Earthmoving and concrete testing are important in construction projects, especially during their initial stages. Effective earthmoving operations establish the groundwork for proper site preparation, grading, and excavation, thereby laying the foundation. Equally important is precise concrete testing, ensuring the structural integrity of roads, bridges, and other structures. Thorough testing is imperative to verify that the concrete used adheres to specified standards, ensuring the durability of construction projects. Over time, efforts have been made to modernize these practices, with new technologies transforming conventional methods.
In line with this evolving trend, engineers from High Speed 2 (HS2), in collaboration with the main contractor EKFB (Eiffage, Kier, Ferrovial, Bam) and equipment supplier Finning, have introduced the DIGital Graphical Earthworks Reporting program known as Digger.
About HS2 Project
HS2is a major railway project in the United Kingdom, aimed at enhancing connectivity by creating a high-speed rail link between London and the North of England. The project involves building new tracks to accommodate faster trains, reducing travel times and increasing capacity.
Efficient Earthmoving with Digger Program
The Digger program is an advanced technology implemented in earthmoving operations, utilizing electronic weight sensors on 700 machines.
Operating in real-time through Finning’s Cubiq platform, it collects and leverages data to monitor and optimize extensive earthmoving activities, particularly within the 80km central section of the HS2 project. This system provides real-time digital insights, allowing for the identification and addressing of inefficiencies on the go.
EKFB Earthworks Director Mark Harrington emphasizes its significance, referring to it as a game changer for earthmoving operations. The program has resulted in substantial cost savings, notably attributed to reduced fuel consumption and a commendable decrease in carbon emissions.
The impact of this technology is profound, resulting in a reported £25 million in cost savings for the project. Notably, a significant portion of these savings is attributed to the reduction in fuel consumption, leading to a commendable decrease in carbon emissions.
EKFB Earthworks Director Mark Harrington underscores the transformative nature of Digger, emphasizing its ability to identify and address inefficiencies in real-time, enabling immediate measures to maintain optimum efficiency. By providing data it enables identification of where inefficiencies are occurring in real time, and can implement immediate improvement measures to ensure optimum efficiency across operations.
To demonstrate its usage, HS2 Ltd gives the example of someone at EKFB’s Brackley site base monitoring the read out from 60 excavators in use. If the system observes an excavator idling with a load, waiting for a dump truck, they promptly alert the EKFB team.This allows for efficient fleet adjustments, ensuring smooth operations. Moreover, the system assists the on-site team in quickly identifying and resolving any congestion points on site roads that might impede haulage operations.
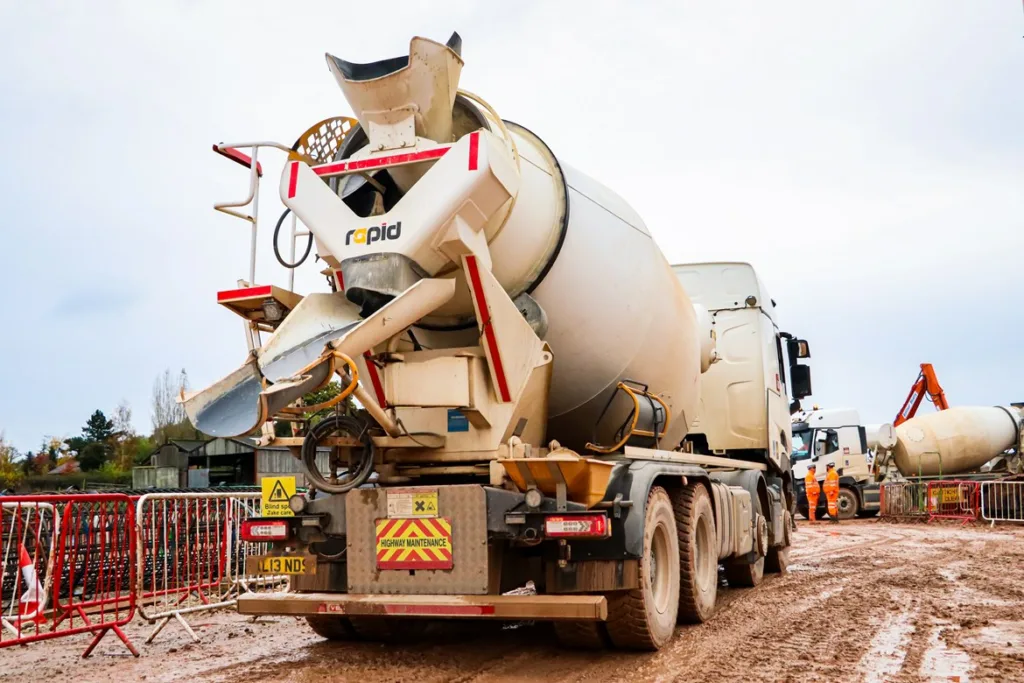
Concrete Testing Innovation with Verifi Technology
In parallel, the Leamington Spa to Birmingham section of HS2, under the management of main works contractor BBV (Balfour Beatty Vinci), has successfully introduced the cutting-edge Verifi technology. Representing a paradigm shift in the monitoring, measurement, and management of fresh concrete properties during transportation, Verifi integrates sensors on concrete mixer trucks linked to proprietary algorithms. This integration eliminates the need for manual consistency and temperature testing of fresh concrete.
The technology enhances productivity and efficiency by providing clear digital readouts. This eliminates delays tied to traditional sampling and testing processes, enabling better scheduling and reducing potential bottlenecks in the construction timeline.
Advantages;
- Enables real-time monitoring of fresh concrete properties during transportation, providing instant insights into its consistency and temperature.
- The technology utilizes on-truck sensors linked to proprietary algorithms, ensuring accurate and precise measurements, surpassing traditional manual testing methods.
- Eliminates concrete waste that would have been generated from manual sampling and testing, contributing to environmental sustainability and cost savings.
- With less plant-person interface and manual handling on-site, it improves safety conditions for workers involved in concrete transportation and delivery.
- Provides clear digital readouts, eliminating delays associated with traditional sampling and testing processes.
- GPS tracking of vehicles equipped with VERIFI® optimizes planning and coordination, improving the overall management of concrete delivery and logistical processes on-site.
- The integration of a fully digital monitoring and reporting system fosters transparent communication between producers and customers.
- Elimination of concrete waste which would have been produced from manual sampling and testing.
In a full-scale trial involving 20,000m3 of concrete, the accuracy and reliability of the technology were evident. HS2 Ltd has now approved its implementation across additional sites on the project. One key advantage of Verifi is the reduction in concrete waste associated with manual sampling and testing. The system is estimated to cut up to 1,500t of carbon when introduced across BBV’s sites.
Collaboration and Future Impact
Steve Phipps, BBV Head of Materials Engineering, anticipates significant benefits as the implementation of Verifi progresses across HS2 sites in the Midlands. This digital solution, born out of collaborative efforts with supply chain partners, not only promises environmental advantages but also marks a monumental step forward in supplying quality-assured concrete to meet the demands of the HS2 project.
Joseph Hartley, Aggregate Industries HS2 technical manager, views the collaboration with Verifi as a monumental step change in supplying quality assured concrete. The system’s visibility into product monitoring and vehicle movements brings unprecedented benefits.
HS2 materials and durability lead Jon Knights sees this innovation as a fantastic example of collaborative efforts yielding cutting-edge technologies. The integration of digital surveillance solutions aligns with HS2 Ltd’s ambitions to reduce carbon and pave the way for a new era in the construction industry.
Conclusion
Efficient earthmoving and advanced concrete testing technologies are reshaping construction practices in the HS2 project. Digger and Verifi exemplify the fusion of cutting-edge technologies, real-time monitoring, and collaborative efforts, promising cost savings, environmental benefits, and improved safety conditions. These innovations not only enhance the efficiency and reliability of transportation-related construction projects but also pave the way for a more sustainable future in the construction industry.
References- newcivilengineer.com, mediacentre.hs2.org.uk,rail-leaders.com