Insulated concrete forms (ICFs) are cast-in-place concrete walls that are sandwiched between layers of insulation material. This construction method is known for its high strength and energy efficiency. Some typical applications of ICFs include residential and commercial low-rise buildings. Walls are made from interconnected forms, which stay in place as permanent structures. Traditional finishes are applied to both interior (drywall) and external faces (stucco, lap siding, brick, etc), therefore buildings with ICFs will look similar to typical constructions, only with slightly thicker walls.
Insulated Concrete Forms
The use of insulated concrete forms dates back to the years after World War II when multiple companies developed structures that resemble today’s typical ICFs. In the 1990s, the Insulating Concrete Form Association (ICFA) was founded with several goals. when Swiss engineers began holding cement walls together with treated blocks of wood. After that, the idea was adopted by chemical companies that developed plastic foams.
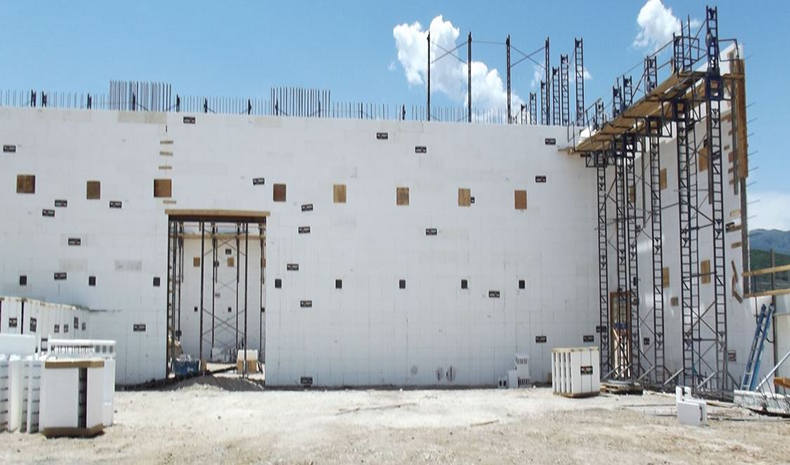
This was later further developed by Jean-Louis Béliveau to regulate the temperature in his parents’ Florida home. The pursuit of these forms is to be permanent wall supports that create space to run wiring and plumbing, provide thermal and acoustic insulation, and be the interior side for exterior walls.
- Conducting research
- Promoting product approval
- Developing new technologies to enhance this construction method
- Achieving acceptance in building codes
The major issue with ICFs was the lack of technical knowledge since installers were not acquainted with the system. Contractors had to work carefully to achieve regulatory approvals and materials were proprietary, leading to much higher costs than conventional frame construction.
Insulated concrete forms (ICFs) and blocks are not new, but their sudden popularity and growth as a building material are. More builders and homeowners are selecting to build with ICFs than ever before, which has led rise to some questions and misconceptions about the material.

Like anything else being put forward for the first time, some home and business owners may be sceptical about using the forms, and some builders who have long worked with wood and concrete, but not ICFs, may be reluctant to use them. These five misconceptions about ICFs and blocks may be keeping you from making the leap to using this innovative product, without you recognising it.
- RELIABLE ICF – Our Insulated Concrete Formwork (ICF) based technology is now approved by Min. of Housing & Urban Affairs, Government of India. Specifications of the same will be included in the DSR that is currently under process.
- Design and construction with our product RELIABLE ICF for mass housing or other Government projects can be formally adopted in any future projects across the country.
While all future government constructions are to use any one of the new technologies listed by CPWD, RELIABLE ICF is the only one that has the added benefit of being fully insulated (100% insulation on walls and roof).
Reliable ICF
Is the most convenient construction system using lightweight, hollow, “Self Extinguishing” grade high-density EPS (expanded polystyrene) moulded forms inter-locking on all six edges to create a building load-bearing wall shuttering?
These are used as a lost shuttering system (shuttering is not removed after concrete pour) to provide an extremely economic and environment-friendly method of wall construction. This permanent insulated formwork is the shell for a super fast & energy-saving building.

A Convenient construction, Greener, Safer & Faster than the traditional systems”
Reliable ICF is a Convenient on-site technology :
- Easily assembled
- With minimal components and tools/tackles
- Uses minimal manpower of limited skills
- Simple stacking of light weight, interlocking, hollow blocks
- Wall shuttering with door – window openings created up to 3m roof height at a time
- Shuttering filled with reinforced concrete, cures adiabatically (at constant temperature and pressure), without any water even in cold climate (-250C).
Why Reliable ICF
- Resource conservation both during & after construction.
- A zero wastage formwork system and
- Adiabatic concrete curing, uses no water at site.
- Saves up to 90 % of HVAC energy
- Reduces HVAC capacities by 50%
- “Green” or recycled concrete with higher flyash content due to zero thermal stress in concrete monolithic, loadbearing concrete walls
- Strong, disaster proof structure
- Safe from fire, earthquakes, floods & cyclones cracks free inner concrete core
- Ultra light shuttering without heavy equipment for construction ensures zero accidents
- Ideal for bunkers, explosion-proof structures
- Remote locations, extreme weather conditions
Types of Insulated Concrete Forms Systems
There are three major ICF system designs: flat system, grid system, and post and beam system. All three methods are accepted by codes and have been deployed successfully in many projects. Flat systems are similar to conventional poured walls, with a continuous thickness of concrete through the entire wall. On the other hand, grid systems have a waffle pattern where the concrete is thicker at some points. The post and beam systems have horizontal and vertical elements of concrete that are completely encapsulated in foam insulation.
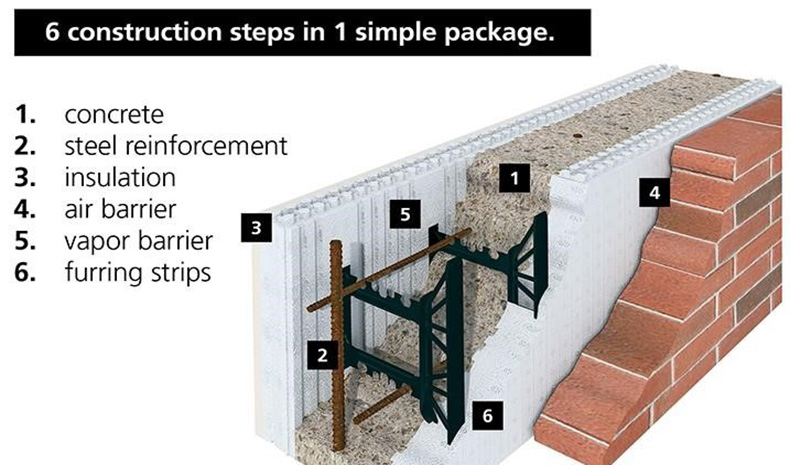
Pros
Strong Walls
Adding an insulated concrete form has the primary advantage of strengthening a building’s walls. The poured concrete hardens around the ICFs, which then reinforces the wall and reduces its vulnerability to vertical and horizontal forces. Depending on whether the frame of the ICF is flat or grid, the wall can be made even more powerful by the frequency and rigidity of the inner connectors. Unlike a normal cement fixture, the pockets and ICFs between the walls actually increase the structure’s strength and durability
Energy Efficient
One of the most appealing aspects of using insulated concrete forms is that it has the potential to significantly reduce the heating and cooling costs of a particular building. That’s also the most impressive feature of ICF walls; they can release heat in the summer and store heat in the winter. In some instances, ICFs are estimated to save about 20% of total energy costs.
As a comparison, the tightness around insulated concrete form walls is much tighter than those of compatible window and door frames. If your insulated concrete forms have a lifespan of 100 years, with no degradation, a single-family ICF home could save up to 110 tons of carbon dioxide compared to traditional wood-framed homes. CO2 savings that high would create a net positive carbon footprint for the cement and the ICFs.
Sound Reduction and Temperature Stability
Through a sandwich of materials, insulated concrete forms are able to act as a sound barrier, protecting the interior of the house from outdoor noises. When a massive material, in concrete, is combined with a light one like foam, fluctuations in temperature, air filtration, and sound are able be dramatically reduced. The layer of foam that insulates the entirety of an ICF wall helps keep it the same temperature throughout – essentially eliminating “cold spots” that occur in frame walls between insulation voids or around the studs. In terms of sound reduction, walls with insulated concrete forms allow for only one-eighth the amount of sound to be penetrated as that of a wood frame wall.
Cons
Don’t Work As Well In Cold Climates
In theory, these walls act as strong insulators of heat at colder exterior temperatures. However, this doesn’t account for the amount of heat that transfers outside. Insulated concrete forms are designed to transfer heat out of the structure so that outdoor temperatures don’t negatively affect the curing process of the concrete. Therefore, ICFs work much better in more tropical climates where the heat transfer and insulation can keep a home cool during the day while also making it comfortably warm at night.
Could Be More Costly Than Expected
The savings regarding insulated concrete forms is undeniable; however, that’s assuming you have the affordable labour to install it. If you decide to incorporate ICFs into your project’s walls or foundation, you might be looking at overall costs that are more expensive than conventional processes. Insulated concrete forms require specialized labour; if your worksite is located in an area with very few contractors capable of incorporating ICF, then you may want to switch to cheaper methods.
ICF Building Process
ICF construction is often considered less demanding than typical construction. Less-skilled labour can be employed to lay the ICF forms (although careful consideration must be made when pouring concrete to make sure it joins fully and cures evenly without cracking). Unlike traditional wood beam construction, no additional structural support is required for openings, doors, windows, or utilities.
ICF Cost
ICF construction will cost about 40% less than conventional construction, primarily because of the labour savings from combining multiple steps into one step. Above-grade ICF construction is typically more expensive, but when adding large openings, ICF construction becomes very cost-effective.
QUICK AND SIMPLE
ICF forms can be assembled by a modest number of workers. Once the forms are in place, concrete pouring is typically completed in a matter of hours. Since concrete is included within layers of rigid foam insulation, curing can continue while other parts of the project proceed.