Construction chemicals have always been playing important roles in virtually all sorts of construction projects, be it industrial projects, residential building projects, commercial building projects and so on. These chemicals are often used in various elements of projects in order to achieve various important qualities such as workability, durability etc. Construction chemicals exist in many varieties from a large number of manufacturers worldwide.
Increasing demand for public, commercial and residential buildings combined with an increasingly urban population is driving the global construction chemical market. Demand for buildings, roads, bridges, tunnels and dams is further driving the market.
Discussed below are different types of construction chemicals used on hardened concrete either as surface application, coating or as repair materials.
Concrete curing compounds
Concrete curing compound consists essentially of waxes, natural and synthetic resins, and solvents of high volatility at atmospheric temperatures. The compound forms a moisture retentive film shortly after being applied on a fresh concrete surface. White or gray pigments are often incorporated to provide heat reflectance, and to make the compound visible on the structure for inspection purposes. Curing compound should not be used on surfaces that are to receive additional concrete, paint, or tile which require a positive bond, unless it has been demonstrated that the membrane can be satisfactorily removed before the subsequent application is made, or that the membrane can serve satisfactorily as a base for the later application.
Polymer bonding agents
Polymer Bonding Agent is an aqueous emulsion of a polymer and chemical admixtures. It is designed for use as a bonding agent with concrete and cement-based products in interior or exterior applications. Polymer Bonding Agent is also designed for use as a polymer modifier in mortars and concretes to develop increased tensile, flexural and bond strengths. The use of Polymer Bonding Agent in concrete and shotcrete also gives significant improvements in resistance to penetration by chlorides and de-icing salts.
Mould releasing agents
Mould release agents come in handy when you have materials that are shaped and constructed in moulds. Without the releasing agent, your mould may become damaged or even break when it is time to remove it. Mould release agents come in a variety of textures with the most commonly used one being an oil type base. If you have never used a releasing agent before, it is similar to placing oil or butter in the bottom of a dish to remove your final baking product. Below, you will find the three most commonly used types and their purpose in the manufacturing industry.



Form release agents
These compounds are applied on the inner surfaces of forms, not only facilitate stripping of formwork but also render concrete surfaces smoother. They also help enhance the life-span of the forms. Form releasing agents can be oil based, resin based, water based, organic chemical based etc.
Protective and decorative coatings
A protective coating is a layer of material applied to the surface of another material with the intent of inhibiting or preventing corrosion. A protective coating may be metallic or non-metallic. Protective coatings are applied using a variety of methods, and can be used for many other purposes besides corrosion prevention. Commonly used materials in non-metallic protective coatings include polymers, epoxies and polyurethanes. Materials used for metallic protective coatings include zinc, aluminum and chromium. Special materials are used in the finishing coats of plastering or over the plastered surfaces to meet one or more of specific requirements such as decorative appearance, high durability,fire – proofing,heat insulation,sound insulation,early completion,high strength etc..
Concrete floor hardeners
These are chemicals added in floor concrete in order to render it denser and more durable. They also usually enhance chemical resistance, impact & abrasion resistance, waterproofing capability etc. besides reducing dusting. All these are required attributes especially for industrial, commercial or factory floors. Ultimately good quality floor hardeners reduce repairs and maintenance of concrete floors drastically besides making them long lasting thus adding to cost effectiveness as well. Floor hardeners can be liquid or solid, metallic or non metallic. Metallic floor hardeners (solid) are well graded ferrous aggregates. Liquid floor hardeners are water, silicate etc. based solutions. Pigmented floor hardeners also improve the appearance of floor surfaces. Floor hardeners are usually applied as per manufacturer’s specifications This construction chemical Improves the abrasion resistance of dusty or poorly cured concrete by up to 3 times. Has good resistance to alkali solution and petroleum solvents but poor resistance to strong acids.
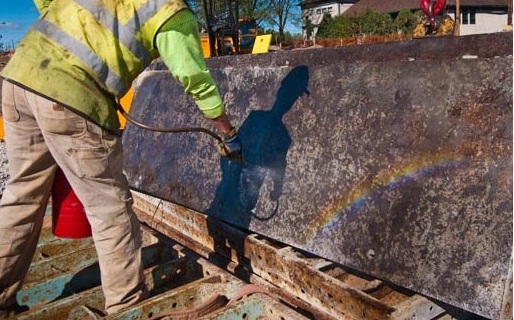


Non-shrink High Strength Grout
Non-shrink grout is a hydraulic cement grout that, when hardened under stipulated test conditions, does not shrink, so its final volume is greater than or equal to the original installed volume. It is often used as a transfer medium between load-bearing members. It is specially formulated to provide extended working time even at high ambient temperatures when mixed and placed at any recommended consistency. Its compressive strength is often very high. Typical compressive strength values are 8,000 psi to 14,000 psi at 28 days, with 1 day strengths in excess of 3,000 psi.
Surface retarders
Surface retarders, also called surface “deactivators,” are applied to fresh concrete to chemically delay the set of the surface mortar. Unlike concrete set retarders, they allow the rest of the concrete to cure normally, without affecting the setting rate or strength gain. Because surface retarders work their magic by stopping the hydration process down to a controlled depth, the underlying concrete will harden properly while allowing easy removal of the surface paste later. When you are ready to expose the aggregate by hosing or high-pressure washing, the depth of aggregate reveal is more uniform with minimal pop-outs.The best time to apply surface retarder is after you’ve completed all finishing operations and the bleedwater has dissipated.
Bond-aid for plastering
Almost all surface applied bonding agents are compounded from polyvinyl acetate emulsions. These water-based adhesives are very safe to use because they are non-toxic, non-hazardous and non-flammable. They meet even the most stringent VOC requirements. As with any coating, surface preparation is essential for a successful application. The surface must be structurally sound and clean, which means free from dust, dirt, oil and efflorescence. On new concrete it is important to determine whether the form release and/or curing compound can be coated. Almost all manufacturers of these types of products will include a statement in their directions regarding compatibility with various coatings. If the surface can be painted, it can be coated with a surface applied bonding agent.



Ready-mix plaster
Ready mix plaster is a factory mixed/premixed sand-cement based plaster. All the activities that are generally undertaken on-site are performed in a quality-controlled environment at plant to ensure no-batch variation and optimum sand gradation, which is of utmost importance for any plaster. Other additives such as fly ash and polymers are also added to it, to improve its performance and various other properties. These are generally used for building houses or making solid structures of any sort. Apart from these, they can also be used for various other purposes that require you to put two or more things together that will hold strong for long. You can also use ready mix plaster to make models.
Polymer modified mortar for repair and maintenance
Polymer-modified mortar is made by replacing a portion of the traditional binders with polymers. Polymers are added to mortar to increase characteristics that may include adhesion, toughness, flexural or tensile strength, and resistance to chemicals. Polymers act to improve the workability and adhesion of non-hardened mortar and often require less added water than does traditional mortar, which results in fewer pores and stronger cements, subsequently reducing water ingress and permeability to salts. Polymer-modified mortar is often commercially available with all ingredients already included in the mixture.
Tile fixing
Tile fixers and tile adhesives form the backbone of your home. A quality tile fixer connects all your tiles together, to create a beautiful canvas from individual pieces. Tile fixing products are used for floorings, bathtubs, washbasins, kitchen tops and any other area where two surfaces need to stick together.



Guniting aid
The guniting is the most effective process of repairing concrete work which has been damaged due to inferior work or other reasons. It is also used for providing an impervious layer. The gunite is a mixture of cement and sand, the usual proportion being 1:3. A cement gun is used to deposit this mixture on the concrete surface under a pressure of about 20 to 30 N/cm2. The cement is mixed with slightly moist sand and then necessary water is added as the mixture comes out from the cement gun. A regulating valve is provided to regulate the quantity of water. The surface to be treated is cleaned and washed. The nozzle of the gun is generally kept at a distance of about 750 mm to 850 mm from the surface to be treated and the velocity of the nozzle varies from 120 to 160 m/sec.
Water repellents
These chemicals have water repelling properties which are exploited to protect masonry and concrete alike from the ill effects of moisture or water. Some examples amongst many types of water repellent are acrylic protective coating, water based silane siloxane water repellent sealer for tiles, stone masonry etc.
Swelling water stops
These are primarily used in construction joints. Quite easy to install, good quality swelling water stops can be a more efficient and economic option to the conventional PVC waterstops in many cases. These chemicals seal the joints by their swelling action when they come in contact with the water of freshly poured concrete. Examples are polyurethane foams and grouts. Swelling PU resins, which turn foamy and expand when coming to contact with water, are used for sealing leaking cracks as well by injecting the chemicals into the cracks.
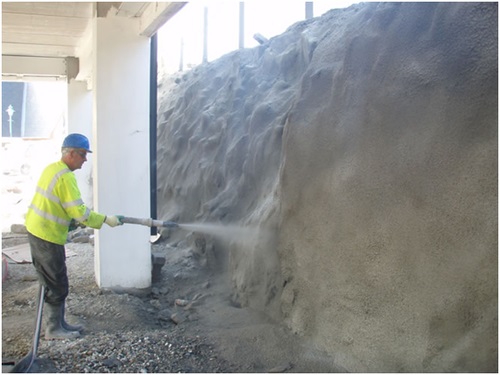


Waterproofing chemicals
These chemicals can be quite useful when a structure’s waterproofing capability is to be given a boost which is especially required for structures constantly dealing with liquids. There are many varieties. Some of them are crystalline waterproofing chemicals, liquid acrylic elastomeric waterproofing compounds, polymer modified waterproofing compounds, cementitious waterproofing compounds etc. Many of these compounds form membranes on the concrete surfaces to protect them from ingress of water.
Adhesives
These construction chemicals are readily used in all sorts of projects, be it commercial, residential, industrial etc. construction projects. Adhesives are expected to have strong bonding capacity besides good waterproofing, weatherproofing etc. qualities. These are also expected to be elastic enough to accommodate repeated expansion and contraction likely to be caused by temperature fluctuations. Adhesives make their ways to a myriad of construction works ranging from floor covering, panel fixing to tile fixing and so on. Various types of adhesives are PU based adhesives, silicone adhesives, acrylic adhesives, UV adhesives etc
Rebar coating
Coatings for reinforcing steel bars can be quite useful when the bars have to be stored or kept exposed to weather for considerable time. They prevent formation of rust on the bar surface which otherwise needs to be removed by sand or grit blasting. A common and effective type of rebar coating is fusion-bonded epoxy coating. Bars can be galvanised as well.
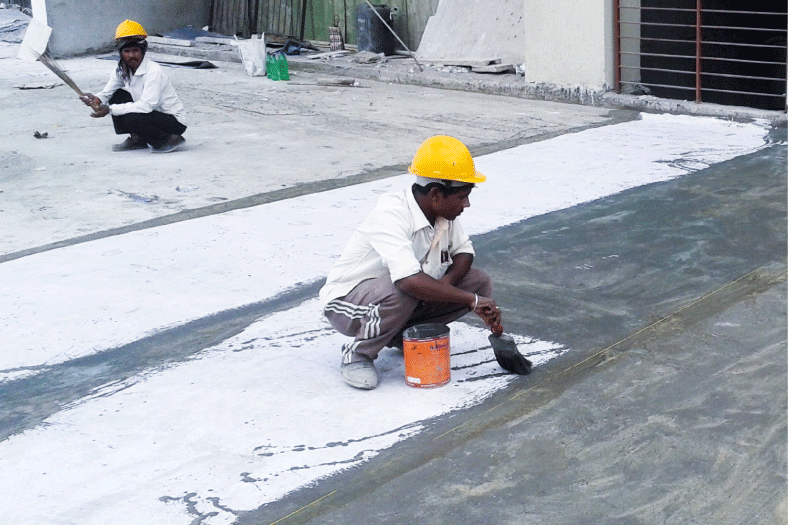


Epoxy grouts
Epoxy grouts have an edge over ordinary grouts especially in harsh environmental conditions such as exposure to extreme temperatures, oil, grease, acids, chemicals and so on. Besides, they are much more durable and abrasion, impact, stain resistant as compared to ordinary grouts. However, they are more expensive too. Having good vibration damping characteristics, epoxy grouts are quite suitable for grouting of industrial equipment or machine foundations.
Epoxy coatings
These can come as water or oil based solutions or as solvent-free. They can be single or two-component. Single-component epoxy paints are usually oil based. Two-component epoxy coatings are mixed in situ in proportions as prescribed by their manufacturers and they are quite suitable for factory, industrial or commercial building applications by dint of their excellent chemical & thermal resistant characteristics, hardness, durability, waterproofing characteristics etc. They are solvent-free. Epoxy coatings are also used in flooring for decorative purposes.
Chemical for for high performance concrete
Construction chemical is now being used to gain the proper attribute of mechanical strength of high performance concrete.HPC mixtures are composed of essentially the same materials as conventional concrete mixtures, but the proportions are designed, or engineered, to provide the strength and durability needed for the structural and environmental requirements of the project. High-strength concrete is defined as having a specified compressive strength of 8000 psi (55 MPa) or greater. Special care is required for production and testing of the concrete and at which special structural design requirements may be needed.
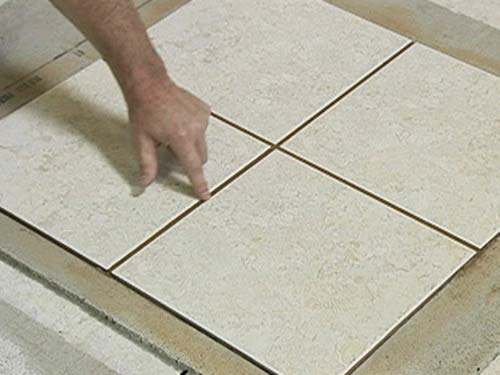


Conclusion
Construction chemicals are compounds that are added to concrete and mortar to enhance compatibility with the structure of buildings. These chemicals improve properties such as durability, surface finish, compressive strength and resistance to undesirable working conditions, and climatic and are expected to drive the industry growth. In addition, the property of these chemicals to minimize the quantities of water and cement required during the construction is anticipated to boost the demand for this product in the upcoming years.