A dry mix mortar plant is used for the manufacturing of pre-mixed dry mortar products by blending cement, sand, and additives in precise proportions. The importance of a dry mix mortar plant lies in its ability to produce consistent, high-performance mortar in large quantities, reducing the need for on-site mixing and improving construction efficiency. This consistency enhances the durability and strength of building materials, ensures better adhesion and bonding, and minimizes construction waste. By streamlining the production process and providing reliable mortar, these plants contribute significantly to the overall quality and cost-effectiveness of construction projects.
A dry mix mortar plant is used for:
- Masonry Work: Producing mortar for laying bricks, blocks, and stone.
- Plastering: Creating smooth and durable finishes on walls and ceilings.
- Tiling: Manufacturing adhesives for securing tiles to floors and walls.
- Repairs: Making repair mortars for patching and fixing damaged surfaces.
- Floor Levelling: Manufacturing self-levelling compounds to create even floors before additional flooring is installed.
- Exterior Coatings: Producing render for protective and decorative applications on building exteriors.
- Specialty Mortars: Creating customised mixes for specific construction requirements, such as fire-resistant or waterproof mortars.
Components of dry mix mortar plant
- Raw Material Storage: Facilities for storing cement, sand, and additives in bulk.
- Weighing and Batching System: Equipment for accurately measuring and mixing raw materials.
- Mixing System: Machinery, such as twin-shaft or drum mixers, for blending materials.
- Drying and Cooling System: Ensures proper consistency and moisture content of the mix.
- Packaging System: Equipment for packing finished mortar into bags or bulk containers.
- Control System: Automated systems for monitoring and controlling production.
- Dust Collection System: Manages and reduces dust emissions to improve safety and compliance.
- Transportation System: Conveyors and mechanisms for moving materials between production stages.
Advantages of dry mix mortar plant
- Ensures uniform and consistent quality of mortar products.
- Optimizes production processes, reducing time and labour costs.
- Eliminates the need for on-site mixing and preparation.
- Produces mortars that enhance the strength and longevity of structures.
- Minimizes material waste through precise batching and mixing.
- Speeds up construction with ready-to-use, pre-mixed mortar.
- Reduces risk of contamination and variability with controlled production.
- Cuts overall costs by improving material usage.
- Provides the capability to produce various mortar types and custom mixes.
- Lowers labor costs by decreasing the need for on-site mixing.
- Enhances safety by reducing the handling of raw materials and dust.
- Cuts down on dust emissions and waste through efficient production methods.
Dry mix mortar plant types
Batch Plants
Batch Plants operate by mixing materials in discrete batches, allowing for the production of various mortar formulations tailored to specific requirements. They are equipped with advanced weighing systems and high-efficiency mixers to ensure uniform consistency and quality in each batch. The ability to easily adjust mix recipes and production volumes makes batch type plants ideal for smaller-scale projects or applications requiring specialized mortar mixes. This adaptability is particularly beneficial for custom residential projects, renovation works, and scenarios where frequent changes in mortar specifications are needed.

Continuous Plants
Continuous Plants are designed for large-scale, uninterrupted production of dry mix mortar. These plants feature continuous mixing mechanisms and automated material handling systems that ensure a steady flow of mortar with consistent quality. The automated processes in continuous type plants facilitate high efficiency and output, making them suitable for major construction projects that demand large quantities of high-quality mortar. They are commonly used in the construction of high-rise buildings, commercial complexes, and extensive infrastructure projects where uniformity and high production rates are essential.
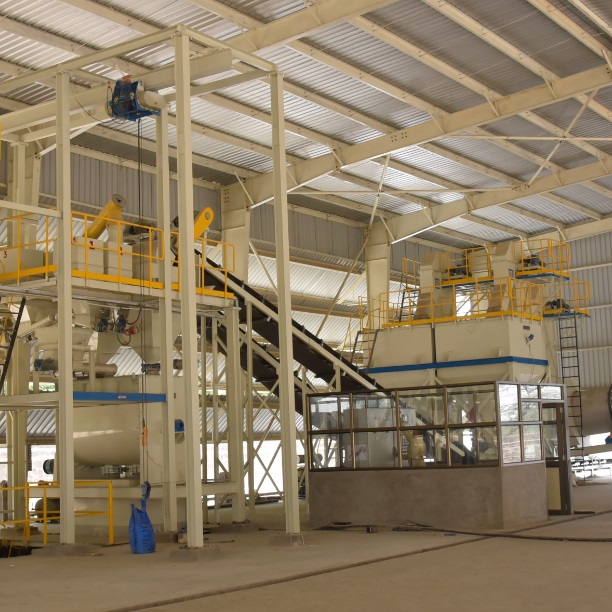
Mobile Plants
Mobile Plants offer the flexibility of on-site production, making them particularly useful for projects in remote or difficult-to-access areas. These portable units are compact and self-contained, featuring mixing systems that can be easily transported and set up at the construction site. Mobile plants enable the production of fresh mortar directly where it is needed, reducing transportation costs and logistical challenges associated with delivering pre-mixed mortar. This capability is advantageous for large construction sites or projects located in areas with limited access, where on-site production helps in managing specific project needs efficiently.

Semi-Automatic Plants
Semi-Automatic Plants integrate both manual and automated processes to produce dry mix mortar. These plants combine automated systems for batching and mixing with manual controls for certain aspects of production, offering a balanced approach between efficiency and cost-effectiveness. Semi-automatic plants are suited for medium-sized projects where a mix of automation and manual oversight can effectively handle production needs. They provide an intermediate solution that improves efficiency over fully manual systems while remaining more affordable than fully automatic plants. This makes them ideal for mid-sized commercial and residential construction projects.

Fully-Automatic Plants
Fully Automatic Plants are the most advanced type of dry mix mortar plant that uses automation systems to handle every stage of the production process. These plants feature integrated control software, high-capacity mixers, and automated packaging lines, which ensure precise control, high consistency, and operational efficiency. Fully automatic plants are designed for high-demand environments where large quantities of uniformly mixed mortar are required. They are best suited for large-scale commercial projects, significant residential developments, and major infrastructure works, where the scale and complexity of production necessitate advanced automation to maintain quality and efficiency.

Why the demand for dry mix mortar plants in India?
The demand for dry mix mortar plants is growing due to their efficiency and consistency in modern construction. Key drivers include:
- Increased Construction Activity: High demand for efficient mortar solutions.
- Consistency and Quality: Uniform quality compared to site-mixed mortars.
- Efficiency and Speed: Reduces construction time and labor costs.
- Reduced Environmental Impact: Supports sustainable practices with lower waste and energy use.
- Urbanization and High-Rise Construction: Meets needs for large-scale and high-rise projects.
- Technological Advancements: Enhanced automation and precision in production.
Conclusion
Dry mix mortar plants are essential for modern construction, providing consistent, high-quality mortar that enhances efficiency and reduces costs. They streamline production processes and support sustainable practices, making them crucial for a wide variety of projects. As technology evolves, these plants will remain key to achieving superior construction quality and performance.
Image Source: apolloinffratech.com, neptune-india.com, schwingstetterindia.com, kiconequip.com, coninfra.in