The bridge industry is moving toward mechanized construction because this saves labour, shortens project duration and improves quality. This trend is evident in many countries and involves most construction methods. Engineers are experimenting with multiple materials for customised demand.Effective decisions on the use of natural resources often require the input of many individuals. Determining how specific criteria affect the selection of materials can lead to better utilization of raw materials.
Important points of consideration for selection of materials to be used in bridge construction are maintenance requirements, lifecycle costs, and lifespan of material. Few of types of materials used in Bridge Construction are discussed below.
Types of materials used in Bridge Construction
Concrete for bridges
More bridges are built using concrete than any other material worldwide, demonstrating continued confidence in the material’s performance and durability. Concrete bridges have a clear track record of flexibility and versatility in terms of both final forms and methods of construction that are hard to match. Durability, aesthetics, economic solutions, simplified construction and rapid deployment techniques all contribute to making concrete the best construction material for any bridge project, whatever the size, form or intended use. Greater construction flexibility can be realised through the many forms of concrete easily available nationwide, making concrete an adaptable resource suitable for deployment for even the most challenging of bridge types or construction sites. The range of structural forms achievable with concrete is limited only by designers’ imagination, enabling the creation of elegant bridge structures that blend seamlessly with natural surroundings. Concrete unites both function and elegance in safe, robust structures, regardless of scale. Architectural surface finishes can add to visual impacts while at the same time eliminating the need for cladding, painting and ongoing maintenance activities.
Concrete bridge types-
Slab
- Slab bridges may be composed of single or multiple spans
- Simple, easy to construct.
- Well-suited for spans up to 50 feet.
- For longer spans, continuity with abutments and piers can mobilize frame action.

Arch
- Concrete arch bridges may consist of either a single arch or multiple arches supported by abutments and intermediate piers.
- Simple, easy to construct.
- Well-suited for spans up to 50 feet.
- For longer spans, continuity with abutments and piers can mobilize frame action.
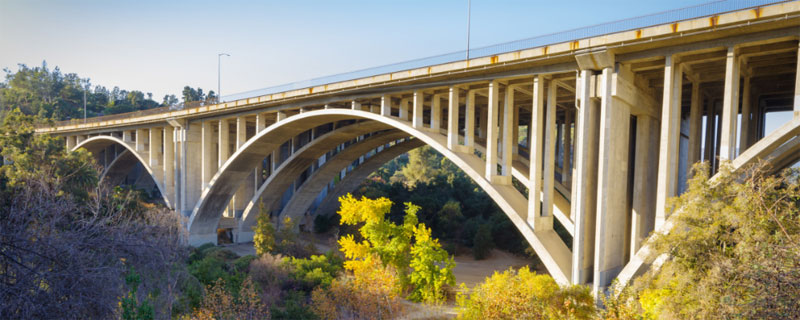
Cable-Stayed
- Cable-stayed bridge with a cast-in-place
- reinforced, or segmental deck.
- Economical and aesthetically pleasing.
- Structurally efficient use of materials.

I-Girder
- A simple beam bridge is commonly used for moderate spans.
- Variations of the precast I-girder include the PCI bulb-tee or bulb-tee sections developed by various states.
- Most popular bridge type.
- Well-suited for spans up to 160 feet.
- Common depths: 20 in., 36 in., 45 in., 54 in. and 72 in.

Box Beams
- A box beam bridge is supported by abutments and piers in the same way as a simple- or continuous beam bridge.
- Common bridge type, especially for low-volume roads.
- Well-suited for spans from 50 feet to 120 feet.
- Common widths of 36 or 48 in.

Segmental
- They can be cast-in-place or precast, and can employ span-by-span or balanced cantilever construction.
- Perfectly suited for gradual and sharply curved alignments.
- Maximum span is greater than 300 feet.
- Repetition of short spans: 70 feet to 150 feet.

Prestressing concrete for bridges
Prestressing concrete bridges involves casting concrete beams with longitudinal holes for steel tendons—cables or bars—like reinforced concrete, but the holes for the tendons are curved upward from end to end, and the tendons, once fitted inside, are stretched and then anchored at the ends. The tendons, now under high tension, pull the two anchored ends together, putting the beam into compression. In addition, the curved tendons exert an upward force, and the designer can make this upward force counteract much of the downward load expected to be carried by the beam. Prestressed concrete reduces the amount of steel and concrete needed in a structure, leading to lighter designs that are often less expensive than designs of reinforced concrete.

Steel for bridges
Steel is widely used around the world for the construction of bridges from the very large to the very small. It is a versatile and effective material that provides efficient and sustainable solutions. Steel has long been recognised as the economic option for a range of bridges.
Structural steel is a high-quality material that is readily available worldwide in certified grades, in products of various shapes and sizes. Prefabrication of steelwork in controlled factory conditions leads to high quality work at minimum cost. The excellent quality control is achieved through a thorough testing regime at the steel mills and during the fabrication processes of cutting and drilling, assembly, welding, and protective treatment. Steel material is supplied in two product forms – ‘flat products’ (steel plate and strip) and ‘long products’ (rolled sections, either standard open sections such as beams, channels, angles, etc or hollow sections). For structural use in bridges these products are inevitably cut (to size and shape) and welded, one component to another. In the structure, the material is subject to tensile and compressive forces. Structural steel generally responds in a linear elastic manner, up to the ‘yield point’ and thereafter has a significant capacity for plastic straining before failure. All these aspects of steel material are utilised by the designer of a steel bridge.
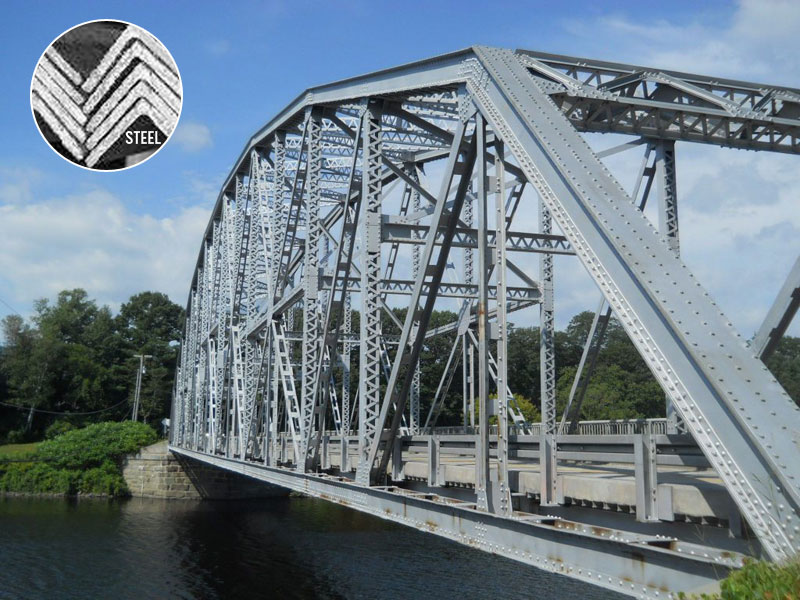
The high strength-to-weight ratio of steel minimises the structural weight of superstructures and thus minimises the substructure costs, which is particularly beneficial in poor ground conditions. Minimum self-weight is also an important factor in the cost of transporting and handling components. Use of steel facilitates shallow construction depths, which overcomes problems with headroom and flood clearances, and minimises the length and cost of approach embankments.
Steel is the most recycled construction material and choosing it for bridges represents a sustainable management of natural resources. When a steel bridge reaches the end of its useful life, the girders can be cut into manageable sizes to facilitate demolition, and returned to steelworks for recycling. Some 99% of structural steel either finds its way back into the steelmaking process where it is used to create new steel products or is reused. There is no degradation in the performance of recycled steel. Alternatively, component parts of steel bridges can be reused in other structures; entire bridges have been relocated and bridges can be designed with ease of future relocation in mind. Steel has broad architectural possibilities. Steel bridges can be made to look light or reassuringly solid, and can be sculptured to any shape or form. The high surface quality of steel creates clean sharp lines and allows attention to detail. Modern fabrication methods can easily provide curvature in plan and elevation. The painting of steelwork introduces colour and contrast, and repainting can change or refresh the appearance of the bridge.
Cast-iron for bridges
Cast iron has a very high resistance to compression which makes it ideal for use in arch bridges where the entire cast iron piece is put under compression. For this reason the first large cast iron bridge, the Iron Bridge, used cast iron for its supportive arch.
Cast-iron columns for buildings had the advantage of being extremely slender, compared with masonry columns capable of supporting similar weight. It is also useful in other kinds of buildings, for instance enabling architects of theaters, churches and synagogues to improve sight lines when supporting balconies, by eliminating or at least making the columns that supported the roof or balconies thinner.
Cast iron became a very popular construction material in the late 1700s. It had previously been too expensive to produce in a large enough quantity for construction, but the advent of many new blast furnaces made cast iron more widely available. Through the Industrial Revolution cast iron bridges became very popular and many still remain

Timber for bridges
A timber bridge or wooden bridge is a bridge that uses timber or wood as its principal structural material. One of the first forms of bridge, those of timber have been used since ancient times. The last two decades have seen a growing interest in timber bridges in many European countries. There are several reasons for this. The growing interest in environmental questions and sustainability has definitely paved the road for more use of structural timber, but also new and innovative use of timber, such as the stress laminated timber deck and better connections, have played an important role. Bridges are naturally divided into two major groups: footbridges and road bridges. The vast majority of timber footbridges have decks made of timber, in one form or another, from simple timber boards or planks to crossed layers of boards and various types of laminated decks. For road bridges the situation is more complex. It is very important to prevent surface water from penetrating the asphalt wearing course, and some kind of impregnable membrane is therefore placed between the timber deck and the asphalt.
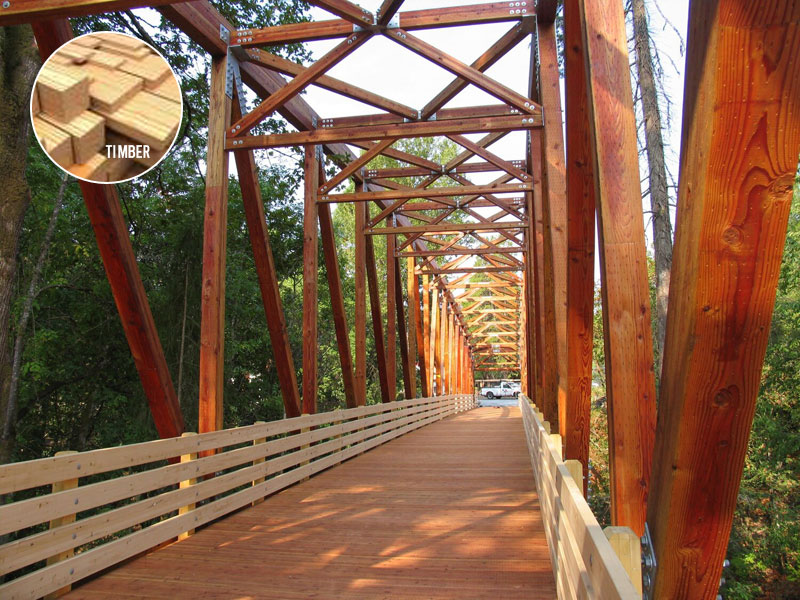
Stone for bridges
Stone is strong in compression and somewhat so in shear, but cannot resist much force in tension. As a result, masonry arch bridges are designed to be constantly under compression, so far as is possible. Each arch is constructed over a temporary falsework frame, known as a centring. In the first compression arch bridges, a keystone in the middle of the bridge bore the weight of the rest of the bridge. The more weight that was put onto the bridge, the stronger its structure became. Stone bridges have been used in one form or another for many thousands of years. The earliest surviving stone structures were most likely based on clapper bridges. These are an ancient form of stone bridge formed by large flat slabs of granite or schist supported on stone or resting on the banks of streams.Despite the expected high construction costs, the cost of masonry arch bridges appears to be similar to that of concrete or steel bridges. This is largely down to the lack of need for expensive machinery or equipment. Masonry bridges have always been built with predominantly manual labour and with relatively simple lifting equipment. The life-cycle maintenance costs for masonry bridges are far lower than for other bridges and, if maintained properly, they can well outlast any other bridge type.

Advanced composites for bridges
Exciting application of advanced composites is for new bridges and bridge deck replacement units has been found in many researches. Both epoxy impregnated fiberglass and carbon fiber materials have been tested in the laboratory on half-scale models of bridge columns to determine the ductility that can be achieved in an older, non-ductile concrete column. Material properties are readily available from the manufacturers but there remained the issue of adequate quality control specifications for the field application. These early applications were rather crude, being hand laid in a similar manner as hanging wallpaper. It required some months to fully develop adequate quality control (QC) specifications so the materials tested in the laboratory could be replicated with confidence in the field. Composites can be divided in a matrix phase and a dispersed phase. The matrix phase has a continuous character and is usually more ductile and less hard. The matrix phase holds the dispersed phase and shares a load with it. The dispersed phase is embedded in the matrix phase in a discontinuous form. The dispersed phase is usually stronger than the matrix phase. Therefore, it’s also referred to as the reinforcement phase.

As awareness of the advantages of composites expands, many fabricators and suppliers say conversations with civil engineers are turning away from resistance to change and skepticism over material capabilities to other factors such as cost and capabilities of the materials. The most interesting application of advanced composites to date is the design and construction of an operating bridge on the state highway system. An innovative highway bridge consisting of hollow carbon-composite tubes and lightweight concrete was built on State Highway Route 86 near Palm Springs, California with the construction completed in 2000.
Conclusion
As years have gone on, we’ve started to see more engineers really start taking a hard look at these types of materials because they are, for the most part, maintenance free. More development can be expected in the material usage of bridge construction in the future.
Info source – concrete society, CRSI.Org, ASCE, Ehow.com, quakewrap.com, Riunet.com, nextcity.org, futureofworking.com, bgcons.com, bde.hgl-content.co.uk, spancrete.com, erkrishneelram.files.wordpress.com, enr.com, dywidag-systems.com, hoyletanner.com, wikimedia.org, westernwoodstructures.com, ASCE, compositesworld.com