
The growing popularity of Aluminum Composite Panels (ACP) has made them the preferred solution for both interior and exterior cladding in modern construction. Known for their strength, durability, and aesthetic appeal, ACP sheets are widely used in both residential and commercial projects. However, for manufacturers, achieving the delicate balance of producing high-quality ACPs at competitive prices is a challenging task. The market demands panels that are not only visually striking but also resistant to weather, fire, and wear and tear. Customers expect these attributes at affordable prices, pushing manufacturers to innovate in order to reduce costs without compromising quality. With narrow profit margins and intense competition, finding this balance is important for ensuring both profitability and reliability.
By adopting advanced technologies, new practices, and strategic interventions, manufacturers can maintain this balance effectively. Here are few practical strategies that producers employ to achieve cost-effectiveness while upholding the quality standards of ACP production.
Reduce Waste for Enhanced Efficiency
An important element of efficient, high-quality manufacturing is waste reduction. Manufacturers can significantly minimize material waste by utilizing advanced machinery and precise production methods. This not only reduces production costs but also enhances the final product’s quality. Regular audits and lean manufacturing principles help identify inefficiencies and streamline production processes. By recycling scrap materials and adopting eco-friendly practices, manufacturers can also reduce disposal costs and improve sustainability. Studies show that lean manufacturing can increase cost efficiency by reducing waste by 20-30%. Prioritizing waste reduction not only lowers expenses but also strengthens a manufacturer’s position in the eco-friendly market, appealing to environmentally conscious clients.
Innovative Design and Strategic Inventory Management
Efficient inventory and product design management are key to profitability and operational efficiency. Manufacturers can categorize inventory into “Runner,” “Repeater,” and “Stranger” products based on sales trends. By prioritizing the production and stock levels of runner and repeater products, manufacturers can avoid overstocking slow-moving inventory, which reduces storage and interest costs. Regional inventory planning aligned with demand patterns ensures quicker order fulfillment and further optimizes stock management. Strategic inventory control can improve cash flow and profitability by reducing carrying costs by 15-25%, preventing overproduction, and enhancing overall financial stability.
Continuous Production and Coating Line Integration
Streamlined production processes supported by continuous production and coating lines are essential for both efficiency and quality. Integrated operations reduce delays and disruptions, ensuring smooth workflow and minimal work-in-progress accumulation. Modern machinery optimizes material flow, minimizing bottlenecks and maintaining consistent product quality. Continuous manufacturing systems cut production time, reduce material costs, and boost throughput by 10-20%, allowing for faster order completion without compromising quality. This strategy enables manufacturers to scale operations effectively while maintaining high standards.
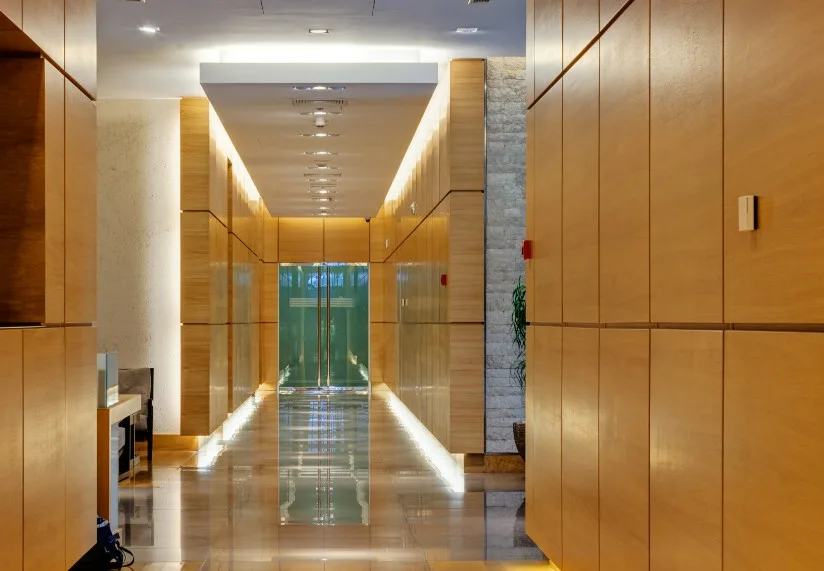
Preventive Maintenance and Machine Monitoring
Well-maintained equipment is essential for manufacturing efficiency and consistent product quality. Scheduled preventive maintenance reduces downtime and repair costs by preventing unexpected malfunctions. Real-time machine performance monitoring allows for early detection of potential issues, helping avoid costly disruptions. Proper equipment maintenance extends its lifespan, reducing the frequency of replacements and ensuring steady output. Preventive maintenance can increase machine lifespan by up to 30% and reduce maintenance costs by 15-20%. By investing in machine monitoring and preventative maintenance, manufacturers enhance productivity and reduce operational risks, ensuring long-term cost efficiency.
Leverage Advanced Technology for Competitive Edge
Modern technologies are transforming how ACP manufacturers balance quality and cost. Automation of repetitive processes reduces labor costs, ensures precision, and minimizes errors. Advanced coating techniques, such as 3-Coat 2-Bake method, enhance product durability and visual appeal, providing customers with higher-quality products. Additionally, data analytics plays a key role in demand forecasting, optimizing manufacturing schedules, avoiding overproduction, and ensuring timely order fulfillment. Companies adopting automation and cutting-edge technology report a 25-30% increase in production efficiency and maintain consistent product quality. By integrating advanced technologies, manufacturers can produce high-quality products efficiently, staying competitive in an ever-evolving market.
R&D Investment for Product Innovation
Investing in research and development (R&D) is an effective way for ACP manufacturers to maintain high-quality standards while cutting costs. Developing new materials or production techniques can lead to improvements in the strength, durability, and fire resistance of ACPs, allowing manufacturers to offer superior products at competitive prices. R&D can also drive innovation in production processes, leading to reduced material usage, lower energy consumption, and more sustainable manufacturing practices. Companies that dedicate resources to R&D can not only improve their product offerings but also adapt to changing market needs, gaining a strategic advantage in a competitive landscape.
Collaborative Partnerships for Cost Reduction
Collaborating with suppliers, distributors, and other key stakeholders in the supply chain can lead to cost savings and improved quality. Manufacturers can negotiate better pricing for raw materials by forming long-term partnerships with trusted suppliers. Additionally, joint ventures or partnerships with technological innovators can provide access to advanced equipment and processes at a lower cost. By working closely with suppliers to optimize the supply chain and ensure a steady flow of materials, manufacturers can reduce inventory costs, improve lead times, and maintain a consistent product quality. These partnerships create an ecosystem of cost-effective and quality-focused solutions, further enhancing profitability and operational efficiency.
Conclusion
Innovation, advanced technology, and strategic planning are essential for balancing quality and cost-effectiveness in ACP manufacturing. By focusing on waste reduction, optimizing inventory, integrating continuous production lines, maintaining machinery, and leveraging cutting-edge technologies, manufacturers can achieve operational excellence. These strategies not only ensure cost efficiency but also elevate product quality, helping companies meet consumer demands while maintaining their position as reliable market leaders. Adopting these practices is important for long-term success, profitability, and sustainable growth in today’s fast-evolving industry.
About the Author;
Rajesh Shah, Chairman and Managing Director (CMD) of Euro Panel Products Limited, also known as Eurobond ACP. He has been on the board for more than 10 years and has 35 years of business experience. Shah is responsible for the company’s management, finance, and strategy.