Screening equipment consists of a drive that induces vibration, a screen media that causes particle separation, and a deck that holds the screen media and the drive and is the mode of transport for the vibration. It is used during the mechanical screening processes, designed to separate one material from another. As the second part of the material handling process, screening equipment is used to separate raw material from a crusher or quarry into even finer grades, coming closer to an end product. There are two types of screens [wet and dry], totally dependent on the raw material. Wet screens utilize spray nozzles and water along with screen vibration in the sorting process, while dry screens use vibration only.
There are different types of screening equipment, which are discussed below.
Trommel Screens
Trommels are widely used in gold mines since they are extremely efficient and very effective at recovering fine gold. The larger-sized models can handle impressive volumes of gold-bearing gravel when operating at peak efficiency. They are often powered by large diesel or electric engines. Modern trommel screens are highly efficient in the separation and processing of wood chips, topsoil, compost, light demolition waste, domestic waste and aggregates. Their rotating drums roll larger pieces of material to allow all fines to flow down and through the trommel screen plates. The latest models feature a highly efficient engine and hydraulic drive system combined with an advanced material processing control system offers maximum production combined with minimum costs. It is ideally suited for screening compost, biomass, soil, gravel & waste. Trommel Screens are attached to the end of grinding mills and scrubbers to perform a variety of screening functions. The trommel screen comprises the rubber-lined steel frame and replaceable screening surface.
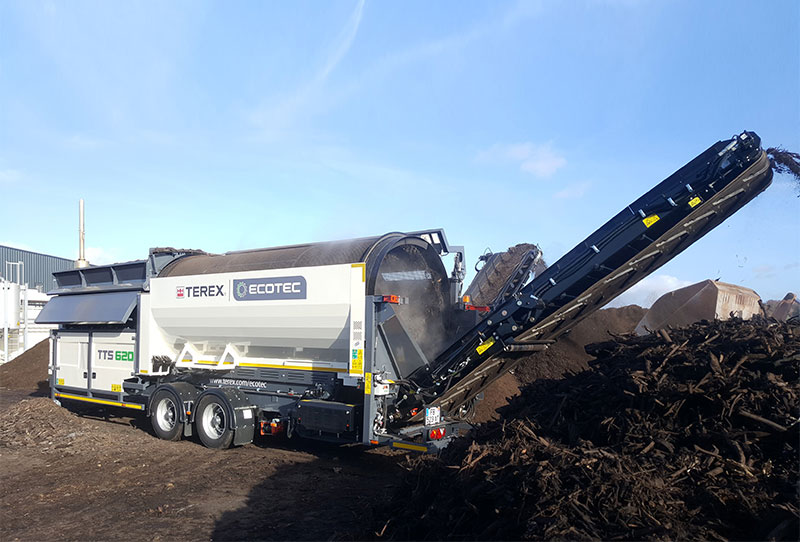
Vibrating Screens
Modern high-performance Vibrating Screens machine is engineered to deliver increased productivity and operating benefits compared to conventional spring-mounted vibro separators. With its hygienic design, this circular vibro screen is ideal for applications where hygiene is of utmost importance. Available as a fully stainless steel unit (including the stand) with contact parts. The conventional and general design for a high frequency vibrating screen consists of mainframe, screen web, eccentric bock, electric motor, rub spring and coupler. The two most common types of vibrators which induce the high-frequency vibrations are hydraulic or electric vibrators, these electric vibrators are either electric motors or solenoids. Common designs for screening decks are either single or double deck. Besides, another feature of high frequency vibrating screens is the static side plates which provide benefits such as smaller support structure, less noise, longer life, and hence less maintenance.
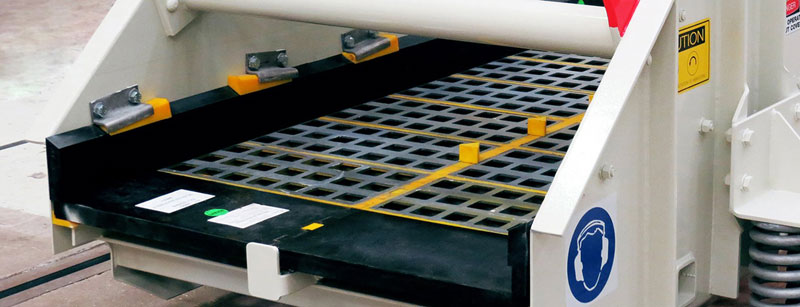
Disc Screens
New age Disc Screen is adopting the patented anti-clogging system, developed for urban and industrial waste through years of experience and testing. The solution involves the isolation of the machine shafts from the material flow in coordination with the liberation of the material through the faceted disk shape. The latest models offer an efficient and cost-effective solution for any high volume screening application. These Screens operate by feeding material from an infeed device to the slope sheet. Smaller material, such as sawdust, falls through narrow openings in the disc, while larger materials like chips, bark and hogged wood continue to move to the end of the screen and fed to a grinder, hog, hammermill, re-chipper, bunker or reject conveyor.

Grizzly Screens
New age grizzly screens have been designed for the toughest applications capable of high capacity and the ability to process abrasive material. These screens have a very robust design, which allows them to operate under tough conditions (primary or secondary). They particularly perform very well when used to remove the fines between two crushing stages. New series grizzly screens are equipped with many features enabling high efficiency and ensuring various operational advantages. These advantages reduce maintenance and servicing costs, along with necessitating less downtime. Grizzly screens can provide either linear or circular motion and each type offers its advantages. Linear motion grizzly screens work best for scalping ahead of primary cone crushers in mining applications, while circular motion grizzly screens for heavy-duty medium to fine pre or post-screening. Primarily used for the heavy-duty screening of undersized materials in bulk material handling applications, the most common industries that utilize grizzly screens include mining, construction, foundry, recycling and industrial.
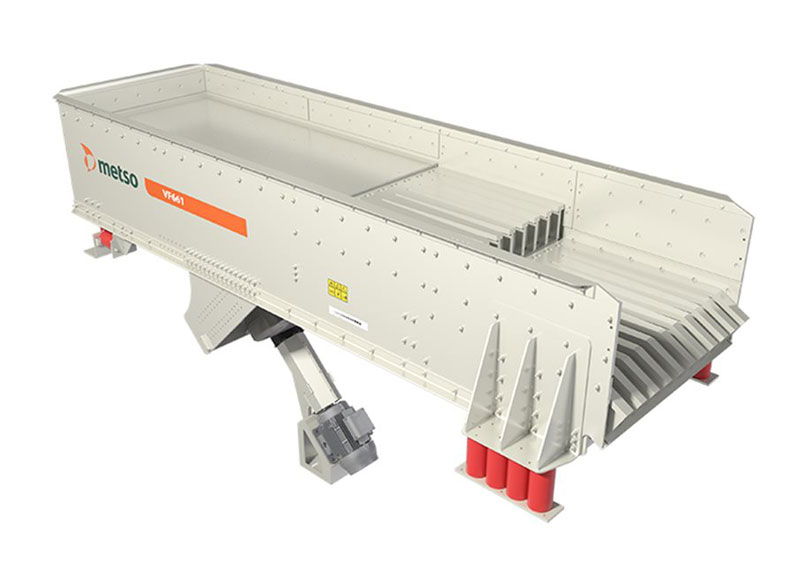
Revolving screens
New generation revolving screens help to overcome problems such as blocking or sticking screens in screening wet adhesive materials. The yield and reliability of the screen have been greatly increased. The application of screen materials includes various properties, such as coal, gangue, coke; hydrated lime and other easily plug wet materials. Be used in power plants, coking plants, building materials, metallurgy, chemical, mining and other industries.

Banana screens
The banana screen is designed by injecting a banana-shaped multi-stage working surface based on a linear classifier. There is a larger slope screen at the feed end, followed by a stepwise decrease at a certain number of angles until the discharge opening, the overall screen surface is concave curved. The sloped screen at the feed end allows for more material to pass through the screen surface with higher screening speeds and thinner material delamination. Modern banana screening machines achieve good separating accuracy at an extremely high feed rate and with difficult-to-screen material. Its operational behaviour makes it a high-speed screen. Compared with conventional vibrating screens, the banana screen handles a considerably larger feed quantity for the same screen area. Different gear unit sizes enable outstanding setting-up to suit your specific application. Balance masses and speeds can be adjusted in stages, enabling linear vibration amplitude and screen box acceleration to be optimally adapted to meet process requirements.

Elliptical-motion screens
Elliptical-motion screening machines are driven by two centric main shafts, which generate a swing diameter as in a free-running drive. Another synchronized shaft transforms the swing diameter into an ellipse defined by its task. The second shaft distorts the swing diameter into an ellipse. The big advantage of these machines is that they can work with a very low inclination or with no inclination at all. or The elliptical-motion screening machine combines the advantages of linear- and circular-motion screens as well as enabling space-saving horizontal installation and high material throughput. Both mechanical and electronic elliptical-motion screens can be selectively varied and adapted to operating conditions. This is done by, amongst other things, altering the throw angle essential for transport speed and by adaptation of parameters important for acceleration of the machine, such as vibration amplitude and speed.

Horizontal Screens
Modern horizontal screens are equipped with two vibrating motors rotating in opposite directions. This dual motor configuration in the Horizontal Vibrating Screen causes the screen’s frame to vibrate in a linear or straight-line motion perpendicular to the plane of the motors. Normally, the motors are positioned at an angle of 50 degrees concerning the screen’s surface. This results in an excellent forward conveyance of oversize particles, even when the screen frame is in an uphill position. Depending upon the application, the horizontal vibrating screens frame can be positioned from 10 degrees uphill to 15 degrees downhill. Maximum capacity is achieved in the uphill position, causing the formation of a pool at the feed end of the machine. The head or pressure from the pool increases fluid throughout. The horizontal vibrating screens of the screens frame efficiently conveys the oversize particles out of the pool area where they are then discharged.
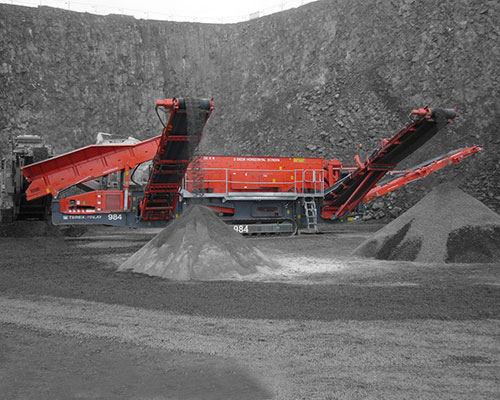
Inclined Screens
The vibrating Inclined Screen is the most popular type of screen. There are various types of Inclined Screens, including two and four bearing, high-speed, and high-frequency screens. The overwhelming majority of installations today are either two or three decks, though there are single and four-deck varieties available as well. Modern models are designed with operator safety in mind. Side plates feature cross beam inspection ports that allow you to inspect the inside tubes for failures when the tube is not visible due to abrasion-resistant lining, thus eliminating the need for operators to crawl between decks for inspections. Foreign material that can corrode or abrade the inside of the cross members and cause premature failure can be flushed out via cross beam inspection ports. The eccentric mechanism features jacking bolts in the mechanism tube to support the eccentric shaft during bearing change-outs, eliminating the need for a crane to suspend the shaft or the chance of the shaft tipping over and injuring workers, creating a safer work environment and decreasing downtime.

Mobile screens
Mobile screens are utilized in construction sites, aggregates production, quarries, and mining operations whenever movable but high capacity screening is required. The latest models come with high-quality components and engineering without compromises ensures trouble-free production. When service is required, it can be done simply and easily through easy-to-access maintenance points.

Conclusion
Screening equipment needs to match the project to ensure it can stand up to the job and function in the right environment. The mining, aggregate and mineral processing industries are the biggest users of screening equipment. These are often used in quarries and mines. With technological advancement the demand is ever-increasing. There is a need for customization of screening machines and the manufacturers are focusing on that.
Image Sorce:
www.metso.com
www.terex.com
www.wirtgen-group.com
www.ife-bulk.com
www.baitemining.com
www.siebtechnik-tema.com