Concrete spalling is a phenomenon where the surface layers of concrete deteriorate, resulting in the detachment, flaking, or chipping of the concrete. It is characterised by the loss of concrete material from the surface, which can range from small fragments to larger sections. Buildings, bridges, parking lots, industrial compounds, all of these structures and more are vulnerable to concrete spalling, exposing the aggregate underneath while leaving the surface of the concrete jagged and patchy.It can weaken the concrete structure, compromise its durability, and potentially lead to further damage if left unaddressed.
Causes of concrete spalling
Spalling is commonly caused by a combination of factors, including:
- Poor concrete mix design
- Insufficient curing
- Freeze-thaw cycles
- Corrosion of reinforcement:
- Chemical exposure
- Carbonation
- Impact or excessive loading
- Alkali-silica reaction
- Structural movement or settlement
- Construction defects
Signs of concrete spalling
Signs of concrete spalling are typically visible on the surface of the concrete and can vary in severity. Here are some common signs that indicate concrete spalling:
- Flaking or Chipping
- Cracking
- Exposed Aggregate:
- Discoloration
- Deterioration of Surface Coatings
- Pitting or Pockmarks
- Hollow or Loose Sounding Areas
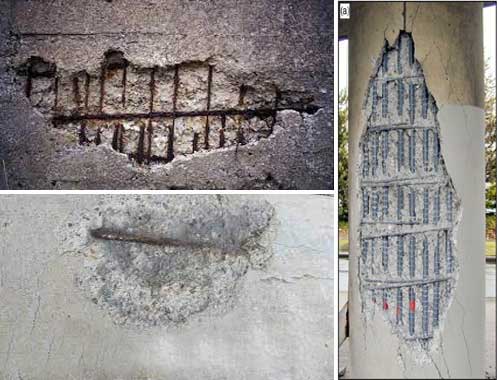
Effects of concrete spalling
The effects of concrete spalling can be significant and have several implications:
1. Structural Integrity: Spalling can compromise the structural integrity of concrete elements. When the outer layers of concrete start to peel off, it exposes the underlying reinforcement bars (rebar) to moisture, which can lead to corrosion.
2. Durability and Longevity: Spalling accelerates the deterioration process of concrete structures. Once the outer protective layer is compromised, the underlying concrete becomes more vulnerable to further damage from environmental factors.
3. Water Ingress and Moisture Problems: Spalled concrete allows water and moisture to penetrate deeper into the concrete structure, exacerbating the deterioration. Moisture ingress can lead to the corrosion of reinforcing steel, expansion and contraction due to freeze-thaw cycles, and the growth of mold or other harmful microorganisms.
4. Reduction in Strength and Load-Bearing Capacity: When concrete spalls, the loss of surface material can lead to a reduction in the overall strength and load-bearing capacity of the concrete, potentially compromising the stability of the structure.
5. Exposed Reinforcement: Spalling can expose the underlying reinforcement, such as steel rebars, to the elements. This can accelerate corrosion of the reinforcement due to moisture, oxygen, and other environmental factors.
6. Increased Vulnerability to Deterioration: Spalled areas create openings and pathways for water, chemicals, and other corrosive agents to penetrate deeper into the concrete. This increases the likelihood of further deterioration, such as freeze-thaw damage, chemical attack, and carbonation.
7. Aesthetics and Surface Damage: Concrete spalling results in the loss of concrete surface layers, leaving behind an unsightly appearance. This can impact the aesthetics of the structure, especially in architectural applications. Additionally, spalling can lead to surface roughness, unevenness, and the formation of cracks, further compromising the visual appeal and functionality of the concrete surface.
8. Safety Risks: Spalling concrete poses safety risks to occupants, pedestrians, and users of the structure. Falling concrete fragments can cause injuries or property damage. Moreover, structural instability resulting from spalling may lead to structural failures and collapse in severe cases.
Concrete spalling repair
The repair method for concrete spalling depends on the extent of the damage and the underlying cause. Here are some common techniques used to repair concrete spalling:
1. Surface Patching: Surface patching is suitable for minor spalling where only the outer layer of the concrete is affected. The damaged area is cleaned, and a patching material, such as polymer-modified cementitious repair mortar, is applied to restore the surface. The patching material is levelled and finished to match the surrounding concrete.
2. Full-Depth Repair: Full-depth repair is necessary for more extensive spalling that affects the underlying layers of concrete and may involve reinforcement. The damaged concrete is removed, and the area is prepared by cleaning and roughening the surface. A repair mortar or concrete mix with appropriate strength and properties is then placed and compacted to restore the full depth of the repair area.
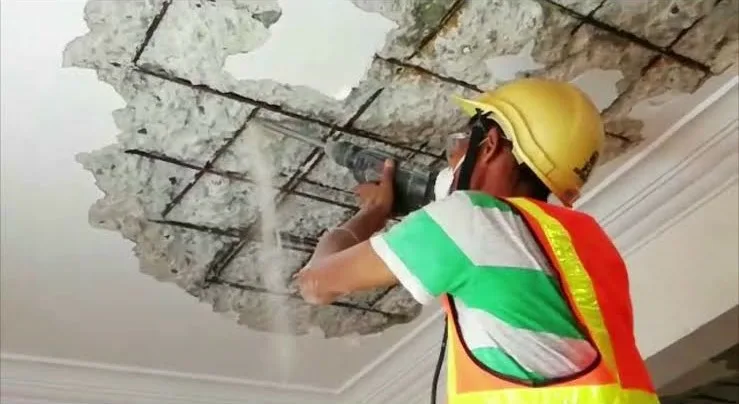
When it comes to repairing concrete spalling, there are different application methods depending on the extent of the damage and the specific repair materials being used. Here is a general overview of the repair application process:
1. Surface Preparation:
- Thoroughly clean the damaged area by removing loose debris, dirt, and any deteriorated concrete. Use a wire brush, chisel, or other suitable tools to clean and prepare the surface.
- If necessary, use a pressure washer or appropriate cleaning agents to remove contaminants such as oil, grease, or chemicals that may hinder the bonding of the repair material.
2. Repair Material Selection:
- Choose a repair material that is suitable for the type and severity of the spalling, as well as compatible with the existing concrete. Options include polymer-modified cementitious repair mortars, epoxy-based compounds, or specialized repair products.
- Follow the manufacturer’s recommendations for the selected repair material, including mixing ratios, application instructions, and safety precautions.
3. Mixing the Repair Material:
- Prepare the repair material according to the manufacturer’s instructions. This typically involves combining the repair material with water or other specified additives to achieve the desired consistency.
- Mix the material thoroughly using a drill with a mixing paddle or other appropriate mixing equipment until it reaches a uniform, lump-free consistency.
4. Application:
- Apply a bonding agent or primer to the prepared surface if recommended by the manufacturer. This helps improve the adhesion between the existing concrete and the repair material.
- Use a trowel or a suitable tool to apply the repair material to the spalled area. Fill the voids, cracks, or damaged sections, ensuring that the repair material is compacted and fully contacts the existing concrete.
- For larger repairs or deeper voids, it may be necessary to apply the repair material in layers, allowing each layer to cure before applying the next.
- Smooth and level the surface of the repair material to match the surrounding concrete, ensuring a uniform and aesthetically pleasing finish.
5. Curing and Protection:
- Follow the manufacturer’s recommendations for curing the repair material. This may involve covering the repaired area with plastic sheeting, applying curing compounds, or moist curing.
- Protect the repaired area from traffic, excessive moisture, and other potential sources of damage during the curing process. Allow sufficient curing time for the repair material to achieve its specified strength and durability.
It’s important to note that the specific application method and techniques can vary based on the repair material and manufacturer’s instructions.
Tips for prevention of concrete spalling
You can avoid concrete by following few preventive measures;
- Ensure proper proportions of cement, aggregate, and water to achieve a strong and durable concrete.
- Follow appropriate curing methods to promote hydration and strength development, reducing the likelihood of spalling.
- Utilize air-entrained concrete or add chemical admixtures to improve the concrete’s resistance to freeze-thaw cycles.
- Use corrosion-resistant materials for reinforcement, such as stainless steel or epoxy-coated rebar, to prevent reinforcement corrosion and subsequent spalling.
- Apply suitable surface coatings or use chemical-resistant concrete mixes in areas prone to chemical attack.
- Avoid carbonation by using low permeability concrete or applying protective coatings to maintain alkalinity and prevent spalling.
- Use reinforced concrete, fiber reinforcement, or protective coatings in areas subject to heavy impacts or excessive loads.
- Avoid reactive aggregates prone to alkali-silica reaction and use non-reactive aggregates instead.
- Implement good construction practices, including proper compaction, adequate finishing, and attention to details, to prevent construction defects that can contribute to spalling.
- Ensure that the water-cement ratio in the concrete mix is within the recommended range.
- Ensure that the reinforcing steel is adequately covered with concrete to protect it from moisture, chlorides, and other corrosive elements.
Conclusion
The consequences of concrete spalling can be severe, compromising the structural stability and safety of buildings, bridges, and other concrete structures. It is crucial to address spalling promptly to prevent further deterioration and potential structural failure. Regular inspections, maintenance, and repairs are essential for mitigating the effects of spalling and ensuring the longevity of concrete structures.