Traditionally, saw cut grade slabs have been predominantly used for industrial flooring applications. However, with the recent advances in flooring reinforcement and construction technologies, it has become possible to completely eliminate saw cuts from flooring and achieve a floor with minimal joints. One of the best approaches to floor construction without any saw-cut and expansion joints is by the way of construction of seamless floors.
Seamless Floors are floor systems where the entire floor area (irrespective of the floor plate size and length: width aspect ratio) are finished without any saw-cut or expansion joints whatsoever. These floor systems are reinforced typically with a top rebar mesh in combination with high tensile strength Dramix® 4D steel fibres and are designed for a particular crack-width (typically ≤ 0.2 mm) imperceptible to the human eye and operationally superior to jointed floors. These floors find preference with oil and chemical industries, pharmaceuticals and food processing industries where liquid tightness, resistance to bacterial and fungal growth and general cleanliness of the floor is highly desired.
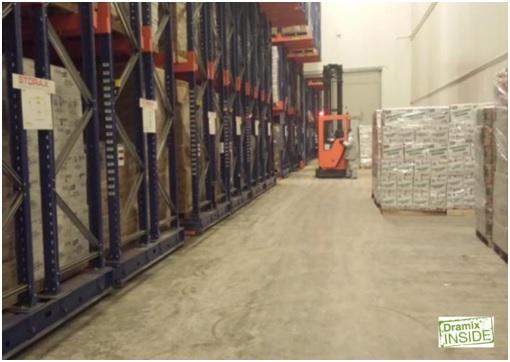
Nature of Applications
Seamless floors cater to a wide variety of industrial applications. They are definitely preferable in a heavy duty industrial environment where there is a lot of forklift movement, where there is a certain amount of flatness requirement that needs to be maintained (as more discontinuities in the form of saw cuts hamper the floor flatness), in heavily loaded areas where the possibility of wear and tear for floors is high, and also in floors where a certain degree of hygiene needs to be maintained. For such applications listed above, saw cut floors have been found to be prone to maintenance problems. These issues extend not only to floors (repeated repair of joint spalls, filling of joints, grinding etc) but also the equipment used on them (such as forklifts, cranes etc.). These have often been known to affect the productivity of the manufacturing processes on the floor.
Advantages
A key factor in a quality floor is its ability to withstand wear and tear over time and to contribute and be a part of the high productivity manufacturing chain in an industrial environment. The following are some of the detailed reasons why seamless floors are preferable over saw cut floors:-
- Less joints means low maintenance cost
Typical saw cut joints are filled with sealants which tend to get worn out over time. Furthermore, continuous movement of forklift and other trucks over these joints leads to chipping and spalling failures along the joints which are detrimental to the long term performance of the overall floor. Refer to Figure 2 for more details regarding this issue.

- Consequently, this has a positive effect on the following other aspects indirectly:-
- There is less maintenance on the forklift trucks, tyres and other equipment in the factory
- There is higher driving speeds for forklift trucks available
- Ergonomic advantages in terms of operator easy of working and reduced
complaints. - Higher output on the shop floor
- Slab aesthetics
This is another important aspect of floor construction which is also linked to the overall manufacturing process and life cycle cost of the project. Absence of pattern joints at small regular intervals allows for flooring contractors to lay large areas of concrete unhindered by regular formwork (see Figure 3). This has an immediate advantage in that the unevenness across smaller panels gets eliminated which allows for a flatter floor to be laid (Figure 4). Thus, operationally, such a floor becomes more desirable as this has the least number of joints which aids in the overall process.
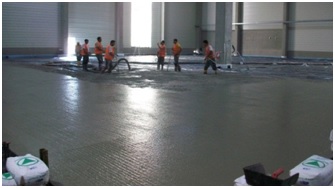
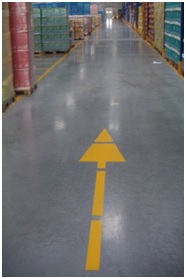
Construction
Seamless floors do not need a high degree of pre planning because the floor panels can be cast in any size and shape. No saw-cutting is to be done for these floors as they are designed for a crack-width requirement (typically ≤ 0. 2 mm). At this limit, the floors are water tight and better performing. Typical section consists of a single or double layer of reinforcement bars/ welded wire mesh along with a healthy dosage of high performance Dramix® 4D steel fibres.
At the construction joint locations, as there are no fibres to bridge the sections, typically the reinforcements are continued across the joint, and the adjoining section at the construction joint is held together by means of additional tie reinforcement provided in such a manner as to meet the same crack-width requirement as the main floor itself (≤ 0. 2 mm). This way, the entire floor is designed as a single tied seamless floor unit without any control joints or expansion joints. Ass the shrinkage movements are handled by the respective small cracks that the floor has been designed for.
Article contributed by
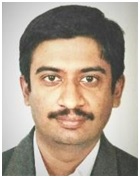
Navneet T. Narayan, Technical Manager, Building Products, Bekaert