Concrete undergoes dynamic loading and rigorous environmental conditions. The development of shrinkage cracks in plain cement concrete is a major problem. To overcome this problem sometimes the addition of synthetic fiber to the concrete mix is beneficial. Synthetic Fiber Reinforced Concrete is increasingly being recognized as a favorable substitute for unsustainable inputs. These fibers are made from synthesized polymers of small molecules. The compounds that are used to make these fibers come from raw materials such as petroleum-based chemicals or petrochemicals. These materials are polymerized into a chemical that bonds two adjacent carbon atoms. Differing chemical compounds are used to produce different types of synthetic fibers. It accounts for about half of all fiber usage, with applications in every field of fiber and textile technology.
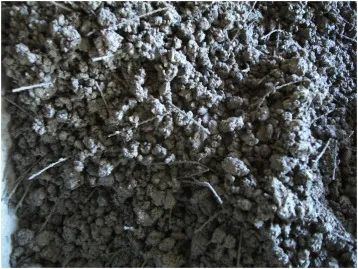
Advantages of Synthetic Fiber Reinforced Concrete
Synthetic Fiber Reinforced Concrete Fiber are more durable than most natural fibers and will readily pick-up different dyes. Also, many synthetic fibers offer consumer-friendly functions such as stretching, waterproofing and stain resistance. Sunlight, moisture, and oils from human skin cause all fibers to break down and wear away. Natural fibers tend to be much more sensitive than synthetic blends. This is mainly because natural products are biodegradable. Natural fibers are susceptible to larval insect infestation; synthetic fibers are not a good food source for fabric-damaging insects. Compared to natural fibers, many synthetic fibers are more water-resistant and stain-resistant. Some of its advantages are;
- Controls and mitigates plastic shrinkage cracking
- Reduces segregation and bleed-water
- Provides three-dimensional reinforcement against micro-cracking
- Increases surface durability
- Reduction of in-place cost versus wire mesh for temperature/shrinkage crack control
- Easily added to concrete mixture at any time before mixing
- Increased durability due to Increased strength of mortar
- No Dampness and leakage
- Improves the abrasion resistance of concrete floors to moving loads.
- Improved impact resistance of floors to point loads
Different types of Synthetic Fiber Reinforced Concrete and its applications
Various types of fibers that have been tried in concrete include acrylic, aramid, carbon, nylon, polyester, polyethylene and polypropylene. Typically they are categorized as Micro and Macro Synthetic Fiber Reinforced Concrete.
Micro Synthetic Fiber Reinforced Concrete
Micro fiber concrete with polypropylene fibers are mainly used to reduce plastic shrinkage in fresh concrete. During the hardening process of concrete, dissipation of heat of hydration of concrete coupled with evaporation of water induces tensile stresses. Beyond a threshold limit of these stresses, micro cracks start developing in the concrete. Micro fiber concrete with polypropylene fibers reduces effective the early shrinkage behavior in the first 10 hours of pouring. The reason is that these types of fibers are able to hold back some water and slow down the evaporation process. They also are able to pick up some limited tensile stresses especially in the early age. These types of fibers work better to reduce plastic shrinkage cracks and are often added in addition to the reinforcement of concrete.

Another application of these fibres lies in improving the fire resistance behaviour of concrete structures at very high temperatures. Concrete as such in itself is a good fire resistant material.Addition of micro fibres in the concrete ensures that as these fibres melt, they create open channels in the concrete pore structure which allows the built up vapours to escape, thereby releasing the internal pressures and preventing the spalling.
Macro Synthetic Fiber Reinforced Concrete
Macro fiber concrete with polypropylene fibers are mainly used in lightly loaded applications where the concrete behavior is calculated as un-cracked concrete just to improve the concrete in terms of their crack behavior and to improve the resistance against the thermal shrinkage process.
The reason that these fibers are mainly used in lightly loaded structures is that in the case of heavily loaded structures, these fibers tend to creep and hence a design in the cracked state under long term loadings does not save the structure in the event of a failure. Macro synthetic fibers do not corrode. Hence in case of macro fibers, no rusty spots appear at the surface. Additionally macro synthetic fibers can be effectively used in applications like temporary linings such as for mines when larger deformations are allowed.
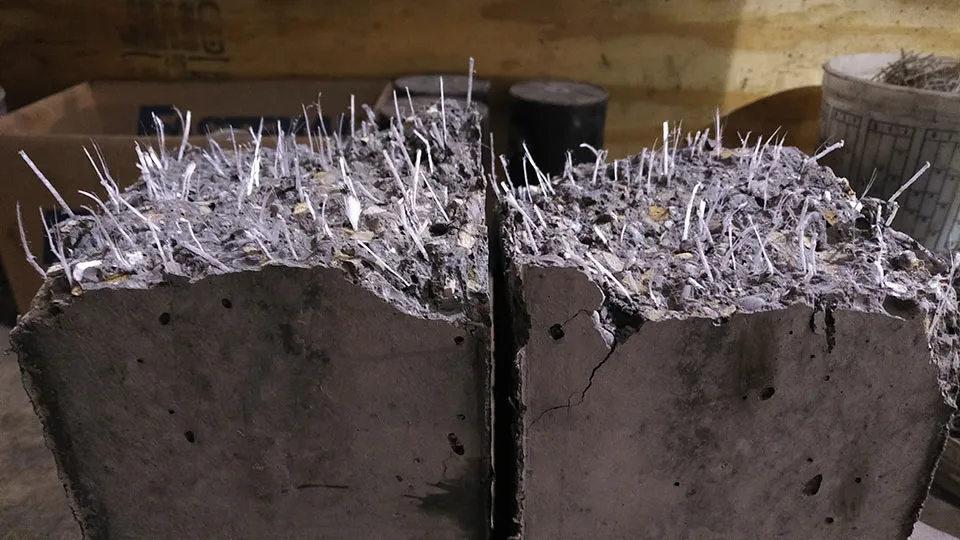
Application of Synthetic Fiber Reinforced Concrete
- Floor for industrial, commercial and residential concrete projects
- Footings, foundations, walls and tank applications
- Concrete pipe, vault structures and precast / prestressed beams, PQC Roads, Parking Area, Pavers,
- Tunnels, Canals & All kinds of Plastering Application.
Conclusion
Synthetic Fiber Reinforced Concrete has been rapidly growing throughout the building industry since contractors and homeowners started to recognize its many benefits. It is gaining an increasing interest among the concrete community for the reduced construction time and labor costs. Besides cost issues, quality matters are of paramount importance for construction and Synthetic Fiber Reinforced Concrete also fulfills these requirements.
Image Source: researchgate.net, sciencedirect.com, bajajreinforcementsllp.in, tunneltalk.com