Fiber reinforced polymer is a composite material that consists of thermosetting resins and fiberglass. The resin brings environmental and chemical resistance to the product and is the binder for the glass fiber in the structural laminate. FRP is poised as one of the preferred modern-day materials owing to its superiority in terms of its adjustable characteristics such as high strength-to-weight ratio, commendable thermo-mechanical, corrosion-resistant properties and customization capabilities.
Advantages of Fiber reinforced polymers
- Lightweight and helps in cutting expenses on labour and installation
- Increases construction speed that further reduces environmental impacts.
- Have high strength as compared to traditional materials.
- FRP has great potential in further maximising the longevity of existing as well as new structures
- Resistant to corrosion and rot
- FRP-based products hardly require an energy-intensive replacement or much maintenance
- FRP can be recycled
- Due to the various options in resins and topcoats, FRP can be adapted for any environment, application, or hazard
- Offer more shape options and thickness specifications available for uniformity and tight control
- Can even be painted in the mold with a special gel that makes paint chipping, cracking, or flaking non-existent.
Types of Fiber reinforced polymer
CFRP
Carbon fiber is anisotropic material in nature, manufactured at 1300 C. The major advantages of this fiber include low density, low conductivity, high fatigue strength, high elastic modulus, good creep level, resistance to chemical effects and does not absorb water as well.
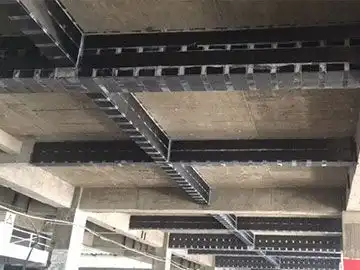
GFRP
Glass fiber is isotropic and resistant to water and chemicals at a low cost are the main characteristics of glass fiber. Relatively low costs compared with other types of FRPs make glass fiber the most generally applied in the construction industry.
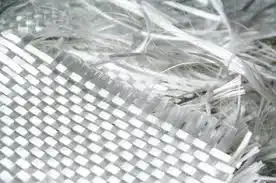
AFRP
Aramid fiber is anisotropic in nature and normally yellow in color. It has sufficient tension for applications such as tendons and cables, however, it holds low compressive strength. and also have low density.
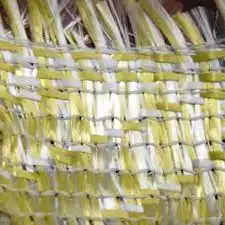
FRP Resins
The type of resin varies from one type of FRP to another, these include:
- Polyester
- Polyurethane
- Epoxy
- Vinyl Ester
Manufacturing of Fiber reinforced polymer products
Forming Process
Bonding the fiber and the polymer plastic is the second and most critical part of FRP manufacture. It can be achieved through several processes, including
- Pultrusion. This manufacturing method is used to create components with long and consistent shapes, such as bars, beams, and rods. It involves saturating the reinforcements fibers with resin by pulling them through a resin bath and then pulling the saturated fibers through a heated steel die.
- Vacuum infusion. This manufacturing method utilizes atmospheric pressure to compact the dry fibers into layers and drive the resin into them.
- Filament winding. This manufacturing method is used to create parts and products that can withstand high operating pressures. Continuous strands of fiber reinforcement are first saturated with resin and then applied to a rotating cylindrical mold.
- Hand lamination. This manufacturing method is commonly used for prototype and low-production quantities due to its low tooling costs. The reinforcement fibers are first placed into an open mold, and then resin is poured into the mold over the fibers.
Curing
Wet reinforcement are pulled out and the thermosetting process begins for curing and hardening.
Cutting the Parts
The last step of the process involves cutting the parts while the line is in motion. This is accomplished by using a traveling cut-off saw, which moves in the same speed and direction as the part being cut.
Different part sizes have unique requisite settings that must be entered before the processing begins.
Fiber reinforced polymer products
FRP offers a wide range of unique benefits — short production and installation time, lightweight, long-term cost savings, corrosion resistance, and superior longevity. Ideal material for use in construction and infrastructure projects including, pedestrian, and trail bridges, cantilever sidewalks, rail platforms, waterfront frameworks, storage tanks and pipes, stairs and handrails, and much more.
- FRP Portable Western Toilet
- FRP Portable Security Cabin
- FRP Water Storage Tanks
- FRP Gratings
- FRP Drainage Cover
- FRP Plant Settlers
- FRP Aquifers
- FRP Garden Recliners
- Fiberglass Mesh
- Fiberglass Panel
- FRP Corrugated Sheets
- FRP Translucent Panel
- FRP Sheets
- FRP Industrial Gutters
- FRP Cladding
Conclusion
Owing to the growing applications in the construction sector, the demand for fiber-reinforced polymer (FRP) composites is expected to increase. FRP materials are one of the strongest commercial materials available. FRP’s toughness allows thin sections to be used; stiffness can be acquired by using structural core materials.