Autoclaved aerated concrete is a versatile lightweight construction material and usually used as blocks. It has a low density and excellent insulation properties.What makes it a significant product is its composition which comprises all natural raw materials. Autoclaved aerated concrete (AAC) is concrete that has been manufactured to contain closed air pockets. It comes in the form of panels or blocks. Lightweight and fairly energy-efficient, it is produced by adding a foaming agent to concrete in a mould, then wire-cutting blocks or panels from the resulting ‘cake’ and ‘cooking’ them with steam (autoclaving). The gas used to ‘foam’ the concrete during manufacture is hydrogen formed from the reaction of aluminium paste with alkaline elements in the cement. It is composed of quartz sand, calcined gypsum, lime, cement, water and aluminum powder, AAC products are cured under heat and pressure in an autoclave.
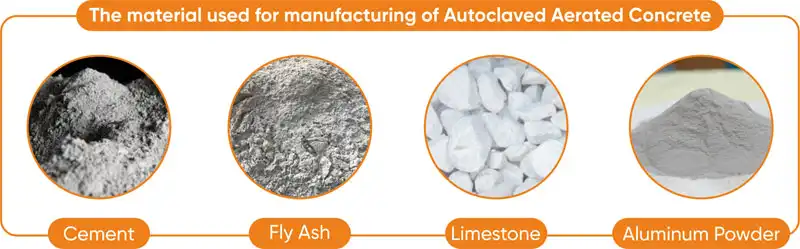
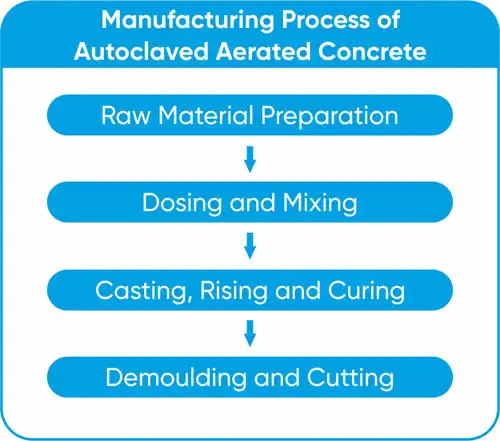
Features of Autoclaved Aerated Concrete
Environment Friendly
The ability of a product to reduce material use, utilize recycled products, and avoid toxic emissions is the basic criteria for determining whether a product qualifies as “green” or can be used in a sustainable manner. In this regard, Autoclaved aerated concrete stands out. AAC is non-toxic which does not pollute the air, land or water. Aerated autoclaved concrete blocks are created of recycled fly-ash, which is a waste generated in steel furnaces. Starting from the production to their transport, to the construction of AAC-based structures and maintenance, these blocks contribute to sustainability through a reduction of carbon footprints. The AAC Blocks are highly resource-efficient and environmentally friendly.
Cost effective attributes
The use of autoclaved aerated concrete has a vast range of cost-effective benefits. The insulation properties of aircrete reduce the heating costs of buildings constructed with autoclaved aerated concrete, which results in consequent fuel savings of the building’s lifecycle. AAC block weighs quite less as compared to the conventional bricks ultimately resulting into great reduction of deadweight. Further, the reduced deadweight results in a reduction of the use of cement and steel which helps greatly in cost savings. Additionally, AAC-related construction doesn’t need more than 24 hours of curing time, the water requirement is substantially reduced which again reduces the costs quite significantly.
Thermal Insulation
Exceptional thermal insulating qualities of AAC Blocks makes them an excellent green product. The thermal conductivity of these blocks helps in maintaining the inner temperature to be warm during the winters and vice versa, which ultimately leads to saving electrical load consequently and enhances energy efficiency.
Moisture Resistance
Moisture from both external and internal sources can cause damage to buildings, therefore, moisture protection is a primary consideration. External moisture sources such as rain and water from the soil and internal moisture, usually forms humidity and can cause condensation both internally and externally. But AAC blocks porous structure evenly distributing the water as small air bubbles throughout the material. Because of their cellular and discontinuous microstructure, there is a resistance of water penetrability and thus provides superior resistance to moisture penetration.
Mould resistant and non-toxic:
AAC is manufactured from non-biodegradable materials, which neither rot nor attract mould, keeping interiors clean and durable. AAC construction has very low air infiltration and is mold resistant, the indoor air quality of AAC structures is always better. Autoclaved Aerated Concretes do not contain any toxic gas substances and does not harbor or encourage vermin.
Seismic resistant:
The recent Nepal mishap has been an eye opener for the building structure worldwide. Therefore, it has become even more important to consider seismic resistibility of individual buildings. The impact of the earthquake is directly proportional to the weight of the building, in this regard, AAC Block is a great choice. The lightweight property of the AAC blocks results in higher steadiness. For instance, the majority of AAC homes in the 1995 Kobe, Japan earthquake survived substantially undamaged.
Sound Absorption:
The porous inhibition of the AAC blocks enables sound absorption. The Sound Transmission Class rating of the AAC blocks up to 45 db. AAC blocks are perhaps the ideal material for the construction of walls in commercial buildings such as hotels and hospitals to name a few.
Fire and Pest Resistive:
Owing to its natural composition and its thickness inhibition, the Autoclaved Aerated Concrete (AAC) Blocks offers excellent fire resistance If fire safety is your prime concern then these blocks are the most preferred product for you. Additionally, AAC Block consists of the inorganic material that helps to prevent termites, damages or losses.
Easy to install:
AAC blocks are very easy to handle and ordinary tools are used for cutting it. AAC blocks also come with larger sizes and fewer joints. This ultimately results in faster construction work as the installation time required is less. AAC Blocks have an attractive appearance and could be adapted to any style of architecture.
Applications of Autoclaved Aerated Concrete
Autoclaved aerated concrete is available in blocks and panels. Blocks are stacked up similar to conventional masonry units, with a thin-bed mortar. Panels are installed vertically, extending from floor level to the top of the wall. AAC is a highly thermally insulating concrete-based material used for both interior and exterior construction. Besides AAC’s insulating capability, one of its advantages is quick and easy installation, because the material can be routed, sanded, or cut to size on-site using standard power tools with carbon steel cutters. AAC is well suited for high-rise buildings and those with high-temperature variations. Due to its lower density, high-rise buildings constructed using AAC require less steel and concrete for structural members. The mortar needed for the laying AAC blocks is reduced due to the lower number of joints. Similarly, the material required for rendering is also lower due to the dimensional accuracy of AAC. The increased thermal efficiency of AAC makes it suitable for use in areas with extreme temperatures, as it eliminates the need for separate materials for construction and insulation, leading to faster construction and cost savings.
Conclusion:
Green building has become the need of time. The product’s segmentation has therefore become even more important.Through adhering to green materials such as AAC Blocks and a little help from technology the efficiency can be materialized in a broader sense. AAC products may be used for both interior and exterior construction, and may be painted or coated with a stucco or plaster compound to guard against the elements, or covered with siding materials such as veneer brick or vinyl siding. In addition to their quick and easy installation, AAC materials can be routed, sanded, or cut to size on site using standard power tools with carbon steel cutters.