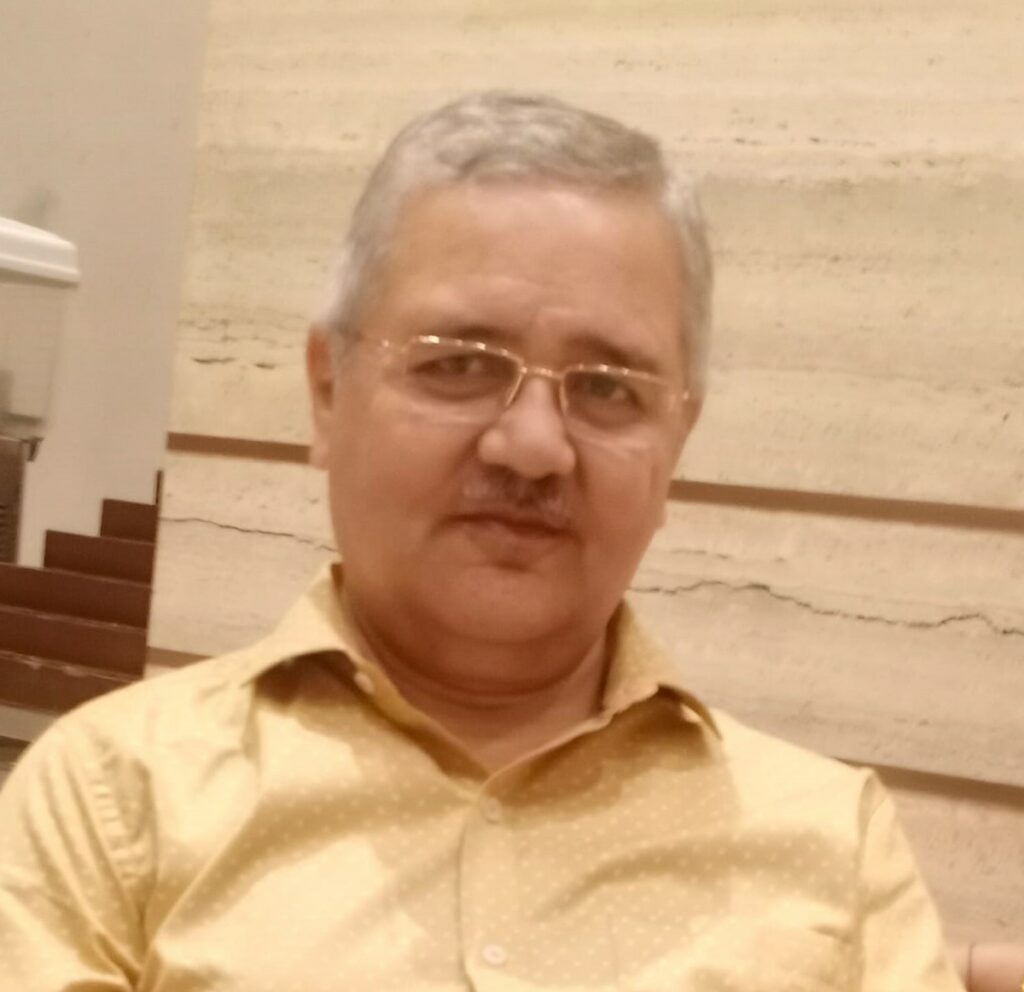
High RPM machines like turbine, rotor, ID / FD fan, compressor etc are mounted on a strong foundation with necessarily strong anchorage. However at times, they are observed to be generating high and unprecedented vibration on their specific body parts which are permissible only within their stringent allowable limit for safe operation of each individual machine. If this high vibration phenomena continues for a long time; it can become a bottleneck for safe and smooth operation of the machine and if they don’t stop within a stipulated time frame, the machine is forced to be operated at reduced load or even calls for its stoppage.
This is an uncalled-for situation for any production unit and all out efforts are deployed to restore the operations to their original capacity at the earliest.
Debottlenecking of this problem requires a root cause search for source of vibrations and then a systematic action plan to control these vibrations to bring them within their permissible limits.
The author of this paper have put in successful efforts in analysing many of such problems of bringing down the unprecedented vibrations to within permissible limits for restoring normal operation of the respective machine.
The paper discusses all about the problem and its details for the benefit of the machine and industries.
Introduction:
Any machine placed on the foundation has two elements. One is generating dynamic motion which is – the machine and another is its static counterpart – the foundation. A member which connects both of them is the anchor bolt which is a part of machine foundation and which is required to have high rigidity to tightly hold its dynamic counterpart for not allowing the dynamic movement to get transferred to any other part of the machine body. This is extremely important for safe operation of the machine operating with high RPM.
Reasons for vibrations for these machines:
There are many reasons due to which these machines generate unprecedented vibrations. Few of the most common reasons, which have been visually identified; are listed below.
- Mis-alignment of the shaft of the machine.
- Imbalanced level of operation of machine.
- Oversized or undersized shaft / pinion.
- Sudden stoppage of machine – missing post stoppage care.
- Change of service conditions like change of fluid handled by the machine, change in operating pressure / temperature etc.
- Change of upstream / downstream reaction.
- Electrical disturbances.
- Control signal disturbances.
- Foundation weakness.
While first 8 conditions are controlled by operation and maintenance crew with a focussed attention to resolve the problem, the last probable reason needs thorough deliberation because it fairly remains an ignored area.
Contribution from foundation for vibrations to the machine parts:
Functionally the foundation can be categorised in two major areas. The first is the top part of the foundation which is a grout – which tightly holds the foundation anchor bolts and another is the entire concrete mass which acts as a stem of the foundation to hold the foundation anchor bolts.
Different phenomena can occur with the foundation, especially from a foundation weakness point of view and which have been encountered during the actual problem solving process; are briefly mentioned below.
- Poor strength of concrete mass of the foundation.
- Deterioration of foundation concrete due to aggressive corrosive conditions around the foundation.
- Mechanical damage to the foundation concrete mass due to any dash or accident during operation of the machine.
- Inadequate or wrong structural design of the foundation or even adverse effects of change in operating conditions of the machine for which the foundation is not designed.
- Mismatch of load transfer and anchorage philosophy.
- Loss of anchorage of foundation anchor bolts with the foundation.
Mitigation measures for resolving these issues;
- Poor strength of core concrete of the foundation can be identified with respective NDT and can be augmented.
- Deteriorated concrete of the foundation can also be treated with suitable methodology under systematic structural rehabilitation drive.
- Mechanical damage to the foundation concrete is quite a visual defect which can be appropriately engineered to arrive at the loss of soundness parameter and can be suitably made up.
- Engineering analysis carried out with the applicable soft-wear for inadequately or wrongly designed foundations; can be an ideal tool to rectify the situation. Here one point which is always to be ensured is that matching the resonance of the machine with exact frequency with that of the concrete foundation is not a healthy symptom.
- Load transfer philosophy has to synchronise with the anchorage action. If sleeves are placed while concreting the foundation and anchor bolts are subsequently placed in the sleeves and subsequently aligned and grouted; then structural dynamics gets restricted to the sleeve volume. If the anchor bolts are erected / placed and aligned along with foundation concreting, then they become an integral part of the foundation and then the load transfer phenomena; aligns with anchorage action.
- With everything matching the design parameters, if the bond of anchor bolts with the concrete foundation is affected by any of the adverse conditions, then there is a quick loss of bond between anchor bolts and the concrete foundation which results in uncontrolled vibrations to the different body parts of the machine.
There are many reasons for getting the anchorage adversely affected as discussed now.
- The first option is mechanical damage to the anchor bolt during maintenance activity or some dash of heavy item with the footing of the machine.
- Another option is sudden thrust experienced by the machine affecting the direction of its rotation and transfer of that thrust can affect the anchorage action.
- One more reason is seepage of the debonding element between the bolt surface and foundation concrete.
- This is a very micro sized activity and requires less than a hairline space.
- Normally oil used for lubrication and other functional purposes, often spills over from the machine body or glands etc and spreads over the foundation.
- If that oil is not immediately removed from there and allowed to be there, it will travel towards the bolt location.
- Cementitious grout and concrete have poor resistance to oil.
- Oil then might react with the surface of cementitious grout or concrete and form a hairline cavity or recess with an adequate width (though in micron) to enter the cementitious grout or core concrete through the hairline space. Oil then travels along the metal surface of the bolt up to its full depth provided for anchoring function.
- Once this phenomena is established, then oil continues to seep within the core concrete and with more seepage of concrete, it widens and distance between the cementitious grout or core concrete and bolt surface from microns to millimetres.
- A photograph of this action is placed below.

It is clearly seen that the surface just adjoining to the surface of the bolt is having a small size recess. That space is good enough for oil to penetrate within that recess and de-bond the bolt from the grout.
This is found to be the significant root cause for such problems for high RPM machines and which remains fairly insignificant for the maintenance crew to identify. Hence when all machine parameters like alignment, shaft dimensions and trimming, flow parameters of fluid passing through the machine etc have been checked, rectified and are found OK and still if the vibrations hit the machine to restrict the functioning of machine to its full load, then oil leakage and seepage through and around the surface of foundation bolt/s must be carefully examined for presence of oil around their surface and for possibility of oil penetrating the foundation core through surface of foundation bolt/s.
Control measures for this condition:
There are few steps and actions which can mitigate vibrations due to this particular problem as have been experienced in many cases with their total successful solution by the authors of the paper are discussed below.
The first and ideal solution to this problem is to stop the machine, chip off the grouting around the foundation bolts and then to clean the bolt pocket to remove oil upto its last drop or trace with suitable means. Once the bolt pocket space becomes completely free of oil, then the bolts can be placed afresh in their desired alignment and level, followed by their grouting with the desired grout. If the machine was removed during its stoppage period, then the machine is to be replaced on the foundation after completion of specified period for curing the grout to establish its full parameters.


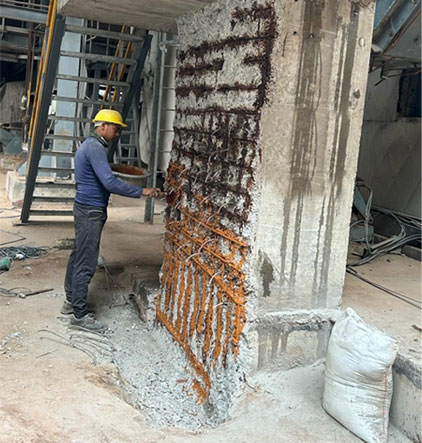
K K Retroflex Solution’s machine vibration control services for machine production units
Although this method is an ideal one and has bright chances of success, it involves stoppage of machines which directly contributes to production loss which is not desired for any production unit. Hence this method – though very sound and stubborn; is accepted as the last option for the rectification action plan.
Second method to mitigate the unprecedented vibrations; is to plug the micro crevice/s around the foundation bolts with suitable means. As it is not advisable to open out core concrete providing foundation to the machine, the only option for this action, is to carry out injection grouting over the top surface of the foundation and around the foundation bolts with the most appropriate material.
- Selection of grout material is to be made with precise care.
- It is required to be compatible with the medium in which it has to perform.
- It has to have required elastomeric properties to sustain thermal and other expansion / contraction phenomena.
- It has to have adequate strength to sustain the shock and thrust during operating the machine.
Hence selection of grouting material must be tailor made and case specific. Even the pressure at which injection is to be made is also required to be calculated with respect to the anticipated plugging process of crevice/s around the foundation bolts.
One more method which has significantly contributed to mitigate the vibrations is foundation treatment.
Foundation treatment can be decided only based on the structural analysis of the same and correlating it with resonance and frequency of the machine placed on it as explained in the earlier part of the paper. If the resonance of foundation and machine match with each other, then foundation falls under a weak zone requiring its strategic strengthening. Hence foundation treatment or strengthening action also have to be case specific which largely includes providing bracings at designed locations, providing jacketing around the foundation with steel or other designed material, strengthening the core concrete by suitable means etc.
Summary:
Vibration on those parts of an operating machine where they are not allowed has remained an eyesore for many machines and Industries. This requires a thorough inspection and careful study to identify its root cause and accordingly to arrive at the most appropriate solution for mitigating them on a permanent basis.
At times the root cause would be in the area which has remained ignored for long years but would have contributed to the unprecedented vibration. This has to be restricted, prevented and stopped with an engineering approach.
The facts placed above are the resultant of field experience of the authors of the paper which have resulted in ultimate success of mitigating the vibrations and bringing the machine operations to their full capacity for a prolonged period.
About the author;
Er. Chirag K. Baxi is the Director of Prudent Forensic Consultancy Private Limited and General Manager of K K Retroflex Solutions. He specializes in Corrosion Control Measures for concrete and steel surfaces, Damage assessment with the FORENSIC ENGINEERING approach and Structural rehabilitation of concrete and steel structures in the Industrial environment. He holds a degree in BE (Civil Engineering) and has completed MBA (Construction Management).
The author has invented CONCARE B 14 (which has been granted a patent) that makes concrete structures sustainable even with salty, saline, untreated or even seawater without deterioration in any of the end properties of constructed elements. He has written (two) drafts of IS Codes on the topic of “Carbon brick lining” and “PolyPropylene Glass lining” which are under the final stage of approval at BIS.
About 40 Technical papers on National and International platforms are authored, published and presented by the author. He has been recognized by several Institutes for his significant contribution to the Civil Engineering Industry.