GGBS (Ground Granulated Blast-furnace Slag) is a by-product of iron manufacturing which is used as a cementitious material used in concrete. GGBS is obtained by the heating of iron ore, limestone and coke at a temperature about 15000C. The process is carried out in a blast furnace. It is obtained by quenching molten iron slag from a blast furnace in water or steam, then dried and ground into a fine powder. GGBS can be used as a partial replacement of OPC cement in concrete production at batching plants. It is highly cementitious and high in calcium silicate hydrates (CSH) which is a strength enhancing compound which improves the strength, durability and appearance of the concrete. Its manufacturing requires less energy and produces less CO2 emissions compared to Portland Cement production. When added to concrete, it acts as a stabilising agent and improves the quality of concrete.
The main constituents of GGBS are Cao, SiO2, Al2O3 and MgO. The chemical composition of a slag varies considerably depending on the composition of the raw materials in the iron production process. Silicate and aluminate impurities from the ore and coke are combined in the blast furnace with a flux which lowers the viscosity of the slag. GGBS cement can be added to concrete in the concrete manufacturer’s batching plant, along with Portland cement, aggregates and water. The normal ratios of aggregates and water to cementitious material in the mix remain unchanged.
Advantages of GGBS
Concrete containing GGBS cement has a higher ultimate strength than concrete made with Portland cement. It has a higher proportion of the strength-enhancing calcium silicate hydrates (CSH) than concrete made with Portland cement only, and a reduced content of free lime, which does not contribute to concrete strength. Concrete made with GGBS continues to gain strength over time Its advantages includes;
- Increases the strength and durability of the concrete structure
- Better workability, making placing and compaction easier
- Reduces the risk of thermal cracking in large pouring
- Reduced shrinkage cracks
- It reduces voids and permeability in concrete
- Provides a workable mix
- Higher flexural strength
- Contains good pumpable and compaction characteristics
- Comes with increasing sulphate attack resistance
- High resistance to chloride ingress
- The heat of hydration is less compared to conventional mix hydration
- The alkali-silica reaction is resisted highly
- Gives good surface finish and improves aesthetics
- Considerable sustainability benefits
- Gradual hydration of GGBS generates both lower peak and less total overall heat
- Does not produce carbon dioxide, sulphur dioxide or nitrogen oxides
Applications of GGBS
GGBS is used to make durable concrete structures in combination with ordinary portland cement and/or other pozzolanic materials. It is used to make durable concrete structures in combination with ordinary Portland cement and/or other pozzolanic materials. Major uses of GGBS are in the production of quality-improved slag cement and in the production of ready-mixed or site-batched durable concrete. Concrete made with GGBS cement sets more slowly than concrete made with ordinary Portland cement and continues to gain strength over a longer period in production conditions.
It can be used in;
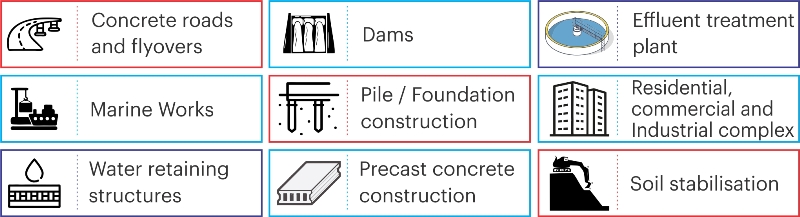
Conclusion
Given above are different advantages and applications of GGBS. These particles have a very glassy texture that makes them increase the workability. This can help in reduction of water as well as Superplasticizers to get adequate workability in common situations. They also have fewer chances to get segregated during handling as well as pumping of the material. More insights on physical properties and chemical composition will be given in an upcoming series of articles.