The trenchless construction methods can be used for the new installation or restoration of existing underground piping infrastructure with minimal disturbance to surface traffic. The method comprises techniques, materials and equipment used for the installation of pipelines and cables below the ground with minimal excavation. With the trenchless method, a shaft only needs to be dug at the start and end of the section of the pipeline. Intersecting roads, rail tracks, rivers and construction sites are virtually unaffected by the work and there is no need to divert traffic, which can be complex and costly.
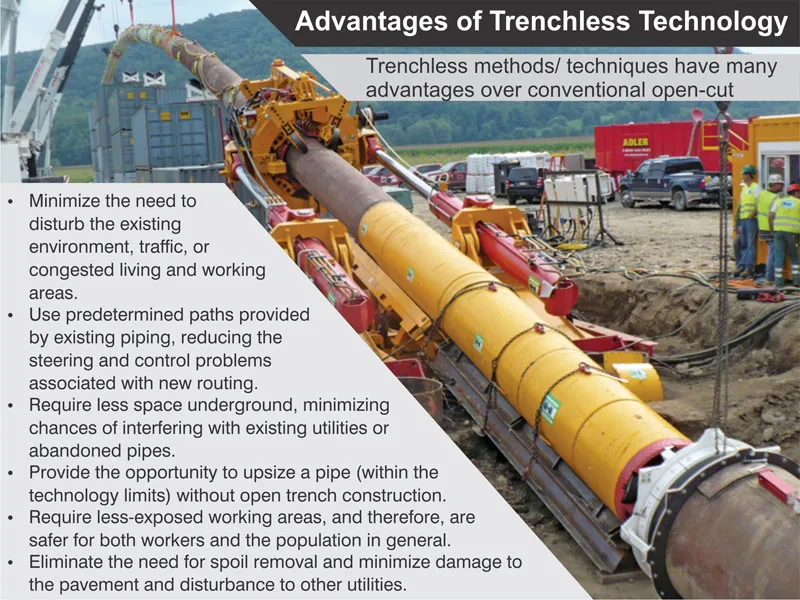
Given below are the different trenchless methods used for the new installation & restoration of underground piping.
Trenchless methods for new installation of underground piping
Horizontal directional drilling
Horizontal directional drilling (HDD) is a trenchless construction method used to install pipelines of various sizes and materials below the ground surface. HDD allows the entire water supply and drainage system of a city to be replaced without causing a major traffic jam and incurring the enormous cost of restoring streets and roads. It involves the use of a directional drilling machine, and associated attachments, to accurately drill along the chosen bore path and back ream the required pipe. It has become a choice alternative to conventional pipe-laying methods that require opening up the earth’s surface up to the depth of installation for the entire pipeline route.
The horizontal directional drilling method involves three stages. The first stage consists of drilling a small diameter pilot hole. Drilling fluid is pumped through the drill pipe to the drill bit where high-pressure jets and the bit will grind the soils ahead of the drill stem. The drilling fluid will also carry the cuttings back to the entrance pit at the drill rig. The second stage is to pre-ream the pilot hole and enlarge it to a size sufficient to safely install the product lines. A reamer is pulled back and rotated while pumping drilling fluid to cut and remove solids to enlarge the hole. Pre-reaming speeds will vary depending on existing soil conditions and the amount of cuttings that are removed from the hole. The final stage is the pullback of the pipe within the pre-reamed hole. The drill rod and reamer will be attached to a swivel, which is utilized between the product line and the reamer to prevent any torsional stress from the rotating drill string being transferred to the product pipe. Horizontal directional drilling is ideal for use where trenching needs to be avoided such as under a railroad, an embankment, highway, and beneath lakes and rivers.
Auger boring
Auger boring is the process of forming a horizontal bore by jacking the steel casing through the earth from the main shaft to a reception shaft. Spoil is removed from inside the encasement using a rotating auger. The rotating augers carry the spoil back through the casing pipe to the main shaft for removal. Auger boring employs a cutting edge attached to the auger within the casing pipe and hydraulic jacks, to rotate and penetrate the soil. So that there is unimpeded rotation within the casing, the auger diameter tends to be slightly less than that of the casing pipe.
An auger boring machine bores through soil or rock with a cutting head attached to the ‘lead’ auger to install a steel casing pipe. These machines are used for the successful installation of sewage ducts and pipelines and crossings beneath infrastructures. The boring machines offered by Herrenknecht in cooperation with Bohrtec GmbH stand out in comparison to conventional construction methods due to their technical, economic and ecological advantages. Their main range of applications is underground pipe jacking.
Impact Moling
Impact Moling is used for the installation of pipes up to 160mm in diameter over distances up to 60metres. It is one of the most widely used trenchless installation methods used for the installation of small diameter pipes or cables using a pneumatic hammering tool. It is carried out at a depth of at least 10 times the diameter of the product pipe or 1 meter, whichever is greater, to avoid surface damage. Impact Moles come in all sizes, from 25mm diameters up to around 63mm in diameter.
Impact moles typically involve the excavation of two pits: a launch pit and a reception pit. After the careful alignment of the mole in the insertion pit, the tool is expected to advance through the ground in a straight line. A single person can operate the mole. The impact mole is positioned on a skid or cradle at the desired line and level determined by a sighting level positioned on the mole. Once the mole is in the desired position, the compressor is activated advancing the mole through the hammering action of the reciprocating head.
Microtunneling
Microtunneling is a trenchless method that combines a remote-controlled, steerable boring machine with a pipe jacking feature used to install product pipelines underneath the ground in a single pass. The microtunneling boring machine (MTBM) is operated from a control panel, normally located on the surface. There is continuous pressure exerted at the excavation point to balance earth and groundwater pressure. An operator controls the microtunneling boring machine remotely. Due to the small size of the bore and the installation process, personnel cannot enter the area. This means the control panel and operator remain on the surface during the procedure. This trenchless machine uses either vacuum soil removal, slurry or augers to install the new lines. They are mounted on a jacking frame which is moved forward using jacks. The automatic steering system enables pipes of diameters ranging from 48 inches to 12 feet to be installed accurately. The automated steering system used for guiding the MTBM during the boring procedure gives very accurate results for curved and long-distance drives. As the machine drills the hole, a jacking rig functions like a jackhammer to push the new sewer pipe in place between the boring machine and the jacking rig.
Micro tunneling is used for the installation of large diameter deep gravity sewers in cities where open-cut installation is not an option owing to existing surface establishments, installation of product pipelines in areas where soil condition is such that an HDD bore cannot be stabilized and long crossings across rivers.
Pilot-Tube Microtunneling (PTMT)
Pilot-Tube Microtunneling (PTMT) is an alternative to conventional microtunneling. It combines the accuracy of micro tunneling, the steering mechanism of a directional drill, and the spoil removal system of an auger boring machine. Pilot tube microtunneling is a multistage method which includes pilot tube boring. This method allows for accurately installing a product pipe to line and grade by use of a guided pilot tube, followed by upsizing to install the product pipe.
Pilot-Tube Microtunneling (PTMT) employs an auger and a guidance system, using camera-mounted theodolite and target with electric light-emitting diodes (LEDs) to secure high accuracy in line and grade. When conditions are favorable, PTMT can be a cost-effective tool for the installation of small-diameter pipes of sewer lines or water lines. This technique can also be used for house connections, direct from the main-line sewers.
Pipe ramming
Pipe ramming involves the use of the dynamic force and energy transmitted by a percussion hammer attached to the end of a pipe. The basic procedure generally comprises ramming a steel pipe through the soil by using an air compressor. Pipe ramming permits the installation of large steel castings in a wide range of soil conditions. It provides continuous casing support during the drive with no over-excavation, and it does not require the jetting action of water or the use of drilling fluids.
The pipe ramming equipment is aligned in the insertion pit in the direction that the pipe is to be installed. Insertion pits may not be required for embankments and slopes as the ram can be designed to start at the side of the slope. Thrust plates are not required for pipe ramming but guide rails are recommended to maintain the grade. There are two types of pipes used in the ramming process: closed-end and open-end pipes. The open-ended pipe is generally preferred as the ramming force required to drive the pipe is less. This reduces the chances of heaving and pipe deflection.
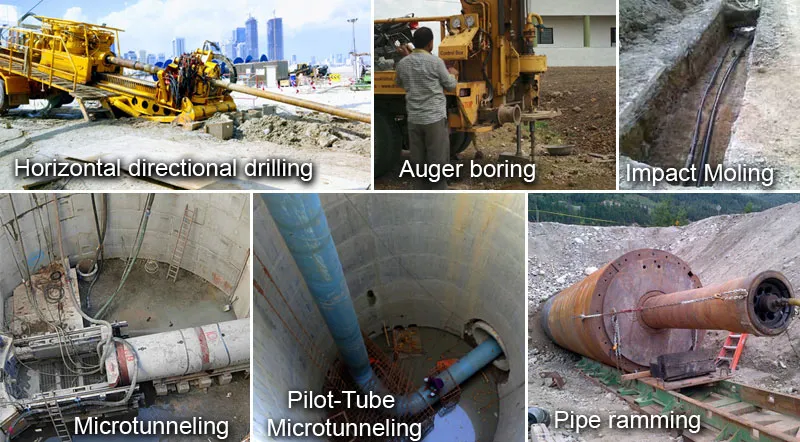
Trenchless methods for restoration of underground piping
Pipe bursting
Pipe bursting is a trenchless method used to replace existing pipelines with the same alignment without physically removing the existing pipeline. Pipe bursting eliminates the need for digging large trenches. Instead, workers dig a series of launching and receiving pits through which the replacement pipe is installed. As the new pipe is laid in place, a tube-bursting tool destroys the old lines. The device is retrieved from the receiving pit and used again on the next section of piping. There are four different means of pipe bursting including lateral, pneumatic, hydraulic, and static pipe bursting. The equipment used in pipe bursting and splitting is the burster/splitter head, an expander which may be incorporated into the burster/splitter head, pulling rods, a rod puller or winch and a hydraulic power pack.
A conical bursting head is fixed to a replacement pipeline, and fed through an entry hole to the broken sewer line. The pointed bursting head breaks the existing, damaged pipeline as it travels through; this is because the bursting head’s cone shape is larger at its base than the existing pipe’s diameter. Using a pull rod or hydraulic power, the entire existing pipe is fractured and pushed from its original location. The replacement pipe, attached behind the bursting head, is then seamlessly fed in place, filling the cavity left behind by the bursting head.
Pipe eating
Pipe eating is a replacement process similar to pipe jacking, where powerful hydraulic jacks force a pipeline into a bore as the bore is created. In this method, a non-man-accessible sewer or pipeline is run down using an unmanned pipe jacking technique, destroyed and removed, and at the same time, the new sewer or pipeline with the same or larger nominal size is laid in the same pipe course.
Localized Repairs
When local defects are found in a structurally sound pipeline, localized repairs are considered. Systems are available for remote-controlled resin injection to seal localized defects in pipes ranging from 4 to 24 in. in diameter. The localised repair methods are generally used to address four basic problems. The first involves maintaining the loose and separated pieces of unreinforced existing pipe aligned to ensure the load-bearing equivalent of a masonry arch. The second is to provide added localized structural capacity or support to assist the damaged pipes to sustain structural loads. The third provides a seal against infiltration and exfiltration. Finally, the fourth is to replace missing pipe sections.
Trenchless pipe relining
Trenchless pipe relining method is used for repairing existing underground pipelines by inserting a relatively small diameter pipe or by spraying coating material into the damaged pipe to create a lining within the pipe, with very limited or no excavation. The key features of these techniques are that the pipe relining has become faster, easier, cheaper, and cleaner. In addition, they avoid traffic jams, destruction of landscape, and other environmental impacts.
Before the relining process is started, the affected pipe is inspected and cleaned of debris. Once cleaning is completed, the necessary length of the liner is cut for insertion. The relining process uses a lining material of polyester felt coated with PVC. This liner is saturated with an epoxy resin and a hardening agent. The felt tube is then inserted into the pipe using water or compressed air, bringing the resin-coated side towards the inner side of the pipe. The tube is expanded until it fits into the pipe and left to cure or harden into the old pipe. These liners are strong and last for a very long time (at least 50 years) which makes the process cost-effective.
Sliplining
Sliplining is done by installing a smaller, carrier pipe into a larger host pipe, grouting the annular space between the two pipes, and sealing the ends. The trenchless method is generally a cost-effective rehabilitation method to replace water and sewer force mains. Methods of sliplining include continuous, segmental and spiral wounds. All three methods require laterals to be re-connected by excavation or by a remote-cutter. In continuous slip lining, the new pipe, joined to form a continuous segment, is inserted into the host pipe at strategic locations. The installation access point, such as a manhole or insertion pit, must be able to handle the bending of the continuous pipe section. The sliplining method uses HDPE pipe that is fused into long lengths before installation. The HDPE pipe is pulled through the existing host pipe starting at an insertion pit and continuing to a receiving pit.
Cured-in-place pipe (CIPP)
The cured-in-place pipe (CIPP) method enables sewer pipelines to be repaired from within by insertion of a lining material through existing manholes or other entry points. The liner is composed of a fabric reconstruction tube that is impregnated with a thermosetting resin that hardens into a structurally sound jointless pipe when exposed to hot circulating water or steam. The fabric tubes which are used by CIPP manufacturers vary by material type, coating type and method of construction. Most of the fabrics are made of woven or non-woven polyester. Other materials such as fiberglass are sometimes incorporated into the fabric as reinforcement.
Tubes are typically layered with at least one fabric layer and another layer that is impermeable to the flow of the liquid resin. Some systems utilize a removable inner tube that serves as a bladder between the liquid resin and the circulating water or air during installation. Fabric tubes are typically constructed to be the same size as or slightly smaller than the inner diameter of the pipe which is being rehabilitated. When pressure is applied for rounding, the saturated fabric stretches to conform to the inner surface of the pipe.
Hydro Excavation
Hydro excavation is a non-destructive and non-mechanical method that uses pressurized water and industrial strength vacuum to evacuate and excavate the soil simultaneously. As hydro excavation breaks up soil, the soil and waste are safely conveyed by vacuum into a debris tank. This method is usually preferred in cases where the soil is cohesive and undisturbed. Other than for sewer pipe restoration, this method can also be used to install poles, fences, potholing or daylighting; slot trenching, debris removal, exposing utilities, piling, etc. The main advantage of this method is that it does not harm any utilities that it may encounter while the process is being carried out because water is used as the cutting tool. Because the equipment is operated from a truck, it is considered a very versatile method that can be carried out anywhere.
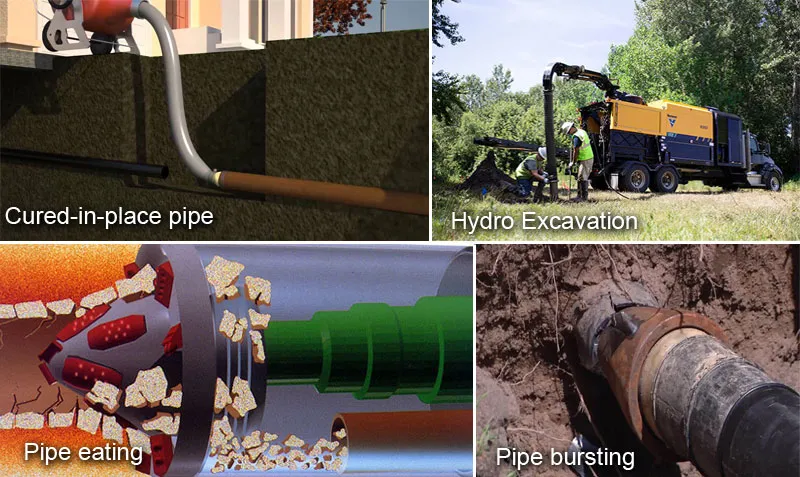
Conclusion
As for any trenchless construction involving newer installation and renewal projects, site-specific and successful completion of a trenchless project is dependent on many factors such as accuracy, maximum installation length, diameter range, and type of application. There are different types of trenchless methods available as discussed above, choose according to your project demand and take expert advice.