There is a need for a smarter approach when it comes to road construction. The aim should be to chalh down the type of road construction that is durable as well as cost effective. Several different types of road construction methods and processes have evolved throughout the years and now we have the more number of options for road construction.The type of surface material used in road construction is largely dependent on traffic volume, weight load and weather conditions. There is a strong desire to optimize the use of materials currently used for road construction and to seek advanced materials that are cheaper, better performing, and less damaging to the environment. For Construction Invoice Templates see Zintego.com
Given below are 5 types of road construction that are durable and cost-effective.
Whitetopping roads
Whitetopping is the covering of existing asphalt pavement with a layer of Portland cement concrete. Whitetopping is divided into types depending on the thickness of the concrete layer and whether the layer is bonded to the asphalt substrate. The principal purpose of an overlay is either to restore or to increase the load-carrying capacity or both, of the existing pavement. In achieving this objective, overlays also restore the ride-ability of the existing pavements which have suffered rutting and deformations, in addition to rectifying other defects such as loss of texture.
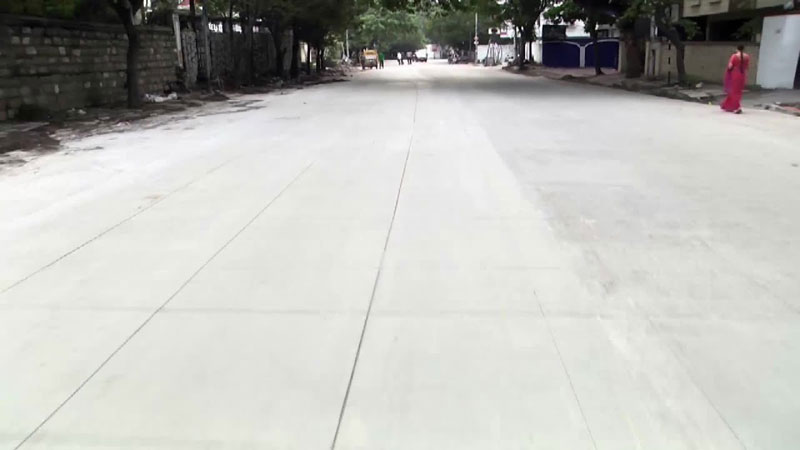
Whitetopping is suitable for asphalt pavement with little deterioration, although repairs can be made to the asphalt if necessary. If the pavement is badly damaged, it should be completely removed and a new concrete pavement should be installed. The pavement should be relatively hard, as well. Deterioration of overlays is significantly increased on asphalt bases with high viscosity. If a grade or a distance between the pavement and a bridge needs to be preserved, the asphalt can be milled so that the height of the pavement does not change. However, white topping requires the asphalt layer to be at least three inches thick. If necessary, a section of a new concrete roadway can be placed under a bridge with gentle slopes on either side that meet up with the white-topped portions of the road.
Polymer Fiber Reinforced Concrete roads
Polymeric fibers are being used now because of their no risk of corrosion and also being cost-effective. Polymeric fibers normally used are either polyester or polypropylene. A significant number of pavement applications use FRC material technology, including highways, local streets, intersections, parking lots, bus pads, sidewalks, driveways, bridge decks, pavement overlays, industrial floors, airfield pavement overlays, and patches . For pavement applications, FRC can be used for new construction as well as for maintenance (patching), rehabilitation (overlays), and reconstruction. For minor pavement rehabilitation, the use of FRC for bonded concrete overlays on asphalt or composite pavements has seen significant growth in the past few years. The thickness of a bonded concrete overlay of asphalt (BCOA) ranges from 3 to 6 in., and the majority of FRC overlays of this type have been for the thinner installations. Macrofibers proves very effective in providing extra structural capacity and maintaining joint load transfer efficiency in UTW [ultra-thin whitetopping] pavements
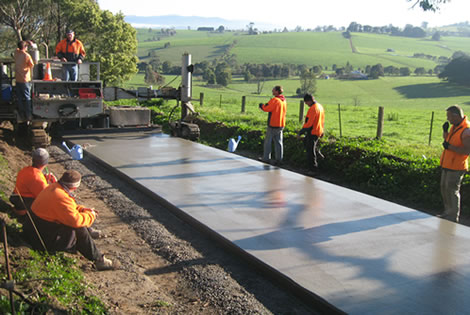
Bituminous roads
Bituminous surface treatment (BST) or chip seal is used mainly on low-traffic roads, but also as a sealing coat to rejuvenate an asphalt concrete pavement. It generally consists of aggregate spread over a sprayed-on asphalt emulsion or cut-back asphalt cement. The aggregate is then embedded into the asphalt by rolling it, typically with a rubber-tired roller. This type of surface is described by a wide variety of regional terms including “chip seal”, “tar and chip”, “oil and stone”, “seal coat”, “sprayed seal” or “surface dressing” or as simply “bitumen.” These are laid down using specialized and proprietary equipment. They are most often used in urban areas where the roughness and lose stone associated with chip seals is considered undesirable.
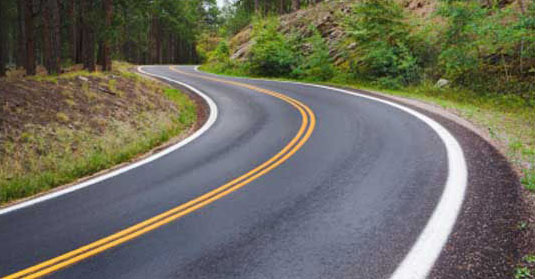
Composite pavement road
Composite pavements combine a Portland cement concrete sublayer with an asphalt. They are usually used to rehabilitate existing roadways rather than in new construction. Asphalt overlays are sometimes laid over distressed concrete to restore a smooth wearing surface. Geosynthetics can be used for reflective crack control. With break and seat and crack and seat processes, a heavy weight is dropped on the concrete to induce cracking, then a heavy roller is used to seat the resultant pieces into the subbase. The main difference between the two processes is the equipment used to break the concrete pavement and the size of the resulting pieces. The theory is frequent small cracks will spread thermal stress over a wider area than infrequent large joints, reducing the stress on the overlying asphalt pavement. Rubblization is a more complete fracturing of the old, worn-out concrete, effectively converting the old pavement into an aggregate base for a new asphalt road. Whitetopping uses Portland cement concrete to resurface a distressed asphalt road.
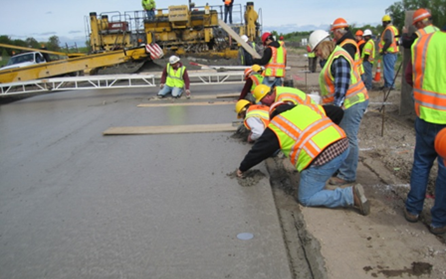
Gravel road
Applying gravel, or “metalling,” has had two distinct usages in road surfacing. The route of the roadway would first be dug down several feet and, depending on local conditions, French drains may or may not have been added. Next, large stones were placed and compacted, followed by successive layers of smaller stones, until the road surface was composed of small stones compacted into a hard, durable surface. “Road metal” later became the name of stone chippings mixed with tar to form the road surfacing material tarmac. The decision of whether to pave a gravel road or not often hinges on traffic volume. It has been found that maintenance costs for gravel roads often exceed the maintenance costs for paved or surface-treated roads when traffic volumes exceed 200 vehicles per day.
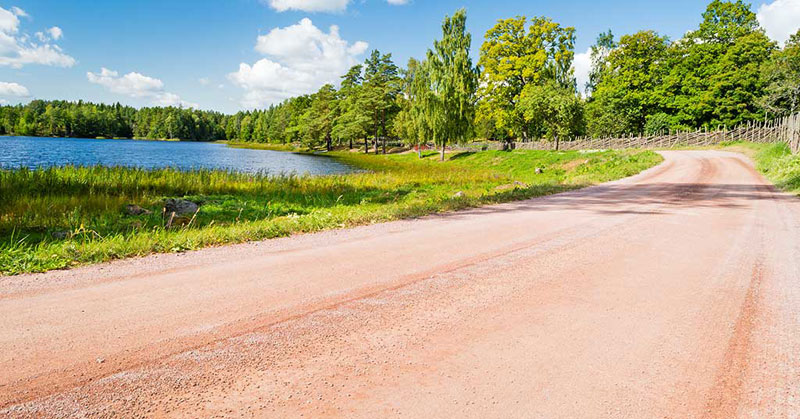
Image Source: youtube.com, barchip.com, engineeringtich.blogspot.com, dot.state.mn.us, khplant.co.za