There has been an increased focus on manufacturing high-performance concrete products by adding various fibers, in different proportions. The fibers like glass, carbon, polypropylene and aramid fibers provide improvement in concrete properties like tensile strength, fatigue characteristic, durability, shrinkage, impact and erosion resistance. Because of such characteristics, Fiber Reinforced Concrete has found many applications across projects. One such product is Glass Fiber Reinforced Concrete (GFRC). It is a composite, consisting of portland cement, fine aggregate, water, acrylic polymer, alkali-resistant glass fiber reinforcement and additives. GFRC is a lightweight, durable material that can be cast into nearly unlimited shapes, colors and textures It is mainly used in exterior building facade panels and as architectural precast concrete. GFRC has more flexural strength than conventional unreinforced concrete.
The popularity of glass-fiber reinforced concrete (GFRC) has grown in the past few years due to its versatility, strength and relative ease of manufacture. GFRC is thinner, which makes them much lighter than thicker conventional reinforced concrete. The principal factors affecting strength properties of GFRC are fiber content, composite density, fiber orientation, fiber length and type of cure. All of these are impacted by the fiber reinforcement.
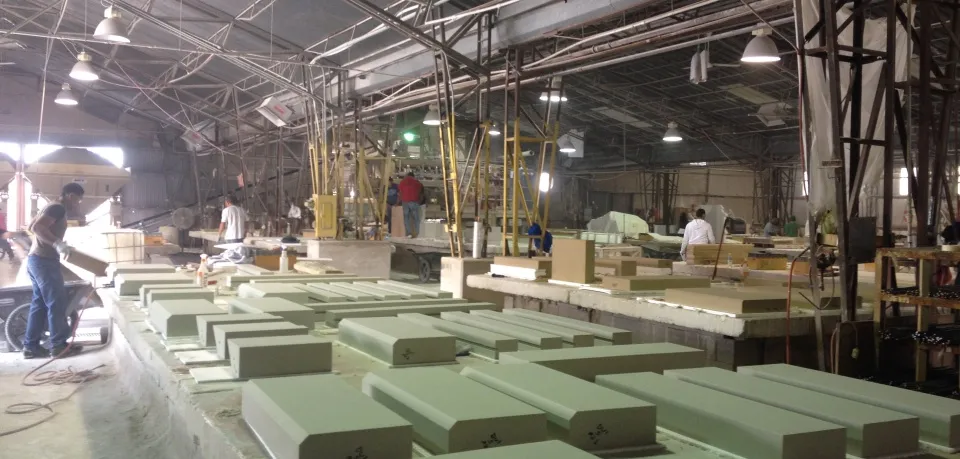
GFRC production methods;
There are various production methods for GFRC manufacturing as explained below;
The spray-up process – in this process the mortar is produced separately from the fibers, which are mixed only at the jet of the spray gun. The glass fiber strands are cut within the spray gun to the required size, using a matrix without fibers, The fluid concrete mixture is sprayed into the forms. The process uses a specialized spray gun to apply the fluid concrete mixture and to cut and spray long glass fibers from a continuous spool at the same time. Spray-up creates very strong GFRC due to the high fiber load and long fiber length,
The pre-mixture process – in this process cement matrix is firstly produced and pre-cut glass fibers are then mixed. Production with pre–mix GFRC may involve several procedures such as injection and vibration, pressing, or shotcreting. The Premix process is further broken down into various production techniques such as spray premix, cast premix, pultrusion and hand lay-up.
Hybrid process – This is an alternative process that involves using a hopper gun to spray the face coat. The fiber loaded backer mixture is often poured or hand packed, just like ordinary concrete. Once the thin face mixture is sprayed into the forms it is allowed to stiffen up before the backer mixture is applied so that prevents the backer mixture from being pushed through the thin face mixture
Filament Winding process – This process involves fiber roving strand passes over several round steel bars placed below the level of a specially modified mortar mix before being wound onto a mandrel. Various continuous fiber cement based composites consisting of unidirectional lamina, cross ply and angle ply laminates can be manufactured with a typical AR glass content
Filter-press process – In this process first a wet fibrous mix is produced with an excess of water. Then this mix is charged into a mold, which has a perforated plate at the base. A filter material is laid on top of the mold base. The mix is then pressed by a top plate, which squeezes out the excess water through the base of the mold and through a small gap between the top plate and the sides of the mold. The filter press process is well suited for mass production of products having simple or complex shapes.
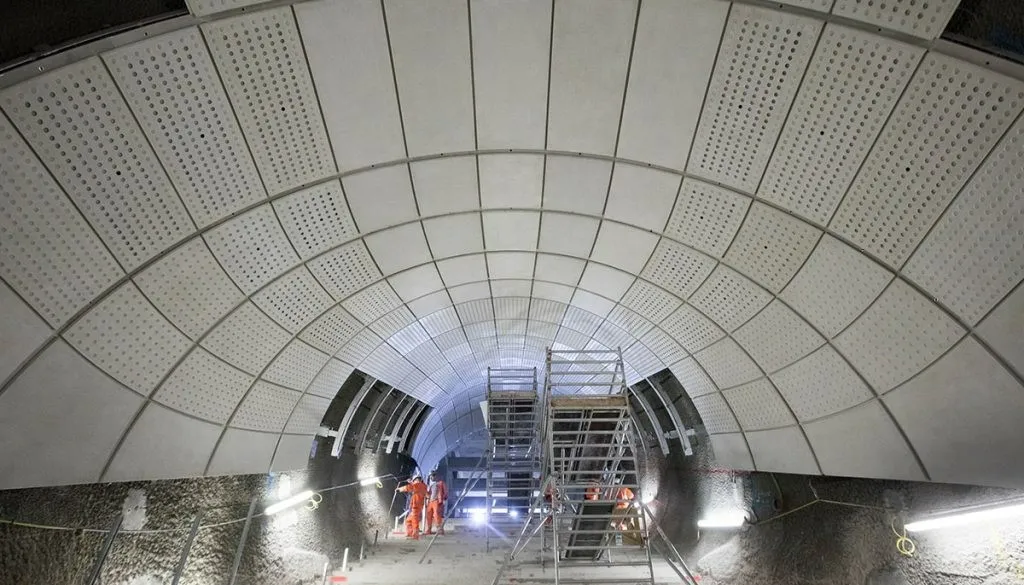
Advantages of GFRC
Since GFRC is reinforced internally, there is no need for other kinds of reinforcement, which can be difficult to place into complex shapes. Its advantages include;
- A high tensile strength than steel
- Non-combustible so it will not burn
- Thinner and stronger than plain concrete.
- Lightweight and tough materials also reduce the transportation expense
- Allow for flexibility in design and reduce the impact on the environment
- Improved strength, increases the capacity to bear seismic loads
- Less vulnerable to weather effects and it is more resistant to freeze-melting than normal concrete
- High flexural strength as high as 4000 psi and it has a very high strength-to-weight ratio
- Expensive equipment is not needed for poured or vibrated GFRC with a face coat
- Doesn’t crack easily-it can be cut without chipping
- Uses less cement than equivalent concrete and also often uses significant quantities of recycled materials
- GFRC concrete can be cast in thinner sections and is therefore as much as 75% lighter than similar pieces cast with traditional concrete
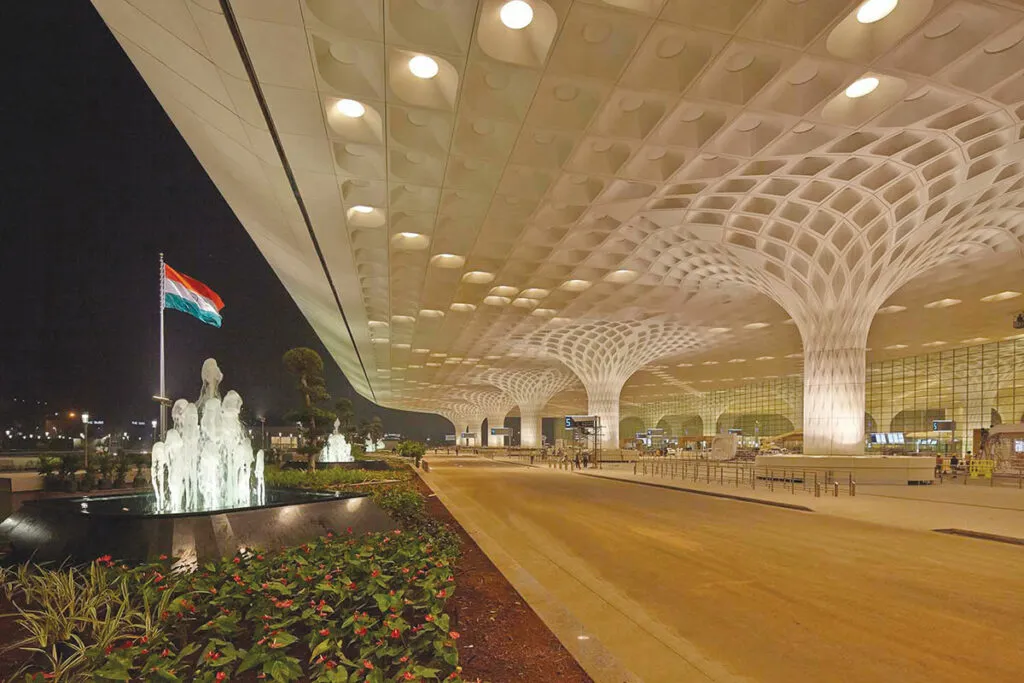
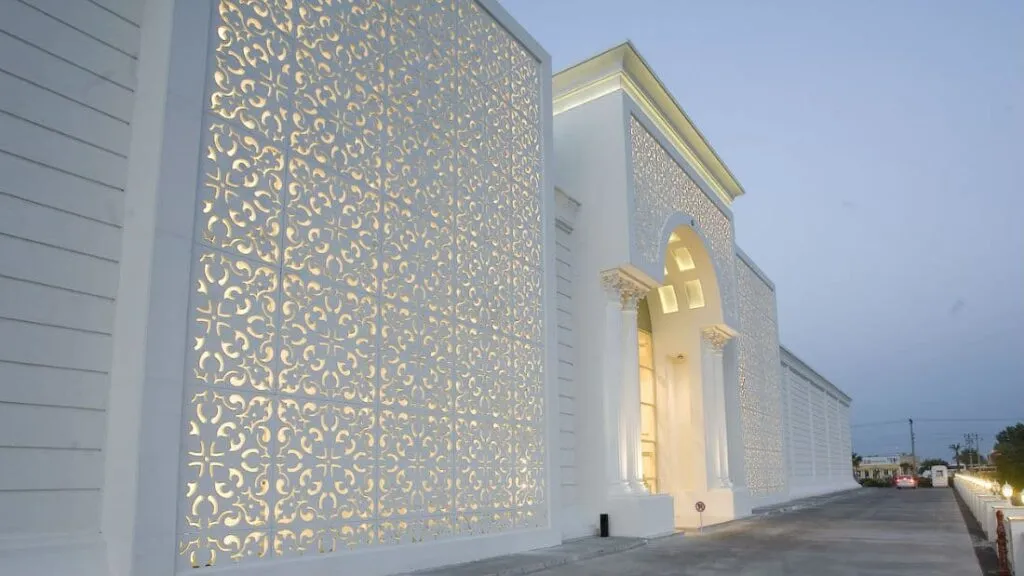
GFRC for architectural design
Applications of GFRC
GFRC can be used wherever a light, strong, weather resistant, attractive and fire retardant material is required. GFRC can be used along spandrels, column covers, soffits, cornices, brackets, quoins, railings, pilasters, copings, domes, etc. Landscape and hardscape use include site furnishings, planters, bollards, urns, tables and fountains. GFRC is also used in historical restorations and renovations, for the replication of building ornaments of terra-cotta, carved stone and even wood. Its application includes;
- Architectural Cladding
- Landscaping
- Roofing
- Walls and windows
- Building Renovation
- Flooring and foundations
- Modular building:
- Bridges and tunnels
- Water and Drainage:
Conclusion
Product manufacturers are actively focused on the research & development pertaining to the production of glass fibers for reinforcing purposes and are laying increased emphasis on the production of advanced reinforcing glass fibers with varying sizes and project needs. Rising demand for glass fibers in various commercial, residential, and civil constructions are anticipated to benefit market growth. Product benefits including high tensile, flexural, and compressive strength are projected to promote its demand as a reinforcement material in concrete. This helps in increasing the strength of the concrete, thereby propelling its demand in the construction of countertops, fireplace surrounds etc. There is also increasing demand for remodeling and renovation activities in the residential construction sector that is fueling the demand for glass fiber reinforced concrete.