A vibratory roller is a heavy construction machinery used in road construction and compaction tasks. It has a vibrating drum that compacts soil, asphalt, or other materials to create a smooth and dense surface. The vibrations help in settling the material and reducing air gaps, resulting in a more stable and durable road or foundation.
Vibratory rollers typically consist of several key components:
- Drum: The drum is the main component that comes in contact with the material being compacted. It can be smooth or have patterns to achieve different compaction results.
- Vibration System: This system includes the mechanisms that generate vibrations in the drum. It enhances compaction efficiency by reducing air voids in the material.
- Engine: The engine provides the power needed to drive the roller and operate its various components.
- Frame: The frame supports the drum, engine, and other components, providing structural integrity to the roller.
- Transmission: The transmission system transfers power from the engine to the roller’s wheels, allowing it to move forward or backward.
- Operator’s Platform: This is where the operator controls and steers the roller. It includes a seat, controls, and sometimes a protective canopy.
- Water System: Many vibratory rollers have a water system to moisten the material being compacted, aiding in compaction and reducing dust.
- Hydraulic System: Hydraulic components control various functions of the roller, such as steering and adjusting the drum’s pressure.
These components work together to efficiently compact different types of materials during construction projects.
Vibratory rollers offer several advantages in construction and compaction:
- Efficient Compaction: The vibrating drum efficiently compacts materials by reducing air voids, resulting in a denser and more stable surface.
- Increased Productivity: Vibratory rollers can cover larger areas quickly, leading to improved productivity on construction sites.
- Versatility: They can be used for a variety of materials, including soil, asphalt, and aggregates, making them versatile for different construction projects.
- Better Surface Finish: The vibrations help achieve a smoother and more uniform surface finish, enhancing the quality of roads and foundations.
- Time Savings: Due to their high compaction efficiency, vibratory rollers often reduce the number of passes needed to achieve the desired compaction, saving time during construction.
- Improved Stability: The compaction provided by vibratory rollers enhances the stability and load-bearing capacity of the compacted material, contributing to the longevity of structures.
- Adaptability to Various Conditions: Vibratory rollers can be equipped with features like adjustable amplitude and frequency, allowing them to adapt to different soil types and conditions.
Types of vibratory rollers
1. Smooth Drum Rollers:
Smooth drum rollers feature a solid steel drum, making them well-suited for compacting granular soils and asphalt surfaces. Their design ensures the creation of a flat and even surface, making them a staple in road construction projects where a smooth finish is paramount. These rollers are particularly effective in achieving the necessary compaction for asphalt layers, contributing to the longevity and stability of the road surface.

2. Padfoot Rollers (Sheepsfoot Rollers):
Padfoot rollers, also known as sheepsfoot rollers, differentiate themselves with segmented pads on their drum surface. This design is tailored for cohesive soils, offering a kneading action that is highly effective in compacting clay and silt. Commonly employed in road construction and earthwork projects, padfoot rollers excel in situations where cohesive soils demand specialized compaction methods, ensuring a solid foundation.
3. Pneumatic Rollers:
Pneumatic rollers stand out with their rubber tires or pneumatic rollers, providing versatility for both soil and asphalt compaction. The tires introduce a kneading action to the compaction process, making them adaptable to various materials. This flexibility, combined with their ability to cover larger areas efficiently, makes pneumatic rollers valuable in projects with diverse compaction requirements, from road construction to general earthwork.
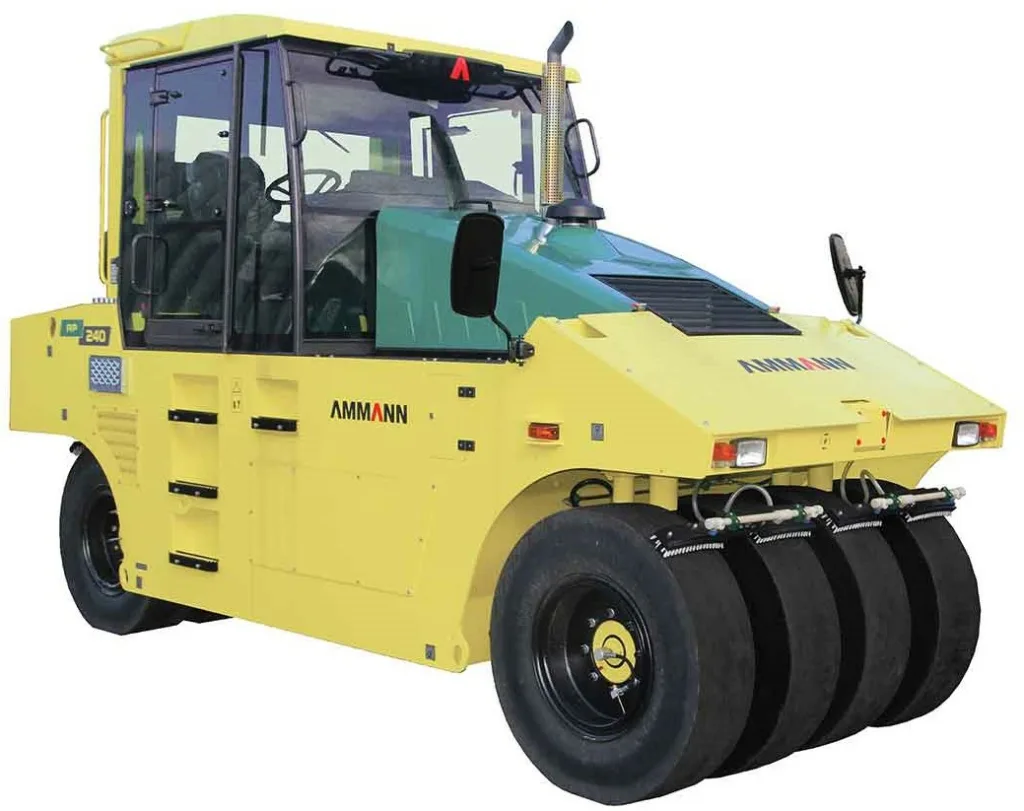
4. Tandem Rollers:
Tandem rollers, featuring two smooth or differently surfaced drums, are designed for comprehensive compaction, addressing both base and surface courses in road construction. The dual-drum configuration enhances their effectiveness, ensuring uniform compaction throughout the layers. These rollers play a crucial role in achieving the desired density and stability in road surfaces, contributing to the overall quality and longevity of the constructed infrastructure.

5. Combination Rollers:
Combination rollers integrate features of both smooth drum and pneumatic rollers, offering a versatile solution for projects with diverse compaction needs. Their adaptability makes them valuable in scenarios where different types of soils or materials require varying compaction methods. Construction projects benefit from the efficiency and flexibility provided by combination rollers in achieving optimal compaction results.
These types of vibratory rollers cater to specific construction needs, providing efficiency and precision in achieving desired compaction levels for different types of soils and materials.
6. Three-Point Articulated Rollers:
Three-point articulated rollers are characterized by their center articulation, enhancing maneuverability. Suited for tight spaces and uneven terrain, these rollers navigate construction sites with flexibility. Their design allows for effective compaction in challenging environments, making them particularly useful in construction projects where accessibility is limited or the terrain is irregular.

7. Walk – Behind Vibratory Roller
Walk-behind vibratory rollers are designed for the compaction of all sorts of soils as well as for the compaction of asphalt. Modern machines feature an optimal combination of centrifugal force, vibration frequency and static weight, resulting in excellent compaction effect. Travel of the machine is ensured by the hydrostatic system, consisting of a regulating hydraulic pump and a hydrometer. Travel speed and direction can be controlled infinitely by the travel control level, within the range from zero to maximal speed. The engine, hydraulic pump, hydraulic oil tank, centrifugal clutch and water tank of sprinkling are located at the base plate which is isolated to the vibrating part of the machine by four rubber mounts. It has a very compact design and offers great visibility to the operator at any angle which allows precise work near to walls and sidewalks.

8. Light Tandem Vibratory Roller
Light tandem vibratory rollers work perfectly against curbs and other obstructions and eliminate the need for special edge compaction efforts. Modern models come with double-drive and double-vibration is standard and helps deliver optimum compaction results. An electronic drive lever makes for smooth starting and stopping and is among the reasons the roller is popular with operators. Other operator benefits include a rubber-mounted platform that limits vibration and an intuitive instrument panel to help make even an inexperienced operator successful. Hybrid models feature vibration-insulated operator’s platforms with intuitive controls and a system for smooth starts and stops on asphalt.
Application of vibratory rollers
Vibratory rollers find diverse applications across construction and infrastructure projects due to their efficiency in soil and material compaction. Some key applications include:
- Road Construction
- Earthwork and Site Preparation
- Landfill Construction
- Airport Runways and Taxiways
- Railway Track Construction
- Residential and Commercial Building Construction
- Trench Backfilling
- Parking Deck Construction
- Sports Field Construction
- Infrastructure Maintenance and Repairs
Conclusion
Vibratory rollers play a pivotal role in modern construction, offering unparalleled efficiency in soil and asphalt compaction. These specialized machines have become indispensable in road construction, pavement maintenance, and various infrastructure projects. By utilizing dynamic forces generated by vibrating drums, vibratory rollers enhance the density of materials, ensuring a stable and durable foundation. As technology continues to advance, vibratory rollers remain at the forefront of construction equipment, contributing significantly to the development of robust and long-lasting structures across diverse industries.
Image Source: casece.com, ammamm.com/en-in, wirtgen-group.com/ocs/en-in/, volvoce.com/india/en-in/, accelinfra.com