Full-Depth Reclamation (FDR) is a cost-effective and sustainable pavement rehabilitation technique that involves recycling the existing asphalt and base materials to create a new, stabilized road base. The process pulverizes the old pavement and mixes it with underlying materials, often incorporating stabilizing agents like cement, lime, or asphalt emulsion to enhance strength and durability. FDR eliminates the need for removing and disposing of old pavement, reducing construction waste and costs while improving structural integrity.
Applications of Full-Depth Reclamation (FDR)
- Rural and Low-Volume Roads – FDR is widely used for rehabilitating deteriorated rural roads, where cost-effective and long-lasting solutions are needed.
- Highway Rehabilitation – It helps in strengthening aging highways by improving the pavement structure without the need for complete reconstruction.
- Parking Lots – FDR is an efficient solution for large commercial and industrial parking areas, reducing downtime and material costs.
- Airports and Runways – Used in rehabilitating taxiways and runways by providing a durable and stable base for resurfacing.
- Industrial and Heavy-Load Areas – Ideal for roads and pavements subjected to high traffic loads, such as ports, warehouses, and logistics hubs.
- Urban Roadway Restoration – Applied in city streets to enhance structural integrity while minimizing disruption to traffic.
- Military and Defense Infrastructure – Used for strengthening roads and airstrips in defense installations, ensuring long-term performance under heavy loads.
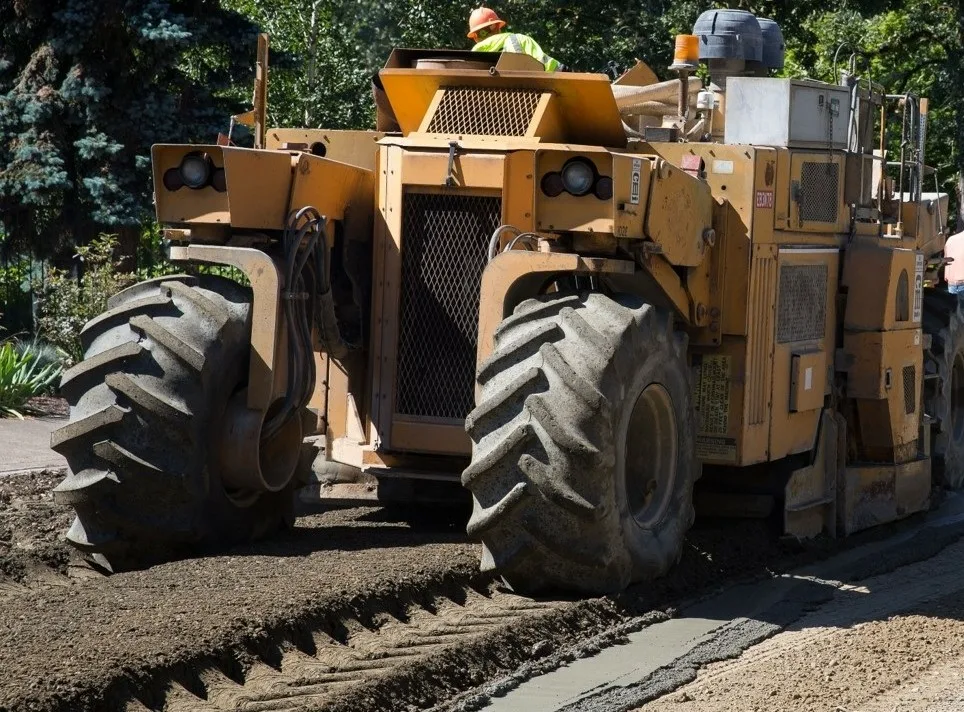
Advantages of Full-Depth Reclamation (FDR)
- Reuses existing pavement, reducing material costs.
- Minimizes waste and environmental impact.
- Enhances pavement durability and load capacity.
- Speeds up road rehabilitation projects.
- Reduces future repair and overlay needs.
- Prevents water infiltration and erosion.
- Mix design can be adjusted for specific conditions.
- Keeps roads accessible during work.
- Provides a durable foundation for resurfacing.
Types of Full-Depth Reclamation (FDR)
- Mechanical Stabilization- Mechanical stabilization involves blending the existing pavement materials with additional aggregates to enhance the base’s strength and durability. This method does not use chemical binders but relies on proper gradation and compaction to achieve stability. It is commonly used in areas where the existing material quality is sufficient but requires improved load-bearing capacity.
- Bituminous Stabilization- In this method, asphalt emulsion or foamed asphalt is added to the pulverized material to create a flexible and durable base. Bituminous stabilization improves moisture resistance, reduces cracking, and enhances pavement flexibility, making it suitable for roads subjected to varying weather conditions and traffic loads.
- Chemical Stabilization- Chemical stabilization involves incorporating cement, lime, or fly ash into the reclaimed material to strengthen the base. This method enhances compressive strength, reduces plasticity, and improves resistance to water infiltration, making it ideal for weak or moisture-sensitive soils. It is widely used in areas with high clay content or poor subgrade conditions.
- Geosynthetic Stabilization- This method integrates geotextiles, geogrids, or other geosynthetic materials into the reclaimed pavement to improve load distribution and prevent base layer movement. Geosynthetic stabilization is particularly useful in areas with weak or unstable subgrades, as it enhances structural integrity and extends pavement life.
- Combination Stabilization- Combination stabilization uses a mix of mechanical, chemical, and bituminous stabilization techniques to achieve optimal pavement performance. By tailoring the stabilization approach based on site conditions, this method provides a highly durable and resilient base suitable for high-traffic roads and challenging environments.
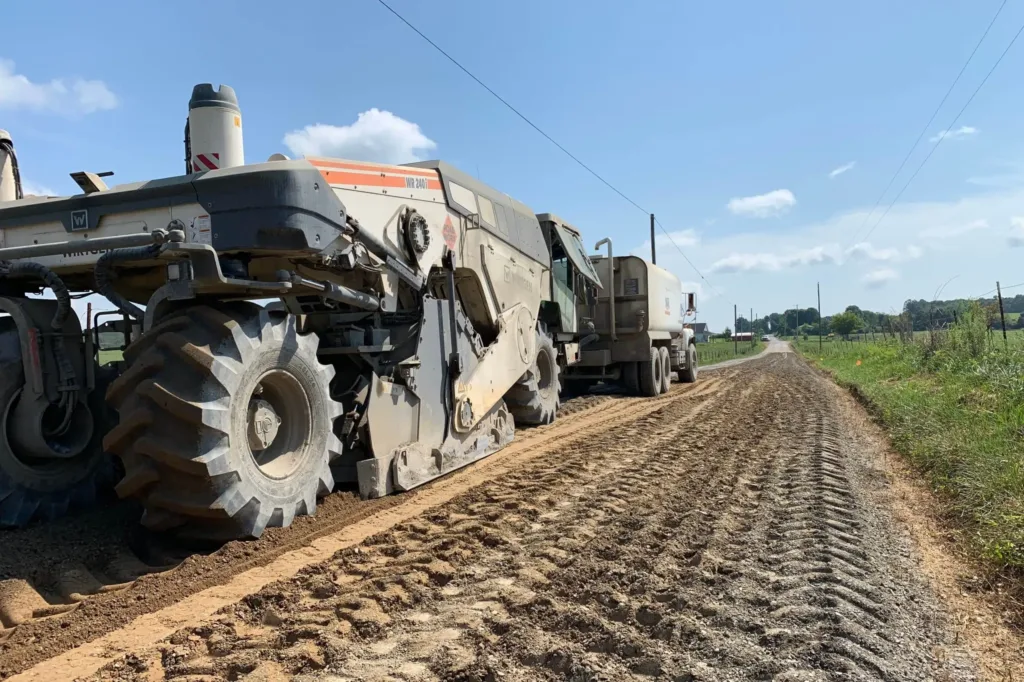
Different Equipment Used for Full-Depth Reclamation (FDR)
Full-Depth Reclamation (FDR) requires specialized equipment to efficiently break down, mix, stabilize, and compact pavement layers, ensuring a durable and long-lasting road surface. Each piece of machinery plays a important role in different stages of the process, from initial pulverization to final paving.
Pulverizer/Milling Machine
The pulverizer or milling machine is the first piece of equipment used in FDR. It grinds and crushes the existing asphalt pavement and base layers into smaller particles, making it easier to mix with stabilizers. This process ensures proper material breakdown, removes irregularities, and prepares the base for further treatment. By reducing large chunks of old pavement, the pulverizer helps create a more uniform mixture, improving the final strength and durability of the reclaimed road.
Reclaimer/Stabilizer
The road reclaimer or stabilizer is responsible for blending the pulverized material with stabilizing agents like cement, lime, or asphalt emulsion. It ensures uniform mixing while maintaining the correct depth and proportion of stabilizers to create a strong and durable base. Equipped with high-powered rotating drums, this machine thoroughly mixes the reclaimed materials with additives, preventing weak spots and ensuring structural integrity.
Cement or Lime Spreader
The cement or lime spreader evenly distributes dry stabilizers over the reclaimed surface, enhancing strength and durability. Proper application ensures a uniform reaction between the stabilizers and the pulverized material, preventing inconsistencies in the pavement. These machines have calibrated spreader mechanisms that control the distribution rate, ensuring optimal performance and preventing excess use of materials, which can lead to waste.
Water Truck
The water truck plays a pivotal role in maintaining the required moisture content for stabilization. It sprays water onto the reclaimed material to activate chemical stabilizers like cement or lime, ensuring better binding and improved compaction. Proper moisture control is essential for achieving the desired density and strength, as too little or too much water can compromise the stabilization process. Water trucks are designed with adjustable nozzles to regulate flow and coverage, ensuring an even distribution.
Motor Grader
The motor grader is used to level and shape the reclaimed material, ensuring a uniform surface with proper grading and slopes. The blade of the grader can be adjusted to achieve precise grading, which prevents water accumulation and improves road longevity. By ensuring an even surface, the motor grader enhances the final pavement’s structural integrity and ride quality.
Pneumatic Tire Roller
The pneumatic tire roller applies uniform pressure using multiple rubber tires to compact the reclaimed material. This helps remove air voids, enhance density, and improve the pavement’s ability to withstand traffic loads and environmental stresses. The roller’s flexible tires adjust to surface irregularities, providing better contact with the material and ensuring thorough compaction. This type of roller is especially useful in achieving a smooth finish and enhancing the load distribution capacity of the stabilized base.
Vibratory Padfoot Roller
The vibratory padfoot roller is used for deep compaction, particularly when stabilizing with cement or lime. Its high-frequency vibrations ensure strong bonding, increasing the road’s load-bearing capacity and longevity, especially in weak subgrade conditions. The padfoot drum design allows for deeper penetration into the material, improving the structural integrity of the stabilized layer. By applying repeated vibrations, this roller ensures uniform density, preventing settlement or premature pavement failure.
Asphalt Distributor
The asphalt distributor is essential when bituminous stabilization is required. It sprays asphalt emulsion or foamed asphalt onto the reclaimed surface, improving flexibility, moisture resistance, and ensuring a longer-lasting roadway. This equipment is equipped with adjustable spray bars that allow precise application, ensuring an even coating that binds well with the reclaimed material. Proper application of asphalt emulsion enhances pavement durability by reducing cracks and preventing water infiltration.
Front-End Loader
The front-end loader is essential for material handling during the FDR process. It assists in stockpiling, transporting, and loading aggregates, stabilizers, or reclaimed materials, ensuring a continuous supply for efficient operation. These machines are equipped with powerful hydraulic arms and large buckets, allowing them to handle heavy loads quickly.
Paver
The paver is the final piece of equipment in the process, applying the new asphalt or concrete overlay over the stabilized base. It ensures a smooth, even surface that provides long-term durability and optimal performance for the roadway. Modern pavers are equipped with automated controls and heating elements that maintain the correct temperature, ensuring proper bonding of materials.
Conclusion
Full-Depth Reclamation (FDR) is a smart and sustainable solution for restoring roads with minimal waste and disruption. Its efficiency and adaptability make it a smart choice for modern infrastructure, ensuring durable and cost-effective roads for the future.