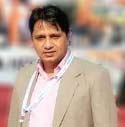
Researchers and various institutes are taking technology to the next level. Development in concrete and various other construction materials has been aggressive and intense.
The development of innovative new building materials has allowed architects to better realise their visions, as they make more daring structures possible due to their improved strength, flexibility and durability. The next decade is likely to be instrumental in seeing some key applications commercially and being adopted by the mass market..
Let’s have a look at a few innovative construction materials that could revolutionize the Construction Sector across the globe.
Solar-Harvesting Roads
Renewable technologies continue to advance with more diverse and unexpected applications, such as the integration of solar harvesting capability in transportation infrastructure. A solar road is a concept where solar panels are embedded into materials used to either replace or rest atop of pathways and roads. There are several major solar road projects presently being developed and/or tested, all sharing the same core principle of roads that collect solar energy.
The first solar road to be implemented, “SolaRoad”, was a solar bicycle path installed in Krommenie, the Netherlands, in 2014. The path is 70-meter long (just under 230 feet). It cost over $3 million to install. Over the past year, this installation has yielded 9800 kWh of energy. It’s been considered a success and may be expanded in the coming months.
For example, TK City, Idaho–based company Solar Roadways develops interlocking hexagonal pavers composed of a photovoltaic (PV) substrate protected by high-strength textured glass. The pavers incorporate LED lighting and heating elements for self-powered roadway illumination and snow-melting capabilities.
Another example is Wattway, an energy-harvesting road surface made by French civil engineering firm Colas. According to the manufacturer, vehicles occupy roads a mere 10 percent of the time; meanwhile, 20 square meters of exposed road surface can be put to use to power a typical single home. A flexible composite material that is only a few millimeters thick, Wattway exhibits a highly textured PV surface. While it lacks the multiple technologies and capabilities of Solar Roadways, Wattway can be applied directly onto the surface of existing pavement and is designed to accommodate the inherent thermal dilation of vehicular paving. The company recently installed a 1-kilometer-long swath of roadway in Normandy with the product, which is anticipated to generate 280 megawatts annually.

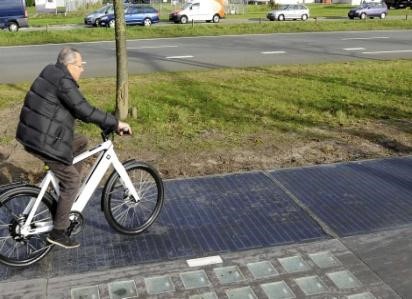

Solar-Harvesting Roads
Cooling system in bricks
Through the combination of clay and hydro-gel, students at the Institute of Advanced Architecture of Catalonia have created a new material that has a cooling effect on building interiors. Hydroceramics have the ability to reduce indoor temperature by up to 6 degrees Celsius.
The Basic Concept behind this is that the Warm air moves through each brick, and its network of tiny holes, heating the water held in each of the pores. As the water is heated, it evaporates, cooling the air and lowering a building’s temperature in the process.
Cool Brick is modular, thus can be stacked into numerous configurations allowing architects and engineers to run riot with form and function. Its 3D lattice creates an especially durable bond once held in place by mortar. The shape of the brick also creates a shaded surface on the wall to keep a large percentage of the wall’s surface cool and protected from the sun to improve the wall’s performance.
Its cooling effect comes from the presence of hydro-gel in its structure which absorbs water, up to 500 times its weight. The absorbed water is released to reduce the temperature during hot days. Incorporating an innovative cooling system in the current building structure has made Hydroceramics into one of the coolest building materials to revolutionize construction. More progress in this direction, may make household air conditioners obsolete.

Pollution absorbing bricks
We now have pollution vacuums in bricks! Developed by assistant professor Carmen Trudell at Cal Poly, college of architecture and environmental design, the Breathe Brick sucks in pollutants in the air and releases filtered air.
The Breathe Brick is designed to form a part of a building’s regular ventilation system, with a double-layered facade of the specialist bricks on the outside, complemented by a standard internal layer providing insulation. At the center of the Breathe Brick’s function is cyclone filtration, an idea borrowed from modern vacuum cleaners, which separates out the heavy pollutant particles from the air and drops them into a removable hopper at the base of the wall.
In short, it is a technology that can be easily applied to the current construction processes.
By performing wind tunnel tests, it was proven that the system can filter 30% fine particle pollutants and 100% coarse particles such as dusts.
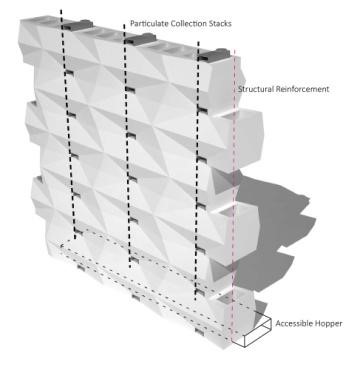


Pollution absorbing bricks
Cigarette butts in Bricks
On a yearly basis, 6 million cigarettes are manufactured and they produce 1.2 million tonnes of cigarette butt waste. The impact on the environment is tremendous. Elements such as arsenic, chromium, nickel and cadmium enter the soil and harm nature.In order to reduce the impact of cigarette butts on the environment, researchers at RMIT developed lighter and more energy efficient bricks made of cigarette butts. In short, innovatively utilizing waste in a much more eco-friendly manner.



Cigarette butts in Bricks
Dr. Abbas Mohajerani, the leading researcher of the project, along with his team discovered that by infusing even 1% of cigarette waste in fired-clay bricks they can have great results in removing pollution from our environment.
Not only does this research help with reducing waste, but the resulting brick is also lighter and requires less energy in manufacturing it.
When cigarette butts are added to clay bricks, the energy needed to fire them was cut by up to 58 percent. The bricks were lighter and were better insulators, too, meaning they could help cut household cooling and heating demands, all while keeping the same strong properties of traditional bricks.
When the cigarette butts are fired in the bricks, the heavy metals and other pollutants are trapped and immobilized in the solid block so they can’t leach “Incorporating butts into bricks can effectively solve a global litter problem as recycled cigarette butts can be placed in bricks without any fear of leaching or contamination,”- Dr. Abbas Mohajerani.
Translucent wood as construction material
Researchers from the University of Maryland devised a way to strip the colors and and chemicals from a block of wood to leave behind a clear, transparent material that’s stronger and more insulating than glass, and biodegrades better than plastic.
We now have translucent wood that can be used to develop windows and solar panels. It is created by first removing the lining in the wood veneer and then through nanoscale tailoring. The resulting effect creates translucent wood that has various application in the construction industry. As a very cheap resource, it can benefit projects by reducing cost of resource. The innovation took place at Stockholm’s KTH Royal Institute of Technology. Lars Berglund, a professor at KTH claims that transparent wood is a low cost, readily available and renewable resource.The secret lies in the natural architecture of the wood, combined with the refractive qualities of the epoxy. Even though its color was gone, the underlying structures in the wood remained the same, including the tiny channels that trees use to transport nutrients. When filled with the epoxy, these channels turned into conduits for light, focusing it and allowing it to pass through. The end product looks more like a piece of plastic than something that once stood in a forest. The wood can be mass produced and can be used commercially. The study was then published by Biomacromolecules.

Graphenea ‘wonder material’
Graphene has earns something of a reputation as a ‘wonder material’ with the potential to revolutionise our daily lives. It was Initially discovered 12 years ago, Graphene is still waiting for wide scale adoption. Its properties, however, suggest it is ideal for construction. This two dimensional, honeycomb lattice is the thinnest material on Earth, but is up to 200 times stronger than steel. It is ultra-lightweight, and acts as a barrier to even the lightest of gases.
Graphene technologies are set to have the biggest impact – from walls to lighting to touch panels, generators and batteries, sensors and solar panels. However, graphene is so difficult to produce that builders have rarely been able to use more than a few flakes of it per project. Until now, that is, as the US’ Oak Ridge National Laboratory has developed a new way of producing it using a technique known as chemical vapour deposition. The range of activity in so many areas that will impact on construction in the space of just over a decade is further proof of graphene’s status as a ‘wonder-material’.

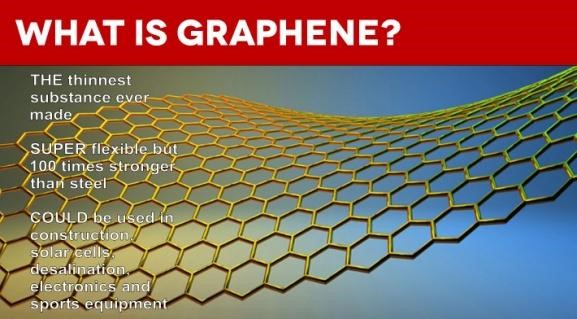
Graphenea ‘wonder material’
The CABKOMA strand rod
The Komatsu Seiten Fabric Laboratory, based in Japan has created a new material called the CABKOMA Strand Rod. It is a thermoplastic carbon fiber composite.
The CABKOMA Strand Rod for seismic reinforcement is a thermoplastic carbon fiber composite. It uses carbon fiber, which is an advanced material, as the interlining, while its outer layer is covered with synthetic fiber and inorganic fiber. It is finished by impregnation with thermoplastic resin.
The strand is the lightest seismic reinforcement and is very aesthetically pleasing. A single strand of CABKOMA Strand Rod of 160 meter length weighs only 12 kg which is 5 times lighter compared to a metal rod.
- Its tensile strength is high, while it is the lightest seismic reinforcement in the world.
- Delicate but strong structural body
- Superb aesthetic quality that achieves lightness

Bio-Plastic Furniture(Biologically produced furniture)
Another very beautiful innovation in the construction industry is the invention of bioplastic furniture. Bioplastic is a polymer with similar characteristics and properties to plastics made from non-renewable fossil fuels. It can be injected, extruded and thermoformed but it is made from plant-based renewable resources (beet, corn starch, sugarcane, etc.). This biobased polymer is fully recyclable and its organic properties mean that, when subjected to an industrial process, it is biodegradable. Moreover, another significant environmental aspect lies in its reduced carbon footprint as bioplastic production results in reduced greenhouse gas emissions. this process is low energy, pollution free and requires low technology for the creation.The use of bioplastic is currently being researched in a number of different industrial sectors, including the automotive industry.


Bio-Plastic Furniture(Biologically produced furniture)
Hardwood Cross Laminated Timber(CLT)
Another common building material that is receiving significant interest is wood. The construction industry is currently enamored with mass timber, based on the development of new methods for tall building construction using a rapidly renewable, carbon sequestering material that outperforms concrete and steel environmentally. Within the burgeoning field of softwood-based engineered lumber products, an unlikely contender has appeared: hardwood cross-laminated timber (CLT). Main benefits of using Hardwood CLT is:-
- Framing with Hardwood CLT Shortens Construction Time
- Hardwood CLT Buildings Are Safer in a Fire
- Hardwoods Are Strong & Resilient
- Hardwoods are Sustainable & Good for the Environment
- Save Money with Hardwood CLT Framing
London-based DRMM Architects developed a CLT panel of rapid-growing North American tulipwood in collaboration with global engineering firm ARUPand the American Hardwood Export Council. The material is now licensed to Stuttgart-based manufacturer Züblin under the name Leno CLT. Unlike typical CLT, which consists of softwood spruce, the tulipwood version is much stronger-and even stronger than concrete by weight-and is considered to have a superior appearance. Furthermore, Leno CLT is made from a rapidly renewable feedstock and can be manufactured in extra large sizes-such as the 14-meter-by-4.5-meter panels used in the Smile.

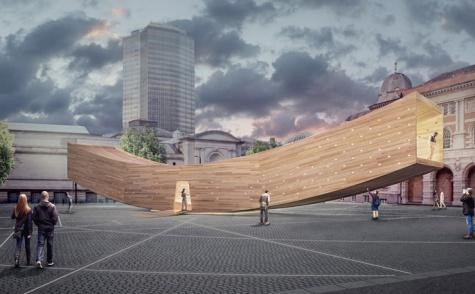
Hardwood Cross Laminated Timber(CLT)
Carbon-fibre balsa
Balsa wood is useful thanks to its stiffness despite being incredibly lightweight; however, it is difficult to produce and therefore expensive. However, a team of researchers at Harvard University have managed to create cellular composite materials of unprecedented light weight and stiffness that could replace it.
Fibre-reinforced epoxy-based thermosetting resins and 3D extrusion printing techniques have been used to create the synthetic replacement. The researchers used these methods to create a ‘honeycomb’ effect in carbon-fibre epoxy materials. Carbon fiber is composed of carbon atoms bonded together to form a long chain. The fibers are extremely stiff, strong, and light, and are used in many processes to create excellent building materials. Carbon fiber material comes in a variety of “raw” building-blocks, including yarns, uni-directional, weaves, braids, and several others, which are in turn used to create composite parts.
The end result is something that could potentially completely replace balsa wood. Not only would it be cheaper, it also eliminates the problems the wood has with irregular grains that make it difficult to use in precision structures.

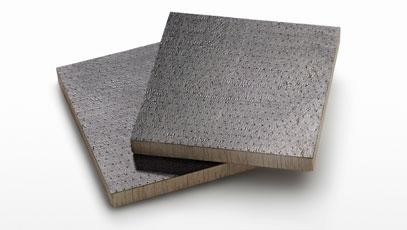
Carbon-fibre balsa
The two most common uses for carbon fiber are in applications where high strength to weight and high stiffness to weight are desirable. These include aerospace, military structures, robotics, wind turbines, manufacturing fixtures, sports equipment, and many others. High toughness can be accomplished when combined with other materials. Certain applications also exploit carbon fiber’s electrical conductivity, as well as high thermal conductivity in the case of specialized carbon fiber. Finally, in addition to the basic mechanical properties, carbon fiber creates a unique and beautiful surface finish.
Aerogel Insulation Material
Aerogels, despite their name, are actually highly porous solids. Their construction process is certainly unique. Liquid is removed from a gel while drying under special conditions, resulting in a material consisting of 80-99% air. Thanks to their uncommon make-up, aerogels hold the lowest thermal conductivity rating of any solid.
A variety of manufacturers have thrown their weight behind aerogel, positioning them as highly effective, environmentally friendly, alternatives to traditional insulation materials. Aerogels have been found to be up to four times more effective than fibreglass for insulation, and up to eight times more energy-efficient than polyurethane. While it has been bubbling below the surface, aerogel insulation is set to explode, adoption-wise, from 2017 onwards.


Aerogel Insulation Material
Self healing concrete
Concrete is one of the most widely used materials in the world, but at some point, no matter how it is mixed, it will crack and deteriorate. Here we are discussing about two main self healing concrete methods:-
By Heating the Concrete:- Dutch civil engineer, Dr. Schlangen at Delft University has created a self healing concrete. In his presentation, he demonstrated the effectiveness of the material by breaking it in two, putting the pieces together, and heating the concrete in a microwave oven. Once the melted material cools down, it joins together.
Of course with this method, the concrete needs heat. If the material is used to create roads, how will they be heated up?? To solve that problem, Dr. Schlagen and his team created a special vehicle that passes induction coils on the road.
Bio Concrete:- The bacteria, either Bacillus pseudofirmus or Sporosarcina pasteurii, are found naturally in highly alkaline lakes near volcanoes, and are able to survive for up to a staggering 200 years without oxygen or food. They are activated when they come into contact with water and then use the calcium lactate as a food source, producing limestone that, as a result, closes up the cracks. In order to keep the bacteria dormant until it is needed, it is placed in small, biodegradable capsules containing the nutrient. When the concrete cracks, and water enters the gaps, it comes into contact with the bacteria and the food source, setting the healing process off. The bacteria then feed on the calcium lactate, joining the calcium with carbonate to form limestone, fixing the crack.
The process has been proven to work effectively, and can even be added to a liquid that could then be sprayed onto existing buildings.
In coming years incredible self-healing material will be used in bridges, tunnels, roads and other buildings, with the bacteria laying dormant for centuries and only ‘coming to life’ when needed.


Self healing concrete
Old is Gold-Roman Concrete
Modern concrete-used in everything from roads to buildings to bridges-can break down in as few as 50 years. But more than a thousand years after the western Roman Empire crumbled to dust, its concrete structures are still standing.
Now, scientists have finally figured out why: a special ingredient that makes the cement grow stronger-not weaker-over time. Scientists began their search with an ancient recipe for mortar, laid down by Roman engineer Marcus Vitruvius in 30 B.C.E. It called for a concoction of volcanic ash, lime, and seawater, mixed together with volcanic rocks and spread into wooden molds that were then immersed in more sea water. When they analyzed it, they found that the seawater had dissolved components of the volcanic ash, allowing new binding minerals to grow. Within a decade, a very rare hydrothermal mineral called aluminum tobermorite (Al-tobermorite) had formed in the concrete. Al-tobermorite, long known to give Roman concrete its strength, can be made in the lab, but it’s very difficult to incorporate it in concrete. But the researchers found that when seawater percolates through a cement matrix, it reacts with volcanic ash and crystals to form Al-tobermorite and a porous mineral called phillipsite
Unlike modern concrete, in which Portland cement to bind the aggregate, Roman concrete uses a mortar mix of volcanic limestone, which reacts to form crystals that expand into the space within the concrete more effectively. This performs the function of microfibers in Portland-based concrete, but better – more resistant to corrosion, and packing the space more tightly. This also cuts the risk of microcracking in the concrete over time, extending lifespan considerably – 2,000 years and counting, as a trip around Rome will prove. Roman concrete is not just stronger than the modern version, it is also greener. The limestone and clay used in Portland cement needs to be heated to over 1,400 degrees Celsius in the manufacturing process, and this accounts for 7% of global carbon emissions. Roman concrete, on the other hand, needs nothing like this kind of heat, as the volcanic ash and lime they used reacts at a lower temperature. This means a potential new concrete formula that is stronger, greener, and longer lasting.

Shotcrete: Shock-proof concrete
A team of researchers at the University of Nebraska-Lincoln has developed a unique type of conductive concrete that could prove a game changer. The brainchild of Professors Chris Tuan and Lim Nguyen, Shotcrete works by absorbing and reflecting either man-made or naturally occurring electromagnetic waves.
Standard concrete aggregates were thrown out during the research process. Replacing them was a secret ingredient: magnetite. This mineral has magnetic properties that soak up microwaves like a sponge. Carbon and metal components were also worked into the Shotcrete mix for further absorption and reflection enhancement.
Shockcrete being applied to a building in spray form (Image: © University of Nebraska-Lincoln).
Professors Nguyen and Tuan first investigated conductive concrete as potential de-icer for pavements, roads, airport tarmacs and the like. Its reflective properties also make Shotcrete ideal for guarding against electromagnetic pulses which could scramble any electronics held within a building. Shotcrete is available as a spray-on solution, so outfitting or renovating existing structures is claimed to be quick and easy.
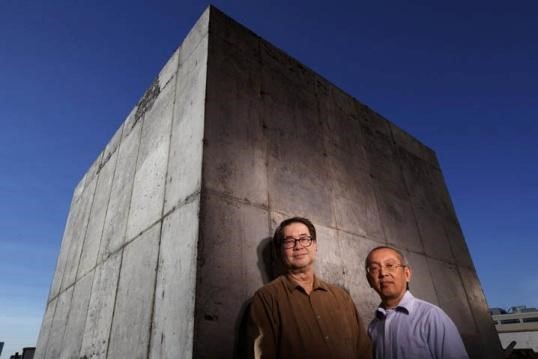

Shotcrete: Shock-proof concrete
Martian concrete
Thanks to new innovation now we have concrete that can be used to build structures in Mars now. The researching team at the Northwestern University, has created concrete that can be made with the materials available on Mars.
We have concrete that can be used to build structures in Mars now. The new concrete also doesn’t require water as an ingredient to be formed. With the scarcity of water as a source, this crucial benefit can make this innovation truly beneficial for the development of structures in Mars.In order to make the martian concrete, sulphur is heated at 240° celsius which melts it into a liquid. The martian soil then acts as an aggregate and once it cools down we get Martian concrete! According to the researching team, the ratio of martian soil and sulphur needs to be 1:1.
There’s another advantage of Martian concrete over Earth concrete, too. On Earth, concrete production is the third biggest contributor of CO2 emissions, largely because of how much concrete we use. And recycling concrete doesn’t help curb that production, because while we’re tearing down concrete structures all the time, it’s time-consuming and resource-intensive to reuse. But on Mars, the concrete could literally just be re-heated until the sulfur melts, and the entire concrete block becomes malleable again. That means any Martian concrete will be almost infinitely reusable, without taking the same toll on Mars as it took on Earth.


Martian concrete
Microscopy images show how much smaller the particle sizes are in the Martian concrete (left) compared to the conventional sulfur concrete (right).
Programmable Cement
As humanity’s most consumed substance after water, concrete remains a primary focus of material research and development. Despite its ubiquity, concrete still holds many mysteries awaiting discovery-such as the recent discovery that the cement in concrete carbonizes carbon dioxide over time, effectively redefining the material’s presumed environmental footprint. Such studies emphasize the need to better understand and shape the material at a molecular level.
A compelling recent example has emerged within the Multiscale Materials Laboratory at Rice University. Rice University Scientists have decoded the kinetic properties of cement and developed a way to “program” the microscopic, semicrystalline particles within. This turns particles from disordered clumps into regimented shapes (cubes, spheres, etc.) that combine to make the material less porous and more durable. The programmable cement will lead to stronger structures that require less concrete, thus reducing concrete production and, in turn, carbon emissions. The other is that it will be more durable. Less porosity makes it harder for unwanted chemicals to find a path through the concrete, so it does a better job of protecting steel reinforcement inside.


Programmable Cement
Light Generating Cement
Dr. José Carlos Rubio Ávalos from UMSNH of Morelia, has created cement that has the ability to absorb and irradiate light. With this new light generating cement the potential uses and application of it can be huge.
The construction industry is evolving and one of the main trends is the move towards a more resource and energy efficient way of creating structures. The researcher claimed that the applications are very broad, and those which stand out most are for the architectural market: facades, swimming pools, bathrooms, kitchens, parking lots, etc. It would also be useful in road safety and road signs, in the energy sector, such as oil platforms, and anywhere you want to illuminate or mark spaces that don’t have access to electricity since it doesn’t require an electrical distribution system and is recharged only with light. The durability of light-emitting cement is estimated to be greater than 100 years thanks to its inorganic nature, and its material components are easily recyclable.
We want light to penetrate the material up to a certain level. In the case of conventional cement, Portland, doesn’t have that capability because when the light reaches its surface it can’t penetrate it
The science behind it: Through the process of poly condensation of raw materials such as river sand, industrial waste, silica, water and alkali. The process is done at room temperature which is why the energy usage is low. In short, we now have smart cement!
Charging the material using natural or artificial light, it hopes to offer new light and thermal functions to the most used construction element in the world in order to reduce the energy consumption generated by current light and thermal systems.


Light Generating Cement
Till now we have just seen a glimpse of what has already been achieved in the construction industry so far. There is so much more new and extraordinary out there for us to see in future and the journey has just begun. We hope that science and technology will keep progressing and accelerating the pace of change that is coming our way!
About author
The author is General Manager of M P Construction Co. with nearly 14+ years of experience in construction projects & leveraging standalone expertise in making timely decisions that positively impact project success. His expertise is Project Execution & Project Management for Various Civil Projects Railways/Metro/Bridges/ Building/Highway/Airports etc. He is currently handling Chennai Metro Rail project, Western Dedicated Freight Corridor and Railway Line Doubling work of Dound-Kalburgi Section in Solapur Division of Central, Railway-Maharashtra.
Image credits: IAAC Institute for Architecture, Carmen Trudell (Both Landscape and Architecture / Assistant Professor, Cal Poly San Luis Obispo), RMIT University, KTH Royal institute of technology & Liangbing Hu, CABKOMA strand rod, Terreform One & Schaffenburg, Brett G. Compton, Harvard University, LUCKYPIC VIA SHUTTERSTOCK, UMSNH of Morelia