Developments in road and highway continue to increase the demand for paved roads. To meet this demand, the soil compaction equipment is required to work on different types of terrains and within a very tight schedule. The vital features required in compaction equipment are higher levels of productivity with fewer numbers of passes and the right frequency settings. Operators must be able to execute their work in a manner that will provide for maximum compaction with suitable roller equipment. The pneumatic tyred roller is one such preferred compaction equipment It is used on roads and highways to achieve density and smoothness. The use of a pneumatic tyred roller, particularly in the construction of roads is necessary to avoid timely road damages and potholes. These types of compaction equipment are suitable for soft base materials or layers of loose soil, grained sands cohesive soils and very effective for bituminous layers where the design mix has a high content of fines. They can be used on both soil and asphalt which benefit a road building contractor to have only one compactor for both stages of construction – base and asphalt.
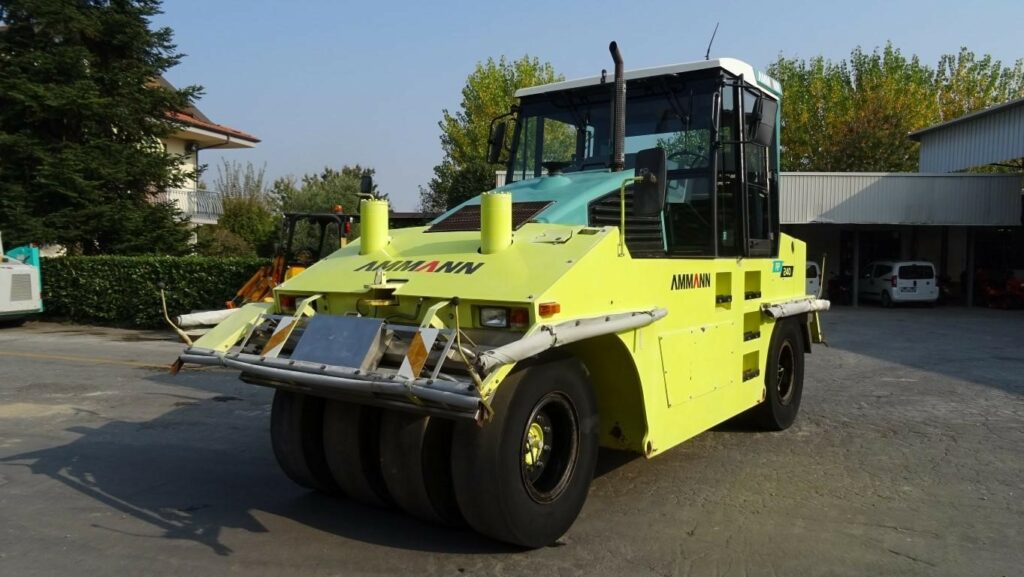
Adopting the pneumatic tyre to compact the layer will not damage the compacted materials. The compact performance can be improved by adding or reducing the counterweight and changing the inflation pressure of the tyres. Because of the kneading effect produced by the tyre’s elasticity, the material displacement will be produced in all directions, forming even dense surfaces without cracks, which can prolong the service life of the road. Discussed below are different types of models used in projects in India.
Pneumatic tyred rollers for compaction adjustment
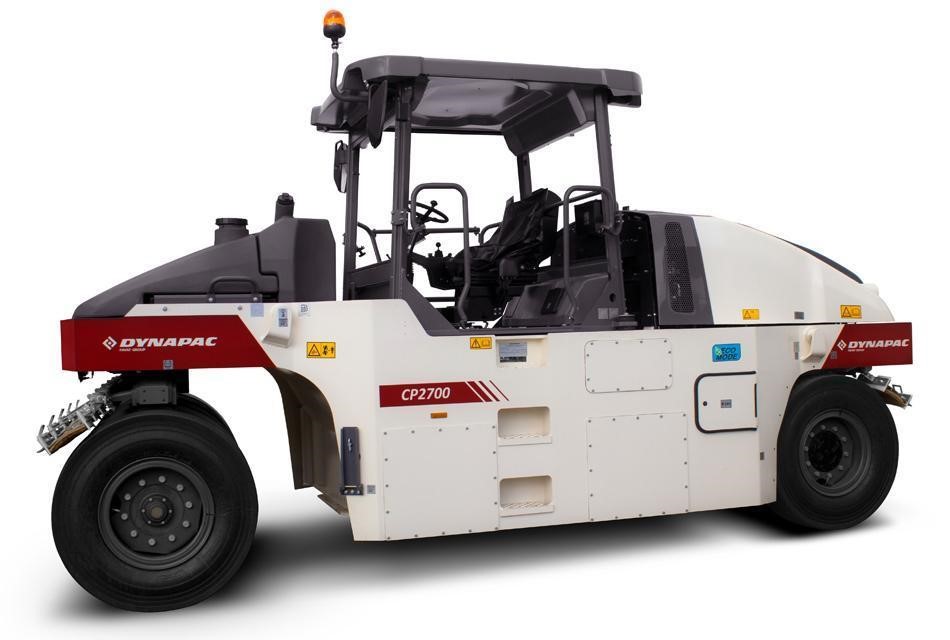
The new pneumatic tyred roller is available with compaction width 2370 mm and a maximum operation mass of up to 30 000 kgs. It is ideally suited for a wide range of high-quality applications. The new models are built with a hydraulic transmission system, which simplifies steering and on-off operations. A single pump, single motor transmission system with steady speed adjustment poses no impact on road material. An optimised engine reduces fuel consumption and emissions. It is easy to change engine liquids and hydraulic fluid without risk of spillage. To reduce noise, the cooling fans are thermostatically controlled, and the entire machine produces a low level of ambient noise. The models are equipped with a spacious platform with operator-friendly controls, plus a rotating and sideways sliding seat and steering assembly. Available as an option is a comfortable cab that provides outstanding all-round visibility with the added benefit of either air conditioning or Automatic Climate Control.
Pneumatic tyred roller to achieve uniform material density
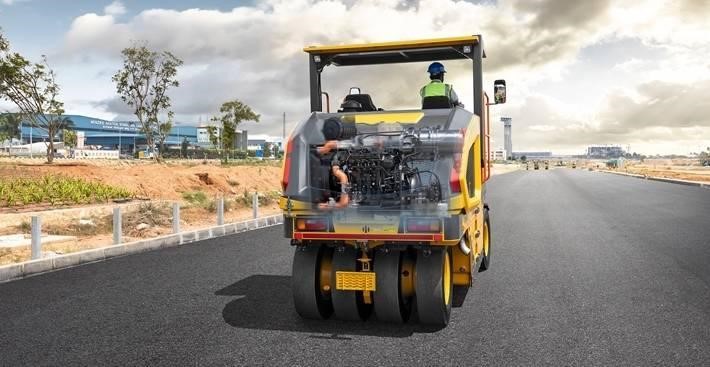
The models now feature the perfect kneading effect required to achieve uniform material density. The four wide front and rear tires overlap by 50mm to provide full-width coverage, while the isostatic levelling cylinders secure consistent contact with the material for excellent surface sealing. This machine has overlapping tyres for complete coverage. The other features of the model includes, hydrostatic drive, ISO-static suspension, rust-proof water system, sealed ballasting compartment, better amplitude and centrifugal force range. It has dual operator seats with a sliding console which provides unobstructed visibility in all directions. Isostatic levelling cylinders keep the front tyres in even contact with the material surface at all times. Irregularities in the material are removed and excellent surface sealing is achieved. The pressurised, rust-proof LDPE water system features an adjustable flow rate which can be used by the operator as needed to help eliminate material build-up on the tire surface, maintain soil surface temperature and reduce water refills. The water storage tank level indicator is clearly in view, allowing the operator to easily monitor the water level. Operator comfort is kept to a maximum with features including a sliding console, outstanding visibility, suspension on both seats.
Pneumatic tyred rollers with easy ballasting
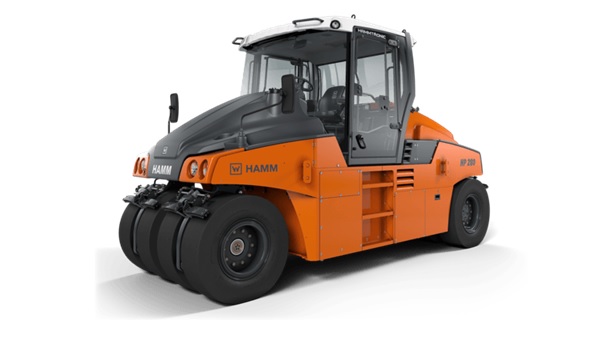
Newer models come equipped with a ballasting concept for fast, optimum equipping of the machine. Ballast can be added or removed to ensure the proper static weight. Space for ballast materials is built into the frame as well as from underneath of the machine, making the adjustment convenient and consistent. Ballast materials include concrete and steel. The ballast spaces between the wheelsets allow the weight of the machine to be adjusted in no time using pre-made ballast bodies. The different variants allow for a high degree of flexibility for compaction force and depth. With its powerful disc brakes, the machine models can be rapidly and safely brought from full speed to a standstill, even when carrying the maximum ballast load. With their well-conceived design, a modern, spacious panoramic cabin and many creative refinements, the new series pneumatic tyred rollers provide the best possible overview and maximum user-friendliness. Whether with a cabin or open operator’s platform that has an outstanding view of the machine and construction site at all times. A special feature of the compact pneumatic tyred rollers is their asymmetric frame. It ensures an unobstructed view of the outer edges of the front and rear wheels. With optimum safety in mind, the brake pedal is integrally arranged on the seat-operating unit in such a way that the driver can find it in the same place in every working position and stop the roller immediately.
Conclusion
Discussed above are different types of pneumatic model operation efficiency are discussed available in India. In next series of compaction articles will focus on newer and upgraded models.
Analysis of Compaction Equipment
Pneumatic tyred rollers with the hydrodynamic propulsion system
Pneumatic tyred rollers with better compaction width