Crushers are mainly used for crushing stones or mineral ores, recycling construction waste, and producing aggregate. This equipment aims to reduce large solid raw material masses into smaller sizes. They also help to change waste material form so that they can be simply disposed of or recycled. They can also be used for secondary and tertiary crushing to produce the finished product and crushing materials between two parallel solid surfaces.
In an ever-changing industry, waste is one of the major issues for companies when it comes to maximising profits and winning tenders. With the proper application of crushing materials can be reused in other areas of industrial applications.

Different types of crushers
There are three types of crushers. Types of crusher depend on the feeding method. These are- Primary crusher, Secondary crusher and Tertiary crusher.
The primary crusher is only for the breaking of large stones into pieces (this means primary crusher is not for the aggregate size material.). Examples of primary crushers are jaw crusher; hammer mill crusher and gyratory crusher. After receiving the primary crusher crush the material and produce a new fresh reduced size of the source material. The primary crusher has only functioned up to that point. A secondary crusher comes into action and further reduces the size. In secondary crushers some sizes of stones may pass directly from sieve number At the end tertiary crusher reduces the size of crushed pieces very much to the required size and it also brings the fineness to the crushed material. Tertiary crushers are at the job site and these are small in size.
Different types of crushers fall under each mentioned type, some of the popular ones are given below.
Jaw Crusher
A Jaw Crusher is one of the main types of primary crushers in a mine or ore processing plant. The size of a jaw crusher is designated by the rectangular or square opening at the top of the jaws. Primary jaw crushers are typical of the square opening design, and secondary jaw crushers are of the rectangular opening design. A Jaw Crusher reduces large size rocks or ore by placing the rock into compression. A fixed jaw, mounted in a “V” alignment is the stationary breaking surface, while the movable jaw exerts a force on the rock by forcing it against the stationary plate. Due to their smaller physical size, jaw crushers are also ideal for tight spaces, such as underground mining and mobile crushing applications.
Newer jaw crusher models are more focused on safety and easy maintenance. Hydraulic separation and individual lifting of shells are in a trend that creates a better environment for any workers on-site working with the equipment
Impact crusher
An impact crusher is a machine that uses striking as opposed to pressure to reduce the size of a material. Impact crushers are designated as a primary, secondary, tertiary or quaternary rotor crusher depending on which processing stage the equipment is being utilized. Impact Crushers may be used as primary, secondary, or tertiary crushers depending on the Producer’s final-product-size needs. Impact Crushers are available in stationary, track, and portable configurations meeting any demand for any of these industries. Although Impact Crushers generally have a higher operating cost than other crushers, they tend to produce a more uniform particle shape (cubical) which is desirable and produces more fines for hot asphalt producers. Common types of Impact Crushers are Horizontal Shaft Impactor (HSI) and Vertical Shaft Impactor (VSI).
The new hybrid models of impact crusher are engineered for maximum feed size, target output size, and total capacity. The newer models are capable of producing construction-grade aggregate, artificial sand and stone materials, run of mine material, especially for the secondary and tertiary crushing stages.
Gyratory crusher
Gyratory crushers are principally used in surface-crushing plants. The gyratory crusher consists essentially of a long spindle, carrying a hard steel conical grinding element, the head, seated in an eccentric sleeve. The spindle is suspended from a “spider” and, as it rotates, normally between 85 and 150 rpm, it sweeps out a conical path within the fixed crushing chamber, or shell, due to the gyratory action of the eccentric. Gyratory crushers provide high throughput and less downtime to bring maximum efficiency to your operation.
The new primary gyratory crushers have new advancements that bring increased speeds, higher installed power and mechanical improvements. All of these combine to bring additional throughput for your primary gyratory crusher.



Cone crusher
A Cone Crusher is a compression type of machine that reduces material by squeezing or compressing the feed material between a moving piece of steel and a stationary piece of steel. The crushed material is discharged at the bottom of the machine after they pass through the cavity. Cone crushers are popular rock crushing machines in aggregate production, mining operations, and recycling applications. They are normally used in secondary, tertiary, and quaternary crushing stages.
The new hybrid models of cone crusher come with multi-cylinder hydraulic cone systems suited for the secondary or tertiary stages of crushing plants by changing body liners and adaptors. It comes with the automatic control and fingertip manipulation system and two hydraulic cylinders that have a protective effect that if one overloads, then another one can fast react to clear choke merely by remote control.
Stationary hybrid crushers
Stationary hybrid crushers combine the advantages of different roll crusher systems and are an ideal solution for primary, secondary and tertiary crushing applications. They have specially designed teeth, hydraulic gap adjustment, overload protection, and a scraper system perfect for dealing with sticky materials. These machines can work at capacities of up to 12,000 metric tons per hour, enabling you to keep productivity high whilst producing high-quality output.
The newer models have a compact design and take up minimal space. The crushing rolls are equipped either with crushing rings, segments, or crushing picks, depending on the application and feed material. The drive system for the rolls consists of individual electric motors for each roll, as well as couplings and gears. Standard components are used for cost-effectiveness and simpler maintenance.
Tracked impact crusher
The overall range of capacity for mobile impact crushers is roughly about 100 to 500 tons per hour. Today’s mobile impact crushers are especially ideal for smaller-scale recycling operations, for on-site recycling, and tight-space urban and roadside applications. These units are transportable by trailer, simply driven off at the location of the material that needs to be processed, and go to work very quickly. With their capability to produce accurately-sized, cubical-shaped end-product, mobile impact crushers work well as stand-alone plants, or they can add significant productivity to any operation, working in tandem with a jaw crusher or screen plant.
The newer models use a direct drive system for optimum fuel efficiency and low operating costs and include several user-friendly features. This ensures that they’re both simple to operate, and easy to maintain.



Roller crusher
This is a type of secondary or reduction crusher consisting of a heavy frame on which two rolls are mounted. These are driven so that they rotate toward one another. Rock fed in from above is nipped between the moving rolls, crushed, and discharged at the bottom.
The newer models offer belt-driven Roll Crushers in four designs: Single Roll, Double Roll, Triple Roll and Quad Roll Crushers, which provide a substantial return on investment by operating at low cost and maximizing yield by generating minimal fines. The rugged design, which incorporates a fabricated steel base frame lined with replaceable abrasion-resistant steel liners, stands up to the toughest mineral processing applications while providing safe and simple operation, including an automatic tramp relief system to allow uncrushable objects to pass while the crusher remains in operation.
Hammer-mill crusher
A hammer-mill is a rock crusher that employs a rain of hammer blows to shatter and disintegrate a variety of materials.
The newer models of this machine generate high-quality aggregates, cubical in shape, with superior soundness. Available in three sizes, the HammerMaster is known for making excellent asphalt chip material, concrete stone, and general base material and road rock. This mill is also capable of making agricultural lime for pH control in farm fields.

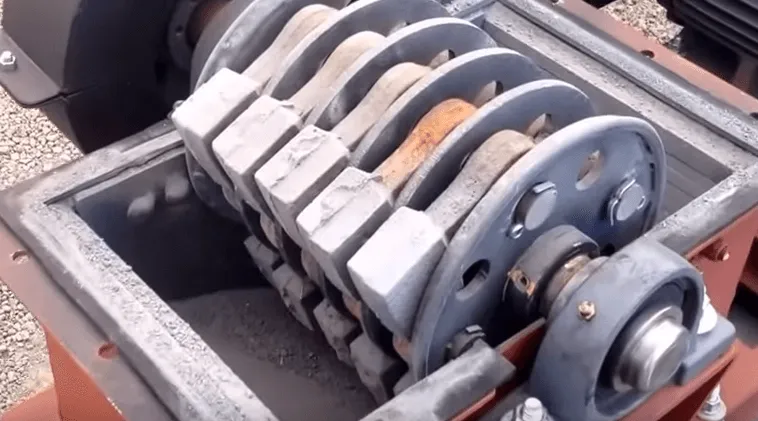
Rod mill crusher
Rod mills run along with the outside gear. Materials spirally and evenly enter the crushing chamber along the input hollow axis by input devices. Steel rods of different specifications are installed in the crushing chamber. When the frame rotates, centrifugal force is produced. At the same time, the steel rods are carried to some height and then fall to grind and strike the material. After grinded in the crushing chamber, the powder is discharged by an output material board.
The newer models of this machine are driven by motor with speed reducer and peripheral large gear, or low-speed synchronous motor with peripheral large gear. The grinding medium steel rod is put into the cylinder which is lifted, and then falls under the action of the centrifugal force and friction force. The materials entering into the cylinder from the feeding inlet are grinded by movable grinding medium and discharged out by overflow and continuously feeding.
Ball mill crusher
A ball mill is a type of grinder used to grind, blend and sometimes for mixing of materials for use in mineral dressing processes, paints, pyrotechnics, ceramics and selective laser sintering. It works on the principle of impact and attrition: size reduction is done by impact as the balls drop from near the top of the shell. The newer models of this machine are widely used in cement, silicate products, new building materials, refractory materials, fertilizer, black and non-ferrous metals and glass ceramics and other production industries of all kinds of ores and other grind-able materials can be dry or wet grinding.

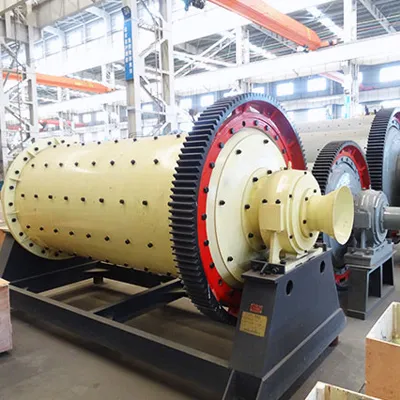

Conclusion
Manufacturers offering crushing equipment have expanded their respective ranges, offering additional capabilities for these segments. Mobility and versatility have been key factors in the development of new models, with many firms also offering new options in the shape of electric and hybrid drive systems.
Image Source:
reasonsto.com.au, mclanahan.com, fte-china.com, rocktechnology.sandvik, tesab.com, zerozedz.en.ec21.com, gkpulverizer.com, 911metallurgist.com,