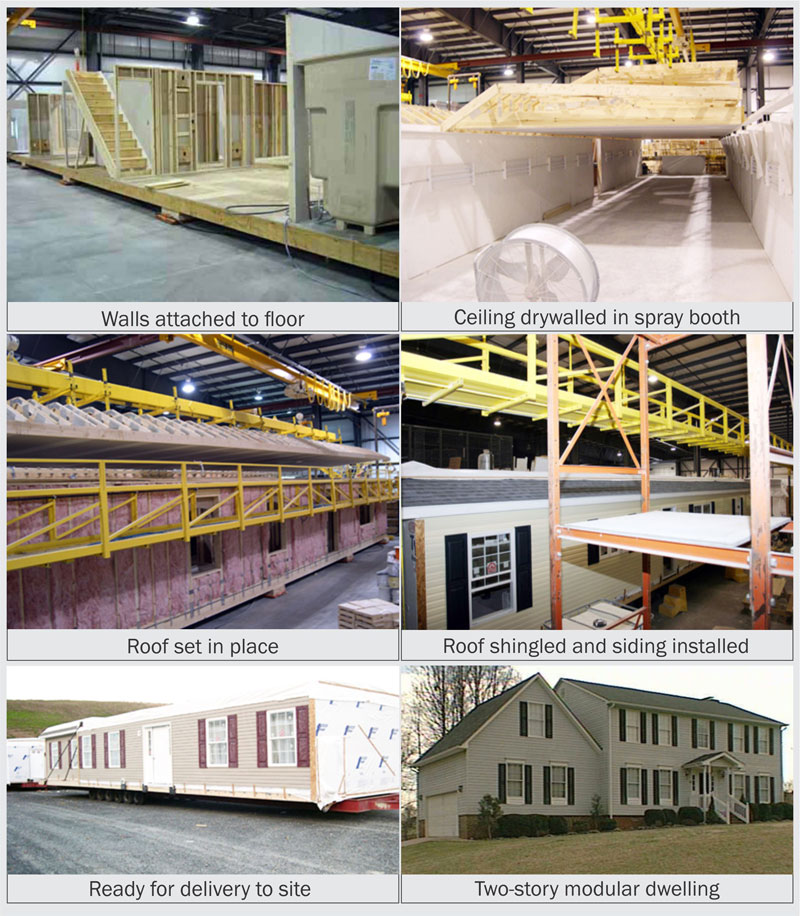
Applications of modular prefab components
- The most widely used form of prefabrication in buildings where a particular part or form is repeated many times.
- In the construction of apartment blocks, and housing developments with repeated housing units.
- Modular Radio bows for mobile phones and other services often consist of multiple prefabricated sections.
- It is also being used for rental apartments, office spaces, evacuation centers, schools, apartment blocks, and single-detached houses etc.
Modular Prefab Construction in India
Globally, modular prefab has already seen significant adoption by the construction sector – Burj Khalifa in Dubai and the Sydney Opera House being two of the finest examples. The Indian construction marketplace is a bit slow in acceptance of newer construction methods because the sector continues to be labour intensive and heavily reliant on traditional construction practices. In this regard modular prefab has given developers the benefit of time, safety and quality, enabling them to produce buildings faster and capture the demand of the customers.
The concept of modular prefab is gaining prominence in the Indian construction market. The entry of prefabricated homes in India has paved the way to innovative and technologically advanced construction and design methods for all kinds of construction, such as high rises, low rises, villas, and mass townships. It is no longer restricted to the creation of cabins at project sites. There is a big opportunity for modular prefab companies in India and with the continued popularity of prefabricated construction.
There are different government provisions that are set to see the modular prefab industry rapidly that includes;
- Real Estate Investment Trust (REIT) to help investors come forward to invest in the Indian real estate market, thus creating an opportunity worth USD 19.65 billion in the Indian market over the coming years
- GHTC- I, Global Housing Technology Challenge, the government plans to bring the latest technologies in the construction sector
- Smart-Cities mission, the nation aims to create sustainable world-class cities and has allocated a budget of USD 29.2 billion.
- HRIDAY, a scheme to develop the heritage cities, an amount of USD 16.5 million has been approved by the central government.
- Other initiatives and plans by the government include AMRUT and PMAY (Pradhan Mantri Awas Yojana, a national housing scheme).
However, it is not void of challenges, factors such as Mass Production / Limited Variety, Front Loaded Design, Transportation Costs & Risk, lack of proper financing options for the prefabricated living spaces, skilled labor demands for assembly etc. are a few of the constraints.
Conclusion
There are multiple advantages and applications of prefabrication construction as discussed above. There is a trend in the increased usage of modular prefab components in the construction sector owing to the cost benefits and time constraints. Rapid urbanization and the need to overcome the shortage in housing, are providing a market scope for modular prefab structures in India.