Screening plants are used to separate raw material from a crusher or quarry into even finer grades. It aids the sorting process by placing the materials in the plant. Granulated ore materials are separated by size, density, or other factors depending on the need of the project. Demand for screening plants is being driven by an increase in infrastructure and construction projects, including mining and other industrial uses. The screening plants are being manufactured to match the project to ensure it can stand up to the job and function in the right environment. The mining, aggregate and mineral processing industries are the biggest users of screening equipment. These are often used in quarries and mines. With technological advancement the demand is ever-increasing. There is a need for the customization of screening machines and manufacturers. Given below are different types of screen plants available for different project requirements
Screening plant types
Circular vibrating screen plant with torsion-free screen frame
The circular vibrating screen is composed of a screen box, screen frame, screens, transmission device, vibration exciter, supporting device, vibration-isolating device, etc. The plant adjusts the amplitude by tube-shaped vibration screen of eccentric shaft and weight. The body moves like a circle to make the materials screened. Modern circular motion vibrating screen models can be equipped with all different kinds of screen mats. Circular motion vibrating screens are best suitable for long-living and economical operations. It can be used in a multitude of industries such as Iron and Steelworks, Coal, Foundry, Sand and Gravel, Mining, Recycling Waste and various other industries.
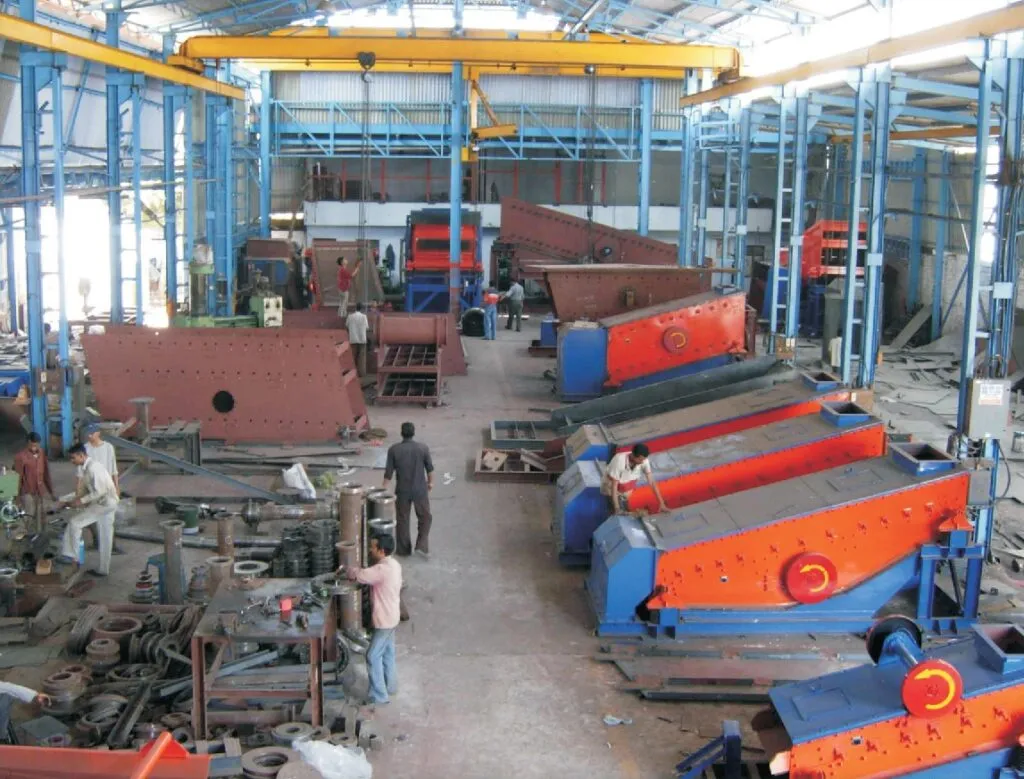
Grizzly screen plant for the toughest applications capable of high capacity
Grizzly screen plants are robust, linear-motion screens designed for heavy-duty scalping, and the removal of fines from the feed before primary crushing. These screens are ideal for tough primary screening of blasted rock, ripped rock and gravel with a high fines content.These screens have a very robust design, which allows them to operate under tough conditions (primary or secondary). These models are available in single or multiple-deck designs and can be designed to fit into your existing machine’s footprint for a seamless transition from old brute force technology to the improved Two-Mass design. The wide variety of screening decks provides improved performance for processing that follows size reduction mills or crushers. Multiple sizing decks are available on a single unit, which allows for versatile usage. The wide range of available screen sizes can be set at various angles to meet your process requirements.

Horizontal Screen plant with dual motor configuration
Horizontal Screens are utilized as a low height aggressive action screening device. They are built with a dual shaft (creating a straight line action at approximately 45 degrees to the horizontal) or a triple shaft. A primary feature of the Horizontal Screen is its aggressive action in applications where blinding or plugging of the screen media openings can occur. Latest models are equipped with two vibrating motors rotating in opposite directions. Depending upon the application, the horizontal vibrating screen frame can be positioned from 10 degrees uphill to 15 degrees downhill. Maximum capacity is achieved in the uphill position, causing the formation of a pool at the feed end of the machine. The head or pressure from the pool increases fluid throughout. The horizontal vibrating screens of the screen frame efficiently convey the oversize particles out of the pool area where they are then discharged.
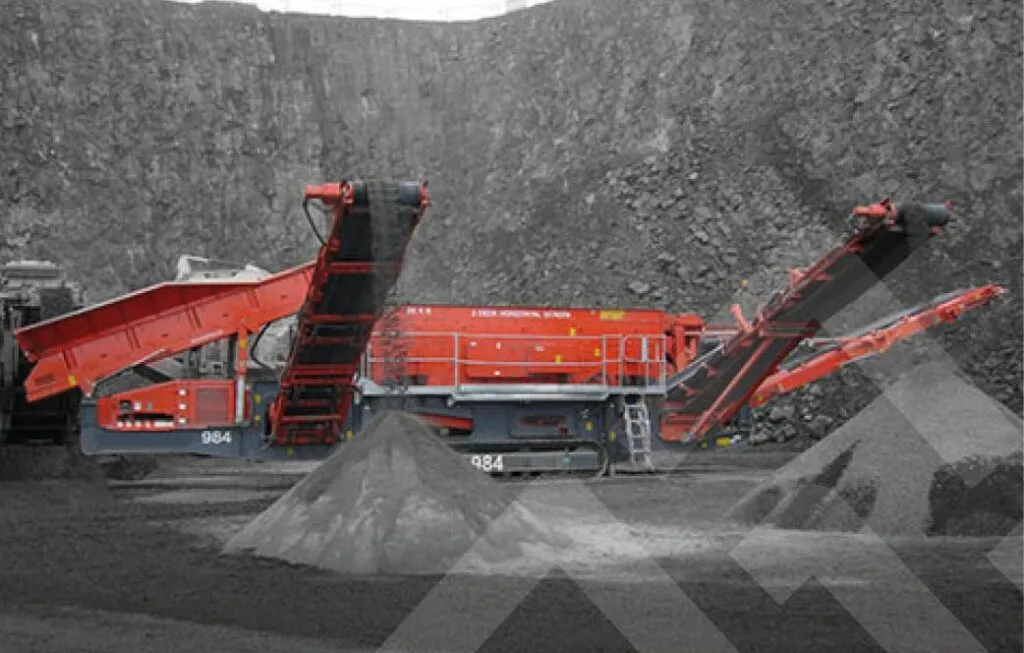
Inclined Screen plant with modular-type drive system
The latest inclined screens plants are equipped with a modular-type drive system for easy servicing. The two-piece drive-shaft system can be detached easily one by one, reducing servicing duration. Additionally, the cardan shaft connecting the modular shafts is more advantageous than traditional heavier and single-piece shafts in terms of easy maintenance. Inclined screens offer reliable and versatile screening in aggregates production plants, quarries, gravel pits and mining operations. Their circular motion and variable slope help you achieve a high production capacity and improve profitability.
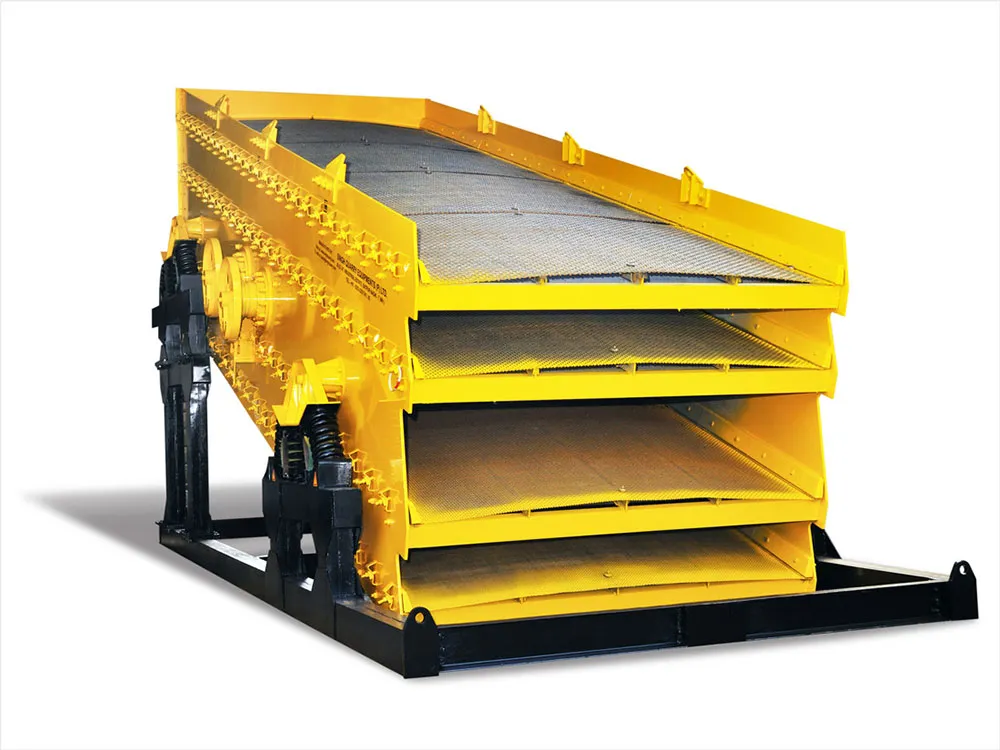
Mobile screen plants for obtaining different grain sizes
Mobile screen plants are used for screening almost all types of natural rock and in recycling. The classifying and coarse screens are available in a double- or triple-deck version. There is a variety of appropriate screen models available for obtaining different grain sizes and for different feed materials. Modern mobile screens come with high-quality components and engineering without compromises ensures trouble-free production. They are ideal for screening and scalping blasted rock, sand and gravel, recycled concrete and topsoil to produce a variety of construction and landscaping materials such as road base, and railway ballast.
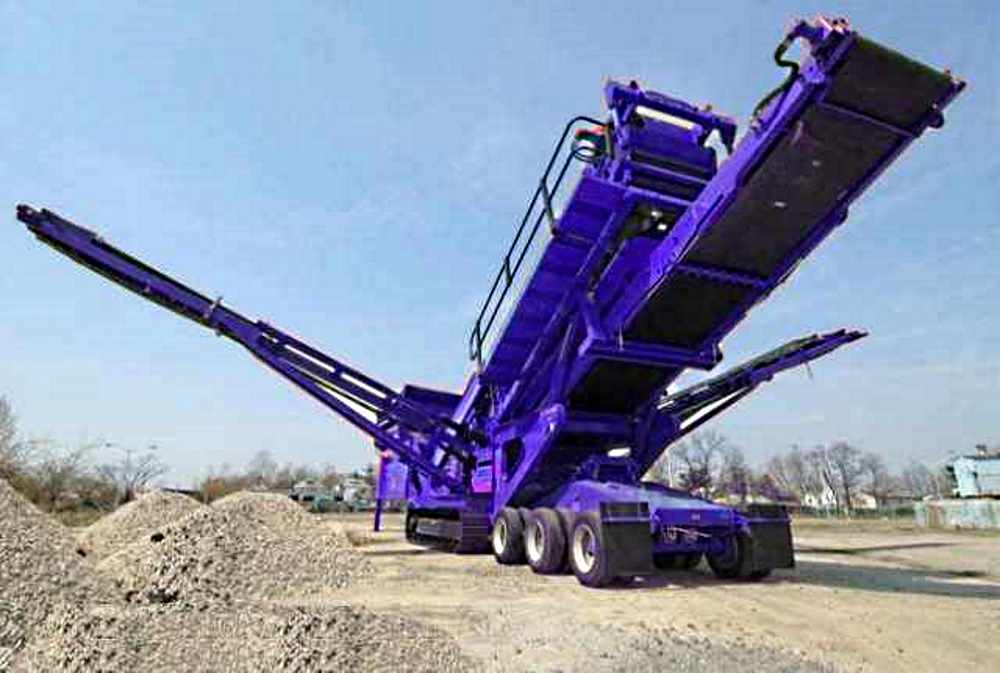
Trommel Screen plant with a hydraulic drive system
Modern trommel screens are highly efficient in the separation and processing of wood chips, topsoil, compost, light demolition waste, domestic waste and aggregates. Their rotating drums roll larger pieces of material to allow all fines to flow down and through the trommel screen plates. The latest models feature a highly efficient engine and hydraulic drive system combined with an advanced material processing control system offering maximum production combined with minimum costs. It is ideally suited for screening compost, biomass, soil, gravel & waste. Trommel Screens are attached to the end of grinding mills and scrubbers to perform a variety of screening functions. The trommel screen comprises the rubber-lined steel frame and replaceable screening surface.
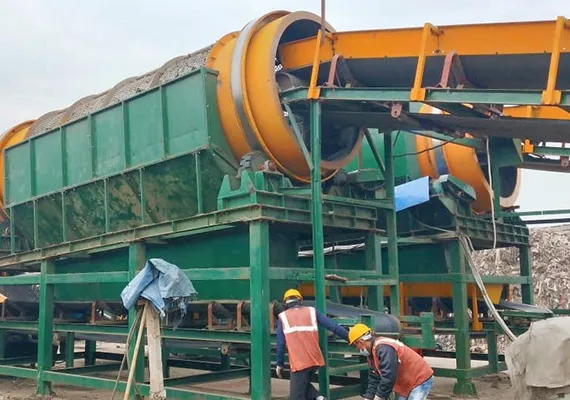
Disc Screen plant with anti-clogging system
Modern Disc Screen models are adopting the anti-clogging system, developed for urban and industrial waste through years of experience and testing. The models come with features such as optional orientation rolls on initial rotors to help transition material onto the main screen area. It covers for dust control can include air pick up to remove lightweight material for coarse material. The latest models offer an efficient and cost-effective solution for any high-volume screening application. These Screens operate by feeding material from an infeed device to the slope sheet. Smaller material, such as sawdust, falls through narrow openings in the disc, while larger materials like chips, bark and hogged wood continue to move to the end of the screen and feed to a grinder, hog, hammermill, re-chipper, bunker or reject conveyor. Low speed, smooth operation eliminates the need for special support structures, and the space-saving design reduces installation costs.

Circulating Vibrating Screens plant with motion modular vibrators
Modern heavy-duty screens that will sort your rock or mineral products effectively. We are experts at designing new custom screening plants and retrofits into existing operations. The conventional and general design for a high-frequency vibrating screen consists of a mainframe, screen web, eccentric bock, electric motor, rub spring and coupler. Modern models feature circular motion modular vibrators with two bearings per vibrator and a unique angle of the circular motion.The two most common types of vibrators which induce high-frequency vibrations are hydraulic or electric vibrators, these electric vibrators are either electric motors or solenoids. Modern high-performance circulating vibrating screens plants are manufactured and engineered to deliver increased productivity and operating benefits. The plant is becoming more widely used across various industries because they allow for strict size-control and efficient separation in material sorting.

Revolving screens plant with replaceable rake screen
Modern revolving screens come with the hydraulic performance of simply perfused rakes and an inclined, replaceable rake screen, this machine offers a maximum flow cross-sectional area. New generation revolving screens help to overcome problems such as blocking or sticking screens in screening wet adhesive materials. The yield and reliability of the screen have been greatly increased. The application of screen materials includes various properties, such as coal, gangue, coke; hydrated lime and other easily plug wet materials. It can be used in power plants, coking plants, building materials, metallurgy, chemical, mining and other industries.

Banana screen plant with different gear units
Banana screen plants are used when there is an increased feed rate or when the capacity must be very high. Latest models are designed with modular components and easy access to replaceable parts to enable quick maintenance, avoiding costly downtime. Modern banana screening plants achieve good separating accuracy at an extremely high feed rate and with difficult-to-screen material. Different gear unit sizes enable outstanding setting-up to suit your specific application. Balance masses and speeds can be adjusted in stages, enabling linear vibration amplitude and screen box acceleration to be optimally adapted to meet process requirements.
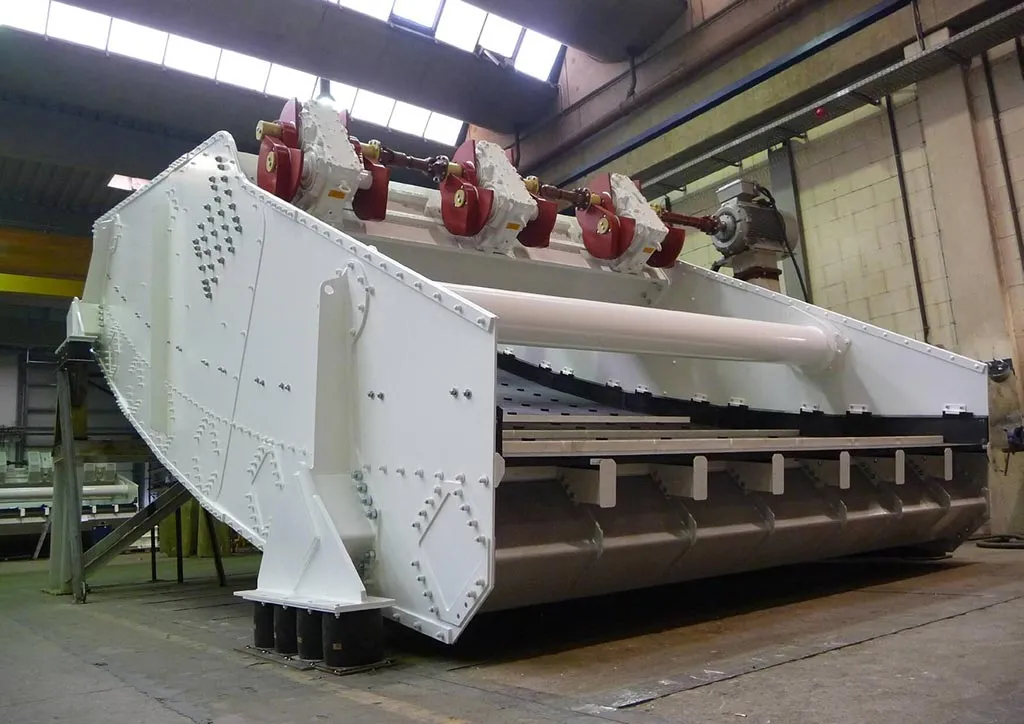
Dewatering vibrating screen plant with synchronisation drive technology
Dewatering Vibrating Screen models come with dual-motor self-synchronisation drive technology with built-in eccentric blocks. The vibration amplitude can be adjusted by the eccentric block. Models are mainly composed of a screen deck, vibrating motor, supporting system and electric control system. Through the synchronous and reverse operation of the vibrating motors, the centrifugal force generated by the two sets of eccentric masses is superimposed along the vibration direction. These screens dewater material and sludge and produce bulk material which can be transported with standard means. They are also used to recover solid particles from liquids, muds or sludges. The robust screen frame is manufactured in either a welded or a bolted and glued design, depending on the application. It is applicable for Mining Tailings Dewatering & Dry Discharge, Water-washed Sand Dewatering, Potash Feldspar Dewatering, Environmental Mud Dewatering and Fine Sand Recovery applications.

Conclusion
The screening equipment market is expanding rapidly due to its vast application in various industries. The construction & mining industries make wide use of screening plants. There is a high need for product development, for which, existing companies are focusing on R&D for creating improved products. Additionally, manufacturers are concentrating on expanding their customization options in response to the specialized needs of their customers.
Image Source: ecomanindia.com, thyssenkrupp-industries-india.com, terex.com, singhcrushers.com, frengimech.com, duromech.in, ecostermfg.com, royaljawcrusher.com, elektromag-joest.com, dewateringscreens.in