Utility tunneling is a trenchless construction method used to construct underground tunnels, specifically designed to protect various utility line systems like pipes, cables, and conduits used for services such as water supply, sewage, electricity, telecommunications, heating, and cooling. These tunnels shield vital utility lines from weather and physical interference, reducing the risk of service disruptions.
The primary roles of utility tunneling in infrastructure include:
- Consolidating Utilities: organise utility lines, reducing the need for surface-level installations.
- Protection: protects against extreme weather, vandalism, and accidents.
- Maintenance and Repairs: makes it easier to access and maintain utility lines.
- Safety: enhance safety by reducing the risk of accidents or interference with utility lines.
- Urban Planning: allow for better urban planning by freeing up space above ground for parks, roads, buildings, and other essential urban features.
Utility tunneling construction process
The method for utility tunneling involves skilled workers entering the designated borehole area. They employ liner plates to both protect themselves and provide stability to the tunnel, ensuring the safety of those involved in the construction process. To maintain stability during tunnel excavation and utility line installation, various temporary support structures are used. These structures may include concrete liner plates, wood lagging systems, or steel ribs. Here are the steps involved:
1. Soil Excavation: Excavation is carried out using one of three methods chosen based on soil conditions.
The first method is hand mining, which is the simplest and involves using hand tools like picks, shovels, or pneumatic tools. A protective shield is used to provide stability during excavation, especially in varying soil conditions, but it is time-consuming.
The second method is open-face mechanical excavation, which is faster and uses mechanical devices with shielded access to the front face for adjustments when necessary. Shields are equipped with powered excavation devices.
The third method is the Tunnel Boring Machine (TBM), which employs rotary cutters, driven either hydraulically or electrically. It is more advanced and has limited access, primarily for circular tunnels.
2. Removal of Spoil: Depending on space, excavation method, and tunnel length, the most suitable spoil removal system is chosen. Common methods include slurry systems, auger systems, vacuum extraction systems, belt or chain conveyors, wheeled carts or skips, and positive displacement pumps.
3. Installation of Segmental Liner: After excavation and spoil removal, liner sections are brought in and connected to the existing ones. Liner plates are typically prefabricated and can be steel or reinforced concrete. Steel plates are in higher demand due to their better strength-to-weight ratio.
4. Control of Line and Grade: Line and grade control is achieved using theodolites and laser systems. Theodolites estimate the current tunnel position, while laser systems detect any alignment variations. Laser systems use LED lights but may be sensitive to temperature changes. Gyroscopes are more sophisticated control devices mainly used in curved tunneling.
The utility tunneling process is labor-intensive but suitable for sites with varying soil conditions. It is important to select the right method as per project requirements.
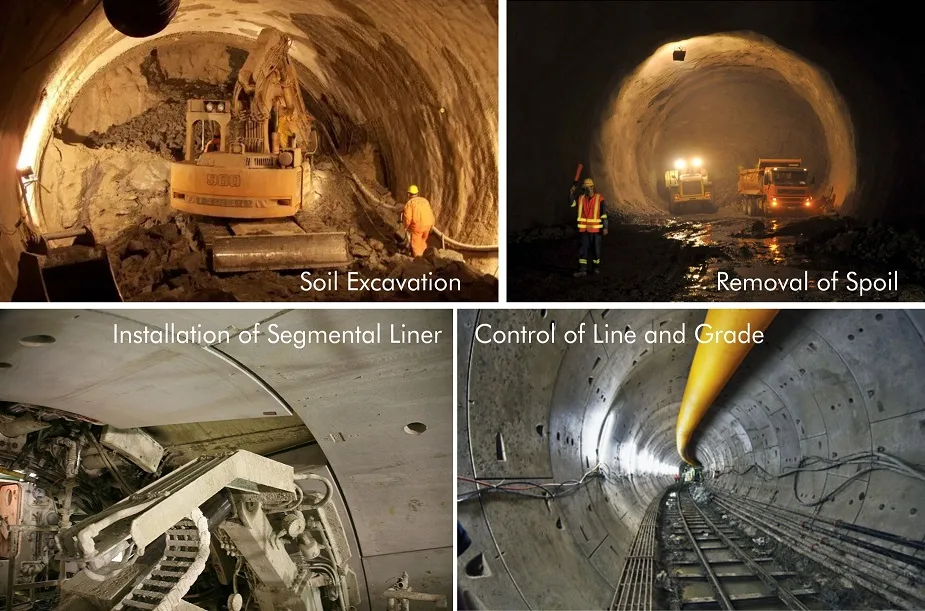
Different methods for construction of utility tunneling
Utility tunneling methods encompass various approaches to creating underground passages or tunnels for the installation and maintenance of utility services. Here are different types of utility tunneling methods:
1. Cut-and-Cover Tunneling: This traditional method involves digging a trench or open excavation, placing utility services within it, and then covering the trench with a protective structure, such as concrete or steel. Cut-and-cover tunneling is often used for shallow utility tunnels.
2. Microtunneling: This method is used for smaller-diameter utility tunnels, typically less than 1.2 meters (4 feet) in diameter. It involves remotely operated micro tunneling machines that bore through the ground, creating tunnels for specific utility services like sewer pipes or utility conduits.
3. Horizontal Directional Drilling: HDD is used to create underground utility conduits without extensive excavation. It involves drilling a borehole from the surface and then pulling utility lines through the drilled hole. HDD is suitable for situations where trenching is not feasible, such as under roads and water bodies.
4. Rock Tunneling: When utility tunnels need to pass through solid rock formations, specialized tunnel boring machines or drilling equipment are used. Rock tunneling methods vary depending on the hardness of the rock and can involve blasting or mechanical excavation.
5. Box Jacking: This method is used for creating larger utility tunnels, typically rectangular. Precast concrete or steel boxes are pushed or jacked through a pre-excavated tunnel route, forming the tunnel as it progresses.
6. Auger Boring: Auger boring utilizes a rotating cutting head to create tunnels for utility services. It’s often employed for shorter, smaller-diameter tunnels.
7. Underpinning: Underpinning involves reinforcing existing foundations and creating utility tunnels beneath them. This method is used to support structures while maintaining the stability of the surrounding ground.
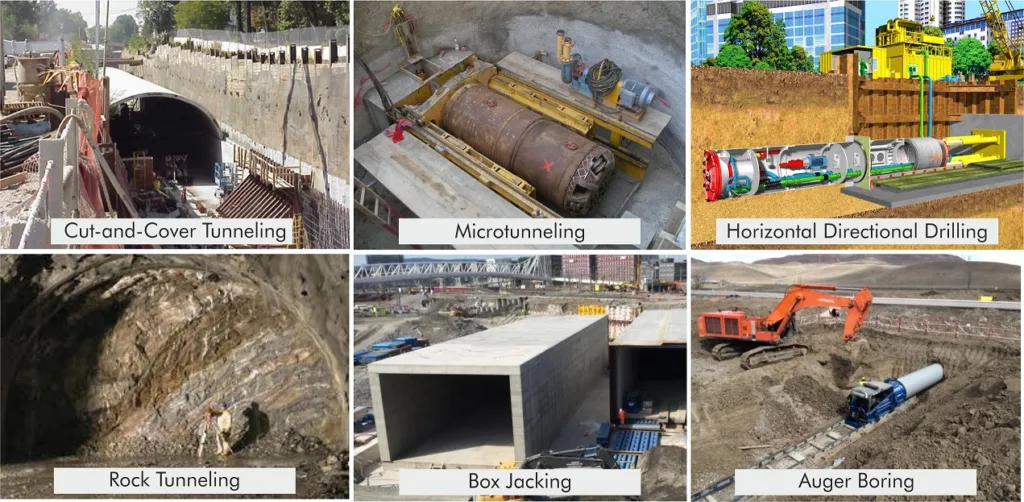
Conclusion
Utility tunneling represents a transformative solution for the increasingly complex infrastructure needs of modern urban environments. As cities expand and the demand for essential services grows, utility tunnels offer a path toward efficient, organized, and resilient utility management while minimizing surface disruption. As trenchless construction method continue to evolve, utility tunneling’s potential to address diverse urban challenges becomes even more promising.