Microtunneling is a trenchless construction method used to cross section tunnels without disturbing the surface above. This method is particularly valuable in urban areas where densely populated infrastructure makes traditional open-cut methods challenging. This trenchless construction method is used to install utility pipelines, such as water, sewage, or gas, with reduced impact on surrounding infrastructure and the environment.
How does the microtunneling method work?
The method involves using a microtunnel boring machine (MTBM) to excavate the tunnel while simultaneously installing the pipeline. The MTBM is guided by a laser system, ensuring precision in tunnel alignment and grade. Spoil (excavated material) is typically removed through a slurry system or a pipe conveyor to the surface. An overview of the method is given below;
1. Site Preparation:
– Identify the entry and exit points for the microtunneling machine.
– Ensure proper access and clearance for the equipment.
2. Pilot Bore:
– Use a pilot drill to create a small-diameter hole along the desired tunnel path.
– The pilot bore establishes the tunnel alignment for the larger microtunneling machine.
3. Assembly of Microtunneling Machine:
– Set up and assemble the microtunneling machine, including the cutting head, jacking system, and pipe-handling equipment.
4. Launch Shaft Construction:
– Build a launch shaft at the starting point, providing access for the microtunneling machine.
5. Installation of Pipe Sections:
– Connect pipe sections at the launch shaft.
– These pipes are pushed into the ground as the microtunneling machine progresses.
6. Microtunneling Machine Operation:
– Start the microtunneling machine, which excavates soil using a cutting head and simultaneously installs the pipe.
7. Jacking System:
– Utilize hydraulic jacks or other systems to push the microtunneling machine forward.
– The jacking force is carefully controlled to prevent excessive soil displacement.
8. Spoil Removal:
– Transport excavated soil (spoils) through the tunnel to the launch shaft using a slurry or other appropriate conveyance system.
9. Monitoring and Guidance:
– Continuously monitor the machine’s position, alignment, and performance.
– Adjust the direction and angle as needed to maintain accuracy.
10. Reception Shaft:
– Construct a reception shaft at the tunnel exit point to retrieve the microtunneling machine and complete the pipe installation.
11. Pipe Connection and Testing:
– Connect the installed pipe to the existing network or infrastructure.
– Perform tests to ensure the integrity and functionality of the newly installed pipeline.
12. Site Restoration:
– Backfill the launch and reception shafts, restoring the surface to its original condition.
– Ensure proper site cleanup and restoration.
Why Mircotunneling is important?
1. Precision Control: Microtunneling utilizes guidance systems, such as laser or gyroscopic systems, ensuring precise control over the tunnel alignment and grade.
2. Minimized Surface Settlement: The controlled excavation process in microtunneling reduces the risk of ground settlement on the surface.
3. Versatility in Geology: Microtunneling is suitable for various geological conditions, including cohesive soils, non-cohesive soils, and mixed-face conditions.
4. Reduced Environmental Impact: As a trenchless technology, microtunneling minimizes disturbance to the environment by avoiding extensive excavation and surface disruption.
5. Increased Safety: The use of remote-controlled microtunnel boring equipments enhances worker safety by reducing the need for personnel to be in the excavation area.
6. Applicability in Urban Areas: Microtunneling is well-suited for densely populated urban environments where minimizing disruptions to traffic, utilities, and structures is critical. It allows for the installation of pipelines beneath existing infrastructure with minimal impact.
7. Reduced Rehabilitation Needs: Since microtunneling causes less surface disturbance, the need for extensive restoration and rehabilitation after construction is significantly reduced. This can result in cost savings and shorter project timelines.
Different types of equipments used for microtunneling
Microtunnel Boring equipment (MTBMs): Microtunnel boring equipment (MTBMs) are specialized equipment used for trenchless excavation and installation of pipelines, conduits, or other underground structures. They operate by boring a tunnel through the soil or rock, typically in a circular profile, while simultaneously installing the desired infrastructure. These equipment come with cutting-edge technology, featuring powerful disc cutters or similar mechanisms to bore through various geological formations. MTBMs ensure precision in tunnel dimensions, making them ideal for projects where accuracy is important.

Slurry Microtunneling equipment: Slurry microtunneling equipment operates by using a mixture of water and additives (slurry) as a support fluid. The slurry stabilizes the tunnel face and carries away excavated material. This method is effective in preventing ground subsidence and maintaining stability in loose or sandy soils. The excavated material is transported through the slurry to a separation plant at the surface. Slurry equipments are commonly used in projects where maintaining ground stability is critical.

Auger Boring equipment: Tailored for softer soils, auger boring equipments utilize rotating augers to gradually excavate material. These equipments are particularly effective in less dense or cohesive ground conditions. Often employed in tandem with pipe jacking systems, auger boring equipments simplify the process of tunneling through softer terrains. The augers remove material as they rotate, creating a bore path that accommodates the subsequent installation of the tunnel lining.
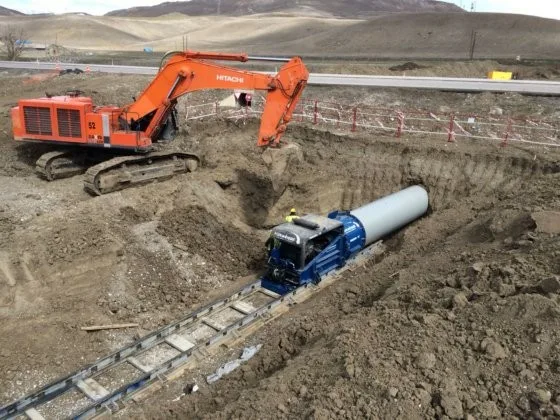
Guided Boring equipment: Equipped with advanced guidance systems, such as lasers, guided boring equipments maintains precise accuracy and direction during the boring process. These systems enable operators to control the alignment of the tunnel with exceptional precision. Guided boring equipments are instrumental in projects where maintaining a specific trajectory is critical, ensuring that the tunnel follows the designated path with minimal deviation.
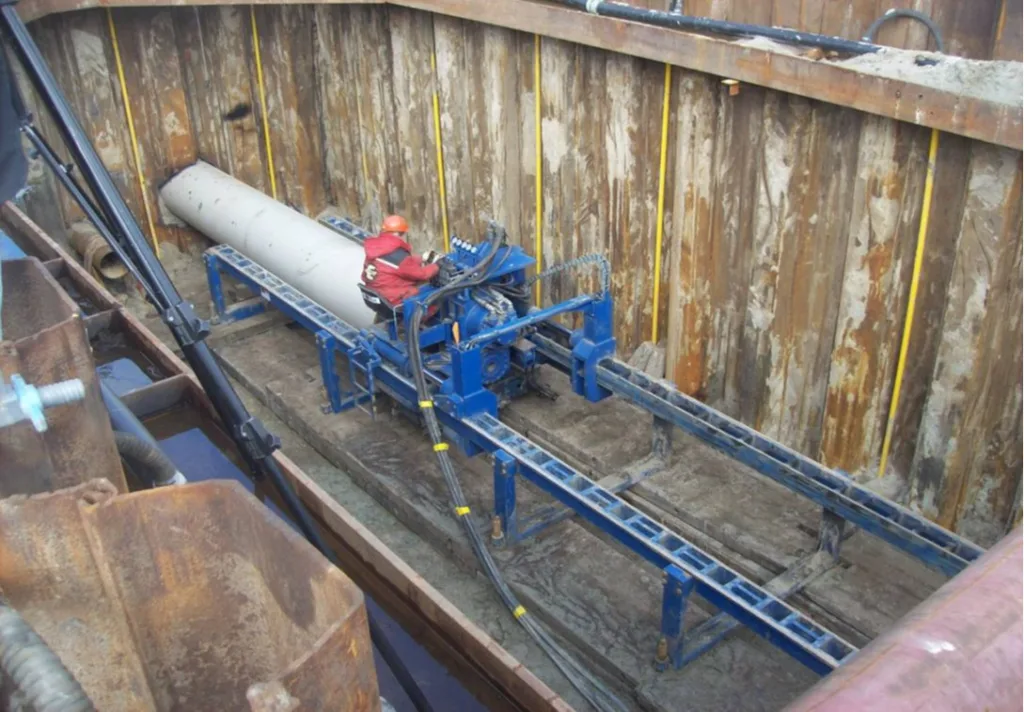
Slurry Shield equipment: Tailored for challenging ground conditions, slurry shield equipments utilize a slurry mixture to stabilize the tunnel face while simultaneously excavating material. The slurry serves a dual purpose by supporting the tunnel face and facilitating the transport of excavated material to the surface. This type of microtunneling machine is particularly effective in areas with unstable or waterlogged soil, providing stability and preventing ground collapse during excavation.

Earth Pressure Balance equipment: Essential for maintaining stability during tunneling, earth pressure balance equipment control the pressure of excavated material to balance the surrounding earth pressure. By adjusting the pressure within the tunnel, these equipments prevent ground settlement and ensure the integrity of the surrounding soil. This makes them well-suited for projects where ground conditions require careful management to avoid subsidence.

Why microtunneling is used in India?
The demand for microtunneling in India is intricately tied to the rapid urbanization and infrastructure development occurring across the country. As cities grow, there’s an increased need for the expansion and maintenance of utility networks such as water supply, sewage, and telecommunication. It is being used in India is due to;
1. Minimal Surface Disruption: In densely populated urban areas, traditional open-cut methods can be highly disruptive. Micro-tunneling allows for underground construction without significant disturbance to the surface, reducing inconvenience to residents and minimising traffic disruptions.
2. Speed and Efficiency: Micro-tunneling often results in faster project completion compared to traditional methods. This efficiency is crucial in urban settings where timely completion of projects is essential to meet the increasing demands of a growing population.
3. Challenging Terrains: India’s diverse topography presents challenges for conventional construction methods. Micro-tunneling is versatile and can navigate through different soil types, terrains, and geological conditions, making it suitable for a wide range of locations.
4. Capacity for Various Utilities: Micro-tunneling is used for various purposes, including the installation of pipelines, conduits, and cables. This versatility makes it a preferred choice for addressing multiple infrastructure needs concurrently.
Conclusion
Microtunneling stands as a transformative method in underground construction, offering a precise and efficient method for excavating tunnels with minimal surface disruption. As cities expand and infrastructure demands escalate, microtunneling stands as a key equipment, promising not only streamlined construction processes but also contributing to the creation of resilient and eco-friendly urban environments. The continued integration and advancement of microtunneling technology hold great promise for the future of subterranean infrastructure development.
References- terratec.com, gypsum.in, volza.com, robbinstbm.com, herrenknecht.com,