Material processing equipments are used to transform raw materials into usable forms and components for construction projects.These equipments are used in various industries to process, transform, or modify raw materials or substances into finished products or components. These equipment are designed to perform specific tasks and processes related to material processing.
Uses of material processing equipments
Material processing equipment is used for a variety of reasons across different industries. Here are some key purposes of using material processing equipment:
1. Size Reduction: Material processing equipment is often used to reduce the size of raw materials or bulk solids. By breaking down large materials into smaller particles, it becomes easier to handle, transport, and store them.
2. Particle Size Control: In many applications, achieving a specific particle size distribution is essential. Material processing equipment allows for precise control over particle size, ensuring that the final product meets the desired specifications.
3. Mixing and Blending: Material processing equipment enables thorough mixing and blending of different components or materials. This is critical in industries where uniformity, homogeneity, or the creation of new materials is necessary.
4. Separation and Sorting:Material processing equipment is employed to separate different components or fractions based on their physical or chemical properties. This enables the extraction of valuable materials, removal of impurities, or segregation of different particle sizes.
5. Forming and Shaping: Some material processing equipment is used to shape and form materials into specific geometries or structures.
Advantages of material processing equipments
Precision and Accuracy: Material processing equipment is often equipped with advanced technologies and control systems that ensure precise and accurate processing of materials. This level of precision is crucial in industries where dimensional accuracy and quality control are essential, such as manufacturing and engineering.
Consistency and Quality Control: Material processing equipment enables consistent and standardized processing of materials, ensuring uniformity in the end products. This consistency helps maintain quality control standards and reduces the likelihood of errors or defects, resulting in improved product quality.
Increased Safety: Many materials processing equipment incorporate safety features and protocols to ensure the well-being of workers. By automating hazardous or repetitive tasks, these machines minimize the risk of accidents, injuries, and exposure to harmful substances, thereby enhancing workplace safety.
Versatility: Material processing equipment often offers versatility in terms of the types of materials it can handle. Whether it’s cutting, shaping, bending, or joining different materials, these machines can be adapted to various applications and accommodate different material properties, expanding their usability across different industries.
Scalability: Material processing equipment can be designed to scale according to production demands. They can handle large volumes of materials and accommodate increased production requirements, making them suitable for businesses with growing needs.
Improved Speed and Throughput: Material processing equipment can significantly increase processing speed and throughput, allowing for faster production cycles.
Automation and Integration: Material processing equipment can be integrated into existing production lines or automated systems, creating a seamless workflow. This integration enhances overall process efficiency, reduces human error, and enables real-time monitoring and control of material processing operations.
With advancements in technology, material processing equipment continues to evolve, incorporating new features, improved functionalities, and advanced techniques.
Different types of material processing equipments
Crushers
Crushers are a type of material processing equipment used in various industries to reduce the size of large rocks, ores, and other raw materials into smaller, more manageable pieces. They are commonly used in mining, quarrying, recycling, construction, and demolition applications. Crushers utilize mechanical force to break down the material by applying pressure or impact. Here are some common types of crushers used for material processing:
- Jaw Crushers:Jaw crushers are primary crushers designed to handle large, hard, and abrasive materials. They consist of a fixed jaw and a movable jaw that forms a V-shaped chamber. The material is fed into the chamber and crushed between the jaws as they close together.
- Impact Crushers: Impact crushers involve the use of impact rather than pressure to crush materials. They are used to crush softer, less abrasive materials such as limestone, gypsum, and recycled concrete. Impact crushers can be horizontal shaft impactors (HSI) or vertical shaft impactors (VSI). HSI crushers use a horizontal impact force to break the material, while VSI crushers utilize the material’s velocity to impact and break it against a rotating surface.
- Cone Crushers: Cone crushers are used for secondary and tertiary crushing applications. They are capable of producing finely crushed materials and are commonly used in the mining and aggregate industries. Cone crushers operate by squeezing the material between an eccentrically rotating cone and a stationary mantle. The crushed material falls through the bottom opening.
- Gyratory Crushers: Gyratory crushers are similar to cone crushers but have a different crushing chamber design. They consist of a conical head gyrating inside a larger bowl-shaped concave. Gyratory crushers are primarily used in mining and large-scale quarrying operations for high-capacity crushing.
- Roll Crushers: Roll crushers are composed of two rotating cylindrical rolls that crush the material between them. They are used for primary and secondary crushing of materials with compressive strength less than 200 MPa. Roll crushers are commonly used in the mining industry and in smaller-scale aggregate production.
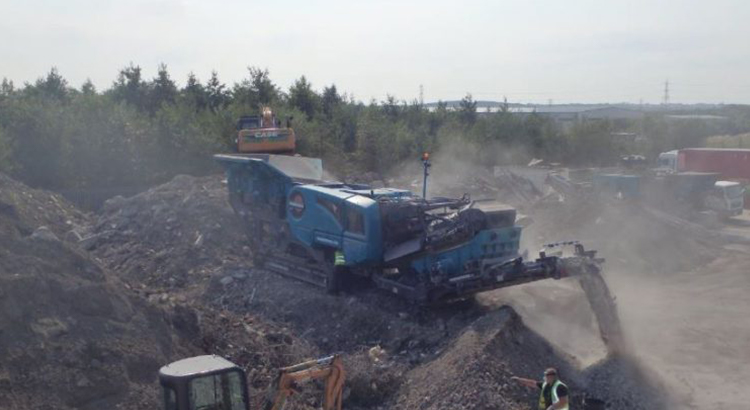
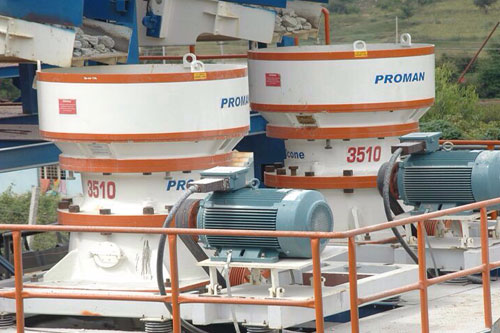
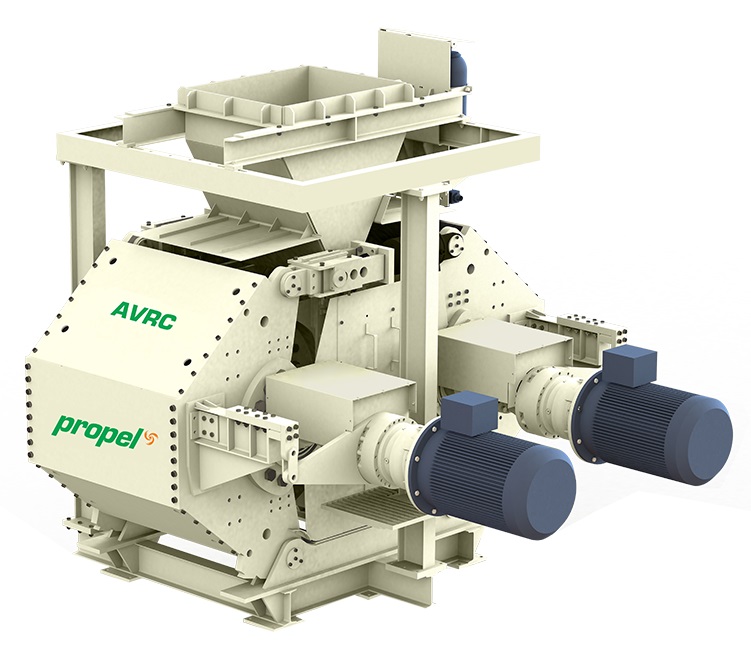
Screeners
Screeners, also known as vibrating screens or vibrating separators, are material processing equipment commonly used in industries such as mining, quarrying, recycling, and construction. They are designed to separate and classify bulk solids, granules, or powders based on their size, shape, or composition. Here’s an overview of screeners and their role in material processing. The screening process involves feeding the material onto the vibrating screen. The screen vibrates in a controlled manner, causing the material to spread out evenly and stratify according to size. Smaller particles pass through the openings in the screen, while larger particles are retained on the screen surface. There are various types of screeners available, each designed for specific applications and material characteristics. Some common types include:
- Inclined Screens: Inclined screens have a sloped surface and are commonly used for coarse screening applications. They are effective in removing oversized materials and scalping off fines.
- Horizontal Screens: Horizontal screens have a horizontal, flat surface and are used for fine screening applications. They provide high screening efficiency and are suitable for processing a wide range of materials.
- Banana Screens: Banana screens are multi-slope screens with curved deck surfaces. They are particularly effective in handling high-capacity applications and materials with high moisture content.
- Trommel Screens: Trommel screens are cylindrical drum-shaped screens that rotate. They are commonly used in the recycling industry and for screening materials such as compost, soil, and aggregates.
- Vibrating Grizzly Screens: Vibrating grizzly screens have grizzly bars or perforated decks that allow coarse materials to pass through. They are often used in primary crushing applications to remove undersized material before it enters the crusher.
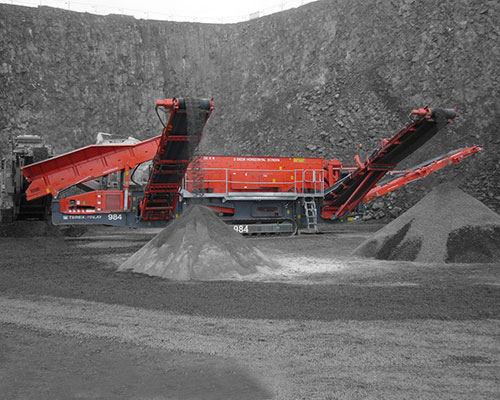
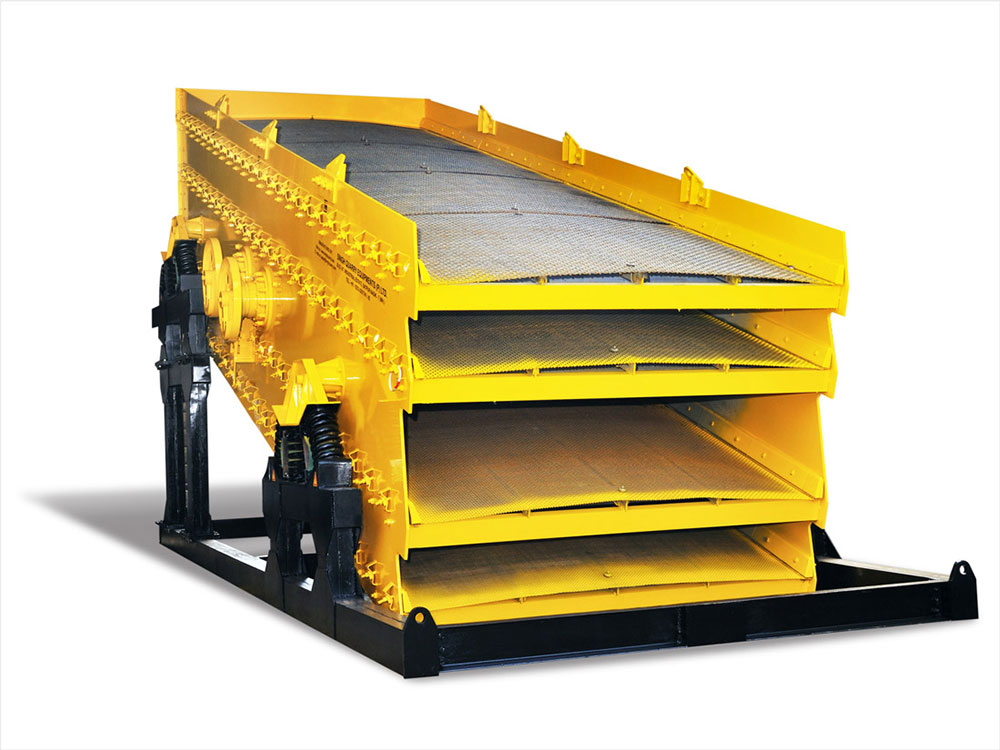
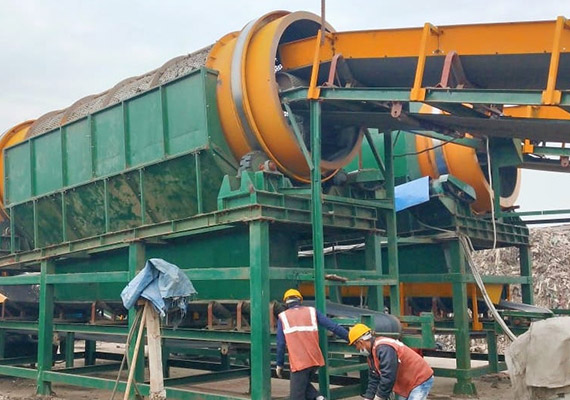
Feeders
Feeders are material processing equipment used to control and regulate the flow of bulk solids, granules, or powders from a storage unit or hopper to downstream processing equipment.
- Vibratory Feeders: Vibratory feeders use vibrations to convey material along a tray or trough. The vibrations generate a forward motion, causing the material to move in a controlled manner. Vibratory feeders are suitable for a wide range of materials and are known for their gentle handling of fragile or delicate products.
- Screw Feeders: Screw feeders consist of a rotating screw or auger that moves material along a trough or tube. The screw design allows for precise control of material flow, making screw feeders ideal for handling fine powders or cohesive materials.
- Belt Feeders: Belt feeders use a continuous belt or conveyor to transport material. The belt speed and design can be adjusted to control the feed rate and ensure an even flow of material.
- Rotary Feeders: Rotary feeders use a rotating drum or disc to meter material. They are commonly used in applications where a controlled discharge of material is required, such as in pneumatic conveying systems.
- Gravimetric Feeders: Gravimetric feeders measure the weight of material being fed and adjust the feed rate accordingly. They provide accurate and precise feeding, making them suitable for applications where precise material dosing is critical.



Conveyor
Conveyor equipment plays a crucial role in material processing industries by efficiently moving materials from one point to another. It enhances productivity, streamlines workflow, and automates the transportation of goods. There are several types of conveyor equipment commonly used in material processing applications. Here are some examples:
- Belt Conveyors: Belt conveyors consist of a continuous loop of material, typically made of rubber, fabric, or metal, that is used to transport items from one location to another. They are widely used in industries such as mining, agriculture, manufacturing, and logistics.
- Screw Conveyors: Screw conveyors use a rotating screw or auger to move materials along a trough or tube. They are suitable for handling various bulk materials, including grains, powders, and liquids. Screw conveyors are commonly used in food processing, agriculture, and wastewater treatment industries.
- Vibrating Conveyors: Vibrating conveyors use vibratory motion to transport materials. They consist of troughs or tubes that vibrate to move materials forward. Vibrating conveyors are often used in applications where gentle handling of materials is required, such as in the food and pharmaceutical industries.


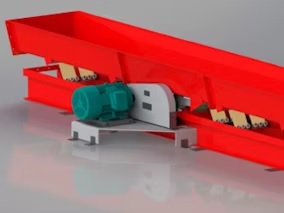
Extruders
Extruders are specialised equipment used in material processing to shape, form, and transform materials through a continuous process called extrusion. Different types of extruders includes;
- Single Screw Extruders: Single screw extruders are the most common type of extruders. They have a single rotating screw that conveys the material forward through a heated barrel. The screw applies pressure and heat to melt the material, and it is then forced through a die to obtain the desired shape.
- Twin Screw Extruders: Twin screw extruders have two intermeshing screws that rotate within a barrel. They provide better mixing, kneading, and compounding capabilities compared to single screw extruders.
- Co-rotating and Counter-rotating Extruders: Co-rotating extruders have screws that rotate in the same direction, while counter-rotating extruders have screws that rotate in opposite directions. Co-rotating extruders are more commonly used due to their higher processing capacity and better self-cleaning capabilities.
- Multi-Screw Extruders: Multi-screw extruders include extruders with three or more screws. They are used for specialized applications that require specific mixing, compounding, or reactive processing. Multi-screw extruders can be configured in various arrangements, such as parallel, conical, or planetary, depending on the specific process requirements.


Conclusion
Material processing equipments are vital for construction as it enhances efficiency and productivity, improves safety, enables efficient handling and transport of materials, facilitates specialized processing, provides versatility and adaptability, and incorporates technological advancements. The utilization of appropriate equipment streamlines construction operations, reduces manual labor, and ensures the successful execution of construction projects.
References:The Builder’s Diary
Image Source: powerscreen.com/en/, puzzolana.com, propelind.com, terex.com, singhcrushers.com, duromech.in, matechequipments.com, trimechindia.com, shivaequipments.com, akshayfoundryequipments.com, umaengineers.com, dphengg.com, vrundavanengg.com, actsengineering.in