Grab diaphragm wall machines are specialised construction equipment utilized for the excavation and construction of diaphragm walls. These machines used a hydraulic arm equipped with a grabber mechanism to efficiently excavate soil and create trenches for the installation of diaphragm walls. With their precise control and ability to operate in various soil conditions, grab diaphragm wall machines ensure accurate and reliable construction of structural walls, providing essential support and stability for a wide range of construction and infrastructure projects.
Components of a grab diaphragm wall machine:
1. Main Frame: The main frame provides structural support and houses the various components of the machine.
2. Hydraulic System: This system powers the machine’s movement and operation. It includes hydraulic pumps, cylinders, valves, and hoses.
3. Hydraulic Arm: Mounted on the main frame, the hydraulic arm extends and retracts to reach the desired depth and position for excavation. It also supports the grabber mechanism.
4. Grabber Mechanism: Attached to the end of the hydraulic arm, the grabber mechanism consists of jaws or claws that open and close to grip and lift soil during excavation.
5. Control Panel: The control panel allows operators to manage the machine’s functions, such as controlling the movement of the hydraulic arm and adjusting excavation parameters.
6. Crawler Tracks or Wheels: These provide mobility and stability to the machine, allowing it to move along the construction site and navigate varying terrain.
7. Reinforcement Bar Installation System: Some machines are equipped with a system for inserting reinforcement bars into the trench after excavation to strengthen the diaphragm wall.
How does a a grab diaphragm wall machine works?
1. Positioning: The machine is positioned at the designated starting point for the diaphragm wall construction, typically marked out according to project plans and specifications.
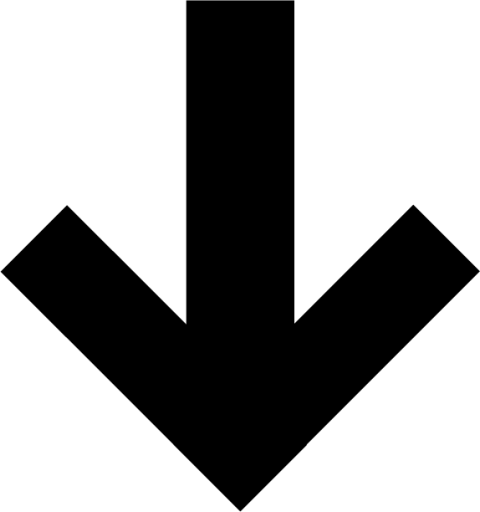
2. Preparation: Operators ensure that the machine is in proper working condition and that all safety measures are in place. This includes checking hydraulic systems, controls, and safety features.
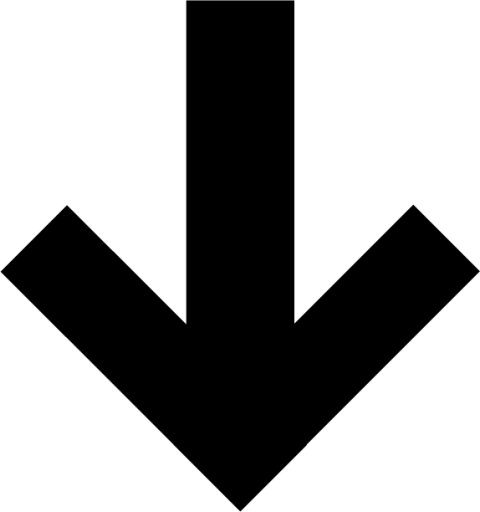
3. Setting Parameters: Operators set parameters such as the depth and width of the trench to be excavated, as well as any specific requirements for the wall construction.
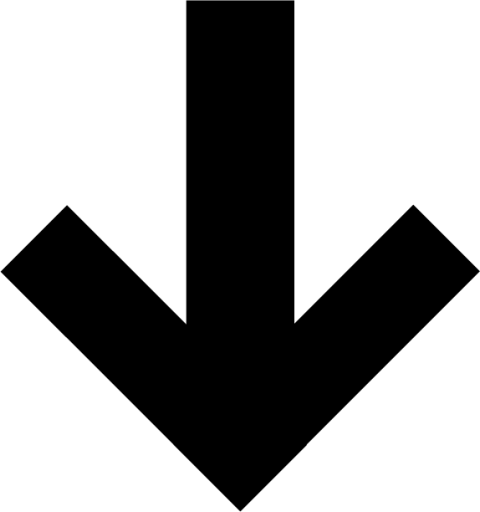
4. Lowering the Hydraulic Arm: The hydraulic arm with the grabber mechanism is lowered into the ground at the designated starting point of the trench.
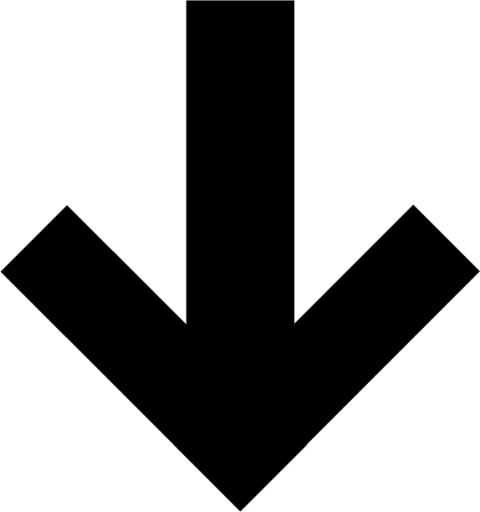
5. Excavation: The grabber mechanism grabs a portion of soil and lifts it out, creating the trench for the diaphragm wall. The machine moves along the designated path as excavation progresses, guided by operators.
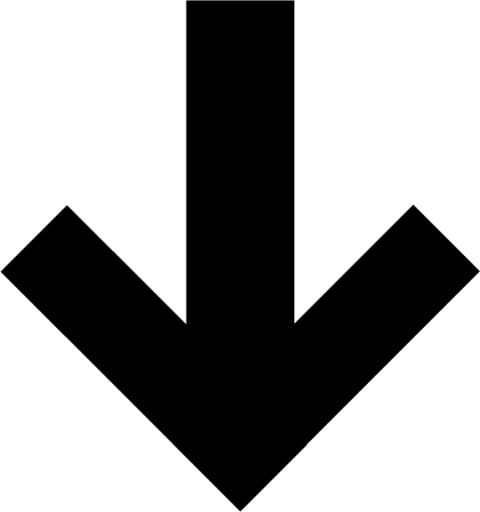
6. Reinforcement Installation: Once the trench is excavated to the required depth, reinforcement bars are inserted into the trench. These bars provide additional strength and stability to the diaphragm wall.
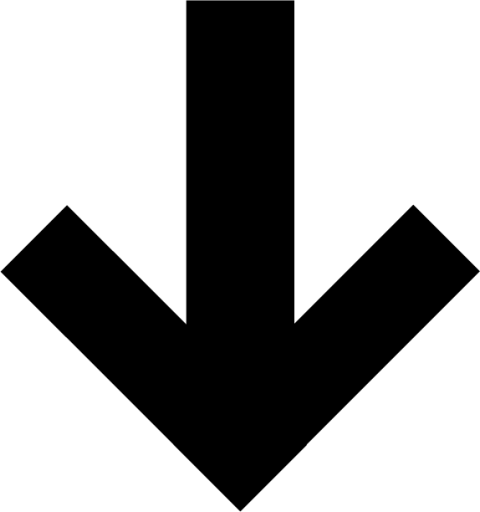
7. Concrete Pouring: Concrete is poured into the trench to form the diaphragm wall. The machine may be equipped with features for pouring concrete directly into the trench.
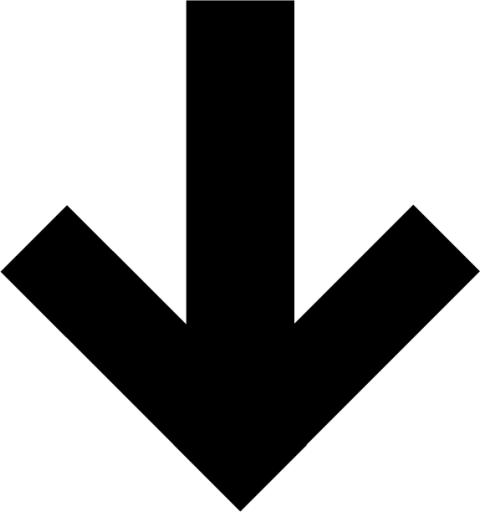
8. Finishing: Operators ensure that the concrete is properly poured and consolidated within the trench to form a solid diaphragm wall structure.
Advantages of grab diaphragm wall machines:
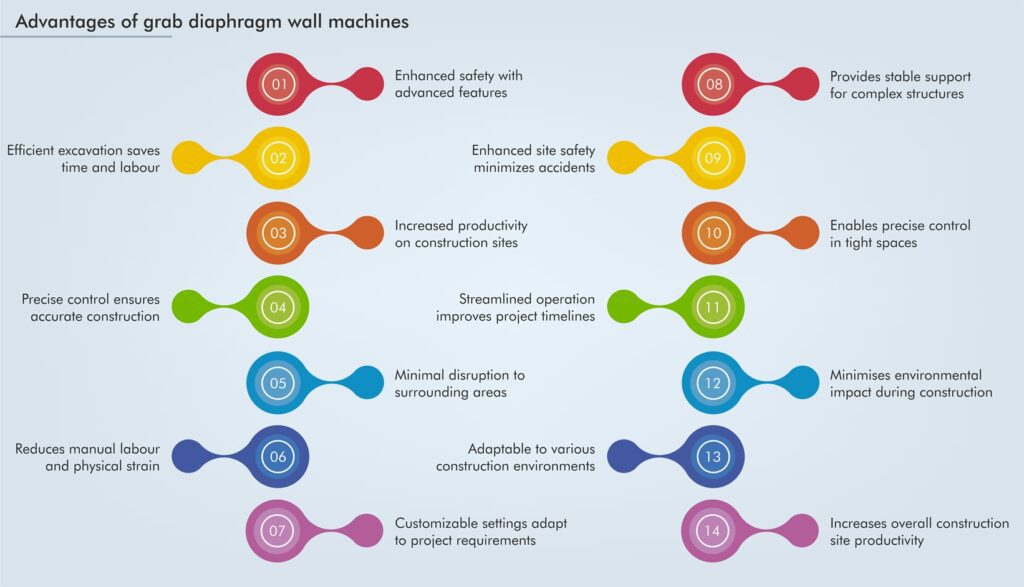
Types of grab diaphragm wall machines:
1. Single-Clamp Grab Machines:
Single-clamp grab machines feature a hydraulic arm equipped with a single clamp for excavating trenches in diaphragm wall construction projects. Their simplicity and efficiency make them ideal for straightforward excavation tasks. These machines offer precise control over the excavation process, allowing for accurate construction of diaphragm walls. Their advantage lies in their straightforward design, which results in ease of operation and maintenance. They are commonly used in a variety of construction projects where diaphragm walls are required, including building foundations, underground structures, and retaining walls.
2. Double-Clamp Grab Machines:
Double-clamp grab machines are equipped with two clamps on the hydraulic arm, enabling faster excavation and increased productivity compared to single-clamp machines. Their dual-clamp design allows for simultaneous gripping and lifting of soil, speeding up the excavation process. These machines are advantageous for large-scale construction projects where efficiency and productivity are crucial. They are commonly used in projects that require extensive diaphragm wall construction, such as deep foundations for high-rise buildings or infrastructure projects.
3. Telescopic Grab Machines:
Telescopic grab machines feature a hydraulic arm with telescopic sections that provide greater reach and flexibility in excavation depths and positions. Their telescopic design allows for adjustable reach, making them suitable for projects with varying excavation requirements. These machines offer versatility and adaptability, allowing operators to adjust the arm length to reach desired depths without the need for additional equipment. Their advantage lies in their ability to handle a wide range of excavation tasks, from shallow trenches to deep diaphragm walls. They are commonly used in projects where excavation depths vary or access to the site is limited.
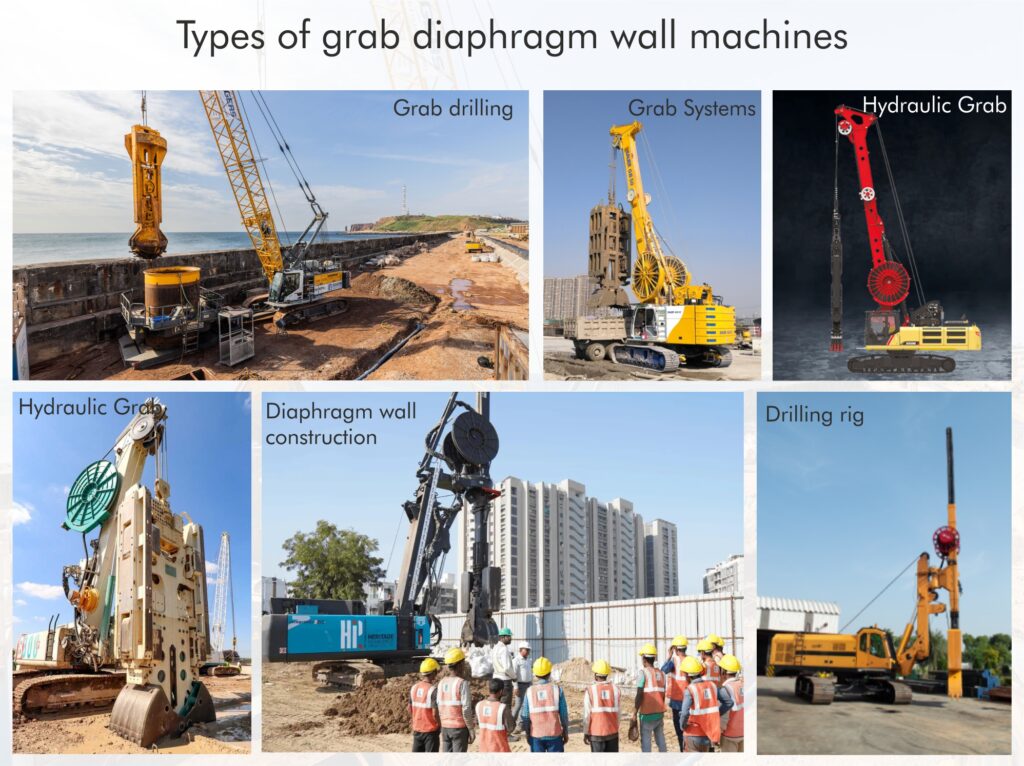
4. Auger Grab Machines:
Auger grab machines utilize auger attachments instead of traditional grabs for excavation, making them effective in challenging soil conditions such as rock or gravel. The auger attachment features rotating blades that penetrate and break up the soil, allowing for efficient excavation even in dense or hard soils. These machines offer superior performance in tough soil conditions, where traditional grab machines may struggle to penetrate the ground. Their advantage lies in their ability to handle difficult soil conditions effectively, reducing excavation time and costs. They are commonly used in projects where conventional excavation methods are impractical due to the soil composition.
5. Hydraulic Rotary Grab Machines:
Hydraulic rotary grab machines utilize a rotating mechanism to improve soil penetration and excavation efficiency. They feature a hydraulic arm with a rotary grab that rotates as it penetrates the soil, allowing for easier excavation in dense or hard soils. These machines offer enhanced soil penetration compared to traditional grab machines, resulting in faster excavation rates and increased productivity. Their advantage lies in their ability to tackle challenging soil conditions with ease, reducing excavation time and effort. They are commonly used in projects where soil conditions require enhanced excavation capabilities, such as urban construction sites or areas with rocky terrain.
6. Compact Grab Machines:
Compact grab machines are designed for use in confined spaces or urban areas where manoeuvrability is limited. They feature a smaller footprint while still maintaining high excavation capabilities, making them ideal for projects with tight access or space constraints. Their compact design allows them to navigate narrow streets or restricted areas with ease, minimising disruption to surrounding structures or infrastructure. Their advantage lies in their ability to perform excavation tasks in challenging environments where larger machines may not be practical. They are commonly used in urban construction projects, basement excavations, or renovation works where space is limited.
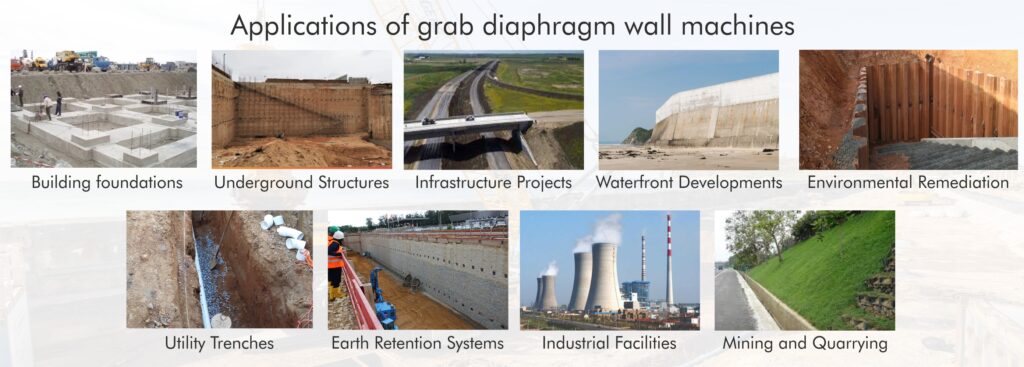
Conclusion
Grab diaphragm wall machines stand as an indispensable equipment used for an array of project requirements. From building foundations and underground structures to infrastructure projects and environmental remediation efforts, grab diaphragm wall machines play a crucial role in shaping the modern built environment. Their ability to handle diverse soil conditions, navigate tight spaces, and enhance safety on construction sites makes them invaluable assets for engineers, contractors, and project managers alike. As technology continues to advance, these machines will undoubtedly remain at the forefront of innovation, driving progress and efficiency in construction and infrastructure projects.
Image Source: liebherr.com, bauer-equipment.in, sany.in, casagrandegroup.com, heritageconstruction.in, apollotechno.com