The growing world population and the rising need for housing consequently leads to a heavier environmental impact due to the high percentage of carbon emissions that take place during cement production. Therefore, there is as much scope and potential for innovation in this field. Green cement is one such innovation. It is a form of cement produced with the help of a carbon-negative manufacturing process. In other words, cement is produced as the final product of a technologically advanced process, utilizing the sludge and other waste materials from factories along with naturally occurring components making it more tensile and with higher compressive strength as compared to the conventional cement categories. Keeping in mind that cement manufacturing leads to deadly gaseous release and CO2, cement production cannot be stopped. It is unimaginable to think of a world without cement production in this fast-moving world. Green Cement can be the solution to cut down the emissions produced in the conventional manufacturing process of cement.
Its production releases fewer carbon leads to a reduction of landfills and majorly contributes to controlling the pollution levels limiting the hazardous consequences leading to serious environmental damage. There are multiple technologies and mechanisms for green cement manufacture, patented by different manufacturing agencies. In the manufacturing process of green cement, carbon dioxide emitted during the manufacturing process is significantly reduced. Green cement can reduce the carbon footprint by 40%. Apart from reducing carbon dioxide emissions, the green cement manufacturing process also helps maintain cement strength. Composed of calcined clay and powdered limestone, green cement has desired characteristics such as reduced porosity and enhanced mechanical strength.
Advantages of green cement
Compared with traditional cement, green cement functions better requires less natural materials in production and releases less carbon dioxide. It also protects land from becoming a dumping ground and ultimately being destroyed. Apart from fly ash, green cement also uses blast furnace slag which can produce harmful environmental effects if it is simply discarded. The materials used in the traditional cement manufacturing process require large amounts of natural gas/coal for heating purposes. Because green cement already contains industrial by-products, the energy needed in production is greatly reduced. Also, unlike Portland cement, green cement is more resistant to changes in temperature, therefore reducing the costs associated with both heating and cooling. Green cement does not require as much heat during its production, releasing up to 80% less carbon dioxide.

Its advantages include;
- Reduce greenhouse gas emission i.e., carbon dioxide emission from the cement industry.
- Limits the use of natural resources such as limestone, clay, shale, natural river sand, natural rocks that are being consumed for making conventional concrete.
- Makes use of industrial waste such as fly ash, silica fume, and last furnace that may require several acres of land to dispose of.
- Requires less energy in production
- Withstands temperature fluctuations and hence decreases costs related to both heating and cooling
- Durable and fire-resistant
- Energy Conserving:
Different types of green cement
Based on several advanced technological attempts, various types of Green Cement are produced. That includes carbon-negative cement, reduced carbon production practices, geopolymers, and modern concrete products.
Magnesium oxychloride cement
Magnesium oxychloride cement is one of the strongest cement possessing certain advantages over Portland cement. It is a high strength, high bonding and quick setting cement with high early strength. It does not require humid curing. It consists of magnesium oxide (MgO) powder and a concentrated solution of magnesium chloride (MgCl2). Having the tremendous load-bearing capacity, it can withstand vibrations from heavy cast iron wheel movement without the least trace of cracks or fissures. It is used in industrial floorings, ship decks, railway passenger coach floorings, hospital floors, ammunition factory floors, missile silos and underground armament factories and bunkers. This type of green cement has enhanced setting time and also has high compressive strength, with the use of additives such as fly ash, the strength, as well as the durability of MOC, can be increased significantly.
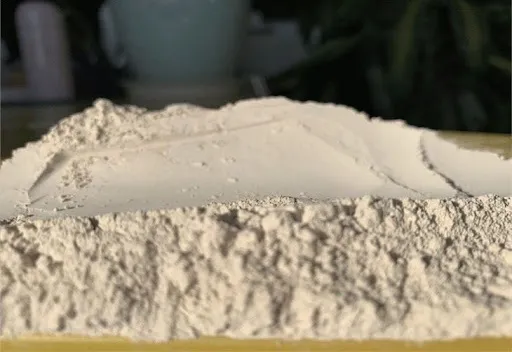
Ekkomaxx Cement
Ekkomaxx Cement is composed of 95% fly ash and 5% renewable liquid additives. Its main features are high early strength, resilience, crack resistance, low chloride permeability, sulphate attack resistance, durability and resistance to freezing and thawing.
Geopolymer cement
Geopolymer cement is a binding system that hardens at room temperature. It relies on minimally processed natural materials or industrial byproducts to significantly reduce the carbon footprint of cement production, while also being highly resistant to many common concrete durability issues. Geopolymer concrete has significant advantages over standard concrete. It is much more long-lasting than standard concrete and requires little repair, thus saving huge amounts of money that would otherwise have to be spent on repairing and maintaining concrete based infrastructure.
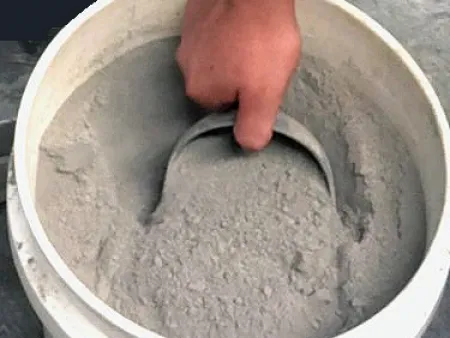
Calcium sulfoaluminate cement
Calcium sulfoaluminate (CSA) is an innovative alternative to Portland cement for tunneling and underground construction projects. It has been used for construction on above-ground projects for years and exhibits properties uniquely suited to the harsh environment of underground construction. The primary advantage of CSA cements is that concretes, grouts and mortars made with CSA Cement, can easily be formulated to achieve compressive strengths over 5000 psi in just a few hours. With CSA Cement is possible to attain the desired26 to 28 day strength in 24 -hours. Rapid setting and high early strength gain is critical in situations where an airport runway, a bridge repair or a damaged freeway must be returned to service in a very short amount of time.
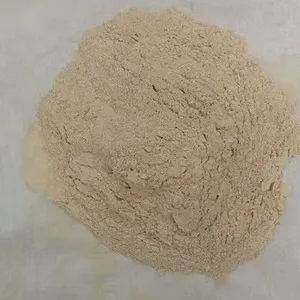
Sequestrated Carbon Cement
Sequestrated Carbon Cement is manufactured by use of CO2-rich gases filtered through seawater. The calcium and magnesium are stripped from the seawater and react with CO2 to produce high-quality cement, which is white, air-permeable and stronger than regular OPC. concrete producers mineralize carbon waste and inject it into concrete. The CO2 is sourced from industrial emitters. They collect, purify, and distribute the CO2 to concrete plants, which store it in pressurized tanks until it is ready to use. Once injected into the wet concrete mix, the CO2 reacts with calcium ions from cement to form a nano-sized mineral, calcium carbonate, which then becomes embedded in the concrete. This makes the concrete stronger. Aside from increased strength, CO2 does not impact the concrete properties. Set-time, slump, workability, air content and temperature.
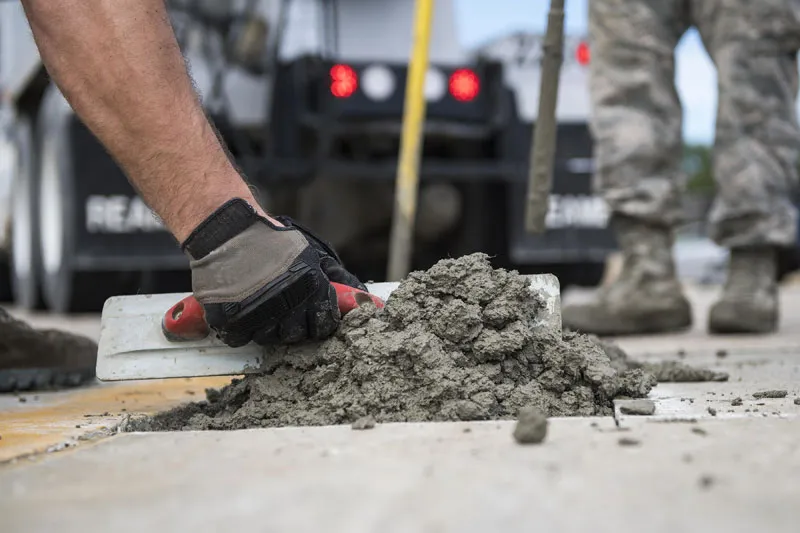
Ferrocrete cement
Ferrocrete cement is manufactured using reinforced mortar or plaster (lime or cement, sand, and water) applied over an “armature” of metal mesh, woven expanded metal, or metal-fibers, and closely spaced thin steel rods such as rebar. It is composed of hydraulic-cement mortar reinforced with closely spaced layers of continuous and relatively small wire mesh. The mesh may be made of metallic or other suitable materials. It has a very high tensile strength-to-weight ratio and superior cracking behavior in comparison to conventional reinforced concrete. Unlike conventional concrete, ferrocrete cement reinforcement can be assembled into its final desired shape and the mortar can be plastered directly in place without the use of a form.
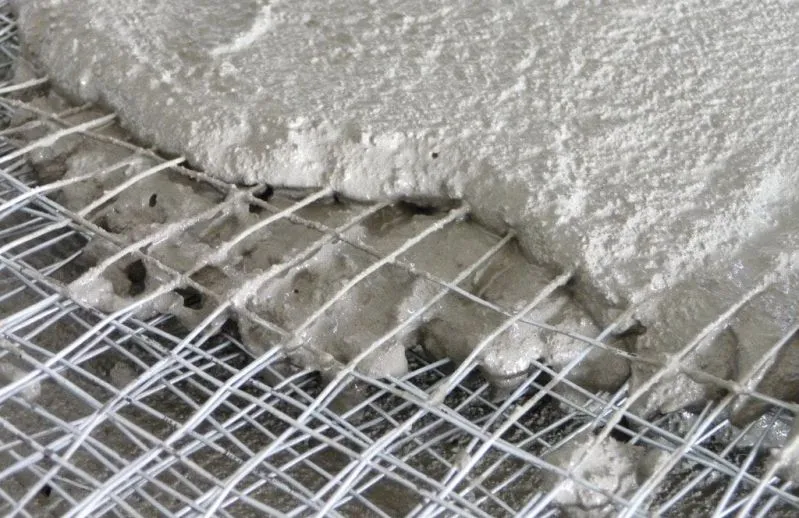
Conclusion
Green cement market demand in India is driven by growth in awareness related to reduction in carbon emissions and its detrimental effect on the environment. In addition, green cement provides better functionality, requires less natural materials during production, and releases less carbon dioxide than traditional cement. Green cement will enable eco-friendly construction – a big step towards saving the planet. Green cement is a revolutionary product that is manufactured in an eco-friendly manner and becomes the foundation of sustainability. Understanding its advantages, many developers today have gradually shifted towards using greener cement. Urban development schemes and efforts to adhere to environmental agency guidelines have also led to its increased demand. The companies are inclined to develop energy-efficient construction. Various companies are undertaking R&D activities to improve the technology. They have utilized numerous raw materials to obtain a cost-effective green cement mixture. Thus, such initiatives and advancements by manufacturers are expected to provide lucrative opportunities for market growth.